Sand casting parts are an essential process in industrial manufacturing, known for its versatility and cost-effectiveness, especially in producing complex shapes and large parts. Here’s a guide to understanding sand casting parts for industrial use, drawn from a variety of comprehensive sources.
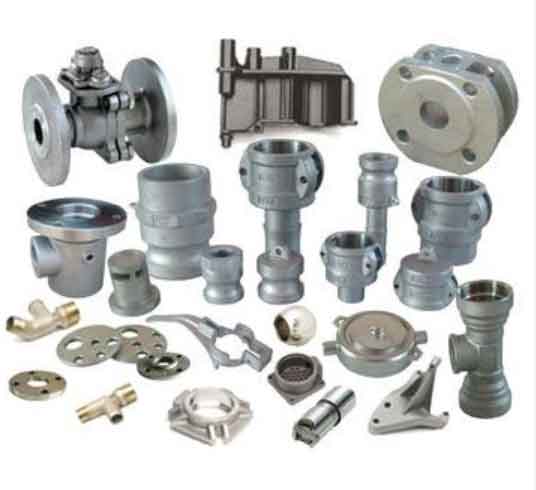
Pattern Creation
Pattern creation is the first step in the sand casting parts process. Patterns, made from materials like wood, plastic, or metal, are replicas of the final product and are used to create the sand mold cavity. The complexity of patterns varies based on the product, with intricate details possible for applications like pump manufacturing. It’s crucial that the pattern design incorporates draft angles to facilitate easy removal from the mold and is made from materials that can withstand sand casting parts process.
Mold Preparation
In mold preparation, the chosen sand is mixed with binders to enhance strength and withstand high temperatures during metal pouring. Sand properties like grain shape, size, refractoriness, and permeability are critical for mold quality. The mold is typically made in two halves: the cope (top) and the drag (bottom).
Core Making
Cores are used to create internal cavities and complex internal features in sand casting parts. They must be strong enough to withstand the molten metal yet weak enough to break away after solidification. The core-making process involves using materials that ensure minimal gas formation and can withstand high temperatures.
Metal Pouring and Cooling
The molten metal, heated in a furnace, is poured into the mold through a gating system. It’s essential to control the pouring speed and the cooling rate, as these factors significantly affect the casting’s microstructure and properties. Cooling rate influences shrinkage, porosity, and potential cracks in the final product.
Shakeout and Cleaning
After cooling, sand casting parts is removed from the mold. This process, known as shakeout, involves breaking the mold and cleaning the casting of sand and other residues. Techniques like high-pressure air or water jets, saws, chisels, and torches are used for cleaning. The surface finish of sand casting parts is also evaluated and can be enhanced through processes like polishing or grinding if needed.
Finishing
The final step involves machining and finishing sand casting parts to achieve the desired dimensions and surface quality. The machining allowance is predetermined to compensate for any extra material that needs to be removed to achieve the final product dimensions.
Comparison with Other Manufacturing Methods
Compared to other manufacturing methods, sand casting parts stands out for its ability to produce parts with complex shapes, including intricate internal passages. It is especially suitable for parts like pump components, where strength and the ability to handle high-pressure are crucial. While the surface finish and tolerances can be managed effectively, additional machining might be required for precision applications.
Materials and Applications
Sand casting parts are utilized across various industries, with automotive and aerospace industries being significant users. It’s capable of working with almost any metal alloy, making it versatile for different applications. The automotive industry, for example, uses sand casting parts for engine components, while aerospace applications include parts like turbine blades.
Environmental Considerations
Industries are increasingly focusing on sustainable practices in sand casting parts. This includes efforts to recycle and reuse sand, as well as reduce energy consumption in the metal melting process.
This overview provides a basic understanding of the sand casting parts process and its applications in industrial manufacturing. The method’s adaptability and ability to produce complex designs make it invaluable for a range of industries.