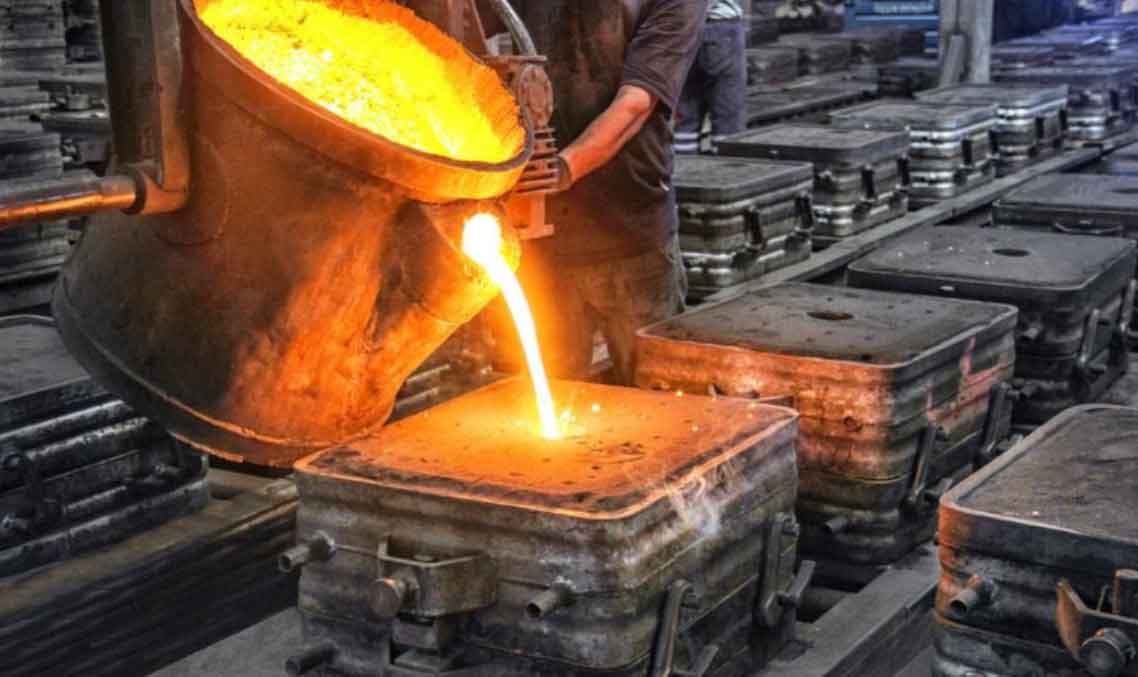
Sand casting is a complex process that involves transforming molten metal into solid objects using molds made from sand. Skilled sand casting manufacturers follow a series of intricate steps to ensure the success of the casting process. Here is a detailed overview of the sand casting process:
- Pattern Making: The process begins with the creation of a pattern, which is a replica of the final product. The pattern can be made from various materials, including wood, plastic, or metal. The pattern accounts for the desired shape, dimensions, and surface finish of the cast part.
- Mold Preparation: A two-part mold is made using the pattern. The mold consists of a cope (upper half) and a drag (lower half). The cope and drag are placed together to create a cavity representing the final shape of the object to be cast.
- Mold Assembly: Before the mold is closed, cores are inserted to create internal features such as cavities and holes in the casting. Cores are made from sand and other materials held together by a binder.
- Sand Molding: The sand used in sand casting is typically a mixture of silica sand and a binder, which holds the sand grains together to form a cohesive mold. The sand mixture is packed around the pattern and the cores, creating the mold cavity.
- Pattern Removal: Once the sand has been properly packed, the pattern is carefully removed, leaving a negative impression of the object in the sand.
- Melting and Pouring: The chosen metal or alloy is melted in a furnace, heated to the appropriate temperature for pouring. The molten metal is then poured into the mold through a gating system, which helps control the flow and prevent defects.
- Solidification: The molten metal cools and solidifies inside the mold cavity, taking the shape of the pattern and cores. The cooling rate and solidification time depend on the metal’s properties and the design of the casting.
- Mold Breakout: After the metal has solidified, the mold is opened, and the casting is removed. Sometimes, minor finishing processes are performed on the casting while it is still in the mold.
- Finishing: Once the casting is removed, any excess material (known as the gating system) is removed from the casting. The casting may undergo various finishing operations, such as grinding, machining, and surface treatment, to achieve the desired final specifications and appearance.
- Quality Control: The final casting is thoroughly inspected for defects and dimensional accuracy. Non-destructive testing techniques, such as X-ray and ultrasonic inspection, may be used to identify any internal defects.
Sand casting is a versatile and widely used process in various industries due to its cost-effectiveness and ability to produce intricate and large-sized parts. Expert sand casting manufacturers employ their skills and knowledge to ensure that each step is executed with precision, resulting in high-quality castings that meet the required specifications.