The main bearing cap of an engine has 5 pieces of integrated sand casting blanks (as shown in Figure 1), with an overall dimension of 148 mm × 114 mm × 68 mm, sand casting mass is 5.4 kg, average wall thickness is 30 mm, and material is QT500-7 ductile iron. The three-dimensional modeling of sand casting designed according to the blank part drawing is shown in Figure 2. The conjoined sand casting is processed into five single engine main bearing caps. X-ray flaw detection is required for sand castings, no shrinkage defects are allowed on the machined surface, and the internal shrinkage grade of the non machined surface meets ASTM E446 Grade 2. The chemical composition requirements of sand castings are shown in the table. Mechanical property requirements of materials: tensile strength ≥ 450 MPa, yield strength ≥ 310 MPa, elongation ≥ 10%, Brinell hardness 160 ~ 221 HB.
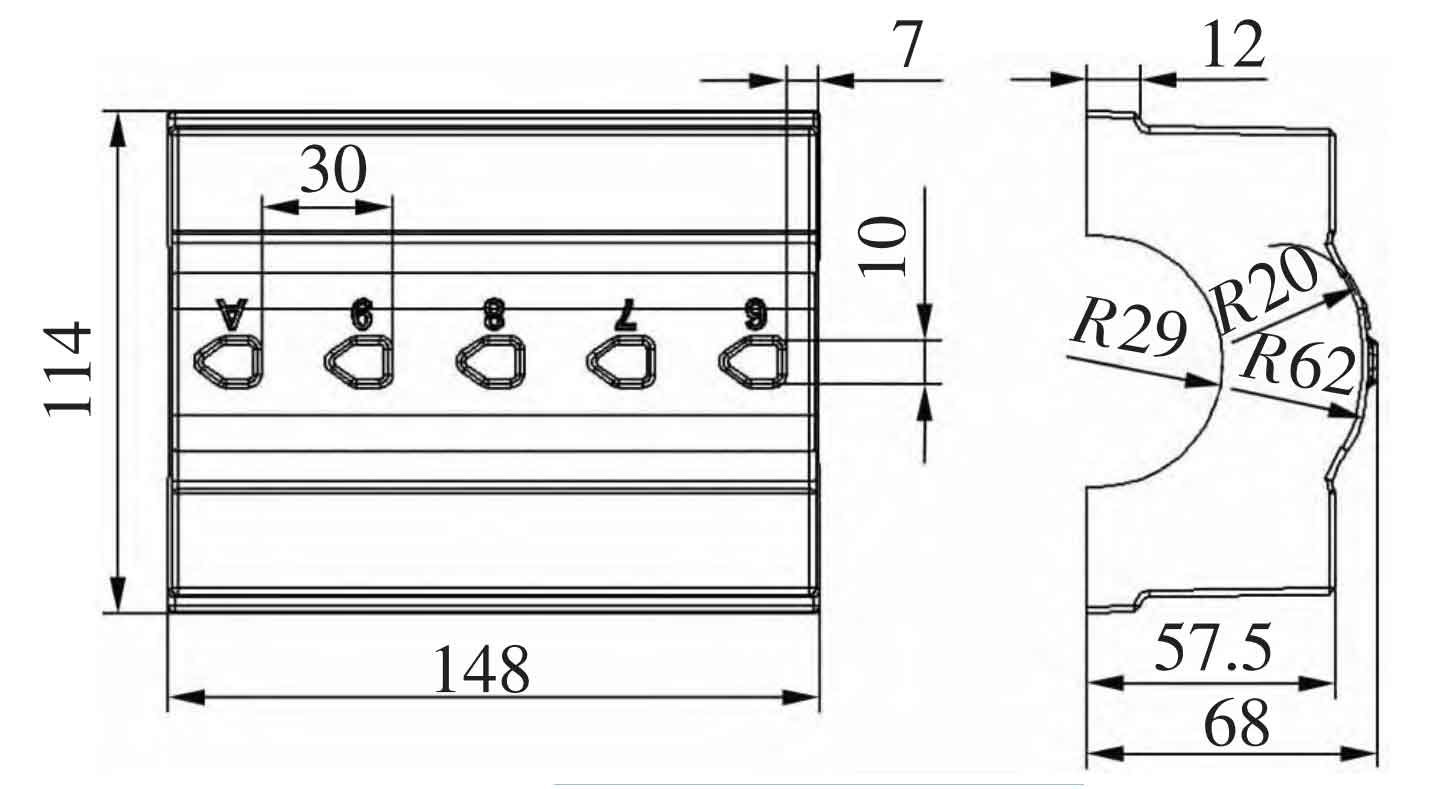
C | Si | Mn | P | S | Sn | Cu | Cr | Mg |
3.000-4.000 | 1.800-3.000 | 0.200-0.800 | ≤0.100 | ≤0.020 | ≤0.015 | ≤0.300 | ≤0.100 | 0.025-0.050 |
