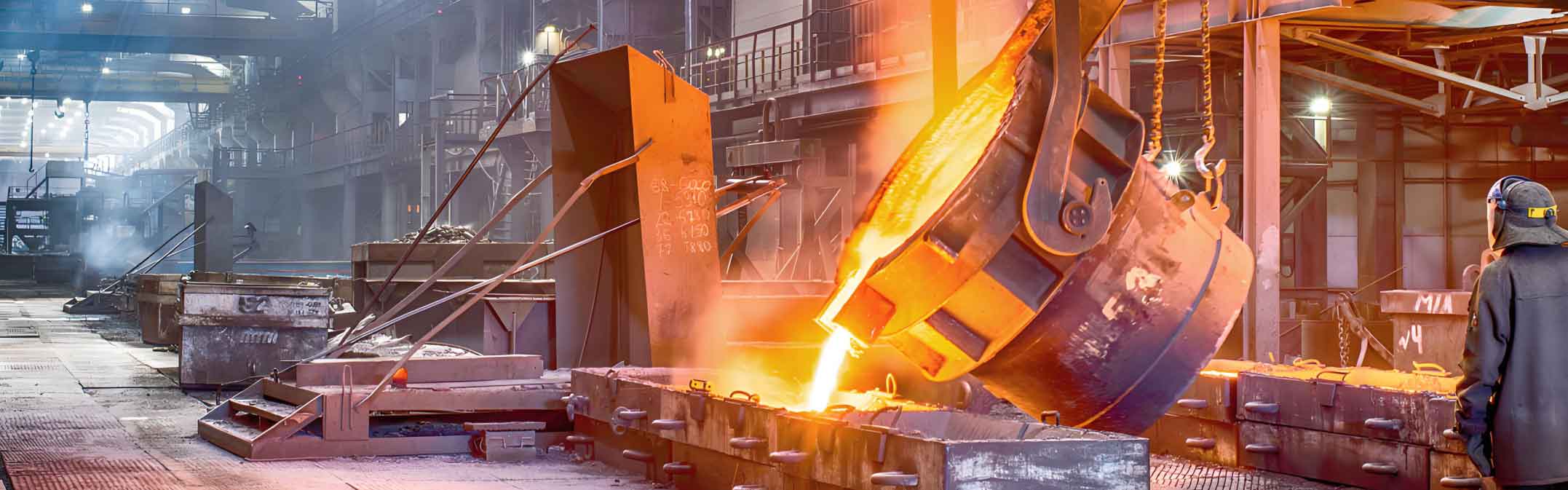
Introduction
Electric vehicles (EVs) represent the future of the automotive industry, with a focus on sustainability, efficiency, and innovation. One of the key challenges in electric vehicles manufacturing is the production of lightweight and high-strength components that enhance vehicle performance and efficiency. Lost foam casting is an advanced casting technique that offers significant advantages for producing complex and precise metal components used in electric vehicles. This article explores the material selection and process parameters critical to optimizing lost foam casting for electric vehicle components.
Importance of Material Selection in Lost Foam Casting
Selecting the appropriate material for lost foam casting is crucial to achieving the desired mechanical properties, durability, and performance of electric vehicle components. The material must withstand the operational demands of electric vehicles while contributing to weight reduction and efficiency improvements.
Table 1: Common Materials Used in Lost Foam Casting for Electric Vehicles Components
Material | Properties | Typical Applications |
---|---|---|
Aluminum Alloys | Lightweight, high strength-to-weight ratio | Battery housings, motor casings, structural parts |
Magnesium Alloys | Very lightweight, good strength | Transmission cases, support brackets |
Cast Iron | Excellent wear resistance, good damping properties | Brake components, suspension parts |
Stainless Steel | Corrosion resistance, high strength | Fasteners, fittings, high-stress components |
List 1: Factors Influencing Material Selection
- Mechanical Properties: The material must possess the necessary strength, toughness, and fatigue resistance for its intended application.
- Weight Considerations: Lightweight materials contribute to the overall efficiency and performance of electric vehicles.
- Corrosion Resistance: Materials with high corrosion resistance are essential for components exposed to harsh environments.
