Chapter 1: The History and Tradition of Casting China
Casting has a long and rich history in China, dating back thousands of years. The country’s casting tradition is deeply intertwined with its cultural, artistic, and technological developments. Here’s an overview of the history and tradition of casting in China:
Bronze Age Casting:
China is renowned for its ancient bronze casting culture, which emerged during the Shang Dynasty (16th to 11th century BCE). During this period, intricate bronze vessels, weapons, and ritual objects were cast using the “lost-wax” method. The bronze artifacts from this era reflect not only advanced metallurgical techniques but also the social and religious significance of casting in Chinese society.
Artistic Expression:
Bronze casting in ancient China was not merely a utilitarian process; it was also an artistic endeavor. Elaborately designed and decorated bronze vessels, often featuring intricate patterns, animal motifs, and inscriptions, served both practical and symbolic purposes. These artifacts were used for rituals, ceremonies, and as symbols of power and authority.
Casting Techniques:
Chinese bronze casting utilized advanced techniques for the time, including the “piece-mold” method, where molds were assembled from multiple parts, allowing for complex shapes. Skilled craftsmen and artisans employed these techniques to create remarkable pieces that showcased the sophistication of ancient Chinese metallurgy.
Continuity and Evolution:
Bronze casting traditions continued to evolve throughout Chinese history, with each dynasty contributing to the art form. The Zhou Dynasty (1046–256 BCE) saw the refinement of casting techniques, while the Ming (1368–1644) and Qing (1644–1912) Dynasties produced exquisite bronze sculptures, incense burners, and other ornamental objects.
Casting in Other Materials:
While bronze casting held a prominent place in Chinese culture, other materials were also cast for artistic and utilitarian purposes. Terracotta figurines, ceramic vessels, and jade carvings were cast using techniques similar to those used in metal casting.
Modern Casting Techniques:
In the modern era, China has embraced a wide range of casting methods beyond traditional bronze casting. Iron, steel, aluminum, and other metals are cast to create industrial and consumer goods, machinery parts, and more.
Cultural Significance:
Casting in China goes beyond utilitarian and artistic purposes; it carries cultural and historical significance. The ancient bronze vessels and sculptures not only provide insights into technological achievements but also offer a glimpse into the values, beliefs, and artistic sensibilities of past civilizations.
Casting as Craftsmanship:
Traditional casting techniques have been preserved in various parts of China, with skilled artisans continuing to create bronze, iron, and other metal artifacts. These craftsmen are custodians of a legacy that reflects the country’s cultural heritage.
Modern Interpretations:
Contemporary Chinese artists continue to draw inspiration from the country’s casting traditions. They blend traditional techniques with modern aesthetics, creating a bridge between the past and the present.
In summary, casting has played a profound role in China’s history and culture. From the ancient bronze vessels of the Shang Dynasty to the modern industrial applications, casting reflects China’s technological prowess, artistic achievements, and enduring traditions.
Chapter 2: The Current Situation of Casting China
Scale and Output Value:
China has one of the largest casting industries in the world, encompassing a wide range of metal casting processes such as sand casting, investment casting, die casting, and more. The industry caters to various sectors, including automotive, aerospace, construction, energy, and consumer goods.
In 2020, China was the world’s leading producer of castings, generating a significant portion of the global casting output. The annual casting production was estimated to be in the tens of millions of metric tons, which represented a substantial portion of the global casting industry’s output.
Market Share:
China’s dominance in the casting industry has led to a significant market share in terms of both production and consumption. The country’s casting products are exported to various countries around the world, contributing to its global market share. China’s casting exports are driven by competitive pricing, a vast industrial base, and improvements in manufacturing technologies.
Industry Trends and Challenges:
In recent years, China’s casting industry has faced challenges and opportunities:
- Environmental Concerns: The casting industry, like other heavy industries, has faced scrutiny due to its environmental impact. China has been working on improving environmental regulations and practices within its industries, including casting, to reduce pollution and promote sustainable practices.
- Technological Advancements: China has been investing in advanced casting technologies to enhance the quality and efficiency of its products. This includes the adoption of digitalization, automation, and process optimization to improve product consistency and reduce waste.