According to the actual molding line of the enterprise, the gating system adopts the horizontal molding line scheme of “the first mock examination and four pieces”. The gating system is designed as shown in Figure 3. The molten iron flows through the riser into the sand casting, and the riser neck acts as an internal runner. The gating system adopts a front closed and back open design, with F internal>F resistance<F horizontal<F straight, and the blocking position is located between the runner and the riser, blocking the flow in the form of a blocking sheet.
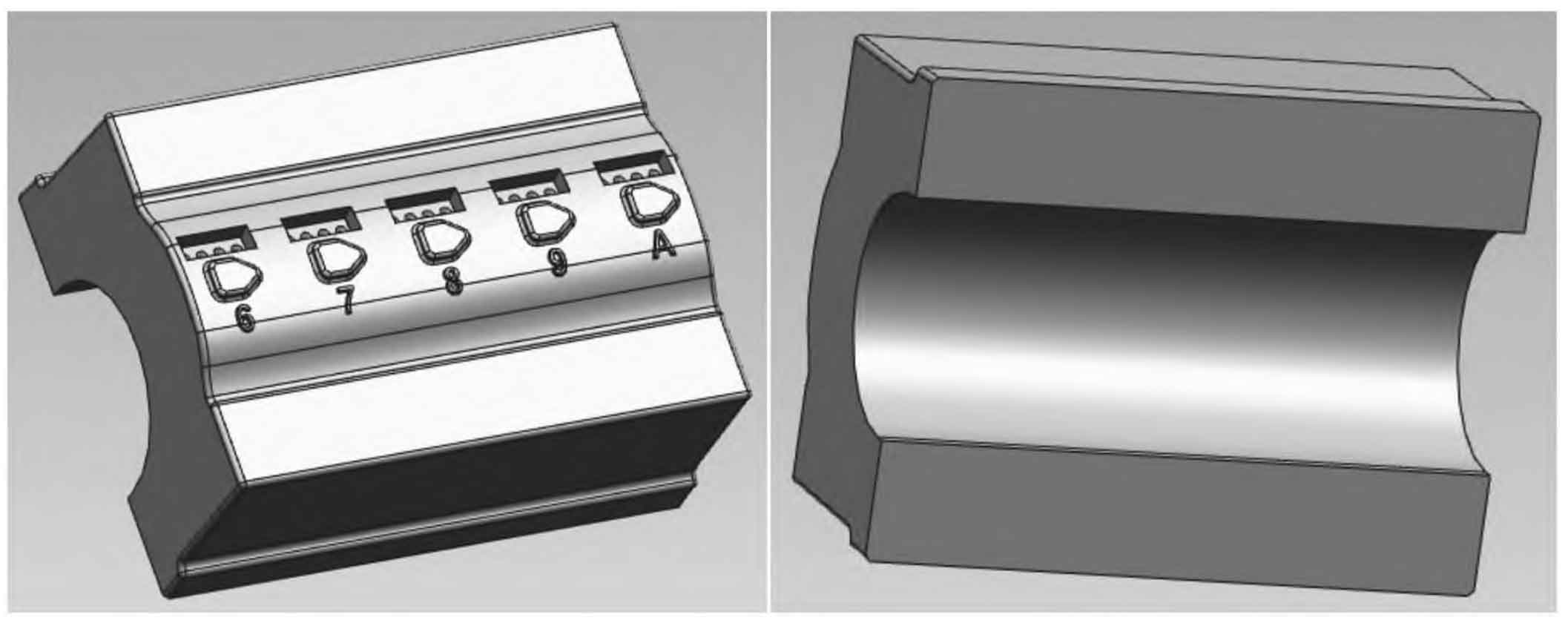
The riser is designed using the modulus method. A cylindrical riser with a diameter of 70 mm and a height of 140 mm is selected. The modulus is 1.31, and the draft angle is 5 °. One riser needs to feed two sand castings at the same time. The empirical formula calculates the total current resistance area F resistance=720 mm2, each current resistance section area is 360 mm2, and the design is 6 mm × 60 mm choke sheet. F resistance: F transverse: F straight=1 ∶ 1.15 ∶ 1.2.