- Thermal Properties: The material’s ability to withstand temperature variations and thermal cycling is important for components in thermal management systems.
- Cost and Availability: Economic factors and material availability play a significant role in the selection process.
Key Process Parameters in Lost Foam Casting
Optimizing process parameters is essential to ensuring high-quality cast components and maximizing the benefits of lost foam casting. The following parameters are critical to the success of the lost foam casting process:
Table 2: Essential Process Parameters in Lost Foam Casting
Parameter | Description |
---|---|
Pattern Density | The density of the foam pattern affects the casting quality and dimensional accuracy. |
Coating Thickness | Uniform coating thickness ensures consistent mold surfaces and reduces surface defects. |
Sand Compaction | Proper sand compaction stabilizes the pattern and prevents mold collapse during metal pouring. |
Metal Pouring Temperature | The pouring temperature influences metal flow and filling of the mold cavity. |
Cooling Rate | Controlled cooling rates prevent casting defects such as shrinkage and cracking. |
List 2: Best Practices for Optimizing Process Parameters
- Pattern Density Control: Use high-quality foam patterns with consistent density to achieve precise and accurate cast parts.
- Coating Application Techniques: Apply the refractory coating evenly and allow sufficient drying time to prevent defects and ensure a smooth mold surface.
- Sand Quality and Compaction: Use high-quality, unbonded sand and ensure proper compaction to provide stability and support for the foam pattern during casting.
- Metal Pouring Temperature Management: Maintain the appropriate pouring temperature for the specific metal alloy to ensure optimal flow and fill of the mold cavity.
- Controlled Cooling: Implement controlled cooling techniques to avoid rapid temperature changes that could cause defects such as shrinkage or cracking in the cast components.
Applications of Lost Foam Casting in Electric Vehicle Components
Lost foam casting is particularly well-suited for producing a wide range of electric vehicle components due to its ability to create complex geometries and achieve high dimensional accuracy. Some notable applications include:
Table 3: Electric Vehicle Components Produced Using Lost Foam Casting
Component | Benefits of Lost Foam Casting |
---|---|
Battery Housings | Lightweight construction, complex internal geometries, improved thermal management |
Motor Casings | High strength-to-weight ratio, precise dimensions, reduced machining requirements |
Suspension Parts | Excellent wear resistance, superior surface finish, enhanced durability |
Transmission Cases | Lightweight, good strength, complex geometries with integrated cooling channels |
Case Study: Battery Housing for Electric Vehicles
Battery housings are critical components in electric vehicles, providing structural support and protection for the battery pack. Lost foam casting enables the production of lightweight and complex battery housings with integrated cooling channels and mounting points. The use of aluminum alloys in lost foam casting ensures a high strength-to-weight ratio, contributing to overall vehicle efficiency.
Case Study: Motor Casing Production
Motor casings in electric vehicles require high precision and durability to support the electric motor and associated components. Lost foam casting allows for the creation of motor casings with intricate cooling channels and mounting features, reducing the need for additional machining. The use of magnesium alloys in lost foam casting results in extremely lightweight and strong motor casings, further enhancing vehicle performance.
Conclusion
Lost foam casting is a highly effective technique for producing complex and precise components for electric vehicles. By carefully selecting appropriate materials and optimizing process parameters, manufacturers can achieve significant improvements in production efficiency, component quality, and overall vehicle performance. The ability to create lightweight, durable, and intricate components makes lost foam casting an invaluable process in the rapidly evolving electric vehicle industry.
Table 4: Summary of Benefits and Applications
Benefit | Description | Typical Applications |
---|---|---|
Complex Geometries | Enables the creation of intricate and detailed cast parts | Battery housings, motor casings, suspension parts |
Reduced Machining | Minimizes the need for extensive post-casting machining | Transmission cases, structural parts |
Material Savings | Eliminates waste material associated with traditional casting methods | Various electric vehicles components |
Improved Surface Finish | Provides superior surface finish, reducing the need for additional finishing processes | High-stress components |
Dimensional Accuracy | Ensures high precision and tight tolerances in cast components | Motor casings, battery housings |
By leveraging the advantages of lost foam casting, the electric vehicle industry can continue to innovate and produce high-performance, efficient, and sustainable vehicles for the future.