- Global Competition: While China has a substantial market share, it faces competition from other countries with established casting industries. Countries with advanced manufacturing capabilities and expertise in specialized casting processes may pose challenges to China’s dominance.
- Quality Improvements: Chinese manufacturers have been working on improving the quality and precision of their casting products to meet the stringent requirements of industries like aerospace and automotive. This involves investing in precision casting techniques and quality control measures.
- Diversification of Applications: The casting industry has been diversifying its applications beyond traditional sectors. For instance, casting plays a role in the production of renewable energy equipment like wind turbines and solar panels.
Given the dynamic nature of the global economy, I recommend consulting more recent sources, such as industry reports, government publications, and news articles, to obtain the latest information on China’s casting industry, including its scale, output value, and market share.
Chapter 3: From Traditional Craftsmanship to High-Tech Production
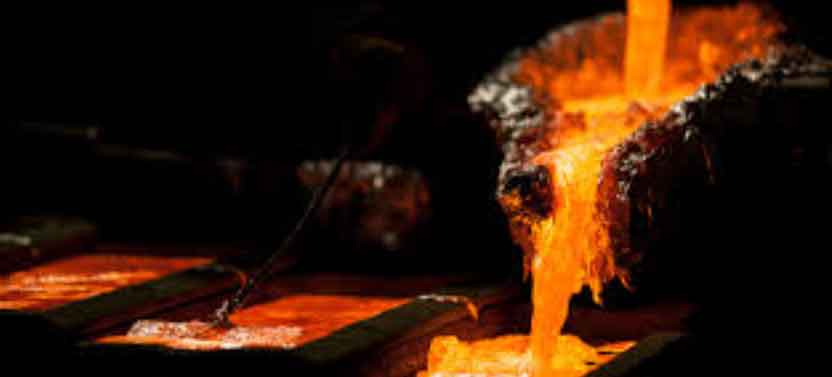
China has a rich history of craftsmanship and traditional production techniques that have evolved over centuries. However, in recent years, the country has also embraced high-tech production methods, combining traditional craftsmanship with modern technology to enhance productivity and efficiency. This transition has allowed China to become a global manufacturing powerhouse, producing a wide range of goods for both domestic and international markets.
Traditional craftsmanship has long been a significant part of Chinese culture and heritage. Skilled artisans have passed down their knowledge and techniques through generations, creating exquisite handmade products. From delicate porcelain and intricately carved wooden furniture to silk weaving and embroidery, China’s traditional craftsmanship has been highly regarded worldwide.
With the advent of modern technology and globalization, China recognized the need to adapt its production methods to meet the demands of the rapidly changing market. The government implemented policies and invested heavily in infrastructure, research and development, and education to foster innovation and technological advancements.
As a result, China has seen a significant shift towards high-tech production in various industries. Advanced manufacturing techniques, such as automation, robotics, and computer-aided design and manufacturing (CAD/CAM), have been integrated into traditional production processes. This has led to increased precision, speed, and scalability in manufacturing, allowing China to produce goods on a massive scale while maintaining quality standards.
China’s high-tech production capabilities are particularly evident in sectors such as electronics, automotive manufacturing, and telecommunications. The country has become a global leader in electronics manufacturing, producing a wide range of consumer electronics, including smartphones, tablets, and laptops. Chinese companies like Huawei, Xiaomi, and Lenovo have gained international recognition for their technological innovations.
Moreover, China has also made significant strides in the development of advanced materials and cutting-edge technologies. For instance, in the field of 3D printing, Chinese companies have made remarkable progress, using additive manufacturing techniques to create complex components and prototypes with precision and efficiency.
In addition to high-tech manufacturing, China has also embraced digitalization and e-commerce, revolutionizing the way products are marketed and sold. Online marketplaces, such as Alibaba’s Taobao and JD.com, have provided a platform for small-scale artisans and craftsmen to showcase their products to a global audience, bridging the gap between traditional craftsmanship and modern consumer preferences.
