1. Introduction
1.1 Background and Significance
Copper is a crucial traditional and modern metal material. It has played a vital role in the development of human civilization. From ancient times to the present, with the continuous progress of electrification, automation, informatization, and networking, the application fields of copper have been expanding continuously, and its core role in construction, daily life, and high-tech fields has become increasingly prominent. Especially with the prosperity of the copper-based microelectronics industry, copper has been widely used in modern technology fields, confirming that copper is not only an important metal inheriting ancient values but also an indispensable key material for modern advanced technology.
Oxygen-free copper, with a purity greater than 99.95%, is widely used in various fields such as power, communication, and superconductivity due to its excellent electrical conductivity, thermal conductivity, corrosion resistance, ease of processing, and welding performance. The production of oxygen-free copper mainly relies on the continuous casting process, which can produce high-purity and high-quality oxygen-free copper materials at a speed of about 100 kg/h or about 4 m/min. Among the continuous casting methods, upward continuous casting (vertical continuous casting) shows significant advantages over horizontal continuous casting in terms of lower defect rate, faster cooling speed, unique production process, less capital investment, rapid start-up, and simplified production process. In recent years, this technology has been rapidly popularized in domestic small and medium-sized enterprises. Compared with traditional casting methods, upward continuous casting can provide more diverse product specifications, higher yield, brighter surface, lower oxygen content, better conductivity, less metal loss, lower energy consumption, less “three wastes” pollution to the environment, and lower production cost. It is considered an ideal choice in the field of copper wire and copper material processing.
However, at present, there are still some gaps between the quality of oxygen-free copper in China and the international advanced level. These differences are mainly reflected in the following aspects:
Aspect | International Situation | Domestic Situation |
---|---|---|
Raw Material Selection | Mostly use A-level cathode copper, such as CCC copper from Chile. | Only some producers use A-level cathode copper, and the choice is relatively limited. |
Production Equipment | Usually have large production scales and use dedicated smelting furnaces to ensure the quality stability of oxygen-free copper. | It is common for multiple copper brands to share the same smelting furnace. |
Pretreatment of Raw Materials and Auxiliary Materials | Attach great importance to this step and are equipped with dedicated pretreatment equipment. | Relatively lacking in this field. |
Technological Improvement of Smelting Furnace | Continuously adopt advanced technologies such as electromagnetic oscillation, nitrogen protection, and vacuum smelting to improve the quality of oxygen-free copper. | Although attempts have been made to use vacuum low-pressure smelting technology, breakthroughs in these technologies are still limited and require continuous innovation and improvement. |
In the production of oxygen-free copper, casting defects seriously affect the quality of the material. These defects mainly include inclusions and pores. According to the national standard of oxygen-free copper (GB/T5231 – 2001), harmful elements such as Pb, Bi, Sb, Fe, Sn, P, and S are strictly limited because once they dissolve into the metal lattice, they will reduce the conductivity and thermal conductivity of oxygen-free copper and damage its inherent high quality. Especially when the P content is too high, it will also affect the welding performance of the material and may cause leakage problems in vacuum electronic devices. In the process of upward continuous casting, casting defects are particularly prone to occur. When using Kazakhstan electrolytic copper (referred to as Hacopper) as the raw material, problems such as inclusion pores, grain coarsening, unqualified elongation, and environmental problems are more obvious. The copper oxide and “copper beans” in Hacopper dissolve in the copper liquid, producing excessive reducing gases, which are precipitated in large quantities when the copper rod is formed, resulting in defects such as depressions and pinholes. At the same time, impurity elements will also reduce the conductivity, thermal conductivity, ductility, and annealability of the oxygen-free copper rod and may even cause fracture during the upward continuous casting process, thus seriously affecting the subsequent processing steps.
