High manganese steel has been used to make tram track ruts since its good wear resistance because of its good wear resistance, and almost all railway forks in the world have been made of this material for more than 100 years. However, with the development of society and the improvement of railway transportation speed, the use life of high manganese steel removal forks
Life puts forward higher requirements. In recent years, researchers have carried out a lot of research on how to improve the service life of high manganese steel forks. Among them, the addition of nitrogen to high manganese steel can not only refine the grain, but also inhibit the precipitation of grain boundary carbides, and its solid solution strengthening effect can not only improve the wear resistance, work hardening performance of the material, but also greatly improve the atmospheric corrosion resistance, so it has become a hot spot in this field.
Under conventional production conditions, the solubility of nitrogen in high manganese steel is not high, which has become a bottleneck that limits its performance and application range, so increasing the nitrogen content in high manganese steel has become an urgent difficulty to be solved in the metallurgical field. At present, there are two main production methods of high nitrogen and high manganese steel: one is pressure smelting and pressure casting; The second is to accelerate the solidification of molten steel and shorten casting
The solidification time of the piece reduces the nitrogen escape in the steel. Pressurized equipment, especially pressurized equipment under high temperature conditions, is more expensive, complex to operate, and dangerous, and foreign commercial high-nitrogen steel is basically smelted under pressure
Method production, high-pressure smelting and casting can not only increase nitrogen content, but also reduce component segregation. However, due to equipment technical conditions and cost restrictions, China’s metallurgical industry has not yet formed an industrial production line for pressure smelting and casting. Therefore, accelerating the solidification of molten steel, shortening the solidification time of castings, and reducing nitrogen evolution during the solidification process have become improved
An effective method for nitrogen content in high casting high manganese steel.
There are two main ways to accelerate the solidification of molten steel and shorten the solidification time of castings: First, reduce the superheat of molten steel to reduce the heat storage of molten steel
Yes; The second is to accelerate the cooling of molten steel, enhance the cooling performance of the mold, increase the heat exchange coefficient between molten steel and the outside world, and shorten the solidification time of the casting by suspension casting. Through the thermal analysis of the solidification process of molten steel, several methods to accelerate the cooling of molten steel are proposed, which significantly shortens the solidification time of molten steel, inhibits the evolution of nitrogen during the solidification process, and effectively improves the nitrogen content in high manganese steel.
1 Thermal analysis of molten steel solidification process
1 Calculation of molten steel casting temperature
Taking the typical composition of nitrogen-containing high manganese steel in a casting enterprise as an example, the main chemical composition (mass fraction) is: 0. 7% C, 18. 0% Mn、6. 0% Cr、0. 2% Al、0. 3% Si、0. 18% N、< 0. 02% S、< 0. 02% P, the rest is Fe. The phase diagram of this nitrogen-containing high manganese steel was calculated using FactSage software, as shown in Figure 1.
When the nitrogen mass fraction is 0. At 18%, the liquid temperature is 1 410 °C and the solid temperature is 1 290 °C. The reliability of the FactSage software calculation data was verified using empirical formula (1):
TM = 1 538 - 90[C]- 28[P]- 40[S]- 6. 2[Si]-1. 7[Mn]- 2. 6[Cu]- 5. 1[Al]- 2. 9[Ni]-17[Ti]- 1. 3[V]- 1. 5[Mo]- 1. 8[Cr]-1. 0[W]- 1. 7[Co]- 1 300[H]- 90[N]-100[B]- 65[O] ( 1)
Substituting the composition of nitrogenous high manganese steel into the formula (1), the melting point is calculated to be about 1 413 °C, which is calculated by FactSage software
Good match. When the material composition changes, FactSage software can quickly calculate the change in the solidification interval of molten steel with different elemental content to find the optimal composition of high manganese steel. The nitrogen-containing high manganese steel has a narrow solidification interval, is sensitive to the casting temperature of molten steel, and the casting overheating is too high, and the casting will form coarse grains and columns
Crystal structure, as well as shrinkage, looseness and other defects, resulting in reduced casting performance. Therefore, casting must be carried out at low superheat, but the casting temperature is too low and it is easy to cause problems such as insufficient casting and blocking the casting port. In industrial production, it is not only advantageous to strictly control the superheat of molten steel
In the casting of high manganese steel, it accelerates the solidification of molten steel, improves the internal quality of ingots, and increases the number of equiaxed crystals.
2 Calculation of heat released by solidification of molten steel
The heat released when molten steel solidifies consists of two parts: one is the heat released by the temperature drop; The other part is molten steel solidification
Latent heat of solidification released. The heat W1 released by molten steel due to temperature drop is:
W1 = C steel m steel ( T1 – T2 ) ( 2)
Formula: C steel is the specific heat capacity of molten steel, 460 J/( kg·°C ) ; m steel is the mass of castings, 1 200 kg; T1 is the casting start temperature, 1 450 °C;
T2 is the final temperature of solidification, 1 290 °C. When molten steel solidifies, a large amount of latent heat of solidification is released, and its magnitude is the same as
The composition and composition of the material is related to:
W2 = m steel ΔHtr ( 3)
Formula: W2 is the latent heat of solidification; ΔHtr is the enthalpy of phase change, 260 kJ/kg. Therefore, the total heat released by nitrogenous high manganese steel from the casting temperature cooling to the solidification temperature is the sum of equation (2) and formula ( 3), that is: W total 1 = W1 + W2 = C steel m steel ( T1 – T2 ) + m steel ΔHtr( 4)。
2 Accelerate the molten steel cooling method
2.1 Casting sand with higher thermal conductivity is adopted
At present, the casting sand used in general high manganese steel production plants is ordinary silica sand or quartz sand, the thermal conductivity is not high, and the thermal conductivity λ is 1. 38 ~ 1. 40 W/(m·K), which is not conducive to the rapid coagulation of castings
solid, replace the casting sand with zircon sand or magnesia with higher thermal conductivity, and the thermal conductivity λ is 1. 8 ~ 2. 5 W/(m·K) can speed up the heat transfer of molten steel and shorten the solidification time of castings.
2.2 Add a cooling device to the sand mold extraction device
At present, the sand mold is generally natural cooling, without a cooling device, but contains a pumping device to reduce the gas in the molding sand, so there are many pipelines inside the mold of the molding sand, and the cooling pipeline is installed in the pumping pipeline.
The use of copper tubes with high thermal conductivity, similar to the blast furnace cooling wall system, the use of this cooling channel to cool the molding sand, can accelerate the cooling of high manganese steel. The cooling channels can be internally connected with compressed cold air or cold
But water cools. When the cooling medium is water with a larger than the heat capacity, more heat is taken away per unit time, and the cooling effect is better, but at the same time, the cooling water has the risk of water leakage, and the danger increases, as long as it is used
When maintenance is timely, this method is still feasible. The cooling device is close to the sand mold, so that the rate of heat transfer from the sand mold in the molten steel increases, which can effectively increase the thermal conductivity of the casting sand, and the air cooling and water cooling effects are different, and the influence on the thermal conductivity of the casting sand is also different. ξ is used to indicate the coefficient of influence of the cooling device on the thermal conductivity of casting sand:
λ effect = ξλ ( 5) formula: λ effect is the equivalent heat after adding a cooling device to the sand mold device
conductivity, W/(m·K); ξ is the correction coefficient of thermal conductivity after adding the cooling device; λ is the actual thermal conductivity of the casting sand, W/(m·K).
2.3 Add cold steel during the casting process
When casting, part of the cold steel is added to the casting mold with the molten steel (or the cold steel is pre-laid in the sand mold before casting), not only can
Accelerate the cooling of molten steel, fine cold steel will form a nucleation core in the molten steel, increasing the proportion of isoshafted crystals in castings. The composition of cold steel should be similar to the composition of smelted steel, or the leftover scraps from the processing of finished steel products. The amount of cold steel added can be converted according to the law of conservation of heat: W3 = C steel m cold ΔT cold ( 6) that is, C steel m cold ΔT cold = C steel m liquid ΔT liquid ( 7) formula: m cold is the maximum value of cold steel added; M liquid is the quality of casting molten steel; ΔT cold is the temperature change of cold steel, that is, from normal temperature to solid
Temperature; ΔT fluid is a change in the temperature of molten steel, that is, from the casting temperature to the solidus temperature.
According to Equation ( 7), it can be concluded that the mass of cold steel should be lower than the total mass of molten steel 12. 65% , taking into account the heat taken away by the sand mold and the cooling medium. Through the test, it was found that the cold steel was added too little, the cooling effect was not obvious, and the addition of too much cold steel would block the casting pipeline and cause poor moldability of the casting parts. The amount of cold steel added is also related to the thickness of the casting, the complexity of the shape, etc., and should generally be controlled within 10% of the total mass of the molten steel. In addition, the particle size of cold steel should be moderate, the particle size is too small, and the molten steel cast in the early stage is washed to the end of the sand mold, and melts when it touches the molten steel
, resulting in fast cooling rate of molten steel at the end of the casting mold, slow cooling rate at the casting port, uneven solidification, internal stress, and even cracks inside the casting causing the casting to be scrapped; If the particle size is too large, cast steel will appear
The phenomenon that the cold steel has not been completely melted when the liquid solidifies eventually has a negative impact on the quality of the casting.
3 Factors affecting the solidification time of molten steel
In the solidification process of castings, the number of solid phases and liquid phases with different thermophysical coefficients continues to change, and the number of them is related to the continuously changing temperature, and with the decrease of temperature, there is also the release of superheating heat and crystalline latent heat, after the molding sand absorbs heat, the temperature rises, the cooling conditions also change, and the mathematical analysis method is used to solve the solidification time of the casting will be very complicated. Therefore, in order to effectively shorten the solidification time of castings and reduce the nitrogen evolution during the solidification process, this paper puts the quality of a casting enterprise as 1. A casting of 2 t is simplified to a radius of 0. 07 m, length 10
m cylinder with a total mass of 7 t of casting sand is solved by the unstable thermal conductivity Fourier differential equation as follows:

Where: W is the total heat released by the molding sand from the casting temperature to the complete solidification of nitrogenous high manganese steel, that is, W1 + W2 – W3,J; F is the surface area of the casting, m2; λ effect is the effective thermal conductivity of molding sand;
T1 is the casting start temperature, °C; T4 is room temperature, 25 °C; τ is the solidification time, s; ρ is the density of molding sand, 2 400 kg/m3; C is the specific heat capacity of the molding sand, 0. 29 × 103 J/( kg·℃ ) 。 Substituting equation ( 4) into equation ( 8) to obtain the calculation formula of the solidification time of the casting:

3.1 Effect of superheat on solidification time of high manganese steel
Use a thermal conductivity λ of 1. 4 W/(m·K) quartz sand, without strengthening cooling and adding cold steel, the superheat of molten steel is set to 30, 40, 50, 60 °C, respectively, substitute formula (9) meter
The relationship between the solidification time of high-manganese steel and the superheat of molten steel is calculated, as shown in Figure 2. It can be seen from Figure 2 that the solidification time of the casting increases with the increase of molten steel superheat, and has a linear relationship, and for every 10 °C decrease in the superheat of molten steel, the solidification time of the casting is shortened by about 45 s, and the effect is not obvious.
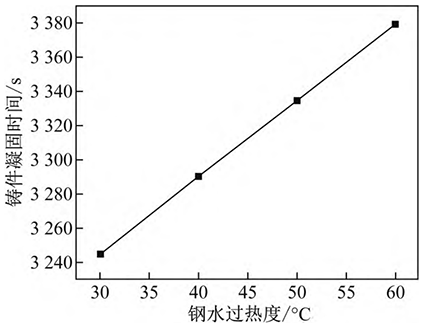
Fig. 2 Influence of superheat degree of molten steel on solidification time
3.2 Effect of thermal conductivity of casting sand on solidification time of high manganese steel
The heat emitted during solidification of high manganese steel, except for some of which is absorbed by cold steel, the rest is exported through casting sand, so the thermal conductivity of casting sand has a greater influence on the solidification time of high manganese steel. Under the condition that the molten steel superheat is 40 °C and no cold steel is added, 4 different casting sands are used, and the thermal conductivity λ is 1. 0、1. 5、2. 0、2. 5、3. 0, substitution formula (9) calculates the relationship between the solidification time of high manganese steel and the thermal conductivity of casting sand, as shown in Figure 3. It can be seen from Figure 3 that the thermal conductivity of casting sand has a great influence on the solidification time of molten steel, and with the increase of thermal conductivity of casting sand, the solidification time of casting is shortened exponentially. However, the cost of casting sand with high thermal conductivity is also high, which is not conducive to industrial production.
3.3 Effect of cooling strength on solidification time of high manganese steel
The casting sand cooling device is adopted to enhance the cooling of the mold by air cooling or water cooling to improve the thermal conductivity of the casting sand. According to the different air cooling or water cooling strength, the thermal conductivity correction coefficient ξ is 1. 0、1. 2、1. 4、1. 6、1. 8, using ordinary casting sand, thermal conductivity to take 1. 4 W/( m·K), take the superheat at 40 °C, and calculate high manganese by substituting the data into the formula (9) without adding cold steel
The relationship between the solidification time of steel and the thermal conductivity correction coefficient of casting sand is shown in Figure 4. It can be seen from Figure 4 that under the premise of not replacing the casting sand, the thermal conductivity correction coefficient of casting sand has a greater influence on the solidification time of molten steel, so the casting sand cooling device is used to shorten the solidification time of the casting by enhancing the cooling performance of the casting mold, and then reduce the nitrogen escape.
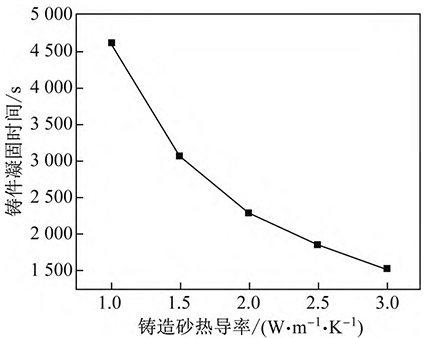
Fig. 3 Influence of thermal conductivity of casting sand on solidification time
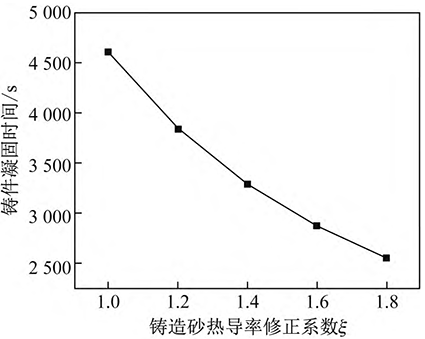
Fig. 4 Influence of correction coefficient of thermal conductivity of casting sand on solidification time
3.4 Effect of cold steel addition amount on solidification time of high manganese steel
The thermal conductivity is 1. 4 W/( m·K), superheat 40°C, thermal conductivity correction coefficient ξ 1. Under the condition of 2, the quality of cold steel is 1%, 3%, 5%, 7%, 9% of the quality of the casting, respectively
The entry equation (9) calculates the relationship between the solidification time of high manganese steel and the amount of cold steel added, as shown in Figure 5. It can be seen from Figure 5 that the solidification time of high manganese steel shortens with the increase of cold steel addition, and the solidification time of castings is shortened by about 170 s for every 1% increase in the mass of cold steel, indicating that the effect of adding cold steel to shorten the solidification time of high manganese steel is significant.
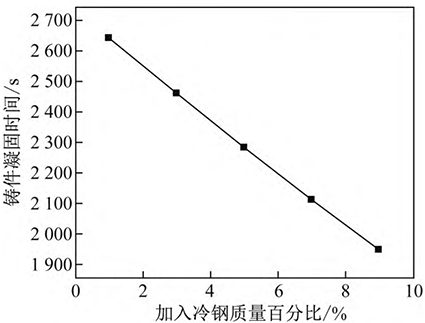
Fig. 5 Effect of percentage of cold steel added to the molten steel on solidification time of casting
3.5 Comparison of solidification time of high manganese steel before and after process improvement
In the casting process, the conventional casting temperature t1 used by a foundry is 1 500 °C, and the thermal conductivity of ordinary quartz sand λ is 1. 4W/( m·K), substitution formula ( 9) can calculate the solidification time τ1 of the nitrogen high manganese steel casting is 3 510 s. According to the research results of Bao Ruibin [20], the superheat of high manganese steel should be 40 °C, the casting temperature t1 should be 1 450 °C, and zirconin sand with higher thermal conductivity should be used, and the thermal conductivity λ should be 2. 1 W/( m·K), the cooling device is cooled by compressed air, and the thermal conductivity correction coefficient ξ is 1. 2. The amount of cold steel added is 5% of the mass of the casting, and the substitution type (9) can calculate the solidification time τ2 of the nitrogen-containing high manganese steel casting after the process improvement is 1 523 s. The solidification time after improving the casting process is 56% shorter than the original. 61%, which greatly reduces the evolution of supersaturated nitrogen during the solidification process of molten steel, and the nitrogen content in high manganese steel is significantly increased. But at normal pressure
Increased nitrogen content under melting conditions can lead to shrinkage defects inside the casting. Therefore, the casting riser needs to be lengthened during casting, and heat treatment and forging and welding are carried out after the casting is formed to reduce the nitrogen content and increase the pair
The influence of high manganese steel internal quality.
4 Conclusion
( 1) The heat calculation model of the solidification process of nitrogen-containing high manganese steel was established, the main influencing conditions for improving the casting of high manganese steel were proposed, and the Fourier differential equation of unstable thermal conductivity was introduced, and the relationship model between the solidification time of high manganese steel and the casting superheat, the thermal conductivity of casting sand and the cooling efficiency of cold steel was established.
( 2) The thermal conductivity of casting sand has the greatest influence on the solidification time of castings, followed by intensive cooling, and the influence of superheat is the smallest; Presented
Measures to accelerate the cooling of molten steel are adopted, such as molding sand with higher thermal conductivity, adding a cooling device to the sand mold, and adding cold steel during the casting process.
(3) Without using high-pressure equipment, the casting process cooling is accelerated by improving the cooling performance of the casting and the method of suspension casting, and the casting is condensed
The fixed time is 56 years shorter than the original. 61%, thereby reducing the evolution of nitrogen during the solidification process, increasing the nitrogen content in the steel, and expanding the application range of high manganese steel.