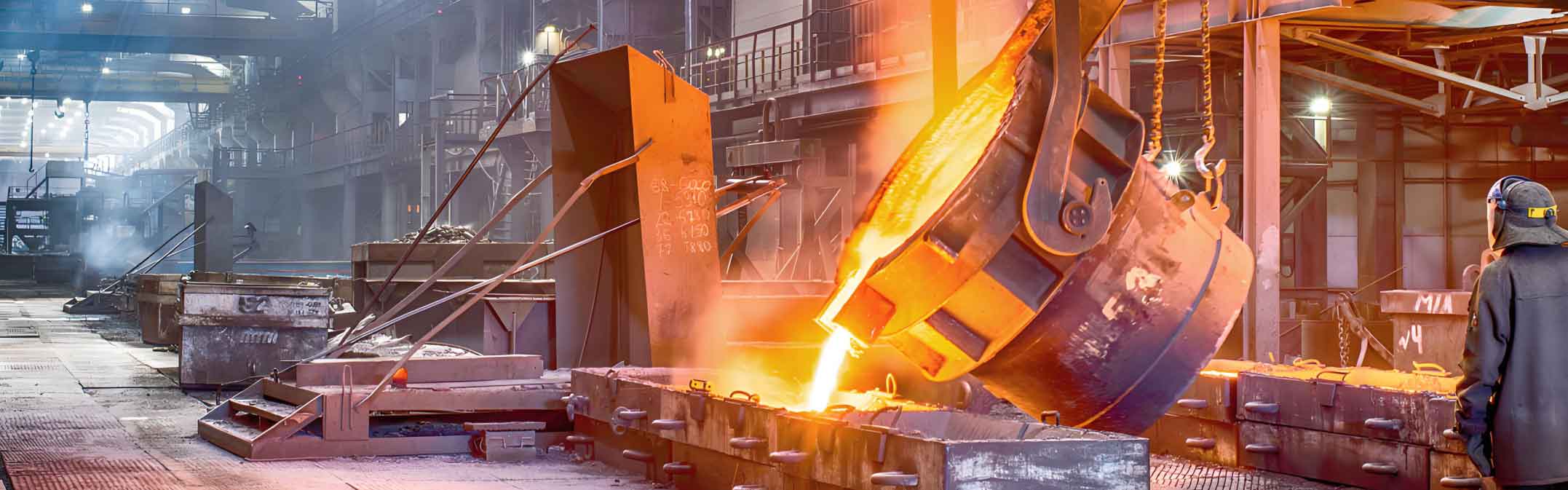
Introduction
Lost foam casting is an innovative metal casting process that offers several advantages over traditional casting methods. It involves creating a foam pattern that is coated with a refractory material. The coated pattern is then placed in a sand mold, and molten metal is poured into the mold. The foam pattern vaporizes, leaving a cavity that is filled by the molten metal, resulting in a cast part. This technique is particularly beneficial for producing complex and precise metal components.
Advantages of Lost Foam Casting
Lost foam casting provides numerous benefits that contribute to optimizing production efficiency:
- Complex Geometries: Lost foam casting allows for the creation of complex geometries that would be difficult or impossible to achieve with traditional casting methods. This is particularly useful for components with intricate internal structures.
- Reduced Machining: The high precision of lost foam casting reduces the need for post-casting machining, saving both time and costs.
- Material Savings: The process minimizes waste material, as the foam pattern is completely vaporized during casting, and there is no need for cores or parting lines.
- Improved Surface Finish: Lost foam casting typically results in a superior surface finish, reducing the need for additional finishing processes.
- Dimensional Accuracy: The process offers excellent dimensional accuracy, which is crucial for components that require tight tolerances.
Process Overview
The lost foam casting process involves several key steps:
- Pattern Creation: A foam pattern is created using polystyrene or another suitable material. The pattern is typically formed by machining, molding, or assembling smaller foam sections.
- Pattern Coating: The foam pattern is coated with a refractory material to create a mold surface that can withstand the high temperatures of molten metal.
- Mold Formation: The coated foam pattern is placed in a flask and surrounded by unbonded sand. The sand supports the pattern and provides stability during casting.
- Metal Pouring: Molten metal is poured into the mold, causing the foam pattern to vaporize and leaving a cavity that is filled by the metal.
- Cooling and Extraction: Once the metal has solidified, the casting is removed from the sand mold and any remaining refractory coating is cleaned off.
Enhancing Efficiency with Lost Foam Casting
To optimize production efficiency using lost foam casting, several factors must be considered and addressed:
Table 1: Key Factors in Lost Foam Casting Efficiency
Factor | Description |
---|---|
Pattern Quality | High-quality foam patterns reduce defects and improve dimensional accuracy. |
Coating Consistency | Uniform coating ensures consistent mold surfaces and reduces surface defects in cast parts. |
Sand Compaction | Proper sand compaction stabilizes the pattern and prevents mold collapse during metal pouring. |
Metal Flow Control | Controlled metal flow minimizes turbulence and ensures complete cavity filling. |
Cooling Rate | Optimized cooling rates prevent casting defects such as shrinkage and cracking. |
List 1: Best Practices for Lost Foam Casting
- Pattern Design: Design patterns with smooth transitions and avoid sharp corners to reduce stress concentrations.
- Coating Application: Apply the refractory coating evenly and allow sufficient drying time to prevent defects.
- Sand Quality: Use high-quality, unbonded sand and ensure proper compaction to support the foam pattern.
- Pouring Temperature: Maintain the appropriate pouring temperature for the specific metal alloy to ensure proper flow and fill.
- Cooling Process: Implement controlled cooling techniques to avoid rapid temperature changes that could cause defects.
Case Studies and Applications
Lost foam casting has been successfully applied in various industries, showcasing its versatility and efficiency:
Case Study 1: Automotive Industry
The automotive industry extensively uses lost foam casting to produce complex engine components, such as cylinder heads and intake manifolds. The ability to create intricate internal passages without the need for cores significantly reduces production time and costs.
Case Study 2: Aerospace Industry
In the aerospace industry, lost foam casting is employed to manufacture lightweight and high-strength components, such as turbine blades and structural parts. The precise control over dimensions and surface finish is crucial for aerospace applications.
Case Study 3: Industrial Machinery
Manufacturers of industrial machinery use lost foam casting to produce durable and complex parts, including pump housings and gearboxes. The process’s ability to produce near-net-shape components minimizes machining and material waste.
Conclusion
Lost foam casting is a powerful technique for optimizing production efficiency in metal casting. Its ability to produce complex geometries, reduce machining requirements, and improve surface finish makes it an attractive option for various industries. By focusing on pattern quality, coating consistency, sand compaction, metal flow control, and cooling rates, manufacturers can maximize the benefits of lost foam casting and achieve higher production efficiency.
Table 2: Summary of Lost Foam Casting Benefits
Benefit | Description |
---|---|
Complex Geometries | Enables the creation of intricate and detailed cast parts. |
Reduced Machining | Minimizes the need for extensive post-casting machining. |
Material Savings | Eliminates waste material associated with traditional casting methods. |
Improved Surface Finish | Provides superior surface finish, reducing the need for additional finishing processes. |
Dimensional Accuracy | Ensures high precision and tight tolerances in cast components. |
By understanding and implementing best practices in lost foam casting, manufacturers can significantly enhance their production processes and achieve greater efficiency, ultimately leading to cost savings and improved product quality.