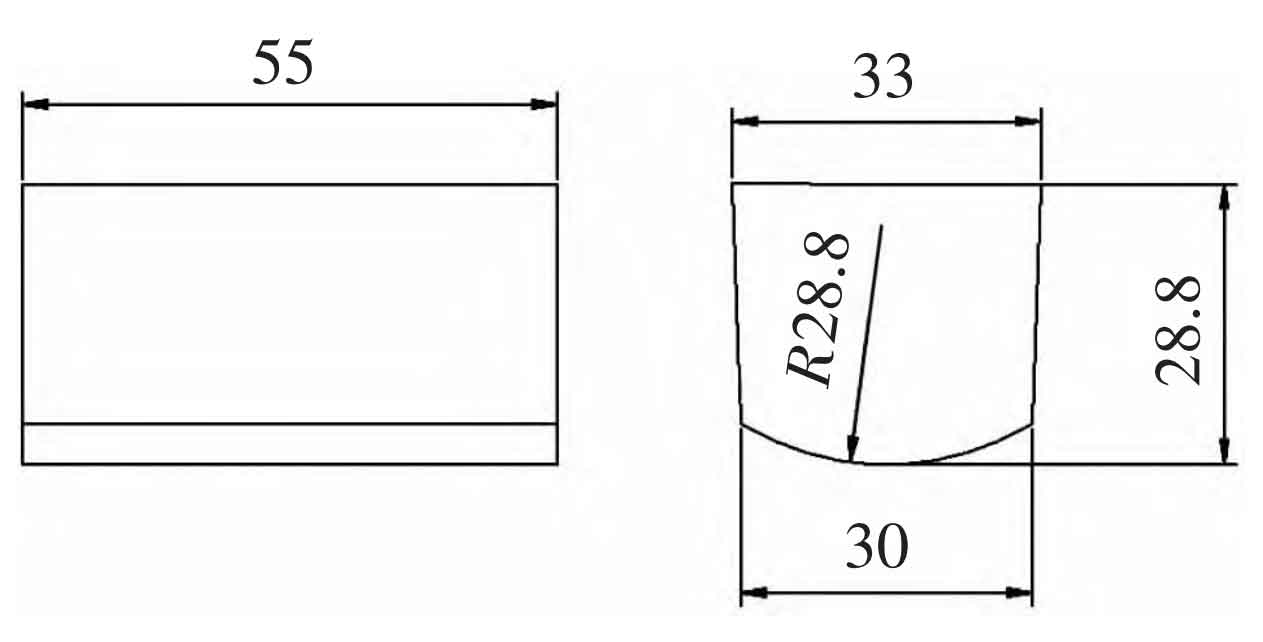
It is found in the actual production that the stability of shrinkage porosity of the safety parts in the automotive parts of nodular cast iron is poor due to the influence of the fluctuation of the actual production process and the application of the proportional solidification theory. Automotive safety parts require stable product zero shrinkage, and unqualified parts will directly lead to recall, so this process optimization still takes realizing sequential solidification as the main design optimization idea. The method to achieve sequential solidification is to match the riser with cold iron. The size of cold iron is shown in Figure 4, and the positions are shown at 1, 2, 3, and 4 in Figure 4.
