Slag hole (including sand hole) is also one of the common defects of gray cast iron cylinder block produced by sand casting, which often appears on the upper mold surface of the casting or the inner surface of the cylinder barrel. Both slag hole and sand hole defects are cavity defects formed in the casting by the penetration of foreign inclusions into the molten iron slag hole, which destroys the integrity of the casting and leads to the increase of casting scrap rate. Therefore, it is also very important to study the causes and elimination measures of slag hole (sand hole) defects.
Figure 1 shows the XRD pattern of slag inclusion on the surface and bottom of the insulation pouring furnace. It can be determined that the surface slag is mainly a mixture of some aluminosilicates, oxides and carbides. SiC is the residue of slag inclusion formed because SiC in smelting auxiliary materials is not completely dissolved, while SnO2 is the burning loss product of Sn added during molten iron smelting. The bottom slag is mainly composed of MnO2, CAS and mgal2o3. The density of these substances is higher than that of molten iron, so they are mostly deposited at the bottom of the pouring furnace.
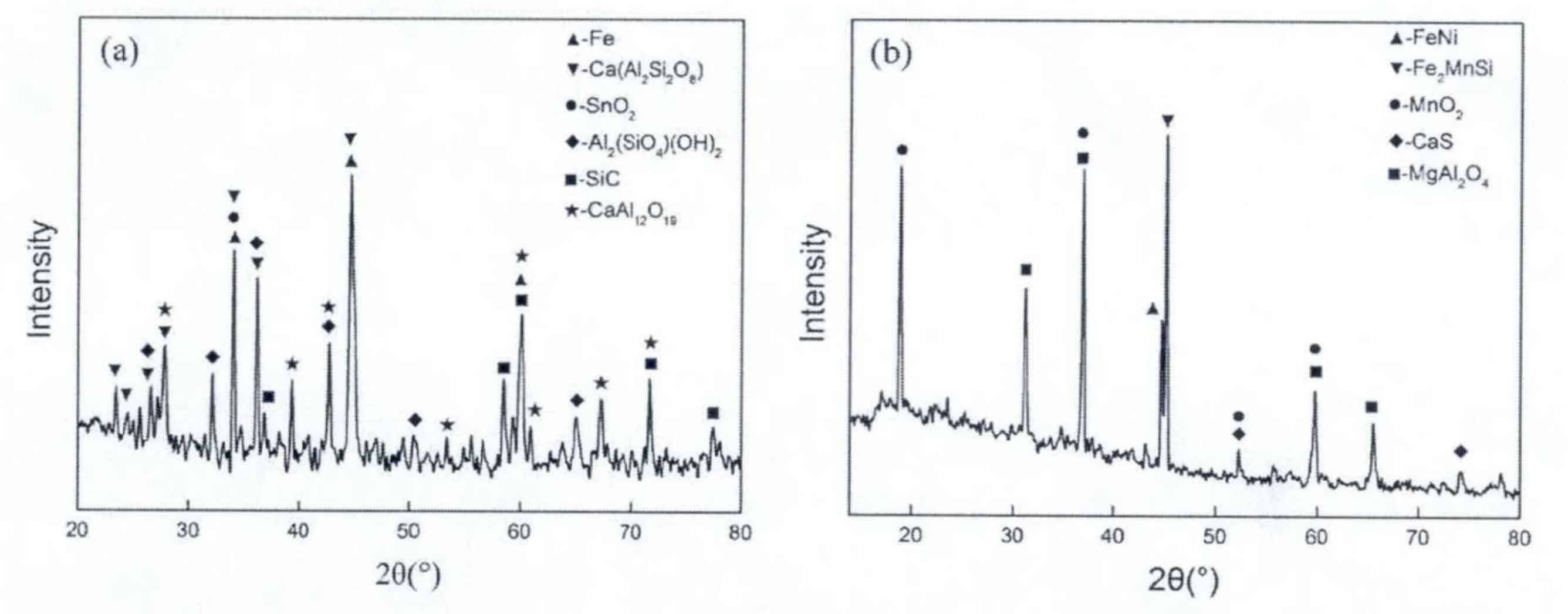
Figure 2 shows the cross-sectional morphology and energy spectrum of slag hole defects in gray cast iron cylinder block. The interior of the dark black slag hole is rough, and there are many particles distributed. According to the energy spectrum analysis of these particles, it is found that there are a large number of O elements. At the same time, the content of Al, Si and Mn elements is higher than that of other alloy elements. Combined with the phase differentiation of slag inclusion in Figure 1, it can be seen that the main component at position 1 should be a mixture of Al2O3, SiO2 and MnO2, At the same time, it may also contain a small amount of CAS or Cao. Due to the high content of Al in the slag, it should be the scum in the molten iron, so the color is white and bright. However, most of the defects are similar to 2, which are dark gray. According to the morphology observation and energy spectrum analysis, they should be the small particles covered on the casting matrix (the large sand particles with poor adhesion may have fallen off after ultrasonic cleaning during the experiment). This defect is mainly due to the sand holes formed by the fallen sand particles or burrs on the sand core.
