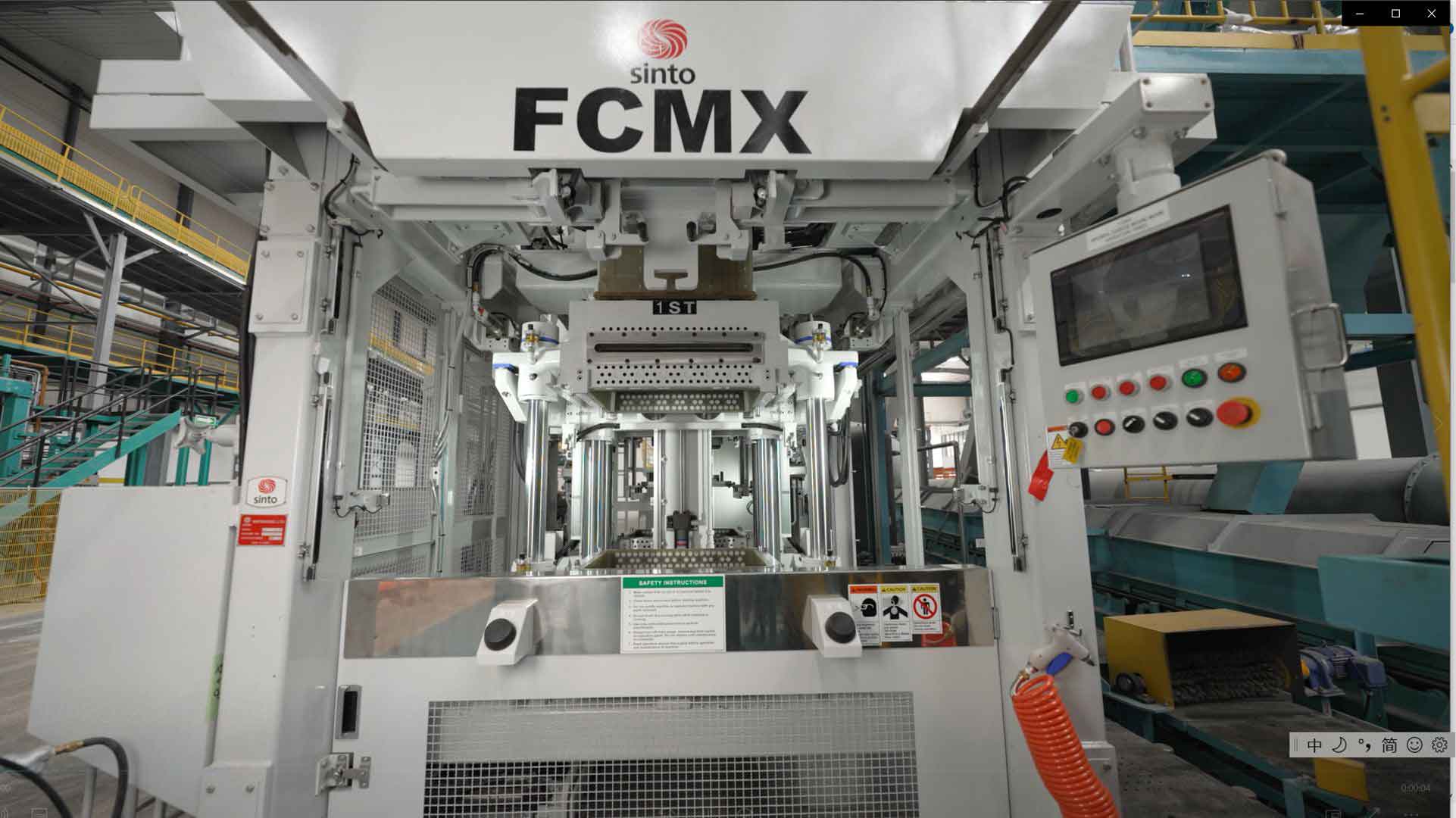
The future of automation in investment casting process holds significant potential to revolutionize this traditional manufacturing method, making it faster, more efficient, and increasingly precise. Automation is set to transform various aspects of the investment casting process, from pattern making to final part inspection. Here’s a look at what the future might hold:
1. Automated Pattern Making
- 3D Printing: Automation will likely expand in the use of 3D printing for creating wax and resin patterns. This technology can significantly reduce the time and cost associated with traditional pattern making, while allowing for greater design complexity.
- Robotics: Robotics could be used for the automated assembly of complex patterns, particularly in cases where multiple pieces need to be assembled before investment casting.
2. Mold Making
- Automated Dipping and Coating: Robots can automate the process of dipping wax patterns into ceramic slurries to build up the mold shell, ensuring consistent coating thickness and reducing material wastage. Automation in drying and hardening processes through precise environment control can further optimize mold quality.
- CNC Machining: For hard molds, CNC machining offers precise and automated preparation, enhancing the dimensional accuracy and surface finish of the final investment casting.
3. Casting and Pouring
- Automated Pouring Systems: Robotic arms and automated guided vehicles (AGVs) can handle the pouring of molten metal, improving precision in pour rates and volumes, which are critical for achieving defect-free castings.
- Process Monitoring: Integrated sensors and real-time monitoring systems can control and adjust process parameters like temperature and flow rate during investment casting, based on the feedback received from the monitoring systems.
4. Cooling and Mold Removal
- Controlled Cooling Systems: Automated cooling systems that precisely control the cooling rate of investment casting parts can reduce internal stresses and deformation, improving the mechanical properties of the cast.
- Automated Knockout: Robots equipped with force-control sensors can be used to remove investment casting parts from the molds, reducing the risk of damage to the parts during extraction.
5. Cleaning and Finishing
- Automated Cleaning: Post-casting processes such as the removal of the ceramic shell, sandblasting, and cutting can be automated to increase throughput and consistency.
- CNC Finishing: CNC machines can perform precise finishing operations, reducing the need for manual labor and improving the surface quality of investment casting parts.
6. Inspection and Quality Control
- Automated Inspection: Advanced imaging technologies and machine learning algorithms can automate the inspection of investment casting parts. Systems like automated X-ray inspection and 3D scanning can identify defects and ensure parts meet quality specifications without human intervention.
- Data Analytics: The integration of data analytics tools can analyze data collected throughout investment casting process to predict potential defects and adjust process parameters automatically to prevent them.
7. Supply Chain and Logistics Automation
- Inventory Management: Automated inventory systems using RFID technology can track materials and finished products throughout the facility, optimizing material flow and reducing waste.
- Robotics in Logistics: Robotics can also be used in packaging and palletizing operations, as well as in loading and unloading materials, enhancing efficiency in logistics operations.
8. Sustainability and Energy Management
- Energy Optimization: Automated energy management systems can optimize energy consumption throughout investment casting process, reducing the environmental footprint of manufacturing operations.
As automation technologies continue to evolve, their integration into investment casting process will likely increase, driven by the need for manufacturers to reduce costs, enhance quality, and meet the increasingly complex requirements of industries such as aerospace, automotive, and healthcare. This evolution will not only reshape how investment casting is performed but also open new opportunities for innovation in product design and manufacturing efficiency.