0 Introduction
As an important component of the engine, the turbocharger plays a crucial role in improving the engine’s performanceIts power, emissions, and economy have a great promoting effect. The volute isOne of the main components of a turbocharger, such as the engine being exposed to high temperature and pressure for a long timeUnder harsh working conditions, there are strict requirements for the dimensional accuracy and strength of the volute. Volute flowThe channel is a complex and variable diameter curved surface, and the channel sand core manufactured by traditional sand mold castingDifficulty in meeting job requirements, and due to limitations in installation space and other factorsThe limitations of component connections make its appearance and structure complex, making it difficult to cast.Taking the spiral case casting produced by a certain mechanical process as the research object, the traditional sand casting mold is prone to wear and damage during repeated use, leading to spiralThe problem of poor stability in the spatial structure and size of the V-shaped flow channel is raised, and 3D drilling is proposedThe production plan of the printed sand core. 3D printing enables the advancement of digital sand core productionOne step optimization, combined with ProCast simulation software analysis for real-time optimization, withThere are advantages that traditional sand casting cannot compare with, as evidenced by Solidworks drawing softwareAccording to the data sent to the 3D printer, the sand mold and sand core can be directly printed, achieving sand moldingNon modular printing production of sand cores.sand casting
The high reuse rate of molds used in traditional sand casting leads to the failure of componentsDimensional accuracy and strength are affected, and they are more sensitive to the complexity of components. The difficulty of mold making is high, and 3D printing sand casting is sensitive to the complexity of componentsIt has low performance and low difficulty in manufacturing sand molds and cores, making it a new forming processMethod. This article adopts the 3D printing sand mold casting method to study the turbocharger voluteStructure, Casting Process Design, Casting Solidification Simulation, and Defect Analysis of Shell CastingsAnalysis and production validation were discussed.sand casting
1. Analysis of snail shell structure
The contour size of the turbocharger volute casting is 148 mm × one hundred and thirty-sixMm × 70 mm, with a mass of 2 kg, its structure is shown in Figure 1. As shown in Figure 2, wallAs shown in the thick analysis, the main body of the volute casting channel is less than 6 mm and belongs to the thin-walled categoryPieces. The structure of the volute casting is complex, with a streamlined “spiral” shapeThe cavity must be smooth to ensure that there is no turbulence in the airway. There are multiple protrusions on the outside of the casting,The overall size is relatively high, which can easily lead to insufficient shrinkage during pouring, resulting in shrinkageCasting defects such as porosity and shrinkage; The flow channel is a curved surface with variable diameter, which needs to be accurately setPlace channel sand. Due to the unique structure and high quality of volute castingsThere are significant difficulties in actual casting. sand castingTherefore, it is necessary to combine 3DPrint to study the casting process forming plan.
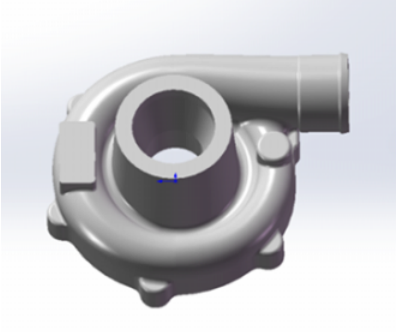
Figure 1 Casting Structure
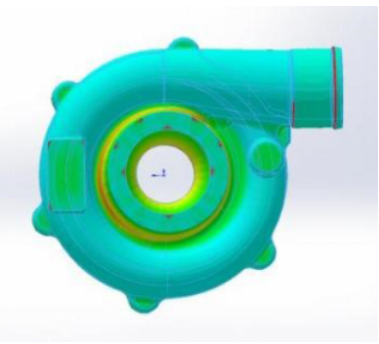
Figure 2 Wall thickness analysis
2. Material Setting and Boundary Conditions
The casting material selected for the spiral case casting is aluminum alloy ZL101A, with chemical compositionAs shown in Table 1, ZL101A aluminum alloy has high strength, good corrosion resistance, and castFeaturing excellent manufacturing performance, it is widely used in aerospace, automotive, and electrical industriesPower grid and other fields . sand casting The boundary conditions and initial conditions for simulation analysis are:The heat transfer coefficient between the shell and the casting is 228 W/(m2·℃), pouring temperatureIt is 720 ℃ and the pouring time is 6 seconds.
