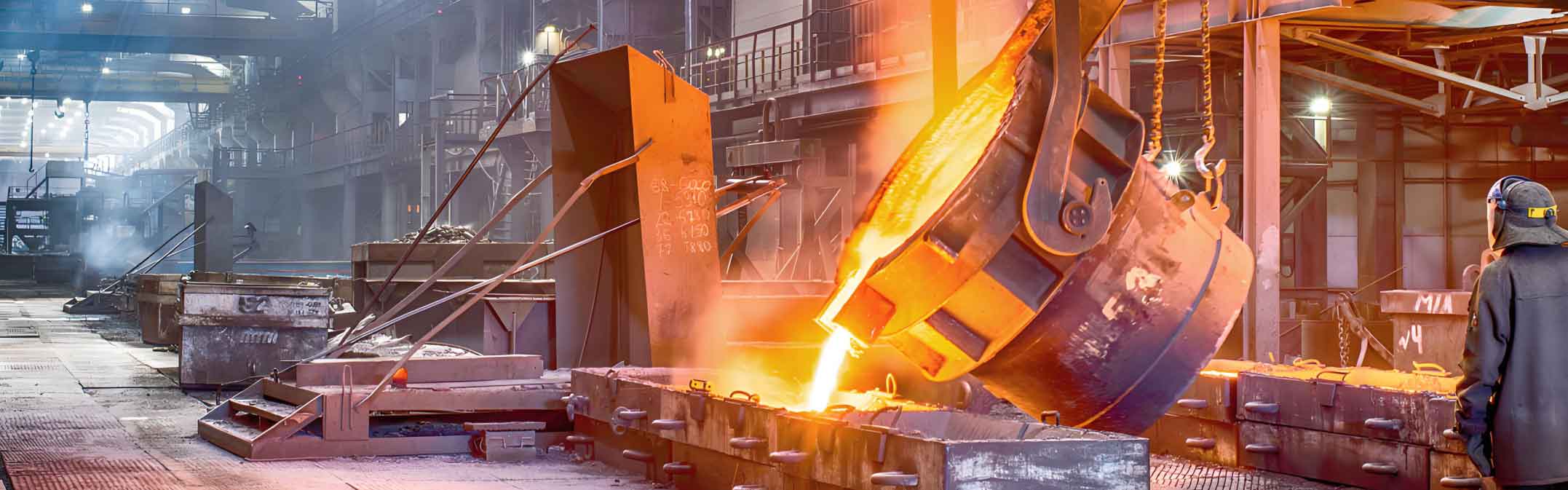
Casting is a critical manufacturing process used to produce a wide variety of components with complex geometries and high precision. Among the various casting techniques, investment casting, sand casting, and lost foam casting stand out for their distinct advantages and applications. This article provides a comprehensive comparative analysis of these three casting methods, focusing on their efficiency and quality, to help manufacturers select the most suitable process for their specific needs.
ZHY Casting
China Leading Engineer Team. 40+ Years' Experience of Casting Manufacture!
Introduction to Casting Methods
Investment Casting
Investment casting, also known as precision casting or lost-wax casting, involves creating a wax model of the desired part, coating it with a ceramic material to form a mold, and then melting away the wax to leave a cavity. Molten metal is poured into this cavity to create the final part. This process is known for its ability to produce highly detailed and precise components with excellent surface finishes.
Sand Casting
Sand casting involves creating a mold from a sand mixture, into which molten metal is poured to form the final part. The mold is typically created by packing sand around a pattern of the desired shape. Sand casting is widely used for producing large components and parts with simple to moderately complex geometries.
Lost Foam Casting
Lost foam casting is a variant of investment casting that uses a foam pattern instead of a wax model. The foam pattern is coated with a refractory material to form a mold, and when molten metal is poured into the mold, the foam evaporates, leaving the final part. This method is known for its ability to produce complex shapes with good dimensional accuracy.
Comparative Analysis of Casting Methods
Efficiency
Efficiency in casting is determined by factors such as production speed, material utilization, and labor requirements.
- Investment Casting:
- Production Speed: Moderate to high, depending on the complexity of the parts and the batch size.
- Material Utilization: High, due to precise mold creation and minimal material waste.
