The anvil produced by steel castings manufacturer is an important supporting component of forging hammers, and its working process is frequently subjected to heavy load impacts, resulting in poor working conditions. Therefore, strict quality requirements are placed on it. The structure of the cast steel anvil is simple, and during the production process, it is necessary to avoid the occurrence of shrinkage and crack defects, reduce shrinkage porosity and aggregation, and reduce sand holes and inclusions. The production of casting products by steel castings manufacturer generally requires processes such as process design, mold making, and product trial production before product development and delivery can be completed. At present, numerical simulation technology is used to analyze the casting process of steel castings manufacturer. With the help of foam processing, 3D printing technology and other methods, patterns and sand molds can be produced quickly, thereby saving costs and improving development efficiency.
The anvil is made of ZG45, with simple structure and single piece production, so it is decided to use foam to make the pattern, analyze the casting filling and solidification process of the steel castings manufacturer with the help of numerical simulation technology, optimize the casting process of the steel castings manufacturer, and ensure product quality.
1. Structural characteristics and technical requirements of cast steel anvil base
1.1 Structural characteristics of cast steel anvil seat
The anvil produced by steel castings manufacturer is a plate type structure composed of three parts spliced into a whole, including an external dovetail structure and an internal dovetail structure. The contour size of anvil products produced by steel castings manufacturer is 1000 mm × 720 mm × 300 mm, weighing approximately 1.3 tons. The structure is shown in Figure 1.
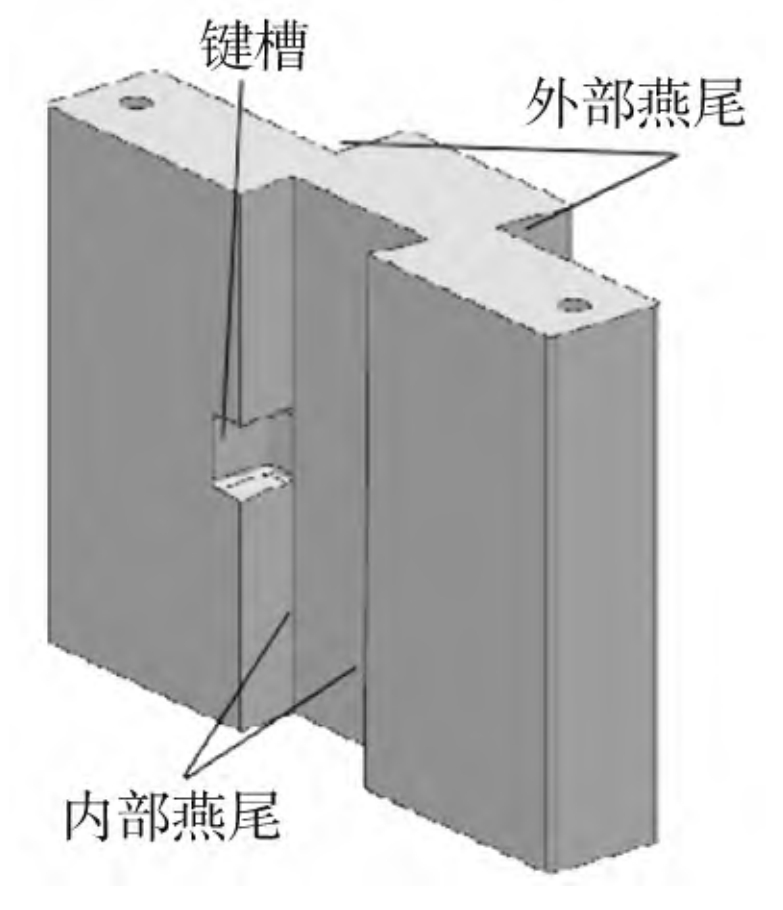
1.2 Technical requirements for cast steel anvils
The material of the anvil produced by the steel castings manufacturer is ZG45, and the chemical composition requirements are shown in Table.