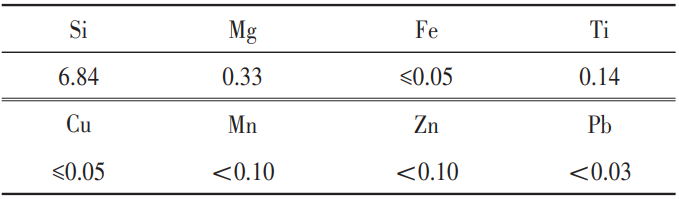
3 Design casting process
Analyzing the structural characteristics of the spiral case, the pipeline presents a “vortex” with a gradient radius featureVortex shaped, the connecting flange of the bearing body is in a circular shape, and a hexagonal star bottom is designedThe pouring system, as shown in Figure 3, is a model of the pouring system in Scheme 1. Sprue cupLocated next to it, the sprue of the middle pouring tube type is located in the center of the casting, while the middle pouringThe pipe type sprue should not be too large to reduce the impact on the molten metal. Riser placementTransfer casting defects at the center of the casting. Set a hexagonal star base at the bottom of the castingThe injection pouring system ensures a smooth rise of the molten metal and smooth filling of the mold.sand casting
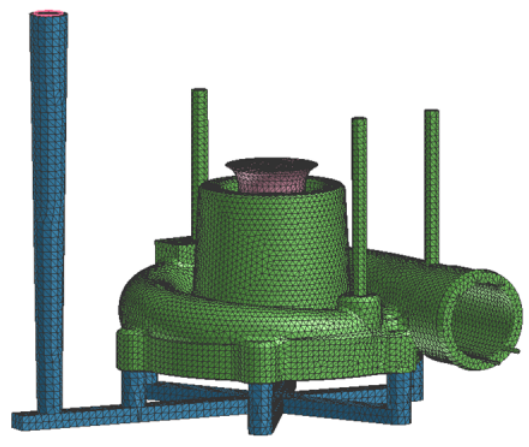
Figure 3: Pouring System Model for Option 1
3.1 Simulation and Analysis of Filling Process
Using sand casting to simulate the flow of molten metal and analyze the filling process. WhenWhen the mold cavity is full, the minimum temperature of the metal liquid is still above 550 ℃, without pouringFoot phenomenon. The simulated filling process is shown in Figure 4. At the beginning of filling, goldThe liquid flows smoothly into the sprue from the gate tube, and from the beginning to 30% filling, the goldThe liquid enters the mold cavity from the bottom runner up, reducing the direct flow from the topThe impact of partial entry into the mold cavity on the bottom of the sand core causes the metal liquid to flow more smoothlyFill the mold, and the sprue of the middle pouring tube type can be evenly located at the center of the castingFilling, reducing the generation of defects, and filling the metal liquid from bottom to top until the endFull cavity. The entire casting filling process is smooth and orderly, without obvious air entrainment phenomenonThe pouring system has preliminary rationality.sand casting
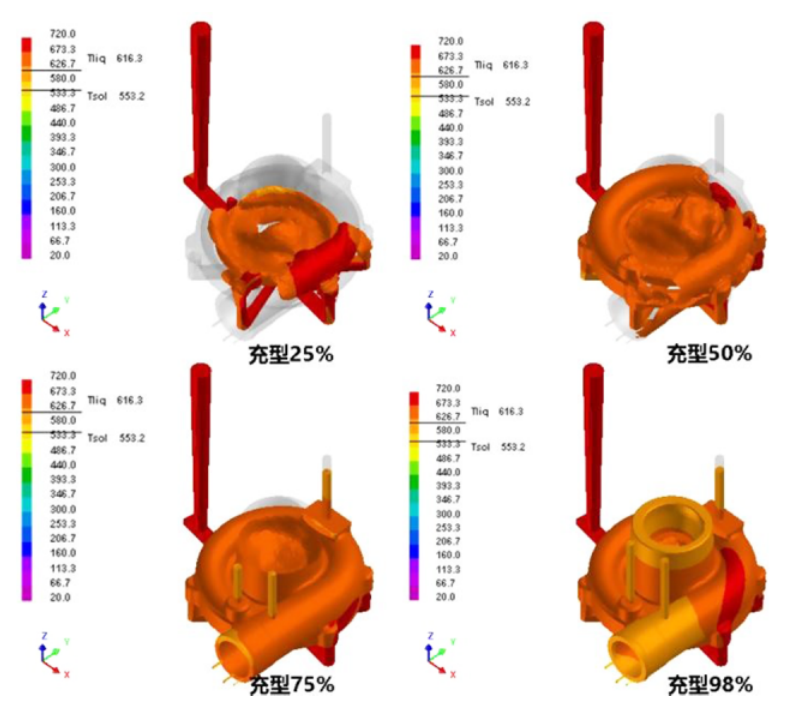
Figure 4 Simulation and Analysis of Filling Process
3.2 Simulation and Analysis of Solidification Process
