
Chapter 1: Understanding the Ductile Iron Casting Process
Ductile iron casting process is a versatile manufacturing process used to create a wide range of metal parts with excellent strength and durability. The process involves several key steps:
- Pattern Making: The first step is creating a pattern, which is a replica of the final product but slightly larger to compensate for shrinkage during cooling. Patterns can be made from various materials, including wood, plastic, or metal.
- Mold Making: The pattern is used to create a mold. The most common method for ductile iron casting process is sand casting, where the pattern is placed in a box and packed with a mixture of sand and a binding agent. The pattern is removed, leaving a cavity in the shape of the part.
- Melting and Pouring: Ductile iron casting process is created by adding magnesium or cerium to molten iron, which is typically derived from pig iron. This addition causes the carbon within the iron to form spherical, graphite nodules, which give ductile iron its flexibility and strength. The molten ductile iron casting process is then poured into the mold.
- Cooling and Solidification: After pouring, the metal is allowed to cool and solidify. During this phase, the nodules of graphite form, giving ductile iron casting process its unique properties.
- Shakeout: Once the metal has cooled and solidified, the sand mold is broken away from the casting in a process known as shakeout.
- Cleaning and Finishing: The cast part may have some excess material (like gates, risers, and flash) that needs to be removed. This can be done through various processes like grinding, sandblasting, or cutting.
- Heat Treatment (if necessary): Depending on the application, the ductile iron casting process may undergo heat treatment to achieve desired mechanical properties, such as improved strength or ductility.
- Inspection and Quality Control: The final step involves inspecting the cast parts for defects and ensuring they meet the required specifications and quality standards.
Ductile iron casting process is popular due to its excellent strength-to-weight ratio, good machinability, and resistance to wear and deformation. It’s used in applications ranging from automotive components and machinery parts to piping and infrastructure projects.
Chapter 2: The Comprehensive Guide to Ductile Iron Casting Process
Ductile Iron Casting Process is a fascinating and complex process that involves several key steps and considerations. Here’s a comprehensive guide to understand how ductile iron is cast:
- Understanding Ductile Iron: Ductile iron, also known as nodular or spheroidal graphite iron, is a type of cast iron known for its improved ductility compared to traditional cast iron. This is achieved by adding nodulizing elements like magnesium or cerium to the iron, which form graphite in spherical shapes within the iron matrix, as opposed to the flaky graphite in gray cast iron.
- Material Preparation: The process begins with preparing the base iron. High-quality pig iron, steel scrap, and other alloys are melted in a furnace to achieve the desired chemical composition. The exact composition depends on the properties required in the final product.
- Nodulization: Once the iron reaches its molten state, it undergoes nodulization. This involves adding elements like magnesium or cerium, which react with the iron to change the shape of the graphite from flakes to spheres.
- Inoculation: After nodulization, the molten iron is inoculated with materials such as ferrosilicon. This step refines the graphite and iron structure, improving the mechanical properties and making the iron more ductile.
- Mold Making: Concurrently, molds are prepared for casting. These molds are typically made from sand mixed with a binding agent. The design of the mold is crucial and must account for the shrinkage of iron during cooling.
- Pouring the Iron: The molten ductile iron is then carefully poured into the molds. The pouring temperature and rate are critical factors in ensuring quality casting.
- Cooling and Solidification: After pouring, the iron begins to cool and solidify in the mold. The cooling rate can affect the properties of the cast iron, and in some cases, sections of the casting are cooled more rapidly to achieve desired characteristics.
- Shakeout: Once the iron has solidified, the casting is removed from the mold in a process called shakeout. The sand mold is broken away, and the casting is revealed.
- Cleaning and Finishing: The castings are then cleaned to remove any sand, scale, or excess material. They may also undergo various finishing processes such as grinding, machining, or heat treatment to achieve the required dimensions and properties.
- Quality Control: Finally, strict quality control measures are employed throughout the casting process. This includes inspecting the chemical composition, microstructure, and mechanical properties to ensure they meet the required standards.
- Applications and Advantages: Ductile iron casting process used in a wide range of applications due to their excellent strength, ductility, and cost-effectiveness. They are commonly found in automotive components, pipe fittings, gears, and machinery parts.
Understanding these steps and their nuances is crucial for anyone involved in ductile iron casting process, whether in a professional capacity or as a part of academic research. The process balances art and science, requiring precise control over numerous variables to produce high-quality, durable castings.