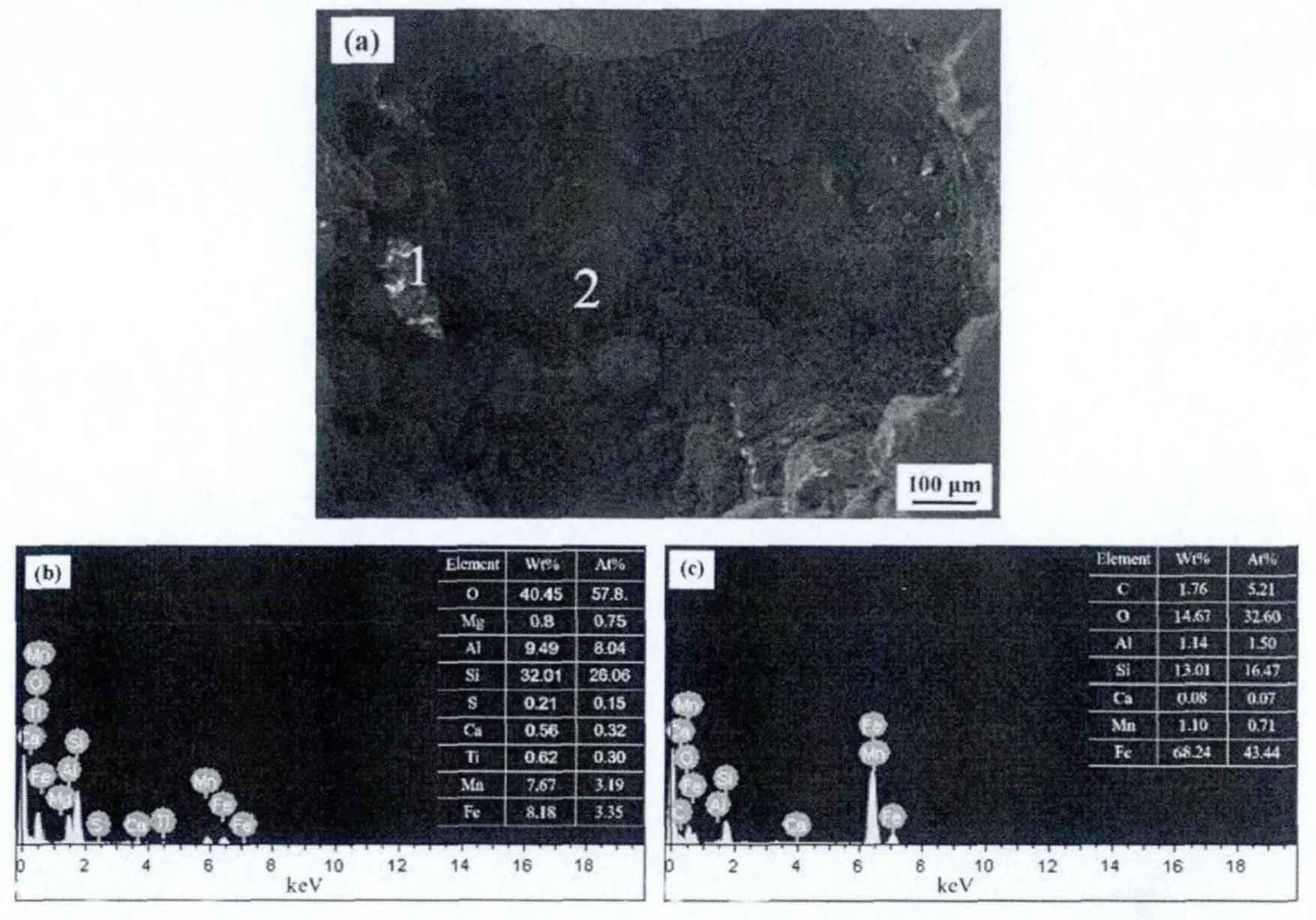
According to the comprehensive analysis, the defect is caused by sand particles (mainly composed of SiO2) and scum during pouring. Sand particles can be used as a kind of foreign inclusions. Therefore, we collectively call the defects caused by sand particles and slag inclusion as slag holes.