The sand casting process can be made more sustainable through various practices and considerations that focus on reducing environmental impact and optimizing resource utilization. Here are some ways to promote sustainable manufacturing in the sand casting process:
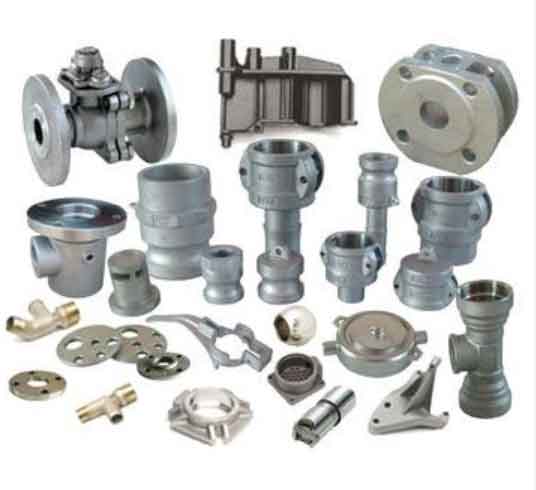
- Sand Management and Reclamation: Sand is a significant component in the sand casting process, and proper sand management can reduce waste and promote sustainability. Implementing sand reclamation systems allows used sand to be processed and reused, minimizing the need for new sand and reducing waste generation. This not only conserves natural resources but also reduces the disposal of sand waste.
- Energy Efficiency: Energy consumption is an important consideration in sustainable manufacturing. Employing energy-efficient equipment, such as high-efficiency furnaces and automated systems, can help minimize energy usage during melting, pouring, and other process stages. Additionally, optimizing process parameters, such as melt temperature and cooling rates, can contribute to energy savings.
- Emission Control and Air Quality: Controlling emissions from the sand casting process is crucial for environmental sustainability. Proper ventilation and filtration systems should be in place to capture and remove harmful gases, particulate matter, and volatile organic compounds (VOCs) generated during the melting and pouring processes. Compliance with environmental regulations and the use of clean technologies can minimize air pollution and protect air quality.
- Waste Management and Recycling: Efficient waste management is essential for sustainable manufacturing. Establishing proper waste segregation practices and recycling programs for materials such as scrap metal, used cores, and other process waste can help reduce landfill waste and promote the circular economy. Additionally, the recycling of metal chips and excess material generated during the casting process can conserve resources and reduce waste.
- Water Conservation: Water usage in the sand casting process can be optimized to minimize waste and conserve this valuable resource. Implementing water recycling and filtration systems can allow for the reuse of water in various stages of the process, reducing the need for fresh water intake. Additionally, implementing water-saving techniques such as closed-loop cooling systems and process optimization can further reduce water consumption.
- Supplier Collaboration: Engaging with suppliers who prioritize sustainability and environmental stewardship can contribute to sustainable manufacturing. Collaborating with suppliers to source eco-friendly materials, reduce packaging waste, and implement sustainable practices throughout the supply chain can promote overall sustainability in the sand casting process.
- Life Cycle Assessment (LCA): Conducting a life cycle assessment of the sand casting process can help identify areas of improvement and guide sustainability initiatives. This involves analyzing the environmental impact of the process from raw material extraction to casting production, use, and disposal. LCA helps in understanding the potential environmental hotspots and enables targeted efforts for improvement.
- Employee Training and Awareness: Educating and involving employees in sustainable practices and environmental awareness can create a culture of sustainability within the organization. Training programs on waste management, energy conservation, and sustainable manufacturing practices can empower employees to contribute to sustainability efforts.
By incorporating these sustainable practices into the sand casting process, manufacturers can minimize the environmental footprint, conserve resources, reduce waste generation, and promote responsible manufacturing. These efforts not only benefit the environment but also contribute to the long-term success and reputation of the company.