The sand casting process is a traditional and widely used method for shaping metal objects. It is an art form that has been practiced for centuries and is still relevant in modern manufacturing. In sand casting, a pattern of the desired object is created using various materials, and then a mold is made by packing sand around the pattern. Once the mold is prepared, molten metal is poured into the mold cavity, allowing it to solidify and take the shape of the pattern. Finally, the mold is broken apart, and the newly formed metal object, known as the casting, is removed.
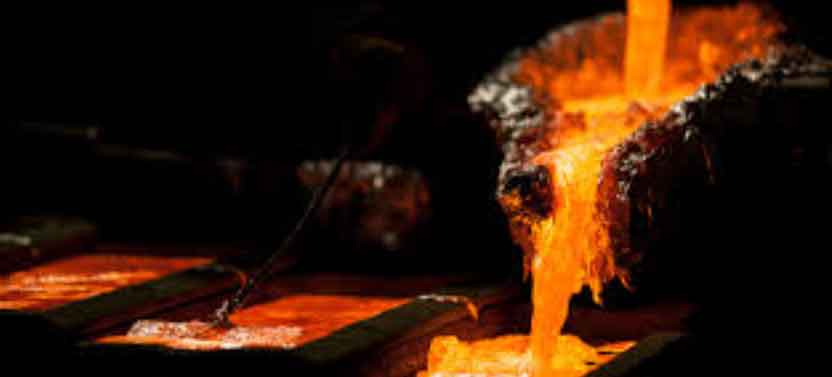
Here is a step-by-step breakdown of the sand casting process:
Pattern Making:
The process begins with the creation of a pattern, which is a replica of the final object. The pattern can be made from wood, plastic, or metal. Skilled craftsmen or pattern makers use their expertise to carve or shape the pattern to the exact specifications of the desired object.
Mold Preparation:
The pattern is then placed in a box or flask, and a mixture of sand and bonding agents, such as clay or resin, is packed around it. The sand should have good flowability and the ability to retain its shape. This mold-making process is known as ramming.
Pattern Removal:
Once the mold is packed, the pattern is carefully removed, leaving behind a cavity in the shape of the desired object. Often, the mold is created in two or more halves to allow for easier pattern removal.
Core Placement (if necessary):
In some cases, the desired object may have internal cavities or complex shapes that cannot be achieved by the mold alone. In such instances, sand cores are created separately and placed within the mold to form the desired internal features.
Melting and Pouring:
The mold is securely closed and prepared for pouring. The chosen metal or alloy is melted in a furnace at high temperatures. Once the metal reaches the desired temperature, it is poured into the mold through a gating system, which consists of channels and gates that help control the flow of metal and minimize turbulence.
Solidification:
The molten metal fills the mold cavity and begins to cool and solidify. The cooling rate and solidification time depend on the size and complexity of the casting, as well as the type of metal used.
Shakeout and Cleaning:
After the metal has solidified and cooled, the mold is broken apart to reveal the casting. This is typically done by mechanical means, such as vibrating or sandblasting. The casting is then carefully removed from the mold and any excess sand or other debris is cleaned off.
Finishing:
The casting may undergo additional processes to remove any remaining gating and riser systems, as well as to achieve the desired surface finish. These processes may include grinding, machining, sanding, or polishing.
Inspection and Quality Control:
The finished casting is inspected for any defects, such as cracks, voids, or dimensional inaccuracies. Various techniques, including visual inspection, non-destructive testing, and measurement tools, may be employed to ensure the casting meets the required specifications.
Post-treatment and Assembly:
Depending on the application and requirements, the casting may undergo additional treatments, such as heat treatment, surface coating, or painting. If the final product requires multiple castings, they may be assembled together through welding, bolting, or other joining methods.
The sand casting process offers several advantages, including its versatility, cost-effectiveness, and suitability for both small and large-scale production. It allows for the creation of complex shapes and is widely used in industries such as automotive, aerospace, and art foundries. While it requires skilled craftsmanship and careful attention to detail, sand casting remains a fundamental method for shaping metal and continues to showcase the artistry and skill of metalworking.