Sand casting is a traditional and widely used method for producing metal components. Despite its simplicity, it can be challenging to create complex geometries with high precision using conventional sand casting techniques. However, recent advancements in sand casting have made it possible to produce intricate shapes with improved accuracy and surface finish. This article explores advanced sand casting techniques for complex geometries, focusing on modern methods and materials that enhance the capabilities of sand casting.
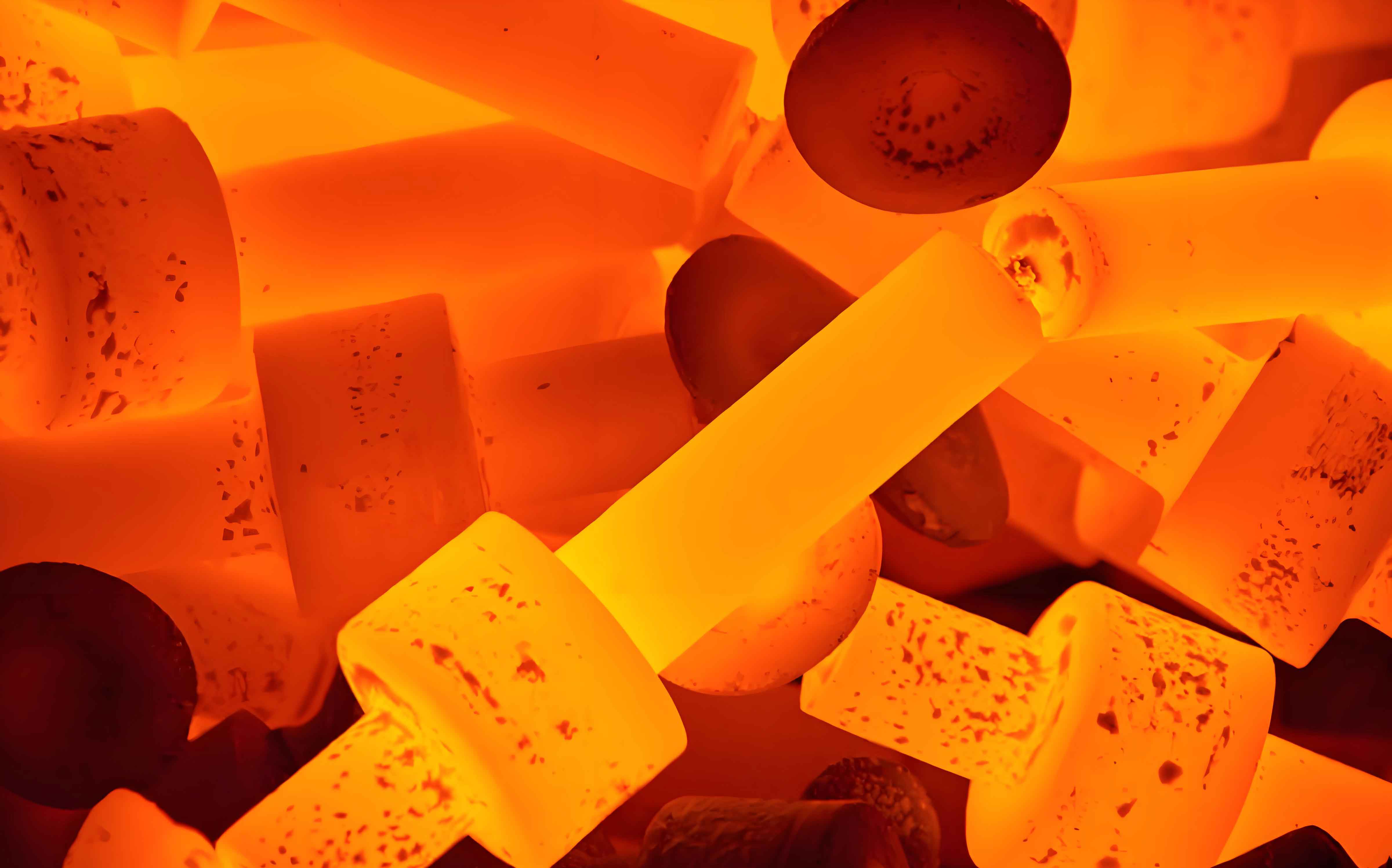
Advanced Sand Casting Techniques
- 3D Printing of Sand Molds and CoresThe integration of 3D printing technology in sand casting has revolutionized the creation of molds and cores. 3D printing allows for the direct fabrication of sand molds and cores from digital models, eliminating the need for traditional pattern making.Benefits of 3D Printed Sand Molds and Cores1. Ability to create intricate and complex geometries2. Reduced lead time and cost3. Improved dimensional accuracy4. Flexibility in design changes3D printed sand molds and cores offer significant advantages in terms of design flexibility and precision. They enable the production of complex internal features and undercuts that are difficult to achieve with conventional sand casting methods.