Chapter 3: Navigating the Complexities of the Ductile Iron Casting Process

Navigating the complexities of the ductile iron casting process involves understanding various stages and techniques. Ductile iron, also known as nodular iron or spheroidal graphite iron, is characterized by its high strength and ductility, which is achieved through a specific manufacturing process. Here’s a breakdown of the key steps and considerations:
- Material Preparation: The first step involves preparing the iron and the alloying elements. The primary materials used in ductile iron include iron, carbon (usually added in the form of coke), and various other elements like silicon, manganese, phosphorus, and sulfur. Additionally, small amounts of magnesium or cerium are added to create the spheroidal graphite structures that give ductile iron its name and unique properties.
- Melting and Casting: The materials are melted in a furnace. The melting process must be carefully controlled to achieve the desired chemical composition and temperature. Once melted, the iron is poured into molds. These molds are often made of sand and are designed to shape the iron into the desired form.
- Nodulizing Process: This is a crucial step in producing ductile iron. The molten iron is treated with a nodulizing agent (like magnesium or cerium) to encourage the formation of graphite in a spherical shape, which is responsible for the enhanced ductility and strength of the iron.
- Inoculation: This process involves adding materials to the molten iron to refine the microstructure and improve the mechanical properties of the ductile iron. Inoculants can include elements like silicon, aluminum, or calcium.
- Cooling and Solidification: After casting, the ductile iron needs to be cooled and solidified. The rate of cooling can affect the microstructure and, consequently, the mechanical properties of the iron.
- Heat Treatment: Depending on the required properties of the final product, ductile iron casting process may undergo various heat treatments like annealing, normalizing, or quenching and tempering. These treatments can enhance the ductile iron’s mechanical properties, such as strength, ductility, and wear resistance.
- Finishing and Quality Control: After cooling, ductile iron casting process removed from the molds and undergo finishing processes like grinding, sanding, and cleaning. Quality control is critical at this stage to ensure the final product meets the required specifications.
- Testing and Inspection: The final products are subjected to various tests, such as tensile strength, hardness, and elongation tests, to ensure they meet the necessary standards and performance criteria.
Each stage of the ductile iron casting process requires precise control and expertise to ensure the final product has the desired properties and quality. Advances in technology, such as computer-aided design and simulation, have improved the efficiency and accuracy of this process.
Chapter 4: The Journey of Ductile Iron Casting Process
The journey of ductile iron casting process from the foundry to fabrication is a fascinating process that combines ancient metallurgical techniques with modern technology. Here’s an overview of the key stages in this journey:
- Raw Material Selection and Preparation: Ductile iron casting process begins with the selection of raw materials, primarily iron, along with carbon, silicon, manganese, phosphorus, and sulfur. Scrap iron or pig iron is often used. These materials are carefully selected and prepared to ensure the right chemical composition for ductile iron.
- Melting: The raw materials are melted in a furnace. There are different types of furnaces used, such as cupola, electric arc, or induction furnaces. The choice depends on factors like the scale of production, desired properties, and cost considerations.
- Nodulization: Ductile iron, also known as nodular or spheroidal graphite iron, gets its properties from the spherical shape of its graphite inclusions. To achieve this, a nodulizing agent (commonly magnesium) is added to the molten iron. This process is crucial as it imparts ductility and toughness to the iron.
- Inoculation: This stage involves adding materials to the molten iron to refine its microstructure and enhance its properties. Elements like silicon, aluminum, or calcium can be added to modify the solidification process and improve characteristics like strength and machinability.
- Casting: The molten iron is then poured into molds made of sand or other materials. The design of the mold is critical and is often based on the final product’s specifications. As the iron cools and solidifies in the mold, it takes the shape of the desired part.
- Cooling and Removal: After ductile iron casting process, the parts are allowed to cool. The rate of cooling can affect the properties of the ductile iron, so this process is carefully controlled. Once cooled, the castings are removed from the molds.
- Cleaning and Finishing: The castings usually have some excess material, like gates and risers, used in ductile iron casting process. These are removed, and the castings are cleaned through processes like grinding or shot blasting.
- Heat Treatment (if needed): Depending on the application, the ductile iron casting process may undergo heat treatment processes like annealing, normalizing, or quenching and tempering to achieve the desired mechanical properties.
