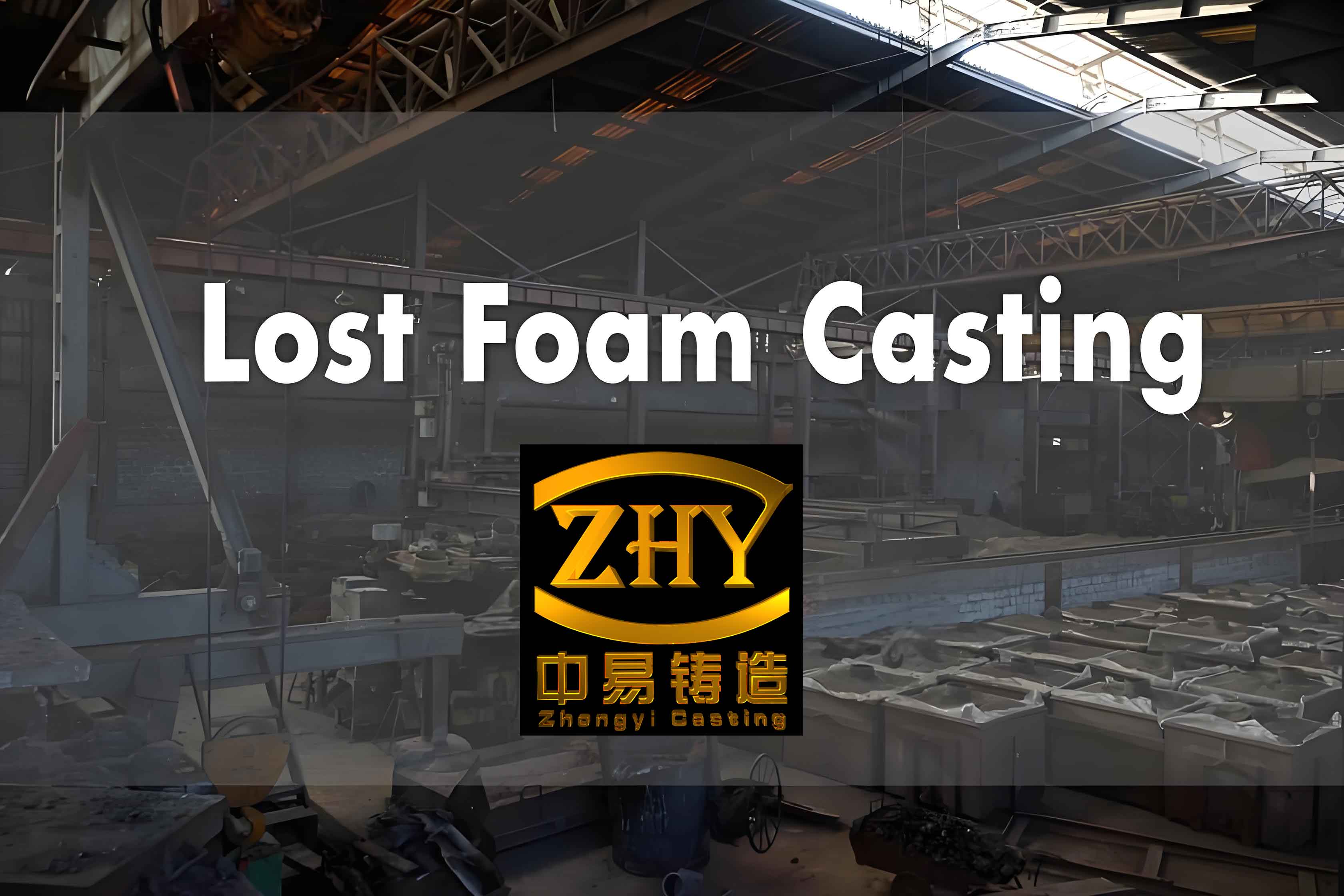
The automotive industry is undergoing a transformative shift toward electric vehicles (EVs), driven by the need for sustainable and energy-efficient transportation solutions. As Electric Vehicle manufacturers strive to enhance performance, reduce weight, and optimize cost efficiency, advanced manufacturing processes like lost foam casting have gained prominence. Lost foam casting, known for its ability to produce complex metal parts with high precision, is particularly suited for the unique demands of Electric Vehicle manufacturing. This article explores the successful implementation of lost foam casting in Electric Vehicle manufacturing, highlighting its benefits, challenges, and key applications.