While China’s transition from traditional craftsmanship to high-tech production has brought many benefits, it has also raised concerns about the impact on traditional artisans and cultural heritage. Efforts are being made to strike a balance between embracing technological advancements and preserving traditional craftsmanship. Government initiatives, educational programs, and cultural preservation projects aim to support and promote traditional crafts while integrating them with modern production methods.
In conclusion, China’s journey from traditional craftsmanship to high-tech production showcases its adaptability and resilience in the face of changing market dynamics. By combining traditional skills with advanced manufacturing techniques, China has become a global manufacturing powerhouse. This transition has not only enhanced productivity and efficiency but also opened up new opportunities for artisans and craftsmen to showcase their skills in the digital age.
Chapter 4: The Technology Progress in Casting China
China has made significant progress in casting technology over the years, showcasing advancements in various aspects such as the application of new materials, the implementation of automated production lines, and the adoption of digital manufacturing techniques. Here’s an overview of China’s progress in these areas:
Application of New Materials:
- High-Performance Alloys: China has been actively researching and applying high-performance alloys such as titanium, nickel-based superalloys, and advanced aluminum alloys for specialized casting applications. These materials offer improved strength, corrosion resistance, and high-temperature capabilities.
- Metal Matrix Composites: China has explored the use of metal matrix composites (MMCs) in casting, which combine metals with ceramic reinforcements. These composites offer enhanced mechanical properties and can be tailored for specific applications like aerospace components.
- Advanced Ceramics: China has focused on casting advanced ceramic materials, including silicon carbide (SiC) and alumina, for applications requiring extreme wear resistance, high-temperature stability, and electrical insulation.
Automated Production Lines:
- Robotics and Automation: Chinese foundries have adopted robotics and automation for various casting processes, including pattern assembly, mold handling, core production, and even pouring. These technologies enhance efficiency, reduce human error, and improve workplace safety.
- Automated Inspection: Automated inspection systems, including visual inspection and non-destructive testing (NDT) techniques, are being integrated into casting processes to ensure consistent quality and detect defects more effectively.
- Data-Driven Manufacturing: Real-time monitoring and data collection from automated production lines enable manufacturers to identify process inefficiencies, optimize parameters, and make informed decisions for continuous improvement.
Digital Manufacturing:
- Additive Manufacturing (3D Printing): China has been investing in additive manufacturing technologies for creating intricate casting patterns, molds, and even complex metal components. This approach reduces lead times, enables rapid prototyping, and allows for more intricate designs.
- Simulation and Modeling: Digital simulations using computer-aided design (CAD) and computer-aided engineering (CAE) software help optimize casting processes, predict defects, and improve the efficiency of the overall manufacturing process.
- Digital Twin: Implementing digital twin concepts, Chinese foundries create virtual replicas of the casting process and monitor real-time data to identify deviations, optimize operations, and enhance overall quality.
- Supply Chain Integration: Digital platforms are being utilized to streamline the entire casting supply chain, from design and simulation to material sourcing, production, and delivery.
China’s progress in casting technology is a result of strategic investments in research and development, collaboration between academia and industry, and a commitment to technological innovation. These advancements contribute not only to China’s domestic industries but also to its global competitiveness in the field of manufacturing and casting technology.
Chapter 5: The Geographical Distribution of Casting China Industry
China’s casting industry is distributed across various regions, each with its own unique characteristics and specialties. Here’s an overview of the main production regions and their characteristics within China’s casting industry:
- Eastern Coastal Region: This region, including provinces like Jiangsu, Zhejiang, and Shandong, is known for its well-established industrial infrastructure and access to shipping ports. It hosts a wide range of casting foundries producing automotive components, machinery parts, and consumer goods. The region’s proximity to export hubs makes it a key player in the global casting supply chain.
- Northeastern Region: Comprising provinces like Liaoning and Jilin, this region historically had a strong heavy industry focus, including casting. While facing economic restructuring, it still contributes to casting production, especially for components used in mining equipment, railways, and heavy machinery.
