Sustainability is becoming an increasingly important aspect of manufacturing processes, including sand casting parts production. Sand casting manufacturers are adopting various strategies to enhance sustainability and minimize their environmental impact. Some key sustainable practices in sand casting parts manufacturing include:
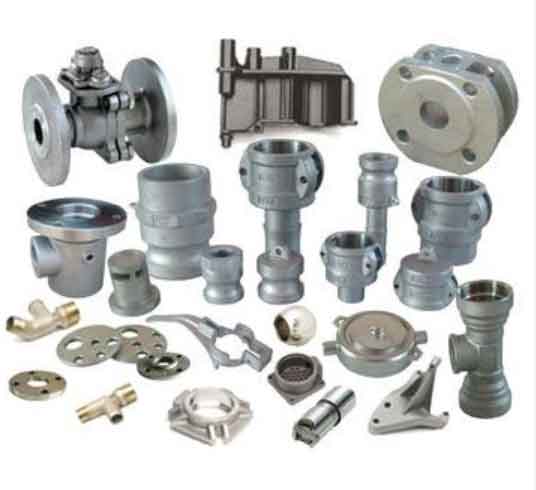
- Material Selection: Using recycled materials or materials with a lower environmental impact can reduce the carbon footprint associated with casting. Opting for eco-friendly materials and alloys, as well as sourcing them responsibly, contributes to sustainability efforts.
- Energy Efficiency: Manufacturers are investing in energy-efficient equipment and technologies to minimize energy consumption during the casting process. Implementing energy-saving measures helps reduce greenhouse gas emissions and overall energy use.
- Waste Reduction: Implementing waste reduction strategies is crucial for sustainable sand casting. Minimizing scrap and reusing leftover sand and other materials can significantly reduce waste generation and associated disposal costs.
- Water Management: Proper water management, including recycling and treating water used in the sand casting process, helps conserve this valuable resource and ensures compliance with environmental regulations.
- Emissions Control: Employing efficient emission control systems helps reduce air pollutants and greenhouse gas emissions generated during the casting process. This contributes to cleaner air and a healthier environment.
- Green Sand Reclamation: Green sand reclamation processes recover and reuse sand, reducing the need for new sand and lowering the environmental impact associated with sand mining.
- Lean Manufacturing: Adopting lean manufacturing principles in sand casting operations can optimize production efficiency and minimize waste, leading to resource conservation and increased sustainability.
- Life Cycle Assessment (LCA): Conducting life cycle assessments of sand casting parts helps identify opportunities for improvement across the entire product life cycle, from raw material extraction to end-of-life disposal.
- Packaging and Transportation: Employing eco-friendly packaging materials and optimizing transportation methods can reduce the carbon footprint associated with delivering the finished parts to customers.
- Certifications and Compliance: Obtaining certifications such as ISO 14001 for environmental management or adhering to sustainability standards ensures that sand casting manufacturers are committed to environmental responsibility.
- Education and Awareness: Raising awareness among employees and stakeholders about sustainability practices fosters a culture of environmental stewardship and encourages the adoption of sustainable approaches.
Sustainable sand casting practices not only benefit the environment but also contribute to the long-term viability and reputation of manufacturers in an increasingly eco-conscious market. As the demand for sustainable products and practices continues to grow, sand casting manufacturers play a vital role in promoting environmentally responsible manufacturing processes.