Introduction to Lost Foam Casting
Lost foam casting is an innovative metal casting process that involves creating a foam pattern, which is then coated with a refractory material to form a mold. This mold is surrounded by unbonded sand, and molten metal is poured into the mold, causing the foam pattern to evaporate and be replaced by the metal, forming the final part. This process allows for the production of highly detailed and complex components with minimal machining and assembly.
Key Benefits of Lost Foam Casting for Electric Vehicle Manufacturing
1. Lightweight Components
Weight reduction is a critical factor in enhancing the performance and efficiency of Electric Vehicles. Lost foam casting enables the production of lightweight components by:
- Material Efficiency:
- Allows for the use of lightweight alloys such as aluminum and magnesium, which offer excellent strength-to-weight ratios.
- Reduces the need for additional machining and assembly, further minimizing weight.
- Complex Geometries:
- Enables the creation of intricate and optimized geometries that reduce material usage without compromising structural integrity.
- Facilitates the integration of multiple parts into a single casting, reducing the overall weight of assemblies.
Benefit | Description | Impact on Electric Vehicles |
---|---|---|
Material Efficiency | Use of lightweight alloys, reduced machining | Enhanced performance, improved efficiency |
Complex Geometries | Creation of intricate, optimized geometries | Weight reduction, structural integrity |
2. Improved Thermal Management
Effective thermal management is essential for the performance and safety of Electric Vehicles. Lost foam casting offers several advantages in this area:
- Thermal Conductivity:
- The ability to cast parts with high thermal conductivity materials, such as aluminum alloys, enhances heat dissipation.
- Customizable designs enable the creation of components with integrated cooling channels and heat sinks.
- Precision Casting:
- The precision of lost foam casting ensures that cooling components fit perfectly within tight tolerances, optimizing thermal management.
- Reduces the need for additional processing, maintaining the thermal properties of the material.
Benefit | Description | Impact on Electric Vehicles |
---|---|---|
Thermal Conductivity | High thermal conductivity materials, integrated cooling | Enhanced heat dissipation, improved safety |
Precision Casting | Accurate casting, optimal component fit | Efficient thermal management, reduced processing |
3. Cost Efficiency
Cost efficiency is a crucial consideration for Electric Vehicle manufacturers. Lost foam casting contributes to cost savings through:
- Reduced Machining and Assembly:
- The ability to cast complex shapes directly reduces the need for extensive machining and multiple assembly steps.
- Integration of multiple components into a single casting reduces labor and material costs.
- Material Savings:
- Precise pattern creation minimizes material waste.
- The use of recyclable materials and efficient recycling processes further reduces costs.
Benefit | Description | Impact on Electric Vehicles |
---|---|---|
Reduced Machining and Assembly | Fewer machining and assembly steps, integrated components | Lower production costs, streamlined manufacturing |
Material Savings | Minimized material waste, use of recyclable materials | Cost reduction, sustainability |
Key Applications of Lost Foam Casting in Electric Vehicle Manufacturing
1. Battery Housings and Components
Battery housings and related components are critical for the performance and safety of Electric Vehicles. Lost foam casting is ideal for producing these components due to its ability to create complex, high-strength parts.
- Battery Housings:
- Lightweight, high-strength housings that protect the battery cells and provide structural support.
- Integration of cooling channels and mounting features directly into the casting.
- Cooling Plates and Heat Sinks:
- Efficient thermal management components that ensure optimal battery temperature.
- High thermal conductivity materials for effective heat dissipation.
Application | Description | Benefits |
---|---|---|
Battery Housings | Lightweight, protective housings with integrated features | Enhanced safety, structural support |
Cooling Plates and Heat Sinks | Thermal management components for optimal battery temperature | Improved efficiency, prolonged battery life |
2. Motor Housings and Components
Electric Vehicle motors require robust and lightweight housings to ensure performance and efficiency. Lost foam casting enables the production of these critical components with precision and efficiency.