- Central Region: Provinces like Henan and Hubei are part of the central region. They are increasingly emerging as casting hubs, benefiting from their strategic location, transport networks, and growing industrial base. Casting in this region includes a diverse range of components for industries such as agriculture, construction, and energy.
- Southern Region: Guangdong and Fujian provinces in the southern region are known for their electronics, consumer goods, and high-tech industries. Casting here focuses on intricate components used in electronics, telecommunications, and precision machinery.
- Western Region: Provinces like Sichuan and Chongqing are part of the western region. While not traditionally strong in casting, they have been developing their casting capabilities to support the growing demand for machinery and equipment in the region. Casting in this area often targets local industries’ specific needs.
- North China: Provinces such as Hebei and Shanxi are part of the northern region. These provinces are known for their historical importance in China’s industrial development and continue to produce a variety of castings for industries including automotive, construction, and machinery.
- Specialized Production Bases: In addition to the main regions, China has established specialized production bases. For instance, Ningbo in Zhejiang is known for automotive components, while Dalian in Liaoning is renowned for its heavy machinery castings. These areas leverage local resources and expertise to specialize in specific casting sectors.
Characteristics of Each Region:
- Eastern Coastal Region: Export-oriented, advanced technology, diverse industries.
- Northeastern Region: Historical heavy industry base, transitioning to new industries.
- Central Region: Emerging industrial base, focus on agriculture and construction machinery.
- Southern Region: High-tech industries, precision casting, consumer goods.
- Western Region: Developing casting capabilities to support local industries.
- North China: Historical industrial importance, varied casting applications.
- Specialized Production Bases: Niche expertise, focused production for specific industries.
China’s casting industry’s geographical distribution reflects the country’s diverse economic landscape and strategic focus on industrial development. The growth of these regions is influenced by factors such as infrastructure, transportation, labor availability, local resources, and government policies aimed at promoting industrial growth and innovation.
Chapter 6: Understand the different casting methods used in casting China
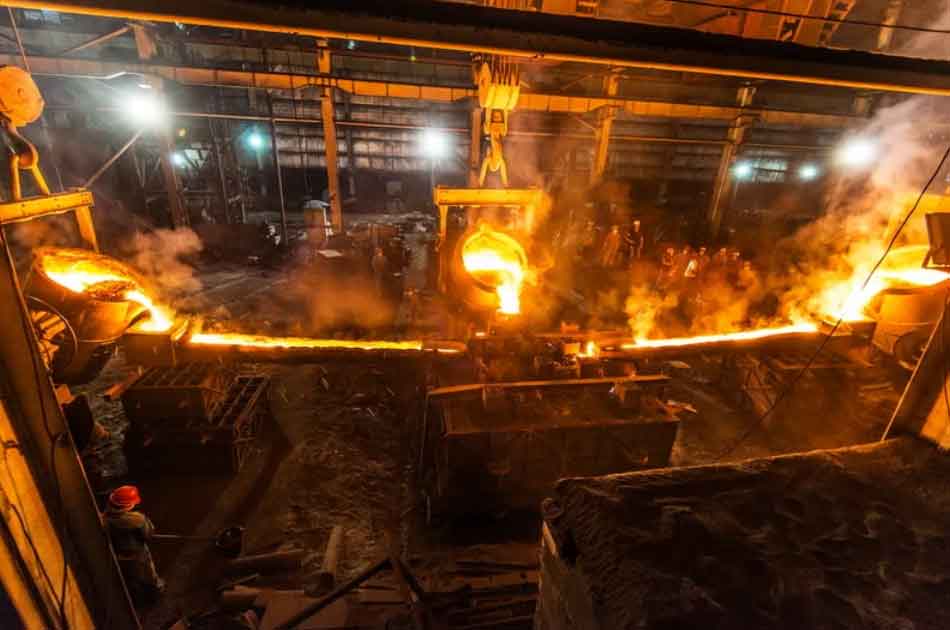
China employs various casting methods to meet the diverse needs of its manufacturing industries. Here’s an overview of the different casting methods used in China, along with their characteristics:
- Sand Casting: Sand casting is widely used in China for its versatility and suitability for various metals. It involves creating a mold using a mixture of sand and a binder around a pattern. Molten metal is then poured into the mold, which is broken to reveal the casting. Sand casting is cost-effective and suitable for both small and large parts with complex geometries.