Numerous studies have shown that casting defects pose a potential risk to the overall structure of the casting, which is a problem that cannot be ignored. The parts of the casting with defects will produce stress concentration, which may cause the casting to fatigue or fracture prematurely. At present, many scholars at home and abroad have conducted extensive research on the performance of cast magnesium alloys, aluminum alloys, and other metal materials and have found that pore defects have a serious impact on the quality and performance of castings. However, there are relatively few studies on the influence of macro casting defects on the performance of copper alloy castings. Therefore, analyzing the reasons for the inconsistent performance of upward continuous casting copper rods and studying the impact of casting defects on the performance of oxygen-free copper rods have certain guiding significance for improving the performance of oxygen-free copper.
1.2 Upward Continuous Casting Process of Oxygen-free Copper
1.2.1 Overview
With the vigorous development of the electrical industry, the quality requirements for cables and wires have also increased correspondingly, making high-purity copper, especially that with less impurities and lower oxygen content, particularly important. Oxygen-free copper is known for its excellent conductivity, high density, excellent plasticity, and good fatigue resistance. The oxygen-free copper continuous casting production technology, that is, the upward casting method, was gradually improved internationally in the 1980s and was first introduced in China in 1988, opening a new era for the production of oxygen-free copper billets (such as slab, tube billet, and wire billet). Among the existing oxygen-free copper production technologies, the upward casting method, continuous casting and rolling method, and dip coating method are the three most commonly used technologies. Compared with the other two technologies, the upward casting method has the following 显著特点:
- Since its casting and drawing processes are not continuous and are completed at room temperature without gas protection, the oxidation problem of the copper material is avoided. This not only reduces the equipment investment cost but also makes the factory layout more flexible.
- The upward casting method allows a large variation range in the single-machine output, and the annual output can be adjusted from several hundred tons to tens of thousands of tons, meeting the needs of different scale enterprises. The design of the multi-head continuous casting machine makes it possible to adjust the production volume by changing the diameter of the casting rod, allowing flexible arrangement of the production plan according to the supply of raw materials and market demand, effectively saving energy.
- By replacing the specifications of the crystallizer and graphite mold, different types of copper materials can be produced to meet the needs of different scale enterprises.
- The melting and heat preservation of the copper material are carried out in two furnaces, which greatly facilitates the possibility of producing alloy copper materials by the upward casting method.
In summary, due to the flexibility of its production process and its ability to cope with changing market demands and product types, the upward casting method has become a key technology in the production of oxygen-free copper.
1.2.2 Basic Principle of Upward Continuous Casting
The upward continuous casting technology is an advanced production method for continuously manufacturing metal products such as oxygen-free copper rods and copper wires. It is significantly different from the traditional sand casting and mainly uses the cooling and crystallization of the metal solution to form the product. This technology slowly and continuously extracts the crystallized metal from the molten metal to form a product with a specific shape. The upward continuous casting system usually includes four key parts: melting system, solution crystallization system, traction system, and take-up system. The melting system is used to melt the metal and maintain its temperature and reserve. The metal solution crystallization system promotes the condensation and formation of a specific shape of the rod or plate of the metal solution entering the crystallizer through the influence of the cooling liquid, and this shape matches the graphite mold inside the device. The traction system is used to continuously pull out the material formed in the crystallizer, which is the core of the production of continuous wire. The take-up system ensures the convenient storage and subsequent processing of the wire or plate by coiling. The schematic diagram is shown in Figure 1.1, which provides an intuitive representation of the process flow of this technology.
Before the start of the upward continuous casting process, a metal wire matching the inner diameter of the graphite sizing tube must be inserted into the tube and slightly protrude from the bottom of the crystallizer. This wire serves as the starting guide wire in the continuous casting process. With the start of the traction system, the guide wire moves upward. During this process, the pressure inside the crystallizer causes the metal melt to enter the graphite sizing tube and form a solid-liquid interface in the cooling crystallization area. With the 协同作用 of the cooling system and the traction system, the metal melt crystallizes and the formed metal wire continuously moves upward, which constitutes the core principle of the upward continuous casting technology.