C | Si | Mn | S | P | Cr | Mo | |
0.42~0.50 | 0.17~0.37 | 0.50~0.80 | ≤0.035 | ≤0.035 | 0~0.25 | 0~0.25 | 0~0.30 |
The key positions of the anvil produced by steel castings manufacturer are the inner dovetail, outer dovetail, and keyway. These areas are not allowed to have casting defects such as shrinkage, porosity, porosity, sand inclusion, slag inclusion, cracks, etc. The anvil produced by a steel castings manufacturer requires quenching and tempering treatment, and the hardness of the treated body is HB205~240.
2. Casting process design for steel anvil base
The anvil produced by the steel castings manufacturer this time is a single piece production. Based on the analysis of the drawings and technical requirements, it is found that its structure is relatively simple, and all surfaces of the anvil blank produced by the steel castings manufacturer need to be machined. In view of the above characteristics, it is preferred to use foam for pattern making, which can improve the product development efficiency and reduce the production cost by eliminating the production link of the mold.
2.1 Selection of parting surface
The foam sample preparation and ester hardened sodium silicate sand molding process are used to make the mold. Compared with the lost foam casting method, because there is no negative pressure, the sand mold depends on the binder to harden, and its permeability is low. The foam pattern must be removed from the sand mold before box assembly, otherwise the foam pattern will decompose and produce a large amount of gas during the pouring process, resulting in a slow pouring speed, or even the gas will overflow from the runner, forming a reverse jet, which will eventually lead to product scrap. In the process design, the removal of foam pattern after sand mold hardening shall be considered, and the large section position shall be selected as far as possible for parting and mold parting. According to the structural characteristics of the anvil, two types of parting schemes can be selected: horizontal and vertical, as shown in Figure 2.
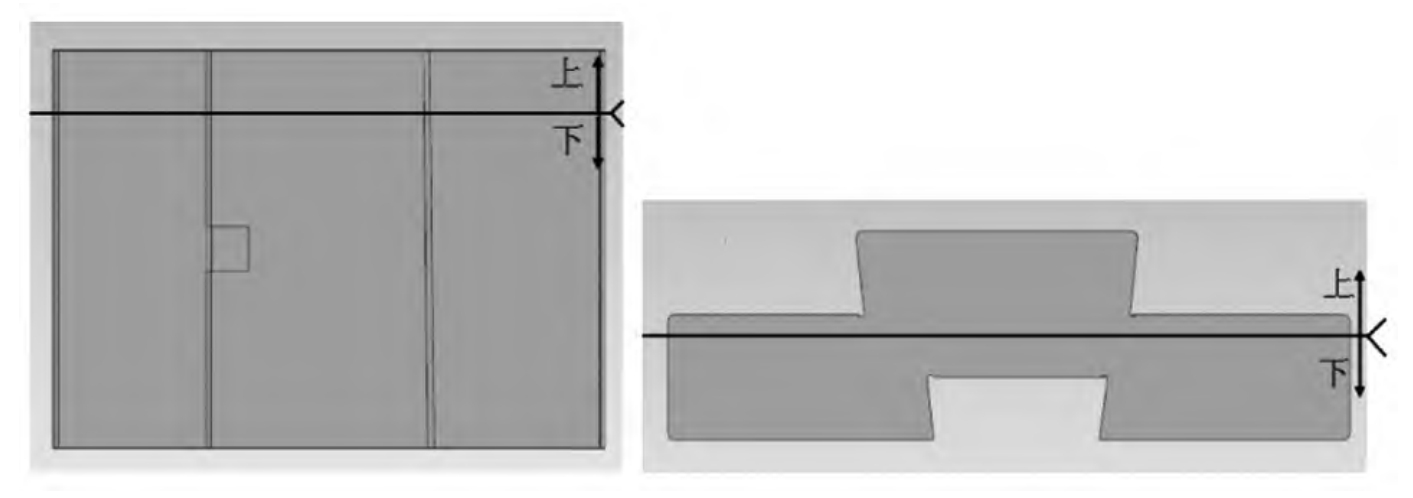
When vertically parting, the molten metal can be filled layer by layer from bottom to top, and the filling process is relatively smooth. Steel castings manufacturer also produce anvils, and the shrinkage deformation of the castings is relatively small. One or two risers can be placed on the upper part for filling. When horizontal parting is used, steel castings manufacturer produce anvil castings during the pouring process, with the large plane facing upwards, which can easily cause sand holes and air holes on the upper plane.
