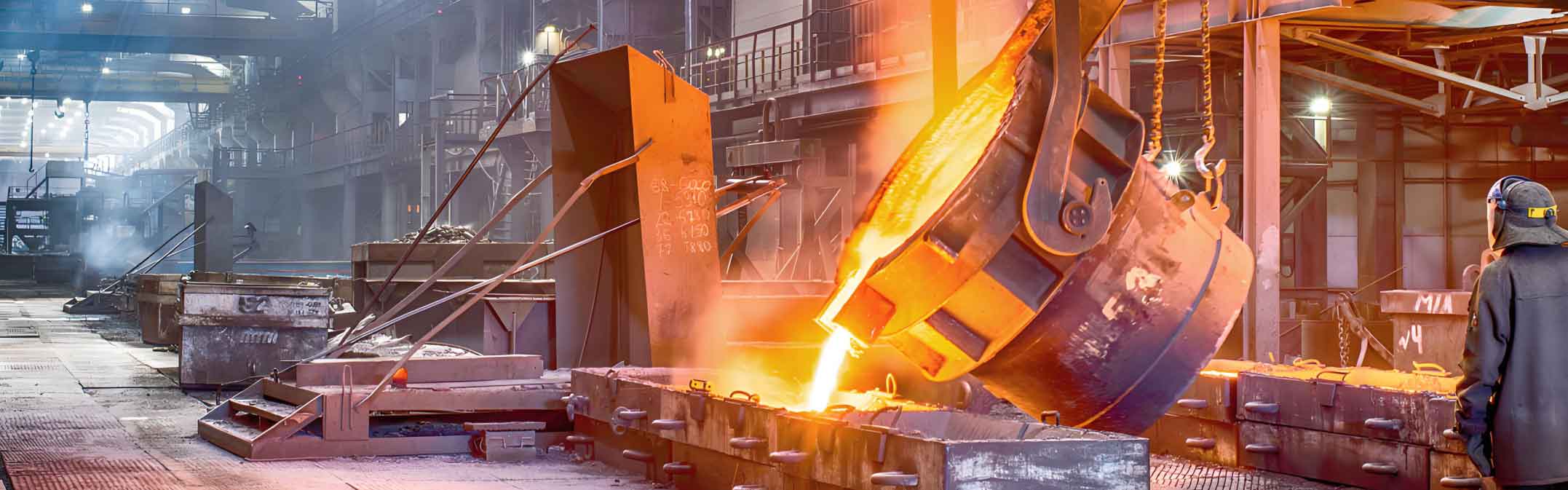
Lost foam casting has become a vital manufacturing process in the automotive industry, providing numerous advantages for the production of complex and high-performance components. This method allows for the creation of parts with intricate shapes and precise dimensions, which are essential in modern automotive design and engineering. This article explores the role of lost foam casting in the automotive industry, detailing its benefits, applications, and future prospects.
Introduction
Lost foam casting is a process that uses a foam pattern, which is coated with a refractory material and then buried in sand. When molten metal is poured into the mold, the foam pattern vaporizes, leaving behind a detailed metal casting. This technique has revolutionized the production of automotive components by enabling the creation of complex geometries with high precision and surface finish.
Benefits of Lost Foam Casting in the Automotive Industry
- Complex Geometry and Precision
- Material Efficiency
- Cost Reduction
- Improved Surface Finish
- Reduction in Machining and Assembly
Complex Geometry and Precision
Lost foam casting allows for the production of parts with complex geometries that would be difficult or impossible to achieve using traditional casting methods. This capability is particularly beneficial for automotive components that require intricate designs for improved performance and efficiency.
Examples:
- Engine Blocks: Intricate cooling passages and lightweight designs.
- Transmission Cases: Complex shapes for optimized performance.
Material Efficiency
This casting method minimizes material waste because the foam pattern is completely consumed during the casting process. The precise control over the pattern and mold also reduces the need for excess material, leading to more efficient use of resources.
Benefits:
- Reduced Scrap: Less material waste translates to lower costs and environmental impact.
- Material Optimization: Engineers can design components with minimal material without compromising strength and durability.
Cost Reduction
Lost foam casting can significantly reduce production costs by simplifying the manufacturing process. The ability to cast complex shapes in a single step eliminates the need for multiple operations and reduces the overall production time.
Cost-Saving Aspects:
- Fewer Tooling Requirements: Simplified tooling reduces initial investment and maintenance costs.
