In the realm of defense and security, strength, reliability, and durability are paramount. Steel casting plays a vital role in meeting these stringent requirements, providing robust and dependable components for critical applications. This article delves into the significance of steel casting in the defense and security sectors, highlighting its contribution to ensuring the strength, reliability, and operational readiness of military equipment and security systems.
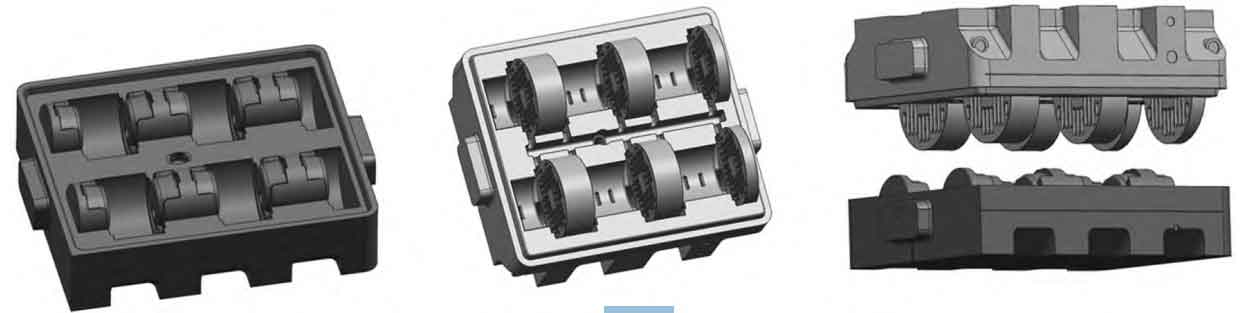
- Defense Applications: Steel casting finds extensive use in various defense applications, including armored vehicles, tanks, artillery systems, naval vessels, aircraft carriers, submarines, and missile systems. These applications demand components that can withstand high-impact forces, extreme temperatures, and corrosive environments. Steel castings offer exceptional strength, toughness, and resistance to wear, making them an ideal choice for defense equipment subjected to rigorous operational conditions.
- Reliability and Durability: Defense and security equipment must operate flawlessly in challenging environments and adverse conditions. Steel castings provide the required reliability and durability to withstand the rigors of combat, prolonged deployments, and exposure to harsh climates. The inherent properties of steel, such as high tensile strength, impact resistance, and fatigue resistance, ensure the longevity and effectiveness of defense systems.
- Precision and Dimensional Accuracy: Accuracy and precision are critical in defense and security applications to ensure optimal performance and interoperability. Steel casting processes, such as investment casting and precision machining, enable the production of complex geometries with tight tolerances. This precision ensures proper fitment, alignment, and compatibility of components, allowing for seamless integration into larger defense systems.
- Material Selection for Specialized Applications: The defense and security sectors often require specialized steel alloys to meet specific performance criteria. Depending on the application, factors such as ballistic resistance, heat resistance, and magnetic properties may be crucial. Steel casting allows for the selection and utilization of specific alloy compositions tailored to the unique requirements of defense equipment, enhancing their performance and functionality.
- Collaboration and Quality Assurance: The defense and security industries place a strong emphasis on collaboration and quality assurance throughout the steel casting process. Collaboration between defense contractors, casting experts, and materials engineers is essential to ensure that components meet strict specifications and standards. Rigorous quality control measures, including non-destructive testing, mechanical testing, and inspection protocols, are implemented to guarantee the integrity and reliability of castings.
- Advancements and Future Innovations: Advancements in steel casting techniques, materials, and manufacturing technologies continue to drive innovation in the defense and security sectors. Additive manufacturing, robotics, and automation are transforming the casting process, enabling faster prototyping, increased production efficiency, and improved component performance. The integration of digital twins, simulations, and data analytics further enhances the design, production, and maintenance of defense equipment.
Steel casting plays a vital role in ensuring the strength, reliability, and durability of defense and security equipment. From armored vehicles to naval vessels, steel castings provide the necessary characteristics to withstand the demanding operational environments encountered in the defense sector. With ongoing advancements in materials, processes, and quality control measures, steel casting continues to evolve, enabling the development of cutting-edge defense systems that safeguard national security and contribute to global stability.