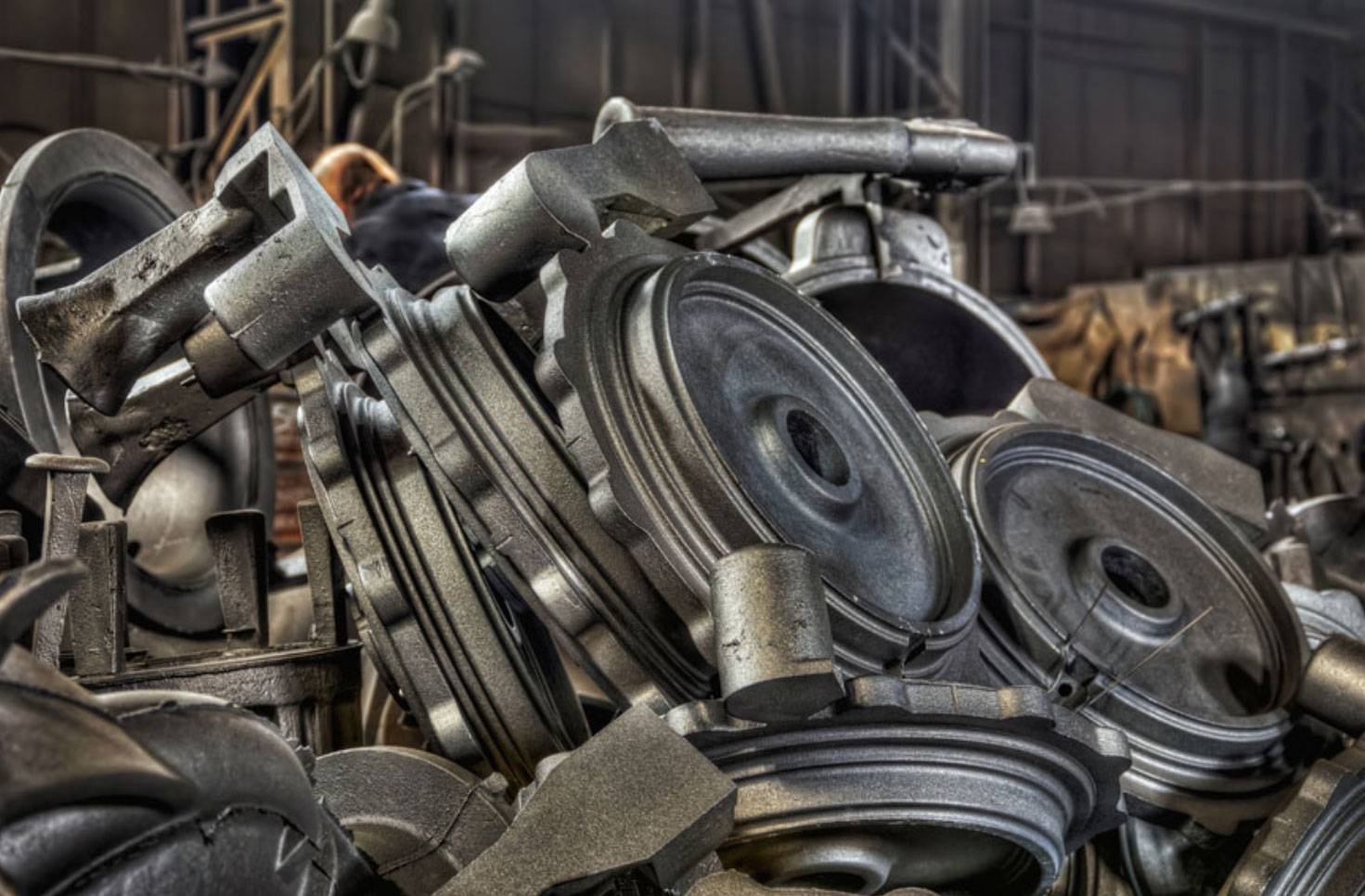
Understanding the ductile iron casting process involves tracing the journey from raw materials to finished products. This process encompasses several stages, each critical to the properties and quality of the final product. Here’s a step-by-step overview:
1. Raw Material Selection
- Iron: The primary ingredient is iron, often recycled from scrap metal.
- Alloying Elements: Elements like carbon, silicon, magnesium, and sometimes copper, tin, or phosphorus are added to achieve specific properties.
- Inoculants: Substances like ferrosilicon are prepared to refine the final microstructure of the iron.
2. Melting
- The raw materials are melted in a furnace, such as a cupola or electric induction furnace.
- Precise temperature control is crucial to achieve the desired chemical composition.
3. Nodulization
- During or after melting, a nodulizing agent, typically magnesium or cerium, is added.
- This step is critical for transforming the graphite within the iron from a flake to a spheroidal or nodular shape, enhancing ductility.
4. Inoculation
- The molten iron is treated with inoculants to further refine the microstructure.
- This stage controls the formation of graphite and improves mechanical properties like strength and wear resistance.
5. Molding
- The molten iron is poured into molds, which can be made of sand or other materials.
- Molds are often designed using CAD software for precision and can be used repeatedly.
6. Cooling and Solidification
- After pouring, the iron cools and solidifies in the mold.
- The cooling rate can be controlled to affect the microstructure and properties of the iron.
7. Removal and Cleaning
- Once solidified, the casting is removed from the mold.
- Excess material, such as gates and risers used in casting, is removed.
8. Heat Treatment (Optional)
- Some ductile iron products undergo heat treatments like annealing, normalizing, or tempering.
- These processes adjust the mechanical properties, such as hardness and strength.
9. Finishing and Inspection
- Castings are finished through processes like grinding, machining, and painting.
- Quality control measures, including X-ray, ultrasonic, or magnetic particle inspection, ensure the casting meets specifications.
10. Final Inspection and Shipping
- Final inspection ensures the product meets all quality and dimensional requirements.
- Once approved, the product is shipped to the customer.
Applications
Ductile iron castings are used in various industries due to their excellent strength, ductility, and versatility. Common applications include:
- Automotive parts (like engine blocks and brake components)
- Infrastructure (pipes and fittings for water, gas, and sewage systems)
- Machinery and heavy equipment (gears, bearings, and hydraulic components)
- Construction (reinforcements, brackets, and structural beams)
Key Advantages
- Versatility: Ability to be cast into complex shapes with varied properties.
- Strength and Ductility: Offers the strength of steel with superior ductility.
- Cost-Effectiveness: Generally more economical than steel in production and machining.
- Wear Resistance: Ideal for parts subjected to stress and wear.
Challenges
- Quality Control: Ensuring consistent quality in large-scale production can be challenging.
- Environmental Impact: Managing emissions and waste from the foundry is a significant concern.
Through this detailed process, ductile iron casting provides a reliable and efficient way to produce a wide range of high-quality, durable components used across many sectors of industry.