Despite the limitations of sand casting in terms of surface finish, dimensional accuracy, and intricacy, it remains a popular method for producing metal parts due to its numerous advantages:
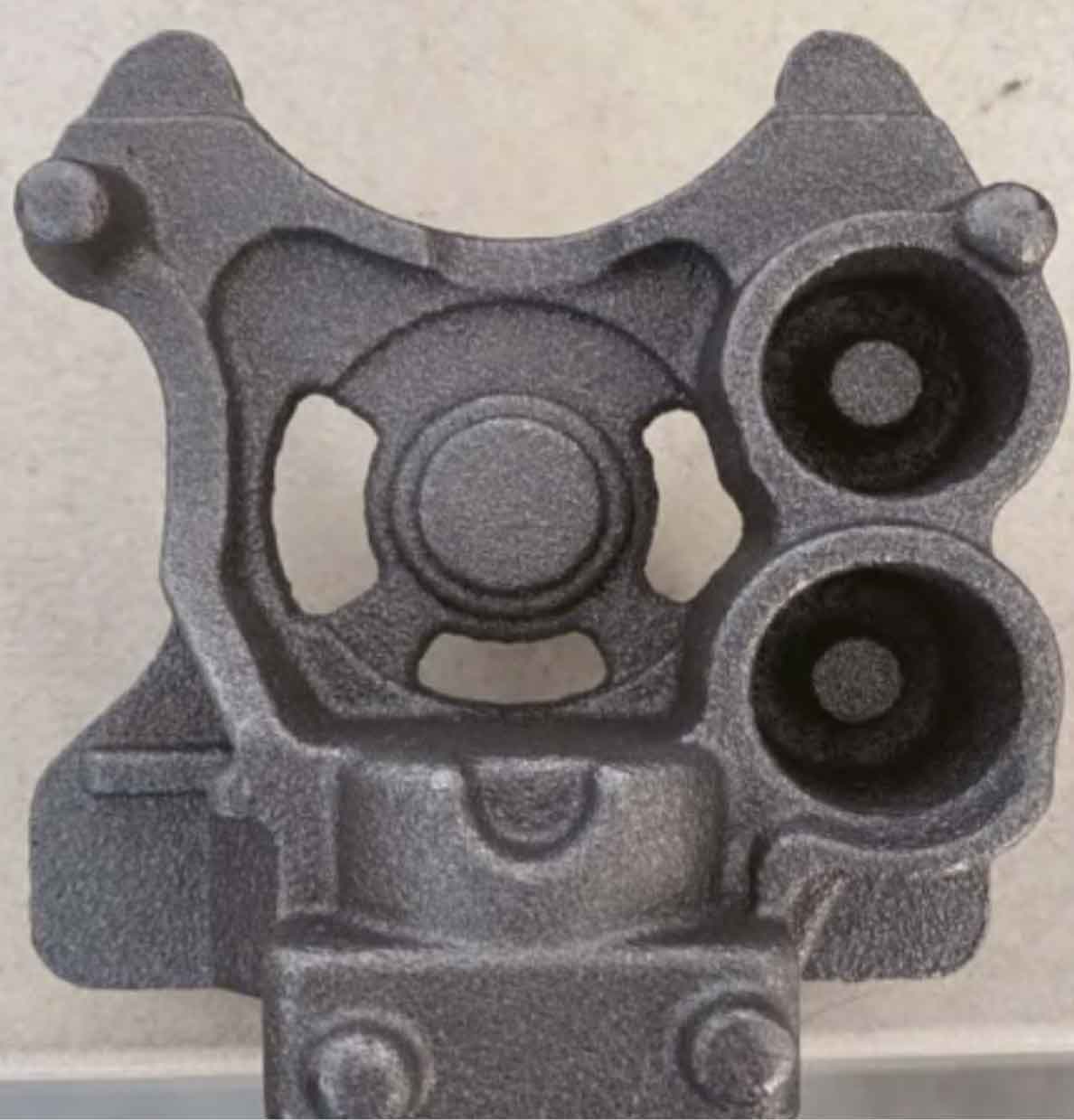
- Low-cost tooling: Sand casting typically requires less expensive tooling compared to other casting methods, making it more cost-effective for small to medium production runs or for producing large, complex parts.
- Material versatility: Sand casting can be used with a wide range of metals, including iron, steel, aluminum, copper, and magnesium alloys. This makes it suitable for many different applications across various industries.
- Large part capability: Sand casting is well-suited for producing large and heavy components, as there are fewer restrictions on the size and weight of the part compared to other casting methods, such as die casting or investment casting.
- Design flexibility: Sand casting allows for the production of parts with complex geometries and internal structures. While it may not achieve the same level of intricacy as investment casting, it still offers a good degree of design flexibility.
- Short lead times: The sand casting process can have relatively short lead times compared to other casting methods, making it suitable for rapid prototyping or when a quick turnaround is required.
Despite these advantages, it’s essential to consider the specific requirements of each project when selecting a casting method. If higher levels of precision, intricacy, or surface finish are required, alternative casting methods such as investment casting or die casting may be more appropriate. Additionally, for high-volume production, the cost savings from sand casting may be offset by the increased labor and material costs involved in producing and cleaning individual sand molds. In such cases, die casting, which employs reusable molds, may prove to be a more economical choice.