In the process of producing oxygen-free copper rods, the melting and casting steps of copper are carried out in an environment avoiding air contact to ensure that the obtained copper rod is an oxygen-free copper rod (with an oxygen content of less than 0.0010%). This oxygen-free copper rod blank exhibits good conductivity and high plasticity due to its pure quality, and the manufactured contact wire has excellent resistance to repeated bending and is not prone to brittle fracture. This makes it an ideal material for producing casting rods of various copper and copper alloy contact wires.
1.2.3 Process Flow
The process of upward continuous casting is essentially an upward continuous casting process. The process flow chart of upward continuous casting of oxygen-free copper rods is shown in Figure 1.2. The following mainly 介绍 the selection of raw materials, smelting, and rod drawing.
1.3 Performance Research of Oxygen-free Copper Castings
Copper and copper alloys are widely used in the production fields of wires, cables, electrical contactors, and electronic components due to their excellent electrical and thermal conductivity, good processability, corrosion resistance, weldability, and relatively economical cost. In recent years, research, technological innovation, and product promotion activities of new materials such as oxygen-free copper, copper-silver electrical contact alloys, copper-iron alloy lead frame materials, and single-crystal copper have achieved remarkable results to meet the development needs of the electronics industry.
The continuous expansion of the national power grid construction and the new round of upgrading of power infrastructure have promoted the increasing demand for high-conductivity oxygen-free copper. A large amount of oxygen-free copper is required for conductive busbars, generator stator and rotor coils. In the next few years, the market demand for oxygen-free copper is expected to increase significantly.
Many domestic and foreign actual engineering projects have conducted experimental research on the conductivity and thermal conductivity of oxygen-free copper castings and achieved a lot of results. The team of Tian Ye from Huazhong University of Science and Technology took oxygen-free copper and different metal and non-metal materials as the research content and used the modulated photothermal method to conduct experiments to explore the contact characteristics between oxygen-free copper and other thermal conductive materials and the main influencing factors of the change in thermal resistance. The experiment pointed out that the contact thermal resistance between oxygen-free copper and metal materials is smaller than that between oxygen-free copper and ceramics, and especially the contact thermal resistance between copper and copper is the smallest. At Shenyang Ligong University, Liu Jinsong explored the influence of the addition of La element on the microstructure and properties of oxygen-free copper strip in the high-temperature sintering state and found that when the La addition amount reaches 64×10⁻⁶, the tensile strength and conductivity of the oxygen-free copper strip are increased by 25.9% and 3.2%, respectively. Yu Jiebing from the University of Chinese Academy of Sciences focused on studying the influence of the surface treatment of oxygen-free copper on the material properties and conducted tests on the thermal radiation coefficient and surface outgassing rate of the surface-treated oxygen-free copper samples. The results showed that the surface blackening treatment has the most obvious influence on the samples, and its thermal radiation coefficient is more than twice that of the untreated samples. In addition, Wei Zhaoxia analyzed the law of the change in the interface contact thermal resistance of the oxygen-free copper material with the increase in temperature and pressure and the decrease in the interface heat flow and material surface roughness in a…conducted dynamic mechanical tests on oxygen-free copper in the strain rate range from 2500 s⁻¹ to 15500 s⁻¹, obtained the true stress-true strain curve, and fitted it using the Power-Law and Johnson-Cook constitutive models. Zhang Lina et al. studied the welding process of zirconium oxygen-free copper using vacuum diffusion welding technology under deformation control conditions, explored the influence of the main process parameters on the welding interface and the mechanical properties of the joint, and provided a process basis for the reliable application of zirconium oxygen-free copper in aerospace engine models. Zhong Yuexi from Changchun Institute of Technology simulated the scratching process of oxygen-free copper using the smoothed particle hydrodynamics (SPH) method, analyzed the influence of contact depth, scratch speed, and non-perpendicular angle on the formation of scratches, and further promoted the understanding of the microscopic mechanical properties of the material. The research shows that there are differences in the influence of process parameters and process settings on the scratching formation process.