- Motor Housings:
- High-strength, lightweight housings that protect the motor and provide structural integrity.
- Complex geometries that optimize airflow and cooling.
- Gearbox and Transmission Components:
- Durable components that withstand high stress and wear.
- Precision casting ensures tight tolerances and smooth operation.
Application | Description | Benefits |
---|---|---|
Motor Housings | Lightweight, robust housings with optimized airflow | Enhanced performance, efficient cooling |
Gearbox and Transmission Components | Durable, precise components for smooth operation | Increased reliability, reduced maintenance |
3. Structural and Chassis Components
Structural and chassis components must be strong, lightweight, and capable of withstanding significant stress. Lost foam casting is well-suited for producing these components efficiently.
- Frame Components:
- High-strength frame components that provide structural integrity and support.
- Integration of multiple parts into single castings for weight reduction and increased strength.
- Suspension Components:
- Durable suspension components that ensure a smooth and safe ride.
- Precision casting for tight tolerances and reliable performance.
Application | Description | Benefits |
---|---|---|
Frame Components | High-strength, integrated frame components | Improved structural integrity, reduced weight |
Suspension Components | Durable, precise suspension components | Enhanced ride quality, increased reliability |
Challenges and Solutions in Implementing Lost Foam Casting for Electric Vehicles
While lost foam casting offers numerous benefits, there are challenges associated with its implementation in Electric Vehicle manufacturing. Addressing these challenges is crucial for successful adoption.
1. Pattern Material Selection
Selecting the appropriate foam material for patterns is critical for achieving desired casting quality. Solutions include:
- High-Density Foams:
- Using high-density foams that offer better dimensional stability and surface finish.
- Ensuring consistent quality through rigorous material testing and control.
- Biodegradable Foams:
- Exploring eco-friendly foam materials that reduce environmental impact and enhance sustainability.
Challenge | Solution | Benefits |
---|---|---|
Pattern Material Selection | High-density and biodegradable foams | Improved casting quality, sustainability |
2. Process Control and Optimization
Maintaining precise control over the casting process is essential for achieving consistent results. Solutions include:
- Automation and Monitoring:
- Implementing automated systems for pattern assembly, coating, and casting.
- Using real-time monitoring to ensure process parameters are within optimal ranges.
- Advanced Simulation Software:
- Utilizing simulation software to model and optimize the casting process.
- Predicting potential issues and making necessary adjustments before production.
Challenge | Solution | Benefits |
---|---|---|
Process Control and Optimization | Automation, monitoring, and simulation | Consistent quality, reduced defects |
Case Study: Successful Implementation of Lost Foam Casting in Electric Vehicle Manufacturing
A leading Electric Vehicle manufacturer successfully implemented lost foam casting for the production of critical components, achieving significant improvements in performance and efficiency.
- Battery Housing:
- Produced lightweight aluminum battery housings with integrated cooling channels.
- Achieved a 25% weight reduction compared to traditional methods.
- Motor Housing:
- Developed high-strength motor housings with optimized airflow design.
- Enhanced motor performance and reduced operating temperatures.
- Structural Components:
- Cast high-strength frame and suspension components with integrated features.
- Improved vehicle structural integrity and reduced assembly time.
Application | Achievements | Impact on Electric Vehicles |
---|---|---|
Battery Housing | 25% weight reduction, integrated cooling channels | Enhanced performance, increased efficiency |
Motor Housing | Optimized airflow, reduced operating temperatures | Improved motor performance, longer lifespan |
Structural Components | High-strength, integrated features | Improved structural integrity, reduced assembly time |
Conclusion
The successful implementation of lost foam casting in Electric Vehicle manufacturing demonstrates its potential to enhance performance, reduce weight, and optimize cost efficiency. By leveraging the benefits of lost foam casting, Electric Vehicle manufacturers can produce lightweight, high-strength components with complex geometries, improved thermal management, and reduced environmental impact. As the automotive industry continues to evolve towards more sustainable and energy-efficient solutions, lost foam casting will play a pivotal role in shaping the future of Electric Vehicle manufacturing. Embracing these advancements and addressing associated challenges will enable manufacturers to achieve new levels of excellence in their production processes, meeting the growing demands of the modern automotive market.