The analysis and simulation of solidification process are shown in Figure 5. Temperature field display of casting coldBut the entire process. From the solidification process, it can be seen that the riser has already solidifiedSolidification is slower in the top area of the volute casting. Because the riser is too small,Poor insulation leads to insufficient shrinkage, resulting in defects. From the end of Figure 5The solidification diagram also shows that the riser has solidified, and the solidification process at the top of the volute is relatively slowSlow, insufficient shrinkage in this area can easily lead to casting after solidification is completedDefects that cannot meet the expected process requirements.sand casting
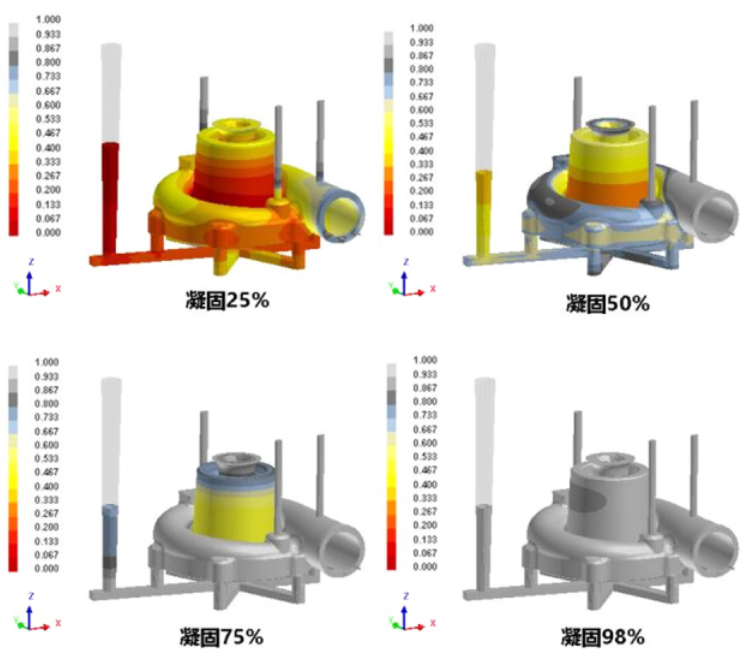
Figure 5 Simulation and Analysis of Solidification Process
4. Defect Analysis
From Figure 6, it can be seen that the casting defects cannot be well repaired during pouringShrinkage of the top area of the casting results in insufficient density of the microstructure in the hot spot area.From the filling process in Figure 4, it can be seen that the metal liquid enters the bottom runner evenly from the runnerFilling the mold upwards, due to the small top riser, it cannot maintain good insulationThe top area cannot be well filled. From the solidification sequence in Figure 5, it can be seen that,The channel of the sprue system solidifies first, causing the top to be unable to provide timely shrinkage, resulting inShrinkage hole. So if the riser is too small and the insulation effect is poor, it can cause shrinkage and looseness in the castingThe main cause of casting defects such as shrinkage. Figure 6 shows shrinkage porosity and shrinkage of castingsHole distribution.sand casting
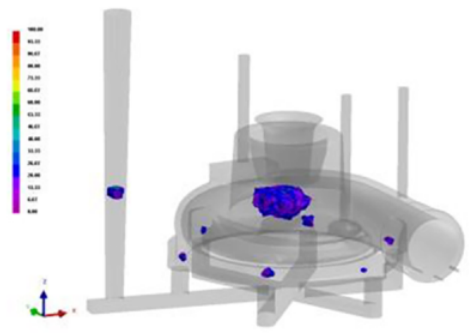
Figure 6 Distribution of shrinkage porosity and porosity in castings
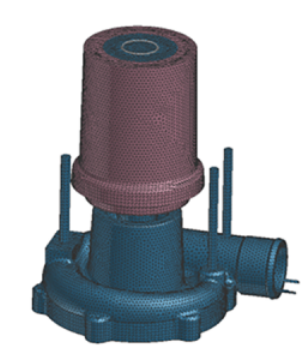
Figure 7 Optimized Pouring System Model
5. Optimize the design of casting process
In response to the defect issue in Scheme 1, Scheme 2 will form a sand mold for the riserIntegrated with the pouring cup, the temperature of the pouring cup can cause the riser to be too small, resulting in insulationThe problem of poor effectiveness has been resolved. Not only does it facilitate the establishment of the model, but it alsoReduce the weight of