1.4 Research on the Influence of Casting Defects on Casting Performance
In the production process, there are often a large number of tiny defects inside the casting, even if the surface of the casting looks intact. Although the upward casting method has the advantages of short processing cycle, strong continuous production ability, high efficiency, and low cost in the production of oxygen-free copper, the quality of the casting billet largely determines the qualification rate of the final product. During the cooling and solidification of the casting billet, bubbles and shrinkage cavities are easily formed inside, and these defects are difficult to completely eliminate during the manufacturing process and can only be controlled as much as possible. Previous studies have shown that pore defects in the casting process will seriously affect the quality of the casting. According to statistics, in 2004, the United States lost up to 400 billion US dollars due to this, while in 1976, Japan’s loss reached 4 trillion yen, accounting for 3% of the GDP of that year. Germany’s annual direct loss is estimated to reach 10 billion marks. In China, the direct economic loss caused by casting defects in the manufacturing industry has 累计 reached 30 billion yuan. These defects will not only cause material fracture failure, lead to machine damage or even the shutdown of the entire production line, but also indirectly cause economic losses. In addition, product failures caused by casting defects will not only bring economic losses but also may lead to reduced or stopped production, and the actual losses are often greater than expected.
In the manufacturing, processing, and use stages, pore defects in the casting are one of the key reasons for cracks and functional failures, which seriously affect the performance and mechanical strength of the casting. These defects, hidden inside the material or casting, are often difficult to detect during processing or use, and the casting with pore defects may deform or crack due to the defects during subsequent processing or use. Frequent mechanical failures caused by pore defects at home and abroad have prompted many scholars and professionals to conduct in-depth research and discussion on the pore defect problem in the casting process.
In the international research field, R.A. Hardin and other American scholars proposed a new method for evaluating the influence of porosity on the elastic modulus of steel and compared and verified the simulation results with the experimental data, confirming the correlation between porosity and elastic modulus. The research pointed out that there is a critical porosity, and when it is exceeded, the stiffness or load-bearing capacity of the steel will decrease significantly, and the relationship between the elastic modulus and porosity shows a nonlinear decreasing trend. Kai You and other researchers calculated the specific morphology and distribution of discontinuous defects such as pores and inclusions through three-dimensional mapping technology and further applied these data to the finite element model. They used a heterogeneous material model to predict the fatigue life and found that the pores and inclusions at the root of the propeller blade significantly increased the local heterogeneity, resulting in an increase in the maximum stress and a theoretical reduction in the fatigue life by half. This 证实 that discontinuous defects significantly affect the performance of the casting. R.W. Rice and others discussed the influence of porosity on the performance of mechanical components and conducted a series of studies on porosity parameters. Zhang and others explored the influence of pore defects on the compressive properties of copper alloys and found that the elastic modulus decreases with the increase in porosity, and the yield strength has a linear relationship with porosity. T. Sumitomo and others studied the influence of the porosity of die-cast AZ91 alloy on the elastic modulus and pointed out that the elastic modulus of AZ91 alloy decreases with the increase in porosity. B. Zhou and others quantitatively analyzed the influence of pores on the tensile properties through microstructure research and static tensile experiments on GW63 alloy and found that both the ultimate tensile strength and fracture elongation decrease with the increase in porosity. Carola Martinez and others studied the influence of porosity on Ti – 6Al – 4V alloy using a variety of surface analysis techniques and electrochemical methods. The results showed that the increase in porosity leads to a decrease in the elastic modulus. ChoongDo Lee studied the influence of porosity change on the tensile properties of A356 aluminum alloy and evaluated the influence of microscopic porosity and microstructure characteristics on the properties using an improved constitutive model. Zixin Li compared the porosity of AZ91D and EA42 alloys in three dimensions using XCT technology and proposed an effective method for predicting the projected area fraction of porosity and further explored its influence on the tensile properties. Shaohua Yan studied the influence of porosity on the performance of welded joints and successfully controlled the porosity by adjusting the welding parameters. It was found that within a certain range, pores have little influence on the joint performance but reduce the fatigue strength. Lenka Kucharikova quantified the defects of AlSi9Cu3 cast alloy, quantitatively analyzed the defect size and distribution using extreme value statistical analysis and NIS Elements software, and revealed the important influence of porosity on the fatigue performance of the alloy.