- Quality Control and Inspection: Quality control is integral at various stages of ductile iron casting process. The final product is inspected for defects, dimensional accuracy, and material properties to ensure it meets the required standards.
- Fabrication and Finishing: Finally, ductile iron casting process might undergo further fabrication processes like machining, painting, or coating, preparing them for their end use in various industries such as automotive, infrastructure, machinery, and more.
This process illustrates the complexity and precision involved in creating high-quality ductile iron casting process, which are integral to many of the tools and machines used in everyday life.
Chapter 5: Unlocking the Potential of Ductile Iron Casting Process Through Advanced
Ductile iron casting process, also known as spheroidal or nodular iron, is a type of cast iron known for its high strength, impact resistance, and elongation. This material is widely used in engineering applications due to its excellent mechanical properties and machinability.
To unlock the potential of the ductile iron casting process, several advanced techniques and considerations can be employed:
- Alloying and Material Composition: Adjusting the composition of ductile iron casting process, such as varying the levels of carbon, silicon, manganese, phosphorus, and sulfur, as well as adding alloying elements like nickel, copper, and molybdenum, can significantly affect its mechanical properties.
- Mold Design and Quality: Advanced mold design, including the use of high-quality sand and binders, can improve the surface finish and dimensional accuracy of the castings.
- Melting and Pouring Techniques: Employing sophisticated melting furnaces and controlled pouring techniques can enhance the uniformity and quality of the metal.
- Heat Treatment: Post-casting heat treatments, such as annealing, normalizing, and quenching and tempering, can be used to alter the microstructure of ductile iron casting process, enhancing its mechanical properties.
- Inoculation and Nodulization: Precise control over the inoculation and nodulization process, which involves adding elements like magnesium or cerium to promote the formation of spherical graphite structures, is critical for achieving desired mechanical properties.
- Quality Control and Testing: Implementing rigorous quality control measures and conducting thorough material testing, including tensile strength, hardness, and impact tests, ensures the reliability and performance of the final product.
- Process Automation and Control: Advanced automation and process control can enhance precision, repeatability, and efficiency in casting.
- Environmental and Safety Measures: Adopting eco-friendly practices and ensuring safety protocols are in place to handle high temperatures and molten metal is essential.
By focusing on these aspects, the ductile iron casting process can be optimized for various applications, including automotive components, heavy machinery parts, pipe fittings, and more.
Chapter 6: Balancing Efficiency and Quality in the Ductile Iron Casting Process