- Die Casting: Die casting is a precise method used for producing high-quality metal parts. Molten metal is forced into a mold (die) under high pressure. China is a significant player in aluminum and zinc die casting, producing components for automotive, electronics, and consumer goods. Die casting offers tight tolerances, excellent surface finish, and high production rates.
- Lost Foam Casting: Lost foam casting (LFC) involves creating foam patterns coated with refractory materials. These patterns are embedded in sand and replaced by molten metal during casting. LFC is used for intricate parts and is particularly popular in automotive and machinery industries due to its potential for near-net shape casting and reduced need for post-processing.
- Investment Casting (Precision Casting): Investment casting, known as “precision casting” in China, is used to create high-precision parts with fine details. A wax pattern is created and covered in ceramic, then the wax is melted out, leaving a mold. Molten metal is poured into the mold, and the ceramic is removed. This method is suitable for aerospace, automotive, and medical industries.
- Centrifugal Casting: Centrifugal casting is employed in China for producing cylindrical parts like pipes and tubes. Molten metal is poured into a rotating mold, which helps distribute the metal evenly and reduces defects. This process ensures a dense structure and can yield better mechanical properties.
- Continuous Casting: Continuous casting is used to create long, continuous shapes like bars, rods, and strips. Molten metal is poured into a water-cooled mold, and the solidified metal is continuously withdrawn. This method is common for producing steel, aluminum, and other metals in bulk.
- Shell Molding: Shell molding, also known as shell casting, involves creating thin-shell molds using a resin-coated sand mixture. These molds offer better surface finish and dimensional accuracy compared to traditional sand casting. Shell molding is used for smaller parts with intricate details.
- V-Process Casting: The V-process involves creating a mold using a vacuum and a special plastic film pattern. Molten metal is poured into the mold, and the film is later stripped away. This method is known for producing high-quality castings with excellent surface finish and reduced defects.
- Continuous Casting: Continuous casting is a method used to produce long and semi-finished products like billets, slabs, and blooms. Molten metal is poured into a water-cooled mold, solidifying into the desired shape as it moves through the process.
Each casting method has its own strengths and weaknesses, making them suitable for different applications and industries. China’s casting industry has harnessed these methods to cater to a wide range of manufacturing needs, from automotive and aerospace to consumer goods and industrial equipment.
Chapter 7: Understand the application of casting China in different fields
Casting plays a crucial role in various industries in China, contributing to the production of a wide range of components and products. Here’s an overview of how casting is applied in different fields within China:
- Automotive Manufacturing: Casting is extensively used in the automotive industry in China. Engine blocks, cylinder heads, transmission cases, and various other components are produced using casting methods. Aluminum and iron casting are common, and processes like die casting and sand casting are utilized. China’s booming automotive market has led to a significant demand for high-quality cast components for vehicles.
- Mechanical Engineering: Casting is vital to mechanical engineering in China, as it produces components for various machinery and equipment. Gears, pulleys, shafts, and housings are commonly cast using methods like sand casting and precision casting. These components are used in industrial machinery, construction equipment, agricultural machinery, and more.
- Energy Industry: Casting is applied in the energy sector to produce components for power generation and distribution. Turbine blades, casings, boiler parts, and other components are cast to withstand high temperatures and extreme conditions. The energy industry in China relies on casting to create critical components for thermal power plants, hydroelectric facilities, and wind turbines.
- Aerospace and Aviation: The aerospace industry in China uses casting for manufacturing components that meet stringent requirements for quality and performance. Precision casting methods like investment casting are employed to produce turbine blades, engine casings, and other critical parts for aircraft and rockets.
- Railway and Transportation: Casting is applied in the railway sector to create components such as brake systems, couplings, wheel hubs, and structural parts for trains and rail systems. The durable and wear-resistant properties of cast components make them suitable for heavy-duty transportation applications.