Considering the need for steel castings manufacturer to produce anvil castings for shrinkage, it is necessary to place a riser on the upper plane. According to the structure and wall thickness of the anvil castings produced by the steel castings manufacturer, three risers need to be placed, which reduces the yield of the process. And adopting the plan of placing a riser in the middle of the horizontal parting, steel castings manufacturer produce anvil castings with significant deformation. Based on the above analysis, the vertical classification scheme was ultimately chosen.
2.2 Processing allowance
The surface of the anvil blank product requires mechanical processing. Firstly, both the internal dovetail groove and the external dovetail groove are not cast, and the finished product is achieved by machining; Secondly, both the internal dovetail groove and the external dovetail are cast into non dovetail structures; Referring to GB/T 6414-1999, the mechanical machining allowance level is selected as H level, with a machining allowance of 8 mm; The removal process of foam pattern after molding is easy to damage the mold surface, and the pouring process is easy to cause sand holes in the steel castings manufacturer production anvil castings. Sand holes are easy to gather on the upper surface of the steel castings manufacturer production anvil castings. At the same time, the upper surface of the steel castings manufacturer production anvil castings is also a gas hole accumulation area, so the upper surface machining allowance is set to 18 mm.
2.3 Riser design
The aspect ratio of the anvil seat is less than 5, and it can be treated as a rod as a whole. Its modulus is 62 mm, and it can be supplemented by selecting a heating riser with a modulus greater than 75.4 mm for the solidification process of anvil seat castings produced by steel castings manufacturer. Using the existing riser of the enterprise, choose the FT400-S350 type heating insulation riser with a reference module of 83.1mm.
2.4 Selection of pouring positions and design of pouring systems
When vertical parting is used, the total height of the anvil castings produced by steel castings manufacturer is relatively high, making it easy to use a stepped pouring system to ensure a smooth filling process. At the same time, the stepped pouring system can also ensure that the upper metal liquid temperature of the anvil castings produced by steel castings manufacturer is high, which is conducive to the formation of a good temperature field in the production of anvil castings by steel castings manufacturer, and facilitates the smooth filling and shrinking of anvil castings.
2.5 Subsidies and Cold Iron Design
Using UG for 3D modeling of products, coupled analysis of the filling and solidification process of anvil castings produced by steel castings manufacturer using ProCAST casting simulation software. The material is set to ZG45, and the composition is taken as the middle value of the chemical composition range. The material properties parameters are calculated using the built-in function of ProCAST software. The casting mold is set to sand mold, the pouring temperature is set to 1565 ℃, the initial temperature of the sand mold is set to 20 ℃, and the pouring speed is 35 kg/s. The temperature field distribution during its solidification process is shown in Figure 3, and the shrinkage and porosity are shown in Figure 4. During the solidification process of the anvil, a large volume of isolated liquid phase zone is formed directly below the riser. Steel castings manufacturer producing anvil castings will produce obvious shrinkage and porosity defects in this area after solidification. This indicates that the feeding distance of the riser in the vertical direction is insufficient. Increasing the feeding distance of the riser can be achieved by setting subsidies on the side of the riser to extend the length of the riser area or by placing cold iron at the far end of the riser to increase the length of the end area. This study adopted a combination of subsidies and placement of cold iron. The initial casting process and casting blanks for producing anvil castings by steel castings manufacturer are shown in Figure 5.
