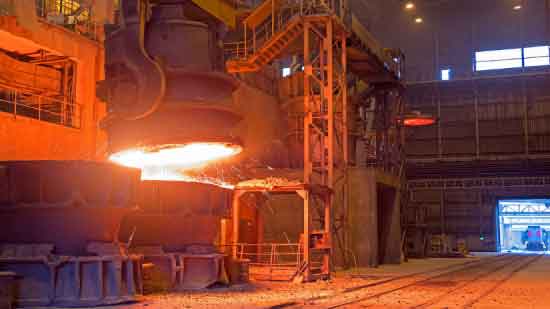
Steel sand casting is a versatile and widely used method for manufacturing complex components. However, it does come with certain challenges that need to be overcome to ensure successful production. Here are some common challenges in complex component manufacturing with steel sand casting and potential solutions to address them:
- Complex Geometry: Manufacturing components with intricate designs, thin walls, undercuts, or complex internal features can be challenging in steel sand casting. To overcome this challenge, advanced pattern-making techniques and precise mold design are essential. Using advanced technologies like computer-aided design (CAD) and computer-aided manufacturing (CAM) can help in creating intricate patterns and molds with high precision.
- Dimensional Accuracy: Achieving tight dimensional tolerances in complex components can be difficult due to the nature of the casting process. Shrinkage and distortion during solidification and cooling can lead to variations in dimensions. To address this, proper mold design, including appropriate allowances for shrinkage, and careful control of the casting process parameters such as pouring temperature and cooling rate, can help achieve desired dimensional accuracy.
- Casting Defects: Steel sand casting can be susceptible to various defects like porosity, inclusions, and surface imperfections. These defects can affect the mechanical properties and overall quality of the components. Implementing effective quality control measures, such as proper gating and riser design, ensuring proper mold compaction, using high-quality sand, and employing suitable melt treatment techniques, can help reduce defects and improve the casting quality.
- Heat Treatment Requirements: Some complex components may require specific heat treatment processes to achieve the desired mechanical properties. Heat treatment can help improve the strength, hardness, and wear resistance of the castings. Proper selection of heat treatment parameters, including temperature and duration, and effective post-casting processing, such as quenching and tempering, can ensure that the components meet the required specifications.
- Machining and Finishing: Complex components often require secondary operations like machining, surface finishing, and assembly. The challenge lies in maintaining the dimensional accuracy and surface quality during these processes. Employing advanced machining techniques, such as computer numerical control (CNC) machining, and utilizing skilled operators and inspection equipment can help ensure precise machining and finishing of complex components.
- Process Simulation and Optimization: Simulating the casting process using computer simulations can help identify potential issues and optimize the manufacturing parameters before actual production. Simulation tools can predict filling and solidification behavior, analyze thermal stresses, and optimize gating and riser designs. This allows for adjustments to be made in the design or process parameters to overcome challenges and improve casting quality.
- Collaboration and Expertise: Overcoming challenges in complex component manufacturing often requires collaboration between the foundry, designers, and engineers. Expertise in steel sand casting, combined with effective communication and collaboration, can help address design and manufacturing challenges, optimize the process, and achieve desired results.
By addressing these challenges through proper design considerations, process optimization, quality control measures, and collaboration between all stakeholders, steel sand casting can successfully produce complex components with the required dimensional accuracy, quality, and functionality.