- Construction and Infrastructure: Casting is used in the construction industry to produce parts for building and infrastructure projects. Cast iron and steel components are used in architectural hardware, bridges, tunnels, and other large-scale structures.
- Electronics and Consumer Goods: The electronics and consumer goods industries utilize casting for producing intricate components used in appliances, electronics, and other consumer products. Die casting and other precision methods are employed to create lightweight and precise parts.
- Marine and Shipbuilding: Casting contributes to the marine and shipbuilding industries by producing components like propellers, rudders, marine fittings, and structural elements. The corrosion-resistant properties of cast materials are crucial in marine environments.
- Mining and Heavy Machinery: Casting is applied to create robust components for mining equipment, construction machinery, and heavy industrial machines. Parts like buckets, buckets teeth, and structural components are produced using casting techniques.
- Medical Equipment: Casting is used in the production of medical equipment components, such as imaging systems, dental devices, and surgical instruments.
Casting serves as the backbone of China’s manufacturing sector, providing essential components for various industries. The country’s expertise in casting methods, combined with its industrial capabilities, has positioned China as a significant player in the global manufacturing supply chain.
Chapter 8: The position of China casting industry in the global casting industry
The China casting industry holds a prominent position in the global casting landscape, making significant contributions to the worldwide manufacturing supply chain. Several factors contribute to China’s position in the global casting industry:
- Production Volume: China is the world’s largest producer of castings in terms of sheer volume. The country’s vast manufacturing capabilities, extensive industrial infrastructure, and skilled labor force enable it to produce a wide range of cast components for various industries.
- Diverse Casting Capabilities: China offers a diverse range of casting methods, including sand casting, die casting, investment casting, and more. This versatility allows the country to cater to the demands of different industries, from automotive and aerospace to energy and consumer goods.
- Supply Chain Integration: China’s casting industry is deeply integrated into the global manufacturing supply chain. Many multinational companies source cast components from China due to its competitive pricing, availability of raw materials, and extensive manufacturing networks.
- Export-Oriented Production: China’s casting industry is known for its export-oriented production. The country produces cast components for a wide range of industries and exports these components to countries around the world, contributing to its global influence.
- Cost-Effectiveness: China’s relatively lower labor and production costs compared to some other developed countries make it an attractive destination for outsourcing casting production. This cost-effectiveness has contributed to the expansion of the country’s casting industry.
- Technological Advancements: China’s casting industry has embraced technological advancements, including automation, digital manufacturing, and innovative casting techniques. This has enhanced the quality, precision, and efficiency of cast component production.
- Investment in Research and Development: China’s focus on research and development has led to advancements in casting materials, methods, and processes. This continuous improvement enhances the industry’s competitiveness on the global stage.
- Global Partnerships: Many international companies have established partnerships and joint ventures with Chinese casting manufacturers to leverage the country’s manufacturing capabilities and gain access to its extensive market.
- High Production Capacity: China’s casting industry benefits from its large-scale production capacity, enabling it to meet both domestic and international demands for cast components across various industries.
While China’s casting industry enjoys a strong position globally, it also faces challenges such as quality control, environmental concerns, and maintaining technological leadership. The industry’s ability to address these challenges while continuing to innovate and provide high-quality products will determine its continued influence in the global casting market.
Chapter 9: Technological innovation and research and development in the field of casting China
China’s casting industry has been actively investing in technological innovation and research and development to enhance its capabilities, improve quality, and remain competitive on the global stage. Here are some key areas of progress in which China has made advancements:
1. New Materials Development: China’s casting industry has been researching and developing new materials to meet the evolving needs of various industries. This includes the development of high-performance alloys, metal matrix composites (MMCs), advanced ceramics, and other materials with enhanced properties such as strength, corrosion resistance, and high-temperature stability.
2. Digital Manufacturing and Industry 4.0: China has been adopting digital manufacturing technologies to optimize casting processes. This involves the use of data analytics, sensors, internet of things (IoT) devices, and artificial intelligence (AI) to monitor and control the casting process in real time. Industry 4.0 principles are being applied to improve efficiency, reduce defects, and enhance overall quality.