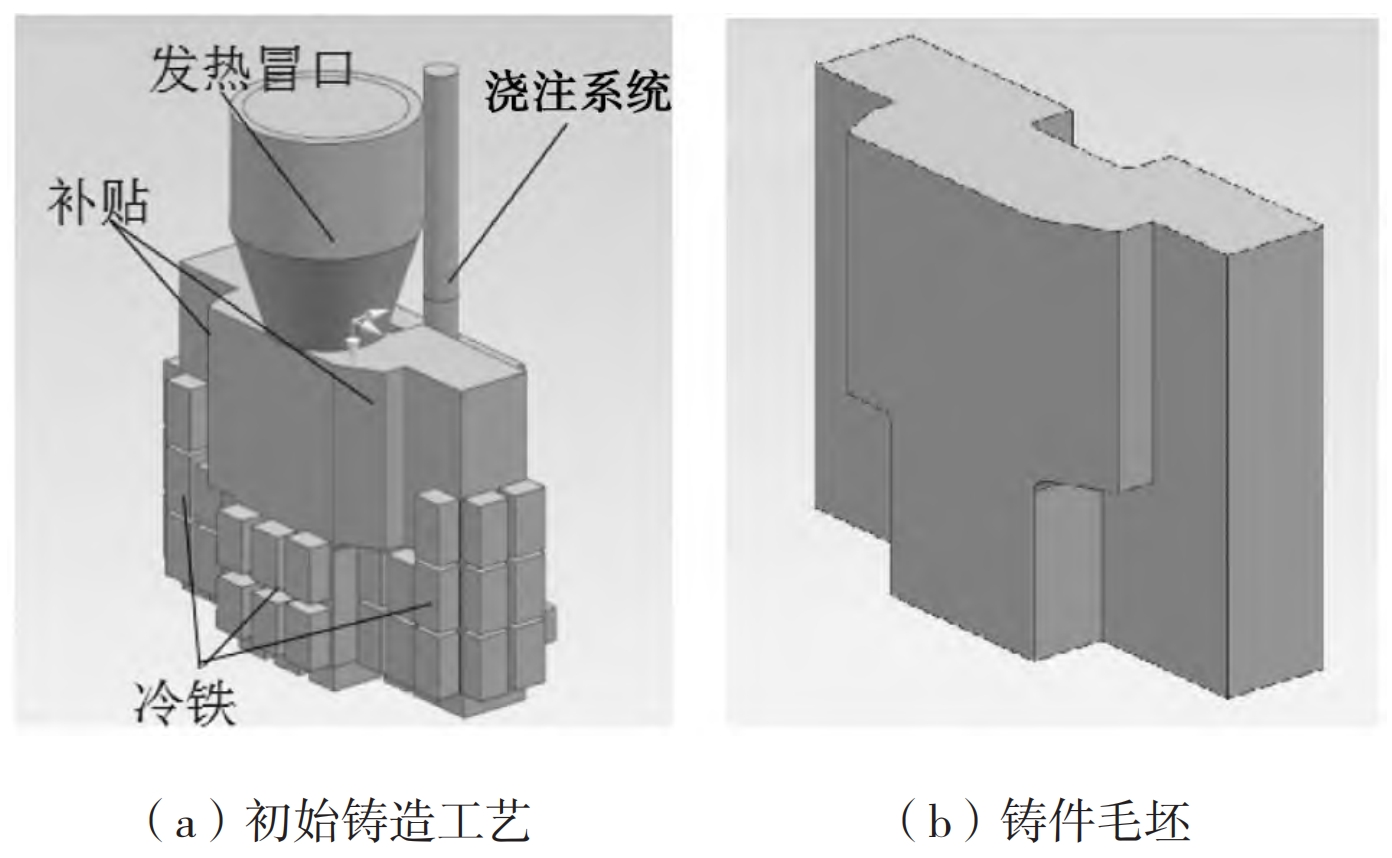
2.6 Feasibility analysis of initial casting process
Simulate the production anvil casting process of optimized steel castings manufacturer using ProCAST software. The thermal properties parameters and boundary conditions are the same as those set in 2.5.
2.6.1 Filling process
Figure 6 shows the numerical simulation results of the filling process of anvil castings produced by steel castings manufacturer. The anvil is first filled into the mold cavity through the two lower inner runners. As the pouring progresses, when the liquid level rises to be level with the upper inner runner, the metal liquid is filled into the mold cavity through the upper inner runner. During the filling process, there is a significant decrease in the temperature of the molten metal at the location where the cold iron is placed.
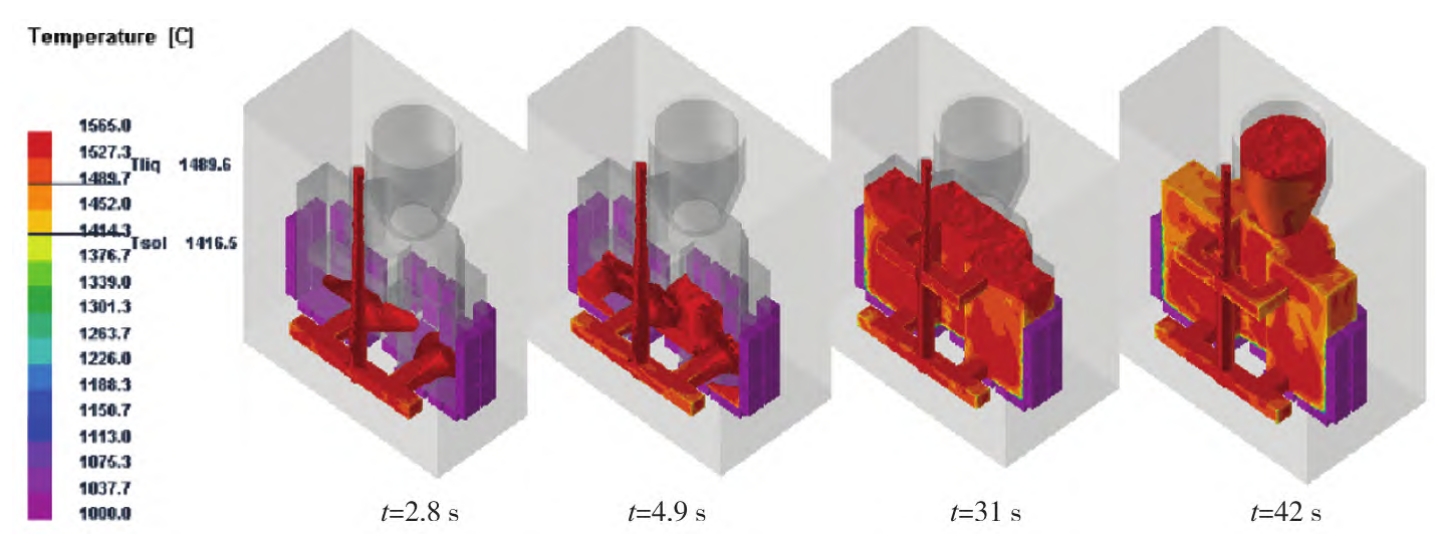
2.6.2 Solidification process
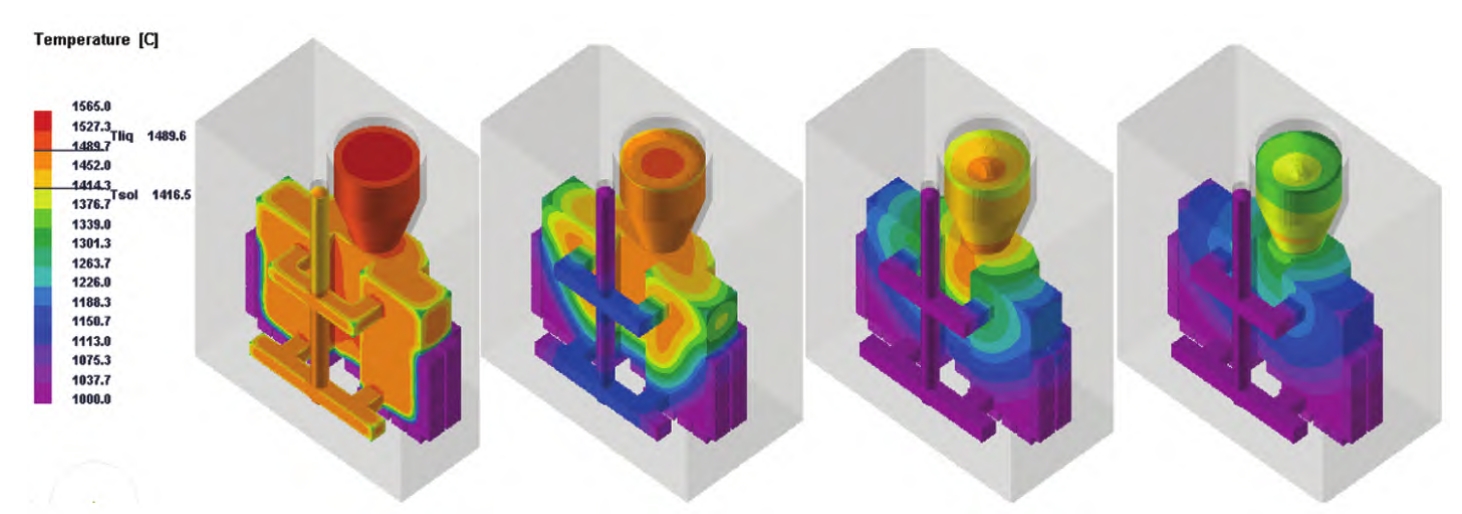
Figure 7 shows the temperature field distribution during the solidification process of anvil castings produced by steel castings manufacturer. Solidification first occurs at the location where the cold iron is placed, gradually solidifying from the bottom plane towards the riser direction, and finally the solidified part is at the riser position. During the solidification process, no isolated liquid phase zone was found, and the steel castings manufacturer production of anvil castings formed a temperature field distribution that was conducive to reducing defects. The distribution of shrinkage and porosity after casting solidification is shown in Figure 8, with defects concentrated in the sprue and riser. No defects were found in the production of anvil castings by steel castings manufacturer, and the solidification simulation effect is good. The production of anvil casting technology by steel castings manufacturer is feasible.
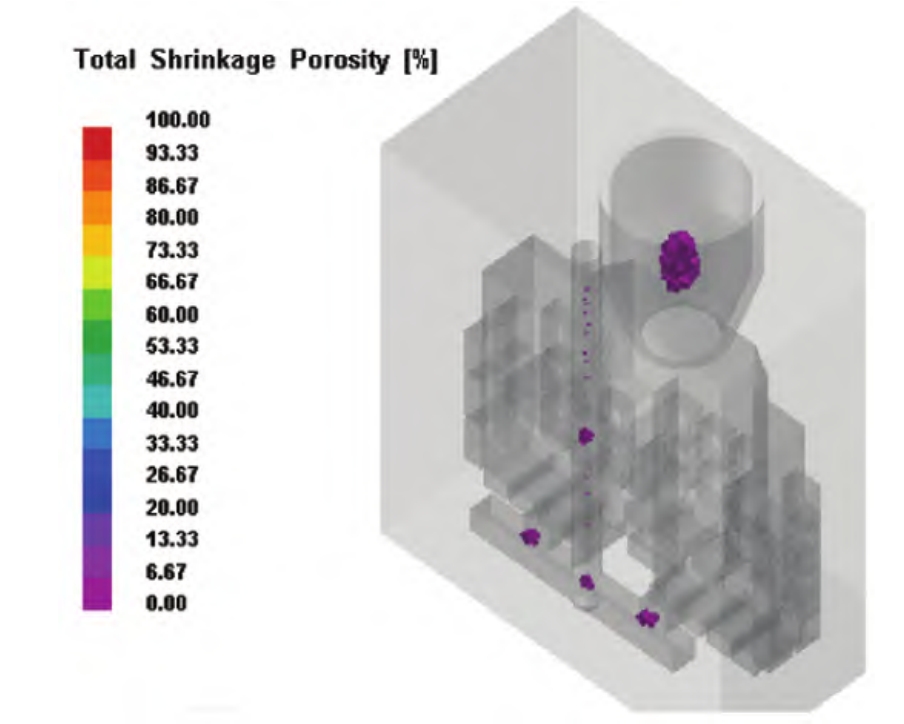