In China, Han Yunfei’s team conducted in-depth research on the casting defects of ZTA15 titanium alloy and their influence on the material structure and performance. They found that the as-cast ZTA15 titanium alloy exhibits residual stress and defects such as pores and shrinkage porosity, which significantly reduce the mechanical properties of the material and are not conducive to its performance in engineering applications. After heat isostatic pressing treatment, these shrinkage porosity defects are compacted and closed, the material structure becomes denser and more uniform, and the mechanical properties are significantly improved, and the performance data become more concentrated. In addition, inclusion defects significantly damage the mechanical properties of ZTA15 titanium alloy, especially its plasticity. Xu Zhanghua and his team compared and analyzed the fatigue performance and microstructure of K4169 alloy thin plates. The results showed that casting defects greatly affect the fatigue life of the alloy thin plates, and the fatigue life of the defective alloy thin plates is less than half that of the non-defective thin plates. Qiu Zhongyuan and other researchers explored the law of the influence of defects on the mechanical properties of high-pressure die-cast aluminum alloys and found that there is a correlation between the porosity and the maximum defect size and the elongation of the material. The increase in porosity or the maximum defect size will lead to a decrease in elongation. Gong Weijia from Southeast University studied the influence of casting defects on the mechanical properties of cast steel joints and the overall truss structure through numerical simulation methods and proposed improvement suggestions for the current quality rating method of cast steel parts. Zhu Lianbing and others studied the influence of the morphological and positional characteristics of pore-like defects on the performance of dog-bone-shaped specimens and long-strip castings and extended the research to the mechanical and fatigue properties of rocker-arm-shaped castings. Hao Liangpin and others focused on the influence of shrinkage porosity defects on the mechanical properties of castings, established a quantitative prediction mathematical model of shrinkage porosity in aluminum alloy castings, and explored its formation mechanism. Liu Hongwei and others developed a module for predicting the influence of shrinkage porosity defects in cast steel and cast iron sand mold castings on performance. Pan Liwen’s team used ProCAST casting simulation software to predict the formation of shrinkage porosity defects in TiAl alloy blades. Xu Hong studied the change law and mathematical model of the heat exchange coefficient in the solidification process of aluminum castings, provided a physical and mathematical model for predicting shrinkage porosity defects, and successfully applied it to the simulation of actual castings. Liu Ligang and others predicted the shrinkage porosity defects in centrifugal casting rolls through the finite element method and the Niyama criterion. Yan Qingsong analyzed the shrinkage porosity defects from the perspective of numerical simulation and pointed out the influence law of these defects on the casting performance. Chen Liliang and others deeply studied the serious destructive effect of shrinkage porosity defects on the casting quality and proposed corresponding prediction methods. Cui Jishun and others improved and added the prediction criteria for shrinkage porosity in domestic solidification simulation software, enriching the methods for analyzing casting defects.
1.5 Quantitative Fracture Analysis Technology
As discussed above, pore defects in the casting have a significant negative impact on its mechanical properties. The morphology and distribution of tiny pores in the casting are highly random and irregular, resulting in that the porosity information determined only by volume density measurement or two-dimensional microstructure observation is extremely limited for the shape and distribution details of the pores. Recently, quantitative analysis of the fracture surface has become a mainstream method for studying the fracture mechanisms of various materials. Previous studies have revealed that the morphological characteristics of the fracture surface can reflect the mechanical properties and fracture behavior of the material. Through quantitative analysis of the fracture surface, detailed information that is difficult to obtain through traditional macroscopic fracture mechanics analysis can be obtained. The method of fracture surface quantitative analysis was initially proposed by EL-Soudani and other scholars. This method is an extended application of stereology theory in non-planar surface analysis, covering the classification of fracture surface types, the measurement of the proportion of fracture surface characteristic areas, and the proportion and area of void volumes. This series of analyses is collectively referred to as fracture surface histomorphometry.
