Lost foam casting (LFC) is a versatile and efficient process used to produce complex and precise metal parts. Despite its advantages, lost foam casting can encounter several common defects that impact the quality and performance of the final castings. This article delves into the causes, prevention, and solutions for these defects to enhance the reliability of lost foam casting.
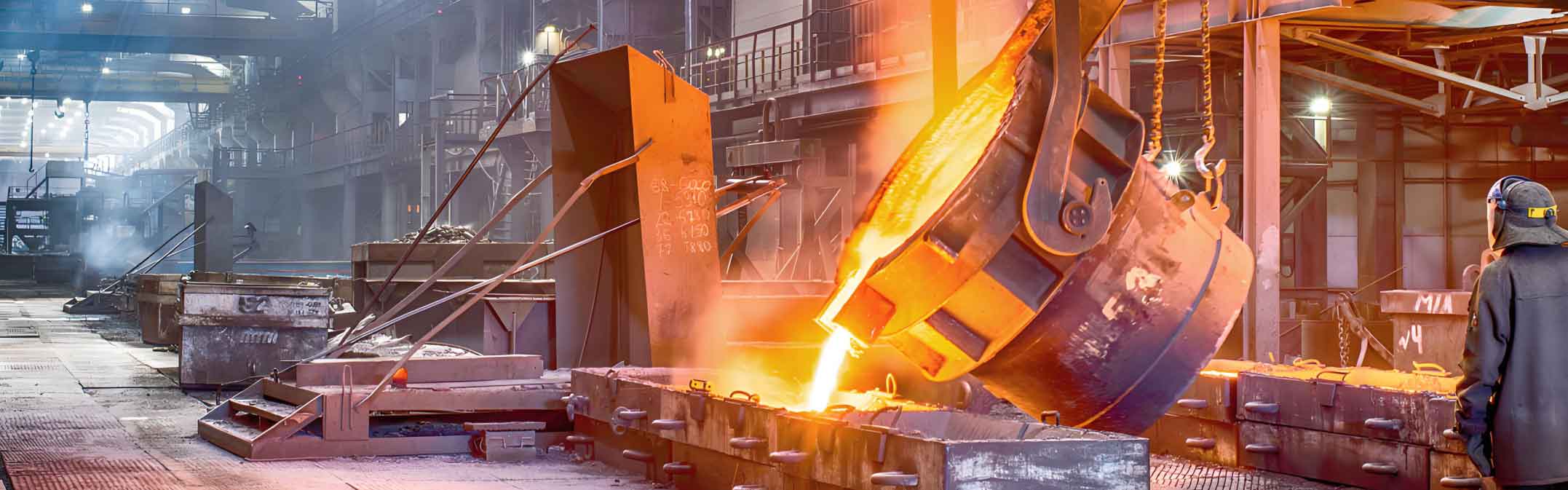
Introduction
Lost foam casting involves creating a foam pattern coated with refractory material, which is then surrounded by sand. Molten metal is poured into the mold, vaporizing the foam and leaving behind a precise metal casting. While this process is advantageous, it is prone to certain defects. Understanding these defects and implementing effective prevention and solutions is crucial for optimizing the lost foam casting process.
Common Defects in Lost Foam Casting
- Gas Porosity
- Metal Penetration
- Shrinkage Cavities
- Misruns and Cold Shuts
- Surface Roughness
Causes, Prevention, and Solutions
Gas Porosity
Causes:
- Trapped gases in the foam pattern.
- Inadequate venting during the casting process.
- Decomposition gases from the foam pattern.
Prevention and Solutions:
- Use low-density foam patterns to reduce gas generation.
- Ensure proper venting in the mold to allow gases to escape.
- Optimize the coating material and thickness to control gas permeability.
Metal Penetration
Causes:
- High pouring temperatures.
- Poor quality refractory coating.
- Inadequate compaction of sand.
Prevention and Solutions:
- Maintain appropriate pouring temperatures.
- Use high-quality refractory coatings with suitable thickness.
- Ensure proper sand compaction around the pattern to prevent metal infiltration.
Shrinkage Cavities
Causes:
- Insufficient feed metal to compensate for shrinkage.
- Inappropriate gating and riser design.
- Rapid cooling rates.
Prevention and Solutions:
- Design adequate gating and riser systems to supply feed metal.
- Use chills and insulation to control cooling rates.
- Optimize pouring parameters to ensure complete filling of the mold.
Misruns and Cold Shuts
Causes:
- Low pouring temperatures.
- Slow pouring rates.
- Complex geometry of the pattern.
