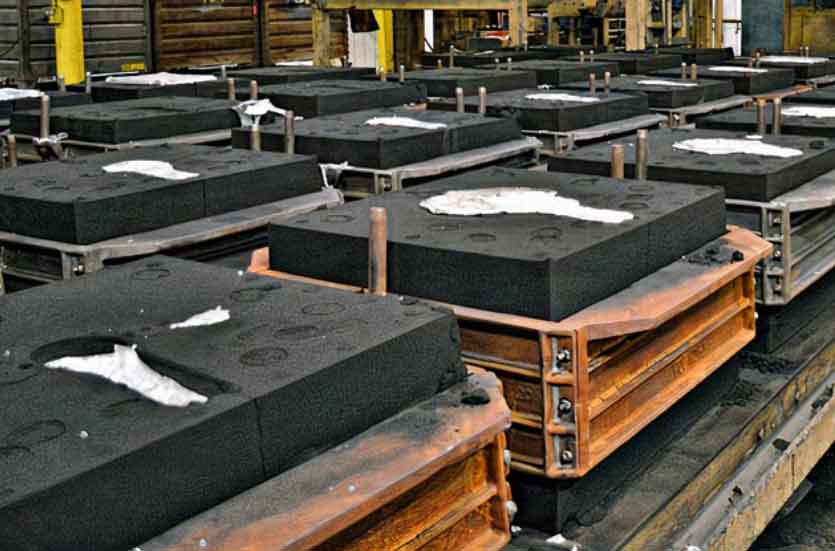
Resin sand casting has seen advancements and found numerous applications across various industries due to its versatility, cost-effectiveness, and ability to produce complex parts. Here are some notable advancements and applications of resin sand casting in industry:
- Improved Resin Binders: Advancements in resin binders have led to improved casting quality and reduced environmental impact. Modern binