In the process of pouring, cooling and solidification, the feeding liquid metal passes through the riser, riser neck and the middle split of the cast iron, and finally reaches the area to be fed. At this time, the riser is the main storage unit of feeding molten metal, and the riser neck is the unit through which the feeding liquid metal flows and is a feeding channel. In this case, if the riser design is too large or too small, it will cause hot spot interference or affect the local heat dissipation of the riser neck, resulting in the failure to make use of the self feeding characteristics of the iron castings and affect the feeding.
Some studies have shown that the position, number and size of risers are related to the material, quality and modulus of the iron castings. It is believed that the feeding channel can be cut off after the shrinkage of the feeding object is completed and the feeding stage is entered. Therefore, the shrinkage modulus coefficient as a measure of riser cooling and solidification time reflects the rationality of riser design.
The mathematical model of contraction time fraction is proposed
According to the definition and determination of shrinkage modulus coefficient of cast iron castings,
For cylinder type cast iron castings, 21 samples of cylinder body type iron castings were counted, as shown in Table 3.1; the relationship between the statistical value and theoretical value of shrinkage modulus coefficient and the mass (unit: kg), overall modulus of iron castings (unit: cm), and mass perimeter quotient (kg / cm3) are shown in Fig. 3.1 to Fig. 3.3.
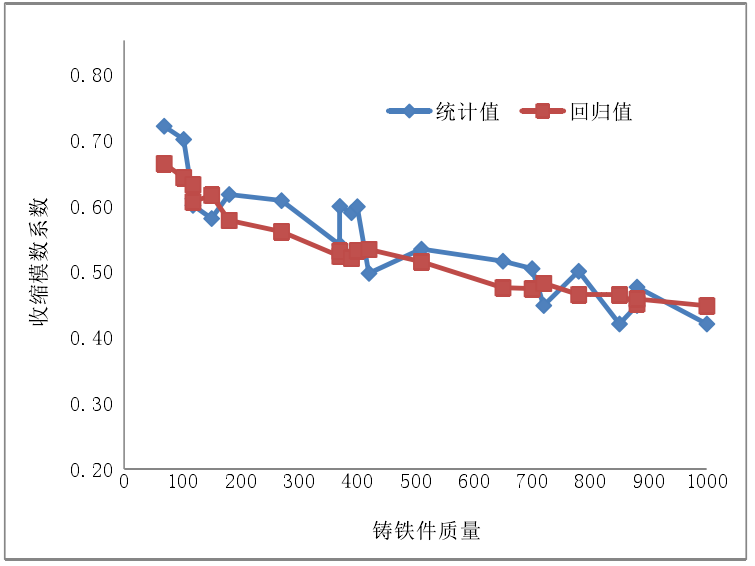
1) According to 21 groups of statistical data of cylinder block iron castings, the statistical value F2 of 13 groups of shrinkage modulus is greater than the theoretical value 2F, the statistical value 2F of 7 groups of shrinkage modulus is less than the theoretical value 2F, and only one group of statistical value F2 of shrinkage modulus is equal to the theoretical value 2F. In addition, F2 < 2F is concentrated in the small and medium-sized cylinder block iron castings, which shows that the design of process riser is generally too large in the actual production of small and medium cylinder block iron castings, and the feeding of cylinder block mainly comes from the feeding effect of riser; for medium and large iron castings, there is F2 > 2F The results show that the feeding effect of riser is limited. The cylinder body iron castings mainly emphasize the self feeding characteristics, and the riser only compensates for the deficiency of self feeding.
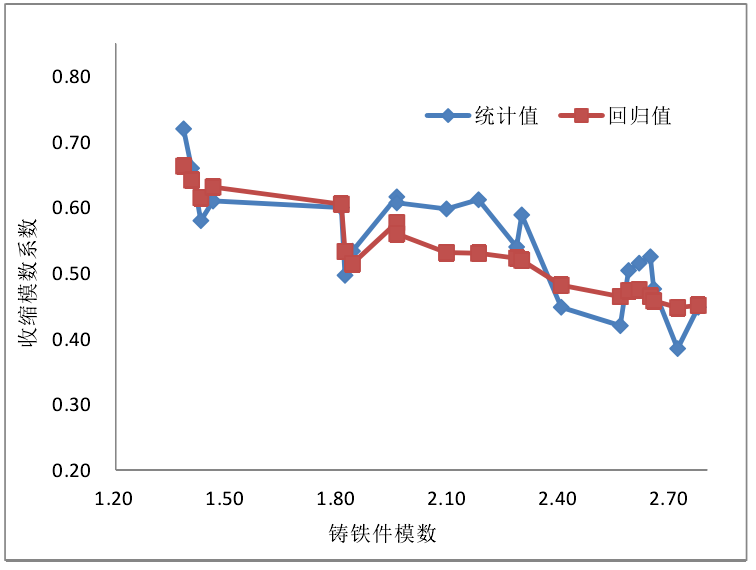
2) The statistical value F2 of shrinkage modulus coefficient of cylinder block iron castings decreases with the increase of iron casting quality and cast iron modulus. For the same quality iron castings, the larger the modulus of iron castings is, the smaller the statistical value F2 of shrinkage modulus coefficient is; the statistical value of shrinkage modulus coefficient of cylinder body iron castings is 2F With the change of the quality perimeter quotient of iron castings, the trend is that the initial stage presents the tendency of vibration and instability, and the later stage tends to be stable.
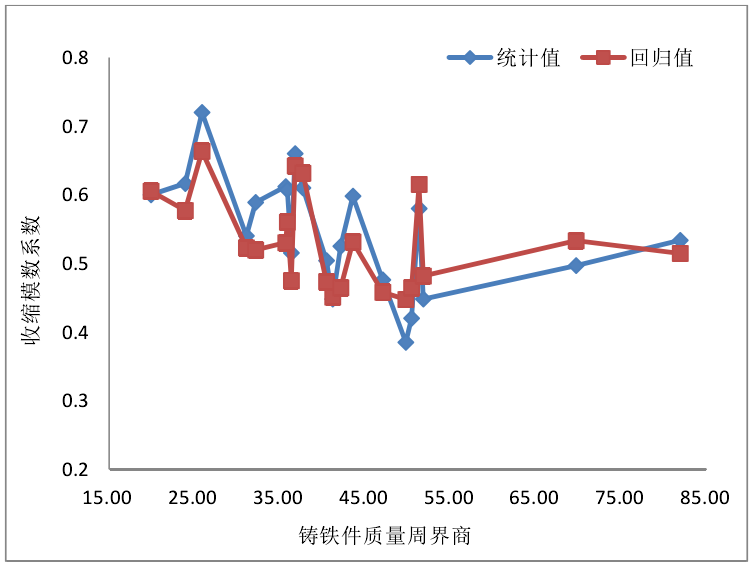
3) The shrinkage modulus coefficient of small cylinder block iron castings is greater than that of large cylinder block iron castings, which indicates that the shrinkage time fraction PC of small cylinder block iron castings is greater than that of large cylinder block iron castings, which is consistent with the process requirements of balanced solidification theory that the more small iron castings should be emphasized, the more feeding is required.