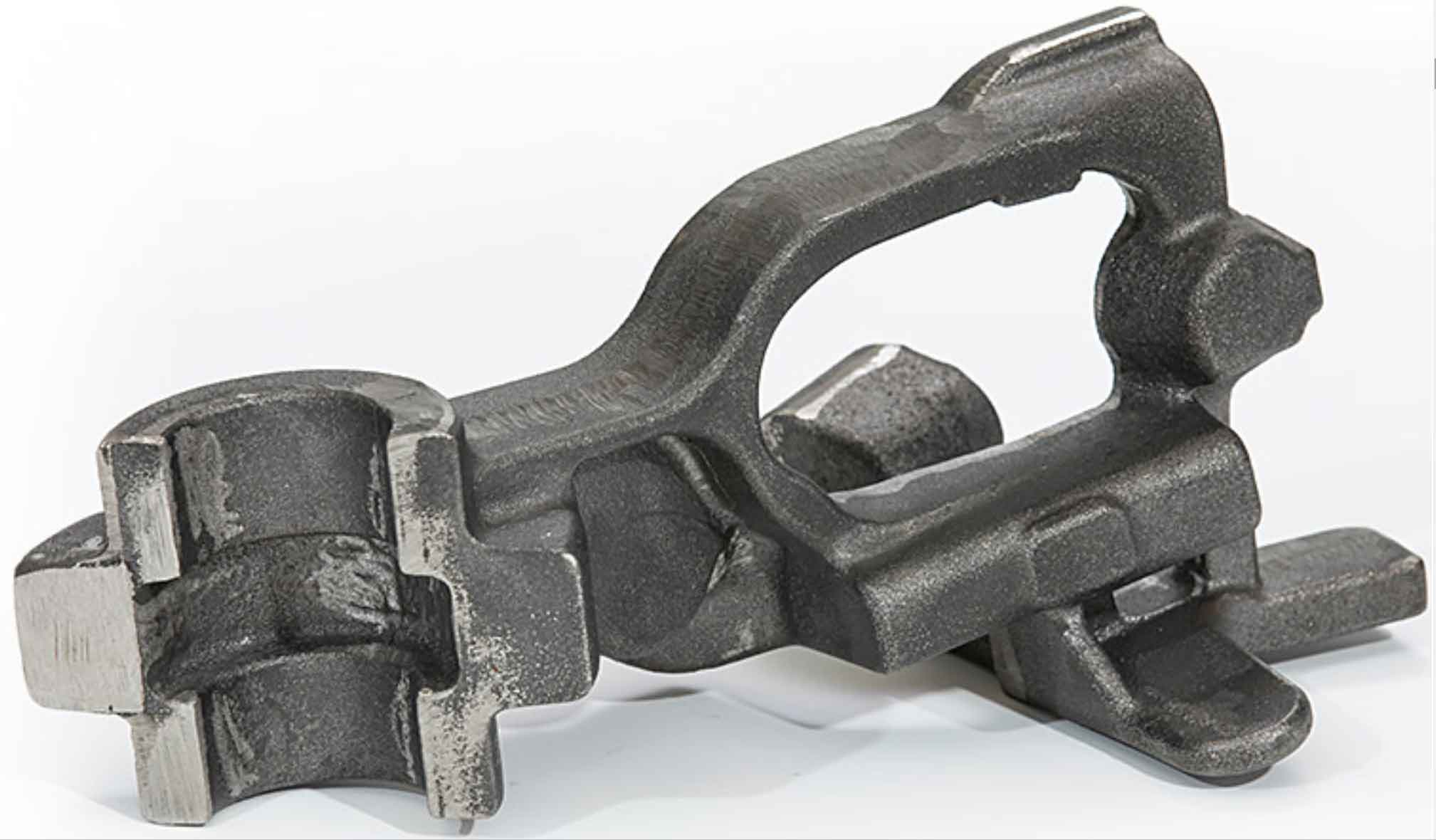
Balancing efficiency and quality in the ductile iron casting process is crucial for producing high-quality castings while maintaining cost-effectiveness and productivity. Here are some key aspects to consider:
- Raw Material Quality: Using high-quality raw materials ensures the integrity of ductile iron casting process. This includes selecting the right grade of iron and ensuring it’s free from impurities that can affect the final product’s quality.
- Melting and Pouring: The melting process should be controlled to maintain the right temperature and composition. Overheating or contamination during melting can lead to defects in the castings. Pouring temperature and rate must also be controlled to ensure complete filling of molds without introducing defects.
- Mold Design and Quality: The design of the molds plays a critical role. They need to be designed to fill evenly and cool at the right rate to avoid internal stresses and distortions. High-quality molds can withstand the stresses of casting without degrading, which ensures consistency in the casting process.
- Nodulizing Process: For ductile iron casting process, the nodulizing process, where spheroidal graphite is formed, is vital. This requires precise control of the process variables like temperature, time, and the addition of nodulizing agents.
- Heat Treatment: Post-casting heat treatments can be used to achieve desired mechanical properties. Controlled heating and cooling processes can enhance strength, ductility, and wear resistance.
- Quality Control Measures: Implementing rigorous quality control measures throughout the casting process is crucial. This includes regular testing of the material properties, inspection of the castings for surface and internal defects, and ensuring compliance with design specifications.
- Process Automation and Control Systems: Implementing advanced control systems and automation can improve both efficiency and quality. Automated systems can provide consistent control over process parameters and reduce the likelihood of human error.
- Employee Training and Expertise: Skilled workers who understand the complexities of the ductile iron casting process are essential. Continuous training and development help maintain high standards.
- Environmental and Safety Considerations: Efficient use of resources and minimizing waste not only improves cost-efficiency but is also environmentally responsible. Safety measures are also critical to protect workers from the hazards associated with casting processes.
- Continuous Improvement: Finally, adopting a philosophy of continuous improvement, where feedback and data from the casting process are used to make ongoing adjustments, can help in balancing efficiency and quality effectively.
These factors need to be carefully managed and balanced to ensure that the ductile iron casting process is both efficient and produces high-quality products. Each casting operation might prioritize these factors differently based on their specific requirements and challenges.