the sand core. The main body of the volute casting channel is less than 6 mm and belongs to the thin-walled categoryParts are not conducive to setting up internal pouring channels, which can easily cause sand flushing defects. Design adoptedThe production method of horizontal parting and vertical pouring. The interior of the volute casting is a cavity flowDesign the sand core of the flow channel, while setting up a convex boss to maintain fixation on the sand core of the flow channel,Considering the generation of porosity in castings, exhaust holes should be appropriately added to the raised areas,Can effectively eliminate gas, reduce the occurrence rate of casting porosity, and reduce casting wasteProduct rate. There are many ribs and protrusions on the outside of the box, and the box is made of one sand moldAnd 1 lower sand molding. Finally, a filter is placed at the riser (gate) to filter the slag and reduce turbulence. Figure 7 shows the optimized pouring systemUnified model.sand casting
5.1 Analysis of simulation results
Figure 8 shows the simulation results of the mold filling process after casting optimization. As can be seen,In the early stage of filling, the metal liquid quickly enters the bottom of the volute, and the entire filling process is relativelySmooth and smooth. When the cavity is full, the minimum temperature of the metal liquid is still 720 ℃Above, there is no phenomenon of insufficient pouring. Figure 8 shows the temperature field from the bottom of the volute to the topThe stepped distribution of the mouth helps to solidify the castings in sequence and ensure the quality of the castings. MaoAs the final filling part, the mouth can transfer gas from the inside of the mold cavity to the ventNear the mouth, thus playing a role in slag discharge and gas removal. In addition, the exhaust holeSetting, further reducing casting defects, designing casting risers and sprue cupsOne piece helps to maintain insulation of the riser, thus providing sufficient repair at the top of the castingShrink. Figure 9 shows the simulation results of the solidification process of the casting, and it can be seen from the figure that the finalThe solidification positions are all near the riser, eliminating the final solidification area in Scheme 1The problem at the top.sand casting
