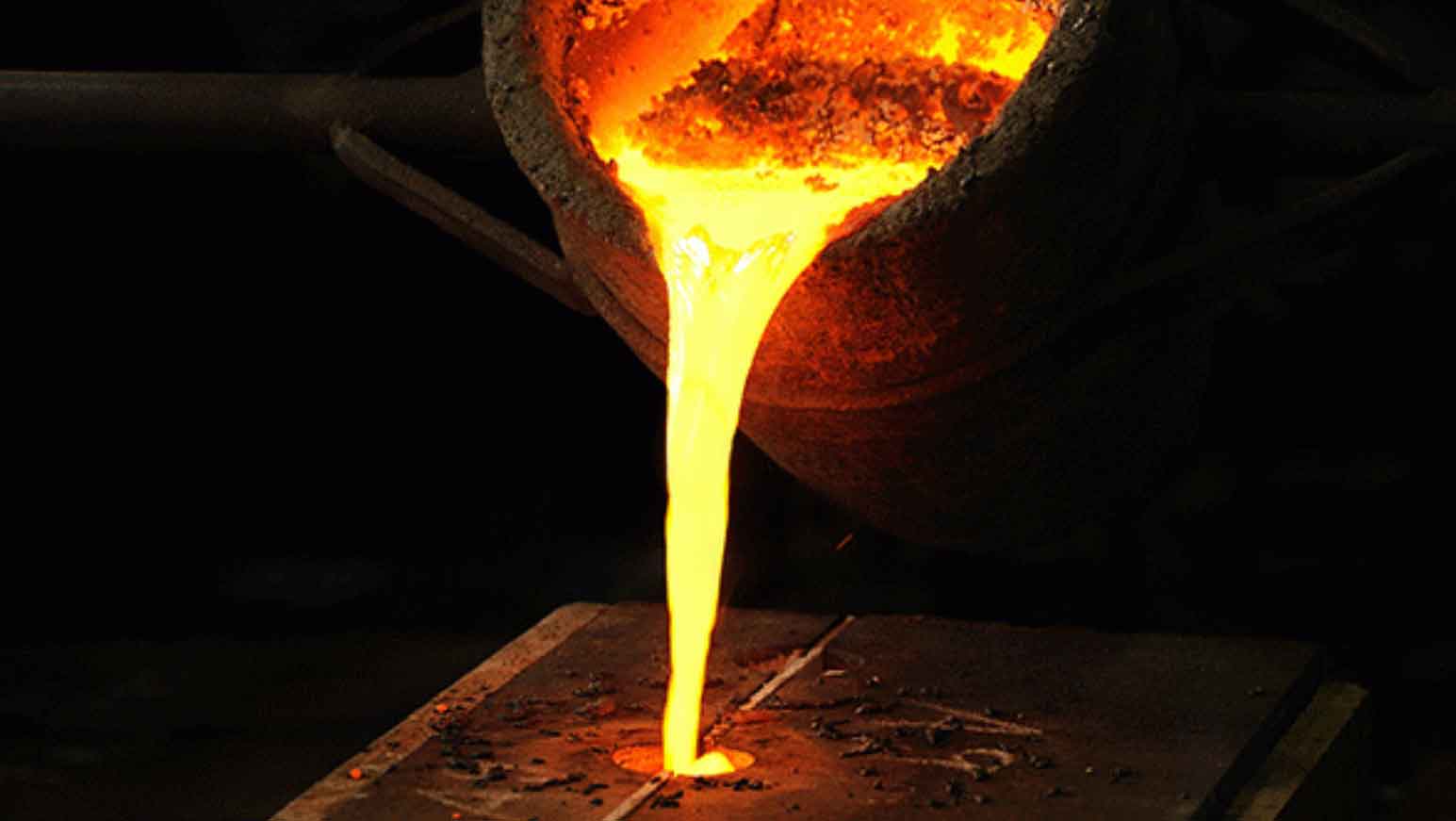
Sand casting is a traditional form of metal forming that has been used for thousands of years. The process involves creating a sand-based mold to shape molten metal into desired forms. Despite its age-old roots, sand casting manufacturing has faced modern scrutiny due to environmental concerns. However, integrating sustainable practices into sand casting can significantly enhance its environmental footprint while also improving efficiency and reducing costs. This article explores several sustainable strategies in sand casting manufacturing.
