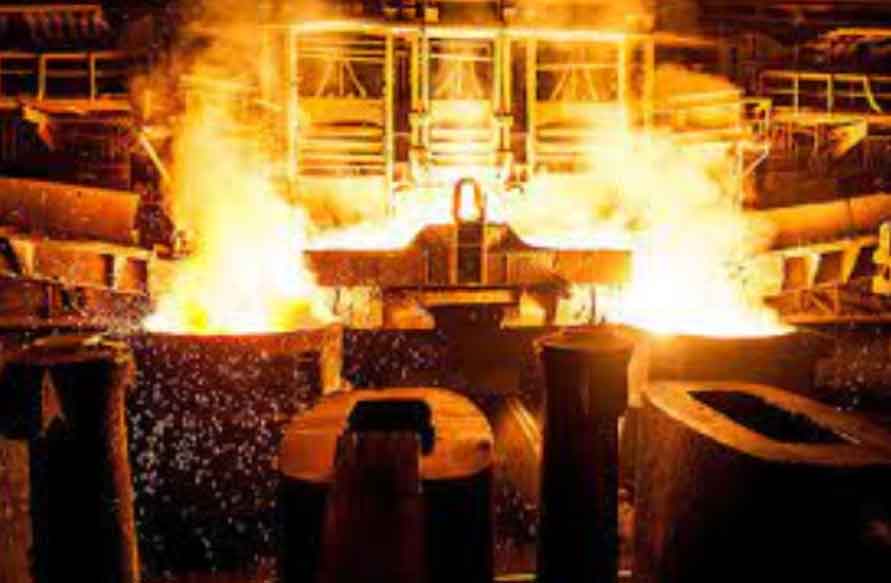
Sand casting and gravity casting are two commonly used techniques in metal casting. They have distinct characteristics and are suited for different applications. Let’s compare sand casting and gravity casting:
- Process Overview:
- Sand Casting: Sand casting involves creating a mold by packing a mixture of sand and a binder around a pattern. The mold cavity is formed by removing the pattern, and molten metal is poured into the mold. After solidification, the mold is broken to extract the casting.
- Gravity Casting: Gravity casting, also known as permanent mold casting or gravity die casting, utilizes a reusable mold made of metal, typically steel or iron. The molten metal is poured into the mold, and gravity fills the cavity. After solidification, the mold is opened to remove the casting.
- Complexity and Detail:
- Sand Casting: Sand casting is suitable for casting complex and intricate shapes with varying wall thicknesses. It allows for the incorporation of cores to create internal cavities or features. The flexibility of sand molds makes it possible to cast parts with intricate details.
- Gravity Casting: Gravity casting is better suited for simpler shapes and parts with relatively thicker walls. It may not be as effective in reproducing highly complex and detailed geometries as sand casting.
- Surface Finish and Dimensional Accuracy:
- Sand Casting: Sand casting can produce a rougher surface finish compared to gravity casting. Additional finishing operations like grinding or machining are often required to achieve the desired surface quality. Dimensional accuracy may be affected due to the mold materials’ inherent flexibility.
- Gravity Casting: Gravity casting generally results in a smoother surface finish with less post-casting finishing required. The use of metal molds provides better dimensional stability, resulting in improved accuracy.
- Production Volume and Cost:
- Sand Casting: Sand casting is suitable for both low and high production volumes. It offers cost advantages for large-scale production due to lower tooling costs and material expenses. However, the labor-intensive mold preparation and casting extraction processes can add to the overall production cost.
- Gravity Casting: Gravity casting is commonly used for medium to high production volumes. While the initial tooling costs for metal molds are higher compared to sand casting, the molds’ reusability and faster production cycles can lead to cost savings in the long run.
- Casting Material:
- Sand Casting: Sand casting is versatile and can accommodate a wide range of casting materials, including ferrous and non-ferrous metals.
- Gravity Casting: Gravity casting is commonly used for non-ferrous metals such as aluminum, brass, and bronze. It may not be as suitable for casting certain ferrous materials due to the high pouring temperatures required.
Sand casting is suitable for complex shapes and offers flexibility, while gravity casting is better suited for simpler parts with improved surface finish and dimensional accuracy. Sand casting can be cost-effective for large-scale production, whereas gravity casting is advantageous for medium to high production volumes. The choice between the two methods depends on the part complexity, surface finish requirements, production volume, and material selection.