Prevention and Solutions:
- Maintain proper pouring temperatures to ensure fluidity.
- Optimize pouring rates to avoid premature solidification.
- Simplify pattern design to improve mold filling.
Surface Roughness
Causes:
- Coarse sand particles.
- Poor quality refractory coating.
- Inadequate mold compaction.
Prevention and Solutions:
- Use fine-grain sand to improve surface finish.
- Apply high-quality refractory coatings to the foam pattern.
- Ensure proper compaction of the mold to achieve a smooth surface.
Comparative Table of Defects, Causes, and Solutions
Defect | Causes | Prevention and Solutions |
---|---|---|
Gas Porosity | Trapped gases, inadequate venting, foam decomposition | Use low-density foam, ensure proper venting, optimize coating |
Metal Penetration | High pouring temperatures, poor coating, sand compaction | Control pouring temperature, use quality coatings, compact sand |
Shrinkage Cavities | Insufficient feed metal, poor gating/riser design, rapid cooling | Adequate gating and riser design, use chills, optimize pouring |
Misruns and Cold Shuts | Low pouring temperatures, slow pouring rates, complex pattern geometry | Maintain pouring temperatures, optimize rates, simplify pattern design |
Surface Roughness | Coarse sand particles, poor coating, inadequate compaction | Use fine-grain sand, apply quality coatings, compact mold properly |
Detailed Analysis
Gas Porosity
Gas porosity is characterized by the presence of small holes or pores within the casting. It is primarily caused by trapped gases that fail to escape during the solidification process. Low-density foam patterns can minimize the generation of gases, while adequate venting ensures that any trapped gases are released. The coating material and its application must be optimized to provide the right balance of permeability.
Metal Penetration
Metal penetration occurs when molten metal infiltrates the sand mold, leading to a rough surface and potential structural weaknesses. High pouring temperatures and poor refractory coatings exacerbate this defect. By maintaining appropriate pouring temperatures and using high-quality coatings, manufacturers can prevent metal infiltration. Additionally, ensuring proper sand compaction around the pattern is essential.
Shrinkage Cavities
Shrinkage cavities are internal voids that form when there is insufficient feed metal to compensate for the volume reduction during solidification. Proper gating and riser systems are critical in providing the necessary feed metal. Using chills and insulation helps control the cooling rates, preventing the formation of cavities.
Misruns and Cold Shuts
Misruns and cold shuts occur when the molten metal does not completely fill the mold, resulting in incomplete or partially formed castings. This defect is often due to low pouring temperatures or slow pouring rates. Ensuring optimal pouring temperatures and rates, along with simplifying the pattern design, can mitigate this issue.
Surface Roughness
Surface roughness affects the aesthetic and functional properties of the casting. It is often caused by coarse sand particles, poor quality coatings, or inadequate mold compaction. Using fine-grain sand, applying high-quality refractory coatings, and ensuring proper compaction can significantly improve the surface finish.
Practical Applications and Case Studies
Automotive Industry
In the automotive industry, components such as engine blocks and transmission housings require high precision and minimal defects. Implementing proper venting techniques and using high-quality coatings have proven effective in reducing gas porosity and metal penetration in these components.
Aerospace Industry
The aerospace industry demands castings with superior structural integrity and minimal defects. Utilizing advanced gating and riser designs, along with optimized pouring parameters, has significantly reduced shrinkage cavities and misruns in critical components like turbine blades and structural parts.
Industrial Machinery
For industrial machinery, components such as pump housings and valve bodies require smooth surfaces and high durability. The use of fine-grain sand and proper mold compaction has enhanced the surface finish and reduced the incidence of surface roughness defects.
Future Trends and Research
- Advanced Simulation Tools
- Development of more sophisticated simulation tools to predict and mitigate casting defects.
- Integration of AI and ML algorithms in simulation for real-time defect analysis and prevention.
- Sustainable Materials and Practices
- Research into environmentally friendly materials for foam patterns and coatings.
- Adoption of sustainable practices in the casting process to reduce environmental impact.
- Enhanced Quality Control Systems
- Implementation of more advanced quality control systems incorporating real-time data analytics.
- Use of IoT and sensor technologies for continuous monitoring and control of the casting process.
Conclusion
Addressing common defects in lost foam casting is crucial for enhancing the quality and reliability of castings. By understanding the causes of these defects and implementing effective prevention and solutions, manufacturers can optimize their casting processes. The integration of advanced technologies and sustainable practices will further improve the efficiency and environmental footprint of lost foam casting, paving the way for future advancements in the industry.