- Less Post-Processing: Reduced need for machining and finishing operations.
Improved Surface Finish
The use of a smooth foam pattern and fine refractory coating results in a superior surface finish on the cast parts. This improved finish not only enhances the aesthetic appeal but also reduces the need for extensive post-casting finishing operations.
Applications:
- Exterior Components: Parts such as brackets and mounts that are visible and require a smooth finish.
- Internal Engine Components: Improved surface finish can enhance performance and reduce wear.
Reduction in Machining and Assembly
Lost foam casting can produce near-net-shape parts, which require minimal machining. The ability to integrate multiple components into a single casting reduces the need for assembly, lowering labor costs and improving overall part reliability.
Examples:
- Integrated Manifolds: Combining intake and exhaust manifolds into a single casting.
- Complex Housings: Casting components with integrated features that eliminate the need for assembly.
Table of Lost Foam Casting Benefits in Automotive Applications
Benefit | Description | Examples |
---|---|---|
Complex Geometry and Precision | Ability to cast intricate shapes with high accuracy | Engine blocks, transmission cases |
Material Efficiency | Minimizes material waste and optimizes resource use | Reduced scrap, material optimization |
Cost Reduction | Lowers production costs through simplified processes | Fewer tooling requirements, less post-processing |
Improved Surface Finish | Results in superior surface quality on cast parts | Exterior components, internal engine parts |
Reduction in Machining and Assembly | Produces near-net-shape parts, reducing further operations | Integrated manifolds, complex housings |
Practical Applications in the Automotive Industry
- Engine Components
- Transmission Systems
- Suspension Parts
- Brake Components
- Structural Parts
Engine Components
Lost foam casting is widely used in the production of engine components due to its ability to create intricate internal features. This method is ideal for casting engine blocks, cylinder heads, and intake manifolds, where complex cooling channels and lightweight designs are essential.
Key Components:
- Engine Blocks: Improved cooling and reduced weight.
- Cylinder Heads: Optimized combustion chamber designs.
- Intake Manifolds: Smooth airflow passages for better performance.
Transmission Systems
Transmission components require high precision and strength, making lost foam casting an ideal choice. The ability to cast complex shapes in a single step ensures that parts like transmission cases and housings meet the stringent requirements of modern automotive designs.
Key Components:
- Transmission Cases: Complex shapes for optimal performance.
- Housings: Integrated features that reduce assembly needs.
Suspension Parts
Suspension components, such as control arms and knuckles, benefit from the high strength-to-weight ratio provided by lost foam casting. The process allows for the creation of durable parts that can withstand the stresses of vehicle operation while maintaining a lightweight design.
Key Components:
- Control Arms: High strength and durability.
- Knuckles: Complex shapes with integrated mounting points.
Brake Components
The precision and surface finish achievable with lost foam casting make it suitable for critical brake components. Parts such as calipers and brackets can be cast with high accuracy, ensuring reliable performance and safety.
Key Components:
- Brake Calipers: Precise shapes for effective braking.
- Brackets: Durable and lightweight designs.
Structural Parts
Lost foam casting is also used to produce various structural parts within a vehicle. These components benefit from the process’s ability to create complex shapes with high precision and excellent surface finish.
Key Components:
- Mounts: Engine and transmission mounts with integrated features.
- Brackets: Structural supports with complex geometries.
Future Trends and Research
- Advanced Materials:
- Ongoing research into new alloys and composite materials will further enhance the properties of cast components, leading to better performance and durability.
- Automation and AI:
- The integration of automation and artificial intelligence in the casting process will improve precision, reduce defects, and increase production efficiency.
- Sustainability:
- Efforts to develop more sustainable casting methods and materials will reduce the environmental impact of lost foam casting.
- Enhanced Simulation Tools:
- Advanced simulation tools will allow for better prediction and control of the casting process, leading to further optimization and improved component quality.
Conclusion
Lost foam casting plays a crucial role in the automotive industry, offering numerous benefits that enhance the production and performance of vehicle components. By enabling the creation of complex geometries with high precision, improving material efficiency, reducing costs, and minimizing the need for extensive machining and assembly, this casting technique has become indispensable. As advancements in materials, automation, and sustainability continue to drive innovation, the future of lost foam casting in the automotive industry looks promising, with even greater potential for improving vehicle performance and efficiency.