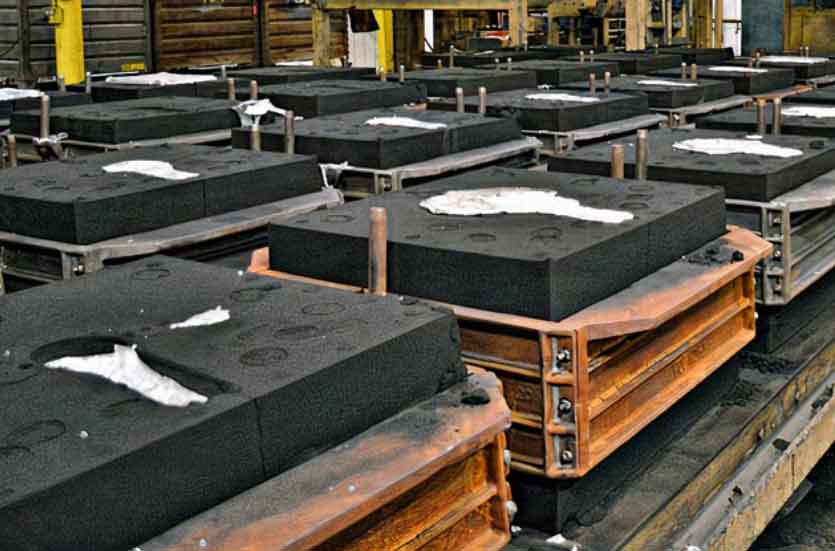
Simulation plays a crucial role in resin sand casting by streamlining the casting process, optimizing designs, and identifying potential issues before actual production. The use of advanced simulation software has become increasingly popular in foundries as it offers numerous benefits that contribute to improved efficiency and cost-effectiveness. Here’s the role of simulation in resin sand casting:
1. Mold Filling Analysis:
- Simulation software allows foundries to conduct mold filling analysis, providing a virtual representation of how molten metal flows and fills the mold cavity. This helps optimize gating and risering designs to achieve a smooth and controlled filling process.
2. Solidification Analysis:
- Solidification analysis predicts the cooling and solidification behavior of the metal in the mold, allowing for the identification of potential defects like shrinkage, porosity, and hot spots. By analyzing solidification patterns, foundries can optimize the process parameters to reduce defects and enhance casting quality.
3. Design Optimization:
- Simulation tools enable designers to evaluate various design iterations virtually, assessing the impact of changes in geometry or material on casting quality and performance. This iterative process helps achieve an optimized design before the physical production begins, saving time and costs.
4. Defect Prediction and Prevention:
- Simulation identifies potential defects and problem areas in the mold and casting process, allowing foundries to implement preventive measures and improve the overall quality of the castings. This helps reduce the likelihood of costly rework and scrap.
5. Process Parameters Optimization:
- Through simulation, foundries can optimize various process parameters, such as pouring temperature, mold temperature, and cooling time, to achieve the desired casting properties and surface finish.
6. Material Selection:
- Simulation can aid in material selection by evaluating the performance of different alloys and materials in the casting process. This ensures that the chosen material meets the specific requirements of the application.
7. Cost Reduction:
- By detecting potential issues early in the virtual phase, simulation minimizes the need for costly physical prototypes and iterative testing. This leads to cost savings and faster time-to-market for new components.
8. Environmental Impact:
- Simulation contributes to a more sustainable casting process by reducing material waste, energy consumption, and the overall environmental impact of foundry operations.
9. Training and Skill Development:
- Simulation software provides a valuable training tool for foundry personnel, allowing them to gain experience and expertise in the casting process without the need for physical prototypes.
In conclusion, simulation plays a crucial role in resin sand casting by streamlining the casting process, improving casting quality, and optimizing designs. It enables foundries to make informed decisions, reduce defects, and achieve cost-effective and high-quality castings, ultimately enhancing their competitiveness in the market.