- Binder JettingBinder jetting is an additive manufacturing process that uses a binder material to selectively join sand particles layer by layer. This process is particularly effective for creating complex molds and cores with high precision.Steps in Binder Jetting Process1. Spread a thin layer of sand2. Apply binder selectively to the sand layer3. Repeat the process layer by layer4. Remove loose sand and cure the binderBinder jetting allows for the production of molds and cores with intricate geometries, thin walls, and fine details. The process is also faster and more cost-effective compared to traditional sand casting methods.
- Lost Foam CastingLost foam casting involves creating a foam pattern of the desired shape, coating it with a refractory material, and then placing it in a sand mold. When molten metal is poured into the mold, the foam pattern vaporizes, leaving behind a cavity that forms the final casting.Advantages of Lost Foam Casting1. Simplification of mold-making process2. Ability to cast complex shapes with high accuracy3. Improved surface finish4. Reduction in machining and finishing operationsLost foam casting is ideal for producing castings with complex geometries, such as automotive engine blocks and intricate mechanical components. The process also minimizes defects and reduces the need for post-casting machining.
- Vacuum Sealed Molding (V-Process)The vacuum sealed molding process, also known as the V-Process, uses a vacuum to hold the sand mold in place without the need for binders or additives. This process involves placing a thin plastic film over the pattern, creating a vacuum, and then filling the mold with sand.Steps in Vacuum Sealed Molding Process1. Place plastic film over the pattern2. Create a vacuum to hold the film in place3. Fill the mold with sand4. Apply vacuum to compact the sand5. Pour molten metal into the moldThe V-Process is advantageous for casting complex geometries with excellent surface finish and dimensional accuracy. It also reduces waste and allows for easy removal of the mold.
Materials for Advanced Sand Casting
The choice of materials used in sand casting significantly impacts the quality and properties of the final casting. Advanced materials and additives have been developed to enhance the performance of sand molds and cores.
- High-Strength SandHigh-strength sand materials, such as silica sand with additives, improve the mold’s ability to withstand high temperatures and mechanical stresses. These materials are essential for producing complex geometries that require precise detail and stability during casting.Characteristics of High-Strength Sand1. Improved thermal stability2. Enhanced mechanical strength3. Reduced thermal expansion4. Better dimensional accuracy
- Resin-Bonded SandResin-bonded sand is a type of sand mixture that uses resin as a binder. This material provides excellent mold strength and surface finish, making it suitable for casting complex shapes.Benefits of Resin-Bonded Sand1. High mold strength2. Smooth surface finish3. Reduced defects and inclusions4. Better dimensional control
- Ceramic SandCeramic sand is an advanced material used in sand casting for its superior thermal and mechanical properties. It is particularly effective for high-temperature applications and producing castings with fine details.Properties of Ceramic Sand1. High thermal resistance2. Excellent mechanical strength3. Low thermal expansion4. Improved surface finish
Applications of Advanced Sand Casting Techniques
Advanced sand casting techniques have expanded the range of applications for this versatile casting method. They enable the production of complex and high-precision components for various industries.
- Automotive IndustryIn the automotive industry, advanced sand casting techniques are used to produce engine blocks, cylinder heads, and other intricate components. The ability to create complex geometries with high accuracy and surface finish is essential for improving engine performance and efficiency.
- Aerospace IndustryThe aerospace industry benefits from advanced sand casting techniques for producing lightweight and high-strength components. Complex geometries, such as turbine blades and structural components, are cast with precision to meet stringent performance requirements.
- Industrial MachineryIndustrial machinery and equipment often require robust and intricately shaped components. Advanced sand casting techniques provide the flexibility and precision needed to produce gears, housings, and other critical parts with complex geometries.
- Energy SectorIn the energy sector, advanced sand casting techniques are used to create components for power generation, such as turbine blades and heat exchangers. The ability to cast complex shapes with high accuracy and material integrity is crucial for the efficiency and reliability of energy systems.
Conclusion
Advanced sand casting techniques have significantly enhanced the capabilities of traditional sand casting, enabling the production of complex geometries with improved precision and surface quality. Methods such as 3D printing of sand molds, binder jetting, lost foam casting, and vacuum sealed molding offer significant advantages in terms of design flexibility, cost-effectiveness, and accuracy. Additionally, the use of advanced materials like high-strength sand, resin-bonded sand, and ceramic sand further improves the performance of sand castings. These advancements have broadened the applications of sand casting across various industries, making it a vital process for producing high-quality, intricate metal components.
4o