As a new tool for material fracture analysis, quantitative fractography uses stereophotography or direct sectioning methods to estimate the actual pore surface area, which makes it possible to convert the measurement results of the fracture surface from a planar scanning electron microscope (SEM) to the actual fracture surface parameters (including contour and surface roughness). These roughness parameters can be correlated with each other through a concise parameter equation, allowing the estimation of the surface area of fracture defects based on the experimental determination of the section roughness parameters. K. BANERJI calculated the average area and perimeter of the dimples on the fracture surface of 4340 steel and proved through case analysis that the quantitative fracture analysis method can detect the 微小变化 in the fracture surface morphology caused by the material microstructure and can obtain values consistent with the actual pore area. Therefore, this study used the quantitative fracture analysis method to measure the porosity of the tensile test fracture surface, which provides important technical support for quantitatively analyzing the influence of internal pores of the upward continuous casting oxygen-free copper rod on the mechanical properties of the material.
1.6 Main Contents of This Study
This paper tests the mechanical and physicochemical properties of oxygen-free copper rods produced by upward continuous casting using different raw materials, analyzes the reasons for the inconsistent performance of upward continuous casting copper rods, and studies the influence of casting defects on the performance of oxygen-free copper rods. In addition, finite element simulation and analysis are carried out on the pore defects of oxygen-free silver copper (TUY03) to study the influence of pore defects on the macroscopic mechanical properties of oxygen-free copper materials. The main research contents are as follows:
- Tensile performance tests are carried out on oxygen-free copper rod materials produced using different raw materials, and the tensile mechanical properties of different samples are compared. The Weibull distribution function is used to evaluate the mechanical stability of these two types of samples, and the mathematical relationship between the cross-sectional porosity and the mechanical properties of the casting is studied. The zero-porosity elongation of these two types of samples is predicted.
- The fracture surface morphology of the upward continuous casting copper rod tensile specimens produced using different raw materials is analyzed, and the source, main components, and formation mechanism of the defects at the fracture surface are explored.
- The corrosion resistance of oxygen-free copper rods produced by upward continuous casting using different raw materials is analyzed using the Shanghai Chenhua CHI600E electrochemical workstation, and the corrosion mechanism of the oxygen-free copper rod material is expounded.
- The conductivity and hardness of oxygen-free copper rods produced by upward continuous casting using different raw materials are measured, and the influence laws of casting defects on the conductivity and hardness of the casting are obtained.
- The finite element analysis of the COMSOL software is used to explore the influence laws of the content and size of pore defects on the macroscopic mechanical properties of oxygen-free silver copper.
1.7 Technical Route
The main research route of this paper is as follows:
Copper recycling, electrolytic copper, and a small part of copper materials are used as raw materials for upward continuous casting to produce recycled copper rods and benchmark oxygen-free silver copper rods (TUY03). Then, electrochemical tests, mechanical property tests (including tensile tests, hardness tests), conductivity tests, and tensile fracture surface analysis are carried out on these samples. The electrochemical…
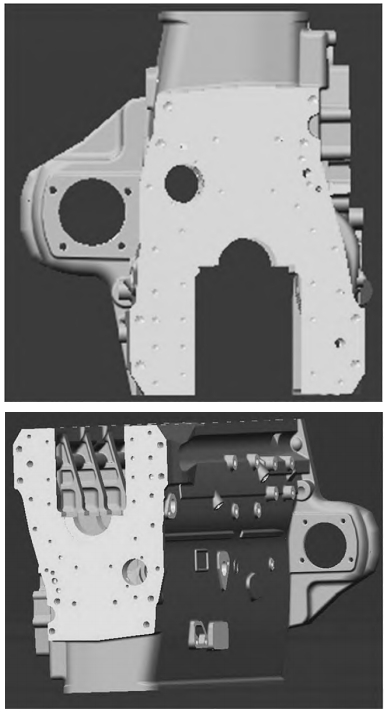