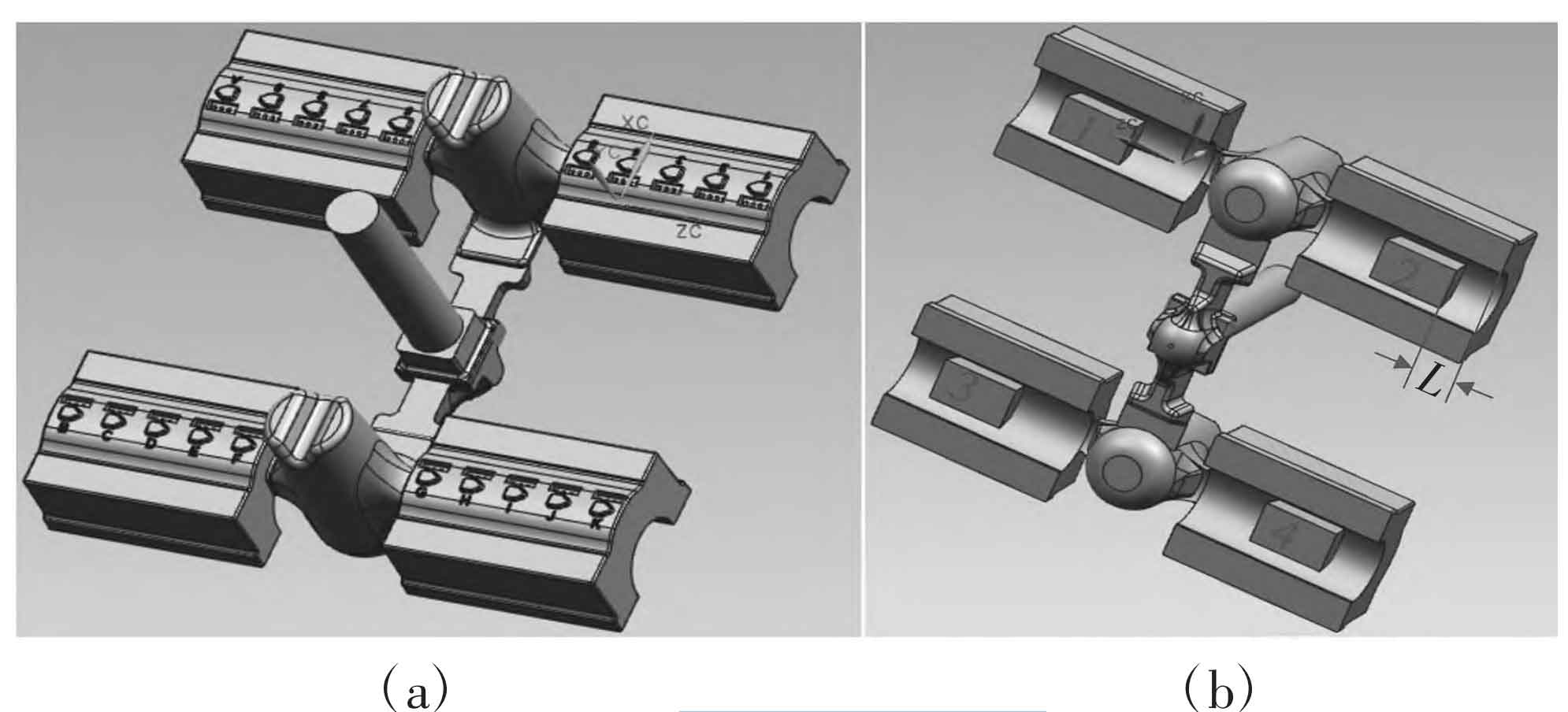
The specific position of the chill is indicated by the offset L between the chill end face and the sand casting end face, as shown in Fig. 4 (b). The main factors affecting the quality of sand castings are the cold iron position offset L, pouring temperature and pouring height. Therefore, orthogonal tests are designed to find the optimal process parameters.