Achieving complex designs with lost foam casting requires careful consideration of various techniques and best practices. Here are some key techniques and best practices to ensure successful casting of complex designs using the lost foam casting process:
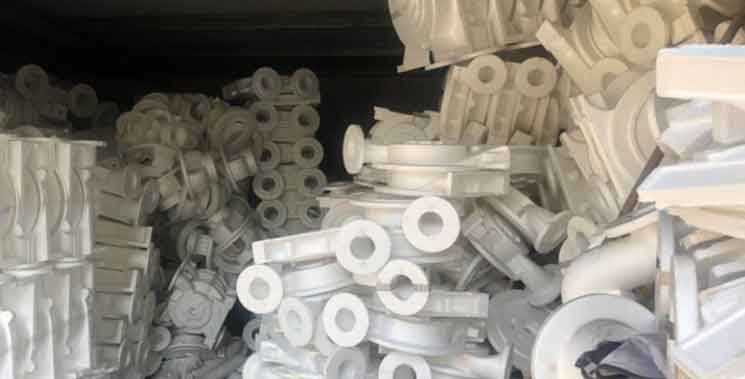
1. Pattern Design and Construction:
- Create foam patterns with the desired complex geometry, intricate details, and appropriate draft angles to facilitate pattern removal from the mold.
- Ensure the foam patterns have sufficient strength and stability to withstand handling during the coating and pouring process.
- Utilize advanced CAD software or 3D modeling techniques to accurately design the foam patterns and visualize the final casting.
2. Coating Thickness Control:
- Achieve uniform and consistent coating thickness on the foam patterns to ensure dimensional accuracy in the final casting.
- Control the viscosity and composition of the refractory coating material to achieve the desired coating thickness. This can be accomplished through proper material selection and application techniques.
- Implement quality control measures to monitor and maintain the coating thickness throughout the pattern cluster.
3. Venting and Gas Escape Channels:
- Incorporate proper venting and gas escape channels within the foam pattern cluster to allow the escape of gases generated during metal pouring.
- Venting helps to prevent gas-related defects, such as porosity or blowholes, in the final casting.
- Position venting channels strategically to ensure effective gas escape without compromising the structural integrity of the pattern cluster.
4. Pouring System Design:
- Design a well-balanced and properly sized pouring system (sprue, runners, and gates) to facilitate smooth metal flow and minimize turbulence.
- Optimize the gating system to ensure even filling of the mold and prevent the formation of cold shuts or incomplete castings.
- Consider the location and design of the pouring system to minimize the impact of turbulence and reduce the risk of erosion on the foam patterns.
5. Process Monitoring and Control:
- Implement process monitoring and control systems to ensure consistent and repeatable casting results.
- Monitor key process parameters such as metal temperature, mold temperature, pouring rate, and solidification time.
- Use real-time monitoring techniques, such as thermocouples or pyrometers, to accurately track and control the casting process.
6. Quality Assurance and Inspection:
- Perform thorough quality checks and inspections on the foam patterns, mold coatings, and finished castings.
- Conduct dimensional inspections to ensure that the complex features and geometries of the design are accurately replicated in the final castings.
- Utilize non-destructive testing methods, such as X-ray or ultrasonic inspection, to detect any internal defects or discontinuities.
7. Post-Casting Processing and Finishing:
- Plan and execute appropriate post-casting processing and finishing operations to achieve the desired surface finish and dimensional accuracy.
- Utilize techniques such as grinding, sanding, machining, or surface treatments to remove any imperfections or excess material.
- Perform final inspections and quality checks after post-casting processing to ensure the desired specifications are met.
By implementing these techniques and following best practices, manufacturers can successfully achieve complex designs with lost foam casting. It is important to optimize each step of the process, from pattern design and construction to post-casting finishing, to ensure the production of high-quality castings that accurately reflect the intricate features and geometries of the original design.