Spheroidal graphite iron is widely used in engine applications due to its excellent mechanical properties, castability, and cost-effectiveness. The thermal conductivity and expansion characteristics of spheroidal graphite iron is critical factors that influence its performance in engine components, such as cylinder blocks, heads, and manifolds. This article explores these thermal properties, their implications for engine applications, and the potential methods to optimize them.
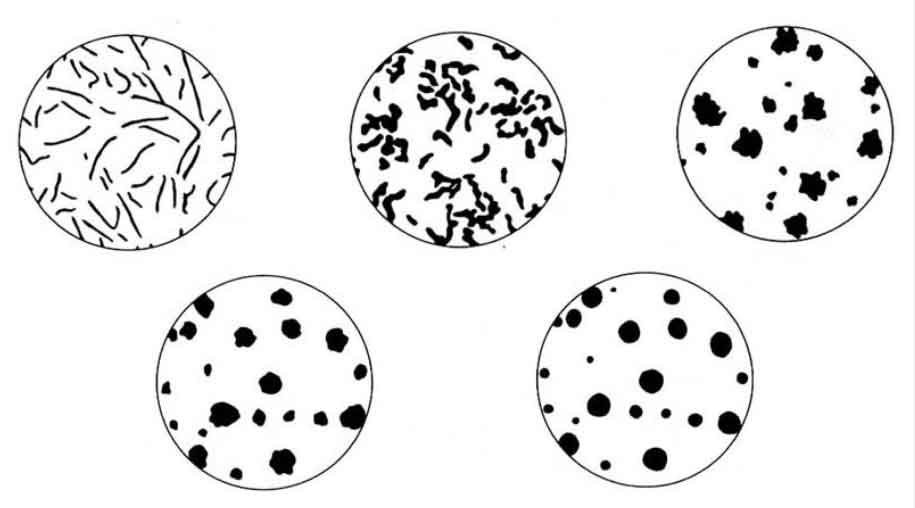
Introduction
The thermal performance of engine components is essential for the overall efficiency, durability, and reliability of an engine. spheroidal graphite iron, with its unique microstructure of spherical graphite nodules, offers a balance of strength, ductility, and thermal properties that make it an ideal material for engine components. Understanding and optimizing the thermal conductivity and expansion characteristics of spheroidal graphite iron can lead to improved engine performance and longevity.
Thermal Conductivity of Spheroidal Graphite Iron
Thermal conductivity is a measure of a material’s ability to conduct heat. For engine applications, high thermal conductivity is desirable to ensure efficient heat dissipation, which helps in maintaining optimal operating temperatures and preventing overheating.
Factors Influencing Thermal Conductivity
The thermal conductivity of spheroidal graphite iron is influenced by its microstructure, composition, and manufacturing processes. Key factors include:
- Graphite nodule size and distribution
- Matrix structure (ferritic, pearlitic, or mixed)
- Presence of alloying elements (e.g., silicon, copper)
Typical Thermal Conductivity Values
Table 1: Thermal Conductivity of Spheroidal Graphite Iron with Different Microstructures
Microstructure | Thermal Conductivity (W/m·K) |
---|---|
Ferritic | 40 – 50 |
Pearlitic | 30 – 40 |
Ferritic-Pearlitic | 35 – 45 |
Ferritic spheroidal graphite iron, with its higher thermal conductivity, is often preferred for components requiring efficient heat dissipation. Pearlitic structures, while offering higher strength, have lower thermal conductivity.
Thermal Expansion Characteristics
Thermal expansion refers to the change in dimensions of a material as it is heated. In engine applications, low and consistent thermal expansion is critical to maintain dimensional stability and avoid issues such as thermal fatigue and warping.
Factors Influencing Thermal Expansion
Similar to thermal conductivity, the thermal expansion of spheroidal graphite iron is affected by its microstructure and alloying elements. The coefficient of thermal expansion (CTE) is a key parameter that quantifies the extent of expansion with temperature changes.
Typical Thermal Expansion Values
Table 2: Coefficient of Thermal Expansion for Spheroidal Graphite Iron with Different Microstructures
Microstructure | CTE (×10^-6 /°C) |
---|---|
Ferritic | 11.5 – 13.0 |
Pearlitic | 12.0 – 14.0 |
Ferritic-Pearlitic | 11.8 – 13.5 |
Ferritic spheroidal graphite iron generally exhibits lower thermal expansion compared to pearlitic structures, making it more suitable for applications requiring tight dimensional control.
Implications for Engine Applications
Cylinder Blocks and Heads
Cylinder blocks and heads are critical engine components that benefit from the high thermal conductivity and stable expansion characteristics of spheroidal graphite iron. Efficient heat dissipation helps in maintaining uniform temperatures, reducing thermal stresses, and preventing engine knock.
Benefits of Spheroidal Graphite Iron for Cylinder Blocks and Heads:
- Improved heat dissipation
- Enhanced dimensional stability
- Reduced risk of thermal fatigue
Exhaust Manifolds
Exhaust manifolds operate under high temperatures and require materials with good thermal conductivity and expansion characteristics to withstand thermal cycling and avoid cracking.
Benefits of Spheroidal Graphite Iron for Exhaust Manifolds:
- High thermal conductivity for efficient heat management
- Consistent thermal expansion to prevent cracking and warping
Turbocharger Housings
Turbocharger housings experience extreme temperatures and rapid temperature fluctuations. spheroidal graphite iron’s ability to maintain structural integrity under these conditions makes it an ideal choice for such applications.
Benefits of Spheroidal Graphite Iron for Turbocharger Housings:
- High thermal stability
- Resistance to thermal fatigue and creep
Optimization Strategies
Alloying Additions
Adding alloying elements such as silicon, copper, and nickel can enhance the thermal properties of spheroidal graphite iron. Silicon improves thermal conductivity, while copper and nickel enhance strength and stability at high temperatures.
Table 3: Effect of Alloying Elements on Thermal Properties
Alloying Element | Typical Addition (%) | Effect on Thermal Properties |
---|---|---|
Silicon | 2.0 – 3.0 | Increases thermal conductivity |
Copper | 0.5 – 1.5 | Enhances high-temperature strength |
Nickel | 0.5 – 2.0 | Improves thermal stability and creep resistance |
Heat Treatment
Heat treatment processes, such as annealing and normalizing, can refine the microstructure of spheroidal graphite iron, improving both thermal conductivity and expansion characteristics.
Benefits of Heat Treatment:
- Refines graphite nodule size and distribution
- Enhances matrix structure for better thermal performance
Casting Techniques
Innovative casting techniques, such as vacuum casting and lost foam casting, can produce spheroidal graphite iron components with optimized microstructures, reducing defects and enhancing thermal properties.
Benefits of Advanced Casting Techniques:
- Reduces porosity and defects
- Produces components with uniform properties
Conclusion
Understanding and optimizing the thermal conductivity and expansion characteristics of spheroidal graphite iron are crucial for enhancing the performance of engine components. Through strategic alloying, heat treatment, and advanced casting techniques, the thermal properties of spheroidal graphite iron can be tailored to meet the demanding requirements of modern engine applications. These innovations ensure that spheroidal graphite iron remains a preferred material in the automotive industry, offering a combination of strength, durability, and thermal efficiency.