Japan has used this method to produce large castings since the 1960s, such as Kobe iron Institute, which is still used to produce large machine tool castings. There are large-scale plastic mold processing workshops and special program-controlled universal processing equipment. The application of lost foam casting in mass production of castings in Japan started late in 1984 and developed rapidly. Nearly 100 universities, research institutes and companies participated in this technological development and research work. The Kansai branch and the profile center under the Japan Casting Association have special committees to carry out technical development from all aspects, including basic research, practical application and new technology development. At present, they have developed “reduced pressure vibration lost foam casting process” and “in mold treatment process”.
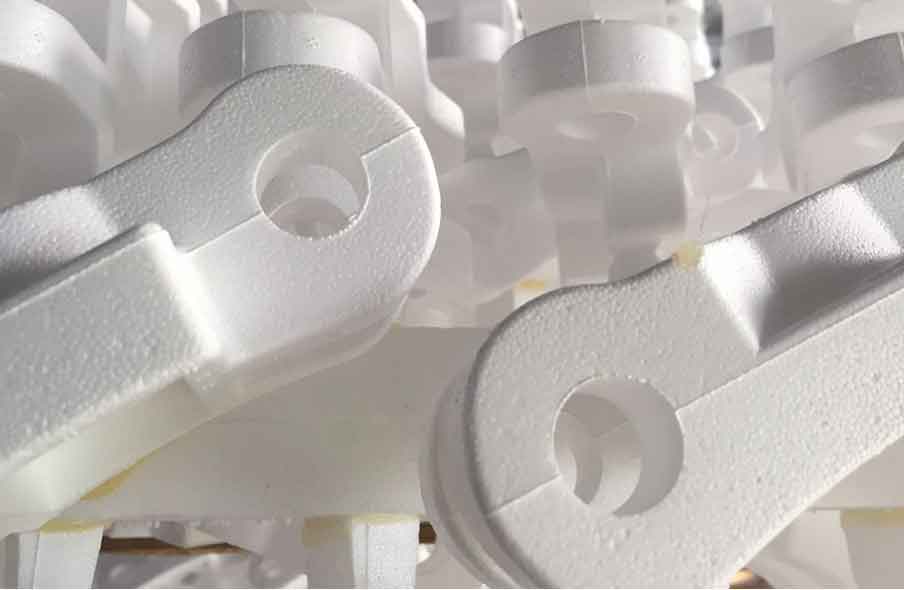
The lost foam casting special committee under the Kansai branch is a cross industry casting, chemical and mechanical research organization, which is a combination of enterprises and academia. This organization is one of the most active organizations in the world casting industry to study lost foam casting. In 1989, the output of castings produced by lost foam casting in Japan has leapt to the forefront of the world. For example, Morikawa company produced 800 tons of castings per month, which is the largest company in the world to produce castings by lost foam casting. The company began to produce Honda Engine Castings, bearing covers, alum pig iron, cylinder liners, high-strength cast iron differential boxes and engine exhaust pipes in, which are characterized by the use of hot-dip casting risers, computer-controlled casting temperature and the use of waste heat for casting heat treatment.
Japan’s casting production mainly depends on small factories. The dry sand lost foam casting process is very beneficial to improve product quality, reduce casting costs and realize the mechanization of casting production. In addition, Japan pays attention to the development of lost foam casting supporting technology, which can ensure the quality and supply of coatings, model adhesives, foam beads, molding equipment, etc, Therefore, dry sand lost foam casting has been widely used in small foundries in Japan.
Japan has learned from the experience and lessons of GM company in the United States from complex cylinder block castings and the successful experience of Ford company in the application of intake and exhaust manifolds, starting with a large number of pipe fittings that can greatly reduce costs. After success, it will gradually be extended to valves, pumps, boxes, hydraulic pressure parts, special-shaped pipe fittings, intake and exhaust pipe bodies, bodies, impellers, bearing supports and other products, Gray iron and nodular cast iron are the main materials of castings produced by lost foam casting, among which nodular cast iron special-shaped pipe fittings have the largest output.