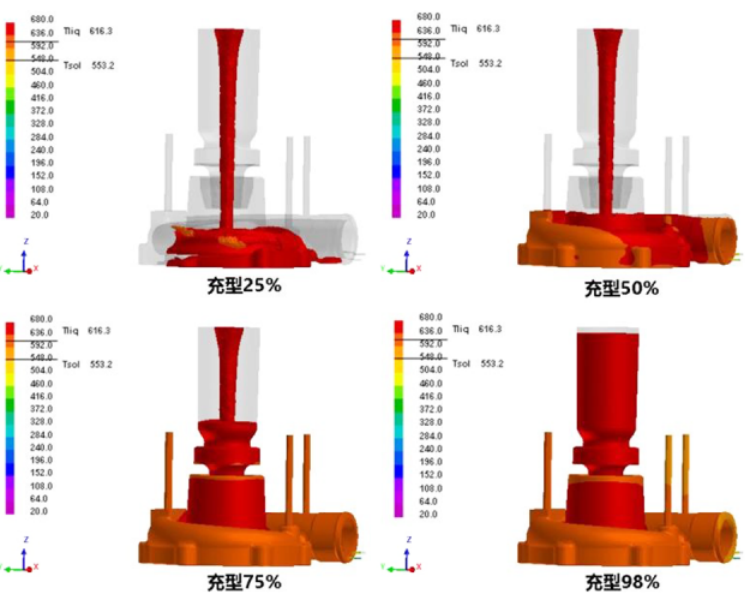
Figure 8 Simulation diagram of optimized filling process
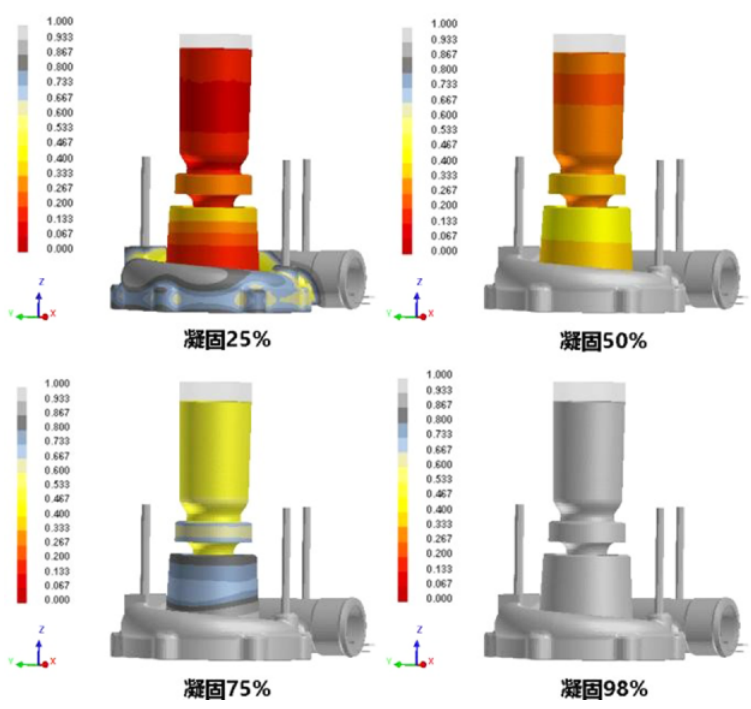
Figure 9 Simulation diagram of optimized solidification process
5.2 Defect analysis after scheme optimization
Based on the simulation results of ProCast, Figure 10 shows the possible locations of shrinkage porosity and porosity. As shown in Figure 10, due to the integrated design of the gate cup and riserHaving sufficient insulation to ensure sufficient shrinkage in the top area of the castingThe defects are all transferred to the riser, with a small amount located at the position of the volute support holeThe position belongs to the threaded hole, with a low shrinkage rate, which does not affect normal production.sand casting
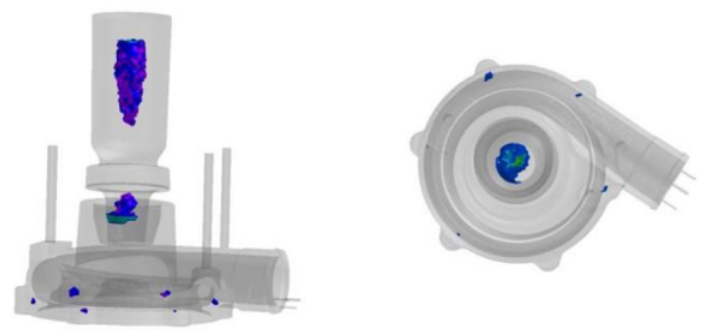
Figure 10 Optimization of Casting Defects
5.3 3D printing sand core design
Based on the optimized casting process, combined with the handling and coating of sand coresDesign four sand cores according to requirements such as improving surface smoothness and box size,As shown in Figure 11. The 1st and 2nd sand cores form the external integrity of the castingOutline of the body, the 3rd sand core is a channel sand core, and the 4th sand core is a riser sand core. branchSelect the position of the profile in the middle. In order to prevent floating cores, all sand cores are equipped withFixed holes have been calculated. At the same time, to prevent misalignment during the box closing process and ensure the cavity sizeInches, positioning is designed between every 2 sand cores. Figure 12 shows the molded core.sand casting
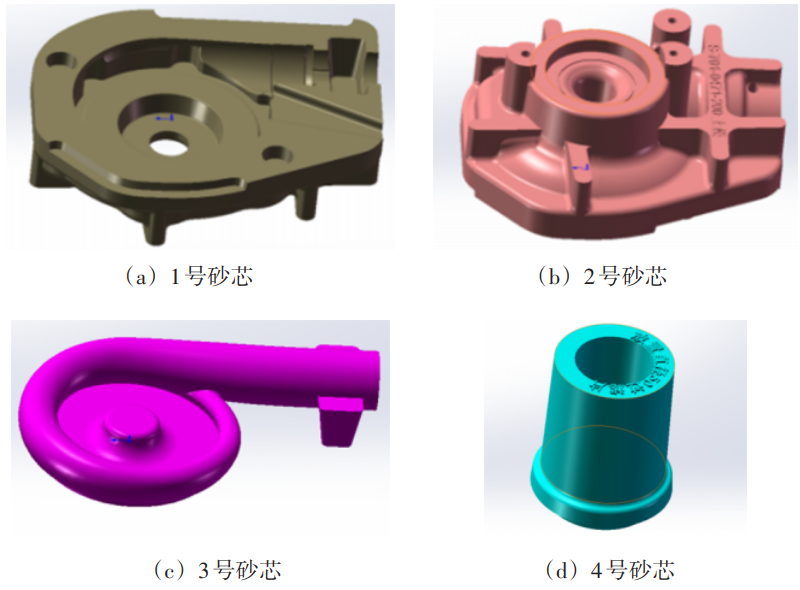
Figure 11 Design of 4 Sand Cores
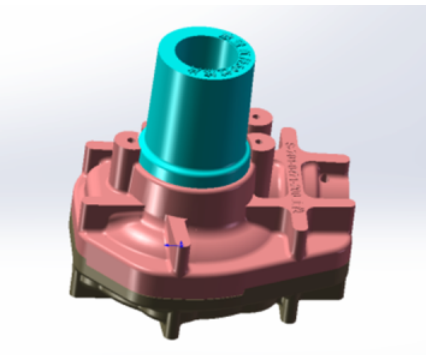
Figure 12 Shape Core Assembly
6 Production Validation and Result Analysis
6.1 Sand core printing
The 3D printing equipment adopts the LaserCore-5300 printer, with a maximum printing size of 700 mm × 700 mm × 500 mm, printing layer thickness0.08~0.35 mm, printing accuracy ± 0.1 mm/100 mm, can meet the requirements of sand coresThe product is printed using resin sand. The adhesive uses furanResin and curing agent. The trial production parameters