3. Additive Manufacturing (3D Printing): China is exploring additive manufacturing techniques for casting applications. 3D printing is being used to create intricate casting patterns, molds, and even some metal components. This approach allows for rapid prototyping, reduced lead times, and the production of complex geometries that might be challenging using traditional methods.
4. Simulation and Modeling: The use of computer-aided design (CAD) and computer-aided engineering (CAE) software is becoming more prevalent in China’s casting industry. Casting simulations help optimize process parameters, predict defects, and reduce the need for trial and error. These simulations improve efficiency and contribute to higher-quality castings.
5. Environmentally Friendly Practices: China’s casting industry is working on reducing its environmental footprint by adopting cleaner production practices. This includes efforts to optimize energy consumption, reduce emissions, and implement sustainable waste management practices.
6. Advanced Tooling and Equipment: Investments are being made in state-of-the-art equipment for casting processes. Advanced robotics, automated inspection systems, and high-precision machining tools are being integrated into casting lines to improve consistency, precision, and efficiency.
7. Collaboration and Research Centers: China has established research and development centers, institutes, and collaborations between academia, industry, and government bodies. These initiatives aim to drive innovation, provide specialized training, and foster collaboration in advancing casting technologies.
8. Quality Control and Inspection Techniques: Advanced non-destructive testing (NDT) techniques, such as digital radiography, ultrasonic testing, and magnetic particle inspection, are being adopted to ensure the quality of cast components. These techniques help identify defects and irregularities in a non-invasive manner.
9. High-Performance Applications: China’s casting industry is focusing on applications that demand high performance, such as aerospace, automotive, and energy sectors. The development of advanced casting methods and materials is tailored to meet the specific requirements of these industries.
China’s commitment to technological innovation and research and development is evident in its efforts to enhance casting methods, improve product quality, and address environmental concerns. By embracing these advancements, China’s casting industry aims to maintain its position as a global leader in manufacturing and casting technology.
Chapter 10: The future trends of casting China
Some potential trends for China’s casting industry could include:
- Digital Manufacturing and 3D Printing: The integration of digital technologies like 3D printing and additive manufacturing into the casting process could lead to more precise and efficient production. This could allow for complex geometries that are difficult to achieve through traditional casting methods. China has been investing in research and development in 3D printing technologies, and this could have an impact on the casting industry’s future.
- Intelligent Manufacturing and Automation: The adoption of intelligent manufacturing practices, including automation, artificial intelligence, and the Internet of Things (IoT), could lead to increased efficiency, reduced waste, and improved quality control. Smart manufacturing processes can optimize production flows, monitor equipment performance, and make real-time adjustments to enhance productivity.
- Green Environmental Protection: Environmental concerns have been growing globally, and the casting industry is no exception. China has been making efforts to shift towards greener and more sustainable manufacturing practices. This could involve adopting cleaner energy sources, reducing emissions, and implementing more efficient waste management techniques.
- Advanced Materials and Alloys: Research and development into advanced casting materials and alloys can lead to improved performance characteristics, such as higher strength, better corrosion resistance, and enhanced heat resistance. China’s focus on technological innovation could drive advancements in this area.
- Precision Casting and Quality Improvement: Precision casting, also known as investment casting, allows for the creation of intricate and high-precision parts. As industries demand higher quality and tighter tolerances, precision casting could become more important in various sectors, including aerospace, automotive, and medical equipment.
- International Collaboration and Globalization: China’s casting industry has been expanding its global reach, engaging in international partnerships and collaborations. This trend could continue as China seeks to become a global leader in manufacturing and exports of cast components.
- Skill Development and Workforce Training: As technologies evolve, the industry will require a skilled workforce capable of operating and maintaining advanced equipment. Training programs and education in casting-related fields could become more important to ensure the industry’s growth.
- Regulatory Compliance and Standards: With the emphasis on green manufacturing and environmental protection, adherence to domestic and international standards for quality, safety, and environmental impact could shape the industry’s future trajectory.
Remember that the actual trends and developments might differ from these predictions, and it’s essential to refer to the most recent sources and industry reports to get accurate insights into the current state of China’s casting industry.