- Labor Requirements: Moderate to high, involving skilled labor for pattern creation and mold preparation.
- Sand Casting:
- Production Speed: High for large batches, as sand molds can be quickly prepared and reused.
- Material Utilization: Moderate, with some material waste due to the sand mold and gating system.
- Labor Requirements: Moderate, with less need for highly skilled labor compared to investment casting.
- Lost Foam Casting:
- Production Speed: Moderate, as creating foam patterns and coating them requires time.
- Material Utilization: High, similar to investment casting, with minimal material waste.
- Labor Requirements: Moderate to high, depending on the complexity of the foam patterns.
Quality
Quality in casting is evaluated based on precision, surface finish, and the ability to produce complex geometries.
- Investment Casting:
- Precision: Very high, capable of producing intricate details and tight tolerances.
- Surface Finish: Excellent, often requiring minimal post-processing.
- Complex Geometries: Highly suitable for complex shapes and fine details.
- Sand Casting:
- Precision: Moderate, with larger tolerances compared to investment casting.
- Surface Finish: Fair, typically requiring additional machining and finishing.
- Complex Geometries: Suitable for simpler shapes; complex geometries are challenging.
- Lost Foam Casting:
- Precision: High, though slightly less than investment casting.
- Surface Finish: Good, with some potential for surface imperfections.
- Complex Geometries: Well-suited for complex shapes, similar to investment casting.
Comparative Table
Parameter | Investment Casting | Sand Casting | Lost Foam Casting |
---|---|---|---|
Production Speed | Moderate to High | High | Moderate |
Material Utilization | High | Moderate | High |
Labor Requirements | Moderate to High | Moderate | Moderate to High |
Precision | Very High | Moderate | High |
Surface Finish | Excellent | Fair | Good |
Complex Geometries | Highly Suitable | Suitable for Simple Shapes | Highly Suitable |
Initial Cost | High | Low | Moderate |
Tooling Cost | High | Low | Moderate |
Application | Aerospace, Medical Devices, High-Precision Parts | Large Components, Simple Geometries | Complex Shapes, Automotive Parts |
Applications and Industry Use Cases
Investment Casting
- Aerospace: Production of turbine blades, engine components, and structural parts requiring high precision and strength.
- Medical Devices: Manufacturing of surgical instruments, implants, and dental devices where biocompatibility and precision are critical.
- Automotive: High-performance engine parts, transmission components, and intricate mechanical parts.
Sand Casting
- Heavy Machinery: Large housings, frames, and brackets where dimensional tolerances are less critical.
- Automotive: Engine blocks, cylinder heads, and other large components.
- Construction: Infrastructure components such as manhole covers, drainage grates, and heavy equipment parts.
Lost Foam Casting
- Automotive: Complex engine parts, transmission cases, and suspension components.
- Industrial Equipment: Pump housings, valve bodies, and machinery components requiring complex geometries.
- Consumer Goods: Production of intricate parts for appliances and machinery.
Future Trends and Innovations
The future of casting technology is likely to be influenced by several key trends:
- Digital Manufacturing: Integration of digital tools such as CAD/CAM and simulation software to optimize casting designs and processes.
- Advanced Materials: Development of new alloys and composite materials that enhance the performance and durability of cast parts.
- Sustainability: Adoption of eco-friendly materials and energy-efficient processes to reduce the environmental impact of casting.
- Automation: Increased use of robotics and automated systems to improve production efficiency and consistency.
Conclusion
Investment casting, sand casting, and lost foam casting each offer distinct advantages and are suited to different applications based on their efficiency and quality characteristics. Investment casting is ideal for high-precision and complex parts, particularly in aerospace and medical devices. Sand casting is well-suited for large, simpler components, making it a cost-effective choice for heavy machinery and automotive applications. Lost foam casting bridges the gap, offering good precision and the ability to produce complex geometries, making it suitable for automotive and industrial equipment.
In summary, selecting the appropriate casting method requires careful consideration of the specific requirements of the application, including precision, surface finish, material utilization, and production efficiency. By understanding the strengths and limitations of each method, manufacturers can optimize their processes, reduce costs, and enhance the quality of their products.