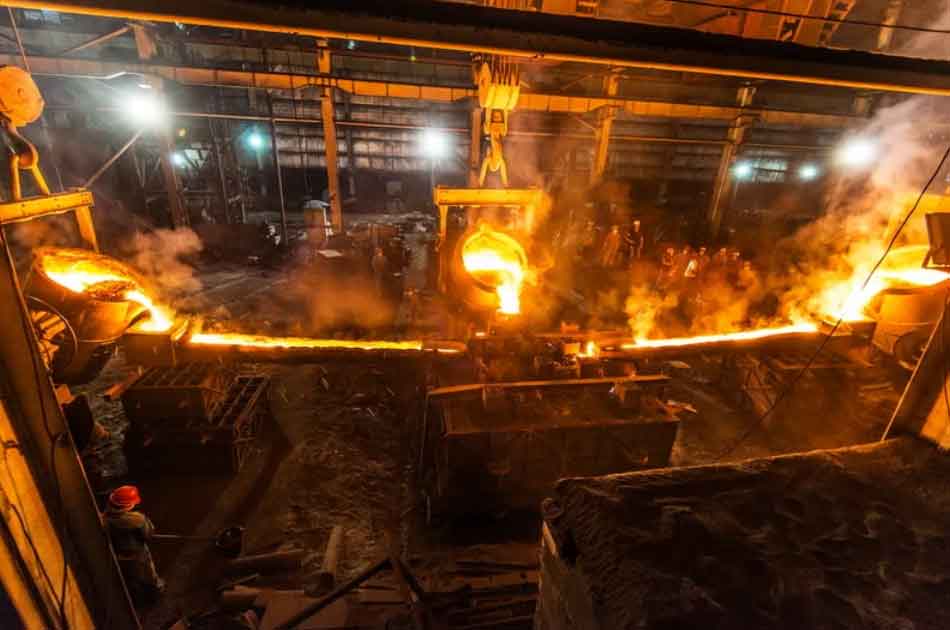
Lost Foam Casting has a very detailed process during its making. Firstly, we need to produce some empty foam model to make a complete casting system, then brush the tailor-made painting on the pervaporation and need to be totally dried.
Lost foam casting, also known as evaporative pattern casting, is a modern and versatile casting process that allows for the production of complex and intricate metal parts. The process involves creating a foam pattern, coating it with refractory materials, and then pouring molten metal into the coated pattern to form the final casting. Here’s a step-by-step overview of the technological process of lost foam casting:
Secondly, we need to install the tailor-made inter-layer sand box on the vibration table which should be filled with dried sand. Then make the bottom sand hard enough on the vibration table, smoothing and filling sand around it after putting the dried pervaporation on the bottom sand.
Thirdly of the lost foam casting technological process, the top of the sand box need to be covered with plastic film. Using the pouring cup to inhaling the air from the box. Then we could start to pour metal inside after the dried sand is hard enough and be shaped.
At last of the lost foam casting technological process, we need to release the vacuum. After the condensation of the casting which should be turn over which will make it easier to take out the casting mold from the box.
- Pattern Creation:
- The process begins with the creation of a pattern made of expandable polystyrene (EPS) foam. The foam pattern represents the exact shape and dimensions of the desired metal part.
- Pattern Assembly:
- Multiple foam patterns may be attached or assembled together to form a complete casting cluster. This cluster of foam patterns is known as the foam pattern tree.
- Pattern Coating:
- The foam pattern tree is coated with a refractory material, typically a fine-grain sand and binder mixture. The coating process can be achieved through dipping, spraying, or sand slurry coating.
- Drying:
- After coating, the refractory material is allowed to dry and cure. The drying process helps strengthen the coating and ensures the foam pattern remains intact during the casting process.
- Mold Assembly:
- The coated foam pattern tree is placed inside a flask, which is a container that holds the mold. The flask is filled with unbonded sand to surround the coated foam pattern.
- Vibration and Compaction:
- The flask with the coated foam pattern inside is vibrated and compacted to ensure the sand fully surrounds and conforms to the pattern’s shape.
- Molten Metal Pouring:
- Once the mold is ready, molten metal is poured into the mold cavity through a pouring basin or gating system. The high temperature of the molten metal causes the foam pattern to vaporize and escape, leaving behind a cavity in the shape of the original pattern.
- Solidification and Cooling:
- The molten metal in the mold cavity solidifies and cools, taking the shape of the foam pattern. As the metal cools, it shrinks slightly, creating a small space between the casting and the refractory mold coating.
- Casting Removal:
- Once the metal has fully solidified and cooled, the flask is removed, and the casting is extracted from the sand mold.
- Finishing::
- OAfter casting removal, the final casting may undergo additional finishing processes such as trimming, grinding, and surface treatments to achieve the desired dimensions and surface quality.
The lost foam casting process is ideal for producing complex and intricate parts with tight tolerances. It offers benefits such as reduced tooling costs, minimal material waste, and the ability to cast multiple parts simultaneously. The process is widely used in various industries, including automotive, aerospace, and machinery manufacturing.