adopt molds that are consistent with the original plan parametersTo analyze boundary conditions and initial conditions. According to the working principle of the 3D printerRationale [17]: First, complete the sand laying process and evenly lay the sand on the workbench;Then proceed with curing, and the print head sprays the resin onto the already laid sand layerFace; Layer by layer solidification, completing sand mold printing in a cyclic manner; Finally, clean up the unfixed partsDissolve sand and remove the completed sand mold and sand core. Figure 13 shows the printing sandThe process of the core.sand casting
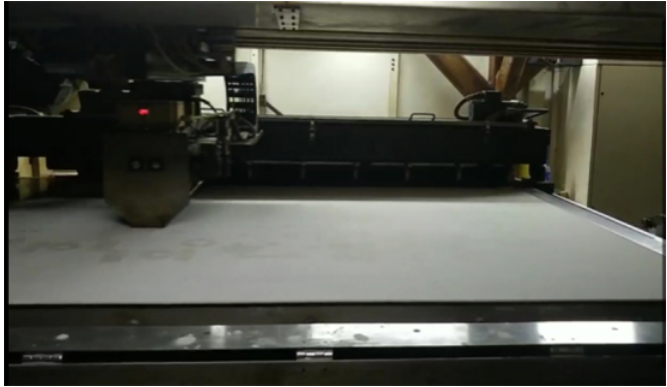
Figure 13: The printer is printing sand cores
6.2 Modeling and pouring
After coating the 1-4 sand cores, stack them one by one according to the design between the sand coresAfter positioning and fixing, fill sand around the core to shape it, and thenAfter the mold is assembled layer by layer, wait for pouring, as shown in Figure 14, which is the actual shape of the core assemblyFigure. Liquid metal is filled by the pouring system in the mold under the action of gravityFill the mold cavity between the sand mold and the sand core, and after cooling and forming, enterConduct sand removal and clean the casting [18]. Figure 15 shows the casting after pouring.sand casting
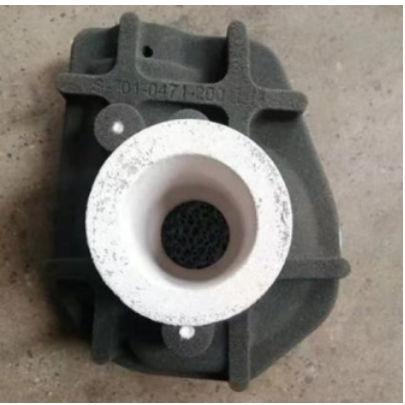
Figure 14 Shape and core assembly physical object
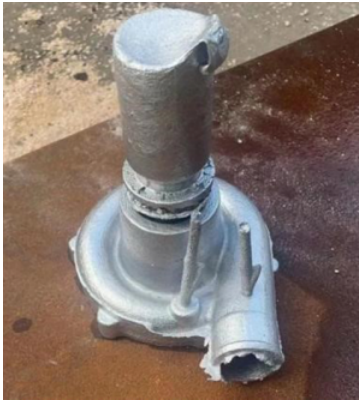
Figure 15 Casting After Pouring
6.3 Analysis of validation results
Spiral casing castings are produced according to the optimized 3D printing sand casting process planProduction validation. The prepared volute casting is shown in Figure 16, and the finished product isThe surface quality of the product casting is good, without casting defects such as shrinkage and porosity. afterThe X-ray inspection results indicate that the casting meets the process design requirements.The 3D printing sand mold casting process has achieved modeless production and can be used directlyPrinting sand molds with any structure eliminates the sensitivity of the mold to the casting structureEmotional constraints. When using 3D printing sand casting technology, the sand mold is integrated, which can reduceThe errors