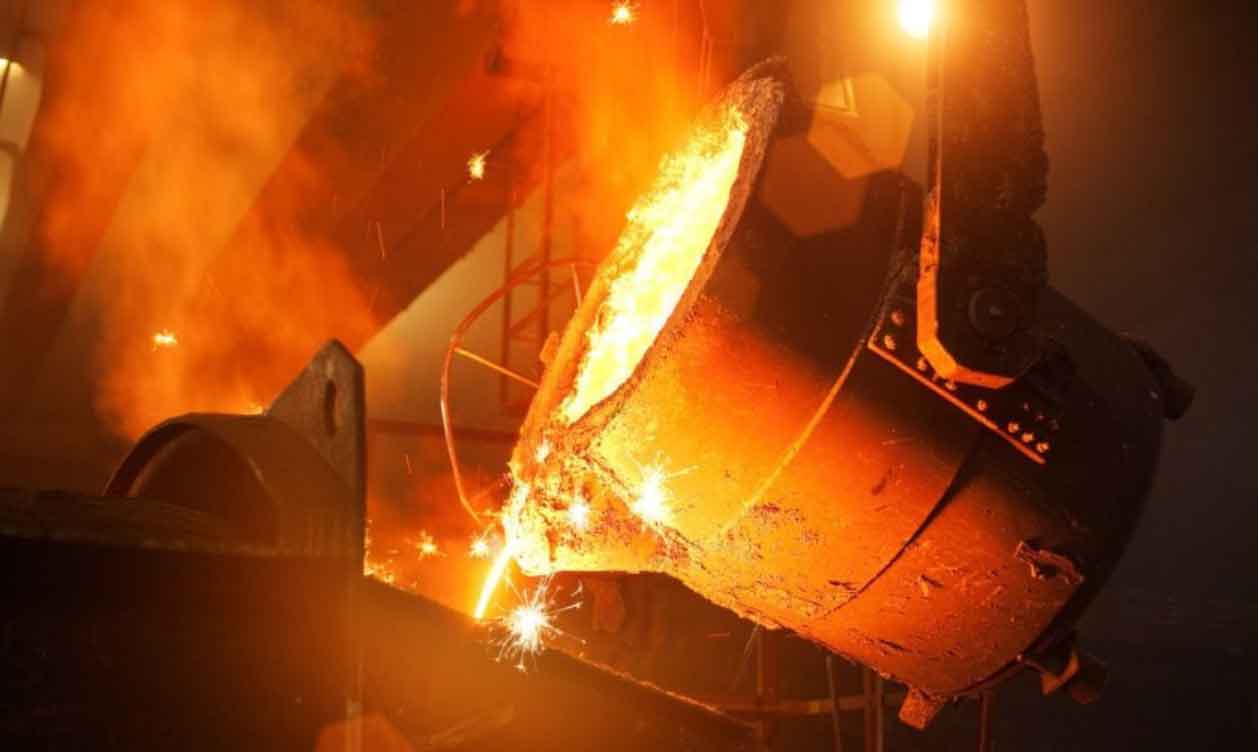
Sand casting and V-method casting are two popular techniques used in metal casting. Both methods have their advantages and disadvantages, and the choice between them depends on various factors such as the type of metal, complexity of the casting, and production volume. Here’s a comparative analysis of sand casting and V-method casting:
- Process Overview:
- Sand Casting: In sand casting, a pattern is created to replicate the final product. The pattern is pressed into a specially prepared sand mixture to create a mold cavity. Molten metal is poured into the mold, and after solidification, the mold is broken to retrieve the casting.
- V-Method Casting: V-method casting, also known as vacuum molding or vacuum sealed molding, involves the use of a plastic film or resin to create a mold. The pattern is placed in a flask, and a plastic film is tightly wrapped around it. The flask is then filled with dry sand, and a vacuum is applied to draw the plastic film tightly against the pattern. Molten metal is poured into the mold, and once solidified, the mold is opened to extract the casting.
- Mold Quality and Surface Finish:
- Sand Casting: Sand casting can produce rougher surfaces compared to V-method casting. The sand molds may exhibit some imperfections, such as sand inclusions or surface roughness, which may require additional finishing operations.
- V-Method Casting: V-method casting typically results in superior mold quality and smoother surface finishes. The vacuum-sealed mold minimizes the occurrence of defects like sand inclusions, resulting in better overall surface quality.
- Complexity and Detail:
- Sand Casting: Sand casting is more suitable for complex and large-scale castings with intricate details. It allows for the creation of complex part geometries and the incorporation of cores for internal features.
- V-Method Casting: V-method casting is better suited for relatively simpler castings with fewer intricate details. The process may have limitations in replicating extremely complex shapes or internal structures.
- Production Volume and Cost:
- Sand Casting: Sand casting is a versatile and cost-effective method for producing both small and large production volumes. It is particularly economical for large-scale production due to lower tooling costs and material expenses.
- V-Method Casting: V-method casting is generally more suitable for medium to high production volumes. While the tooling costs may be higher compared to sand casting, the improved surface finish and reduced post-casting operations can lead to overall cost savings.
- Casting Material:
- Sand Casting: Sand casting can be used with a wide range of materials, including ferrous and non-ferrous metals, such as iron, steel, aluminum, and bronze.
- V-Method Casting: V-method casting is commonly used for casting non-ferrous metals, such as aluminum, brass, and bronze. It may not be as suitable for casting certain ferrous materials due to the high pouring temperatures required.
Sand casting is a versatile and cost-effective method suitable for complex and large-scale castings, while V-method casting offers better surface finish and is more suitable for medium to high production volumes with simpler castings. The choice between the two methods depends on factors such as casting complexity, surface finish requirements, production volume, and material selection.