The gray iron casting of a certain type of automobile engine block has a maximum outline dimension of 371mm × 329mm × 256mm, a weight of 35kg, a basic wall thickness of 3.5mm, and a relatively simple shape. The casting is produced on HWS molding line, with damp sand technology. After the sand core pre assembly is completely cleaned, it is directly poured into the sand mold by the automatic core setting machine. It is required that there should be no air hole and sand hole defects after machining, and it should be checked by pressure test of water jacket and oil passage leakage, which requires high quality of castings.
In the process of mass production, the leakage rate of oil channel processing is up to 7%, which seriously affects the product quality. After getting the feedback information of the processing, through the analysis of the casting processing waste, it is found that there are obvious “fleshy” phenomena in the main oil channel and the plugging hole of the casting, as shown in the figure, and most of the “fleshy” defects are layered, and after the “fleshy” defects are polished, there are small agglomerates or massive sand grains inside.
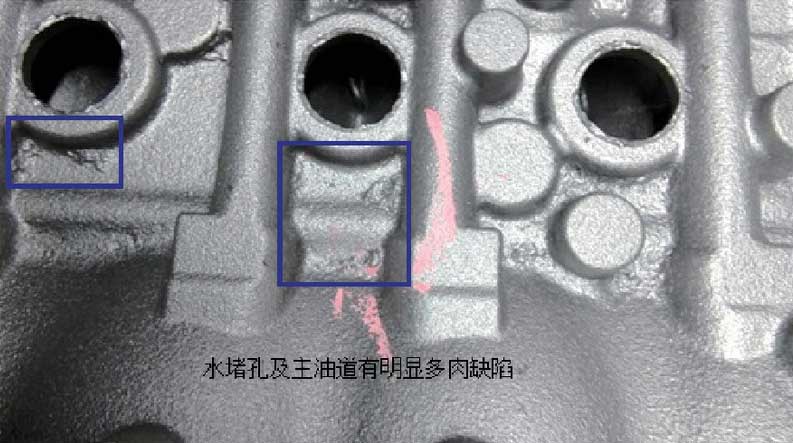
There is obvious liquid exudation after pressure test of casting. The appearance defects of pressure test leakage are as shown in the figure. After dissection, the inner cavity is stained for nondestructive testing, as shown in the figure. When the developer is sprayed on the outer surface, it is obvious that the colorant penetrates from the inner cavity of the casting to the surface of the casting, as shown in the figure, indicating that the defect is a through defect. Combined with the above characteristics, the defect is judged to be sand inclusion Scab Defect.
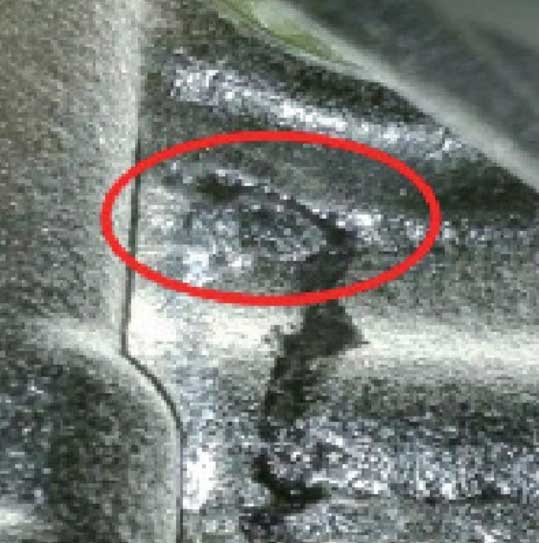
Although there are different opinions on the causes of scab, most of them think that the volume expansion and water migration of molding sand are the basic causes of scab defects. After pouring the molten metal, with the heating effect of the molten metal flow, the surface water of the mold moves inward. The migration of water leads to the formation of a dry layer on the surface of the mold. The strength is increased, and a high wet layer and a weak layer are gradually formed in the mold. When the strength and toughness of the weak layer are insufficient, the surface layer of the molding sand may be cracked, the sand layer may be cocked up, and scab defects may be formed. With the continuous erosion of liquid metal, the warped sand layer may break and break, leaving the sand layer in the original place or being carried into other parts.
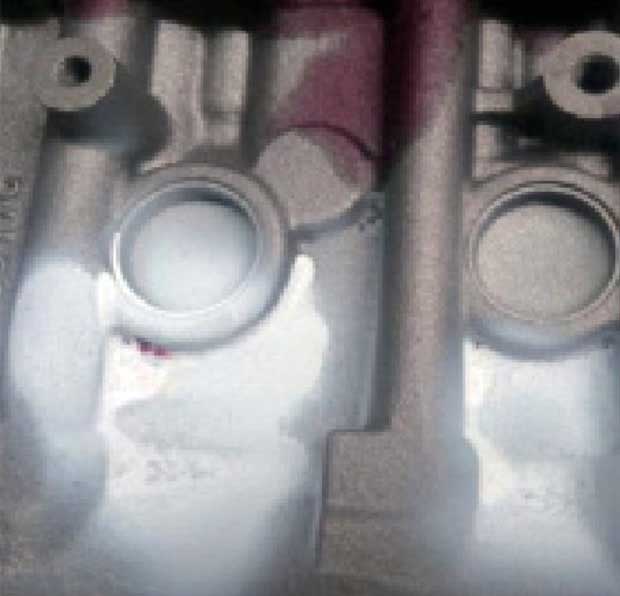
Through the observation of the defects, it can be found that the defects conform to the characteristics of scabbing defects, that is, the surface sand layer is warped or part of it breaks off during the pouring process, and scabbing defects are formed at this position, and oil and water leakage occurs after processing. In addition, some of the lost molding sand is washed to the top of the casting, which may cause sand hole defects and lead to casting scrap.
1) In the case of simple shape, especially in the engine block and other gray iron castings with local large plane position, the scab and sand inclusion defects are easily formed in the local large plane position when the performance of molding sand deteriorates or deteriorates.
2) If there is Scab Defect in the product, the performance of molding sand shall be analyzed immediately, and the performance parameters of molding sand shall be adjusted, especially the adjustment of mud content and water ratio of molding sand.
3) For the Scab Defect of the product, on the premise that the product quality is not affected, reducing the pouring temperature can significantly reduce or even contain the proportion of sand inclusion and Scab Defect.
4) If aluminosilicate fire-resistant alcohol-based coating is applied to the parts with sand and scab, the scab defects can be completely eliminated even when the properties of molding sand fluctuate, so as to improve the qualified rate of products.