generated during the assembly process of small sand molds can improve the dimensional accuracy and strength of sand molds or cores [19]. So designing the riser and sprue cup as one not only allows forTo achieve the function of insulation riser, reduce casting defects, and also improve the snailDimensional accuracy and strength of shell castings. In summary, the 3D sand mold printing snailThe shell casting scheme has advantages that traditional casting cannot compare with.sand casting
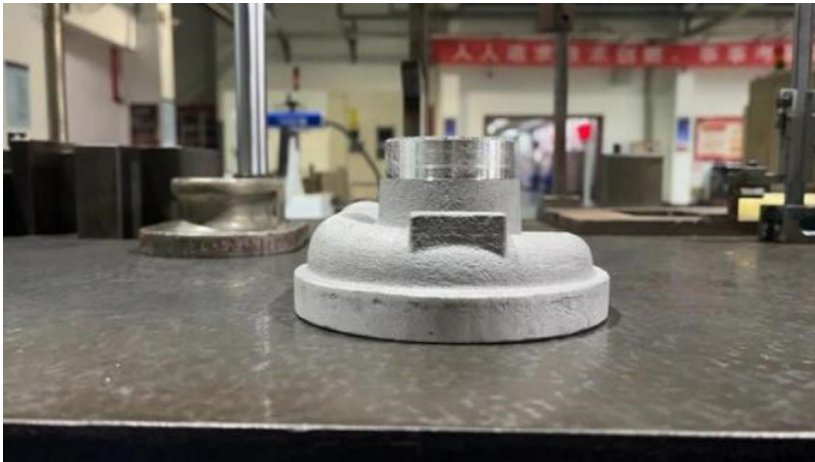
Figure 16 Real object of spiral case sample
7 Conclusion
(1) According to the 3D printing sand mold casting process plan, carry out the spiral case castingAnalysis of trial production results shows that this process plan can replace the traditional core assembly molding process,Save the time and cost required for the production of new casting molds, while also combiningProCast simulation software greatly shortens the development cycle of samples.(2) Use ProCAST casting simulation software in the design to simulate the filling process of castingsSimulated and simulated the temperature field during the mold and solidification process, and analyzed the original pouring processThe causes of shrinkage porosity and shrinkage cavity casting defects in the system have been identified, and solutions have been proposed to address these issuesFor the purpose of process optimization. Option 1: Due to the small riser, the insulation effect is affectedPoor results result in poor shrinkage of the top area of the casting, resulting in defects. according toThe optimized process plan integrates the design of the riser and gate cup, resulting inThe defect rate of the produced products has been well controlled, further improving the quality of castingsQuality has improved the economic benefits of the enterprise.(3) 3D printing technology does not need to consider the issues of mold lifting and material withdrawalQuestion: The riser and sprue cup can be designed as one unit to reduce sand coresTotal number, simplifying the core assembly molding process, while improving the dimensional accuracy and strength of castingsReduce the difficulty of on-site operations and quality waves caused by complex operationsMove.sand casting