1. Green Sand Reclamation and Use
One of the primary components of sand casting manufacturing is the green sand—named for its wet state rather than its color—which can be reused in numerous casting processes. Optimizing the reclamation of green sand not only minimizes waste but also reduces the need for new raw materials. Manufacturers can enhance green sand recovery by implementing advanced mechanical and thermal reclamation systems that clean and refresh the sand for repeated use. Moreover, sourcing local sand reduces transportation-related emissions, further enhancing the process’s sustainability.
2. Energy Efficiency in Melting Processes
Melting metal requires significant energy, typically obtained from burning fossil fuels, which contributes to greenhouse gas emissions. To counteract this, manufacturers can adopt energy-efficient furnaces, such as induction furnaces that reduce energy consumption and enhance melting rates. Implementing process controls that optimize furnace operation times and temperatures can also conserve energy. Additionally, integrating waste heat recovery systems helps in repurposing the heat generated during metal melting for other uses within the facility, such as heating or preheating other materials.
3. Enhanced Material Efficiency
Material efficiency is crucial in reducing waste and operational costs in sand casting manufacturing. Techniques such as optimizing the design of gating systems—the channels through which molten metal flows into the mold—can substantially decrease material usage and waste. Advanced simulation software helps predict and improve the quality of sand casting manufacturing before actual production, minimizing the likelihood of defects and reducing the need for multiple prototypes.
4. Recycling and Effective Waste Management
Recycling plays a pivotal role in sustainable sand casting manufacturing. Beyond reusing sand, recycling scrap metal and other by-products is essential. Effective separation and collection systems enable the recovery of metals that can be melted down and reused, reducing the demand for virgin raw materials. Proper disposal or repurposing of non-recyclable materials, such as spent binders or sand contaminated with hazardous materials, is also vital. Exploring secondary markets, like construction or agriculture, where spent sand can be used, helps in diverting waste from landfills.
5. Alternative Materials and Technologies
Exploring alternative mold materials and binders that have a lower environmental impact than traditional sand and clay can further green the sand casting manufacturing. Research into biodegradable and less energy-intensive binders is ongoing, promising to reduce the emissions associated with traditional materials. Innovations like 3D printing of sand molds can also enhance precision in sand casting manufacturing, reducing waste and potentially decreasing the reliance on conventional binders.
6. Water Conservation Techniques
Since green sand must be kept moist, sand casting manufacturing can consume considerable amounts of water. Implementing water recycling systems in the sand preparation process is crucial for sustainable operation. These systems clean and recycle water, significantly cutting down on overall water use. Additionally, moisture control systems can optimize the amount of water used, ensuring that the sand retains sufficient moisture without excess.
7. Focus on Worker Safety and Environmental Health
Sustainable practices in sand casting manufacturing also extend to improving the safety and health conditions in manufacturing facilities. Reducing exposure to silica dust and other hazardous emissions through improved ventilation systems, proper protective equipment, and regular health monitoring ensures a safer working environment. This not only helps in compliance with environmental and safety regulations but also improves employee satisfaction and productivity.
Conclusion
Integrating sustainable practices into sand casting manufacturing is not just about reducing environmental impact—it also enhances operational efficiency and can lead to significant cost savings. As industries worldwide strive towards greener manufacturing processes, sand casting manufacturing can remain a viable and environmentally responsible option by adopting these sustainable strategies. This transition not only helps manufacturers meet stricter regulatory standards but also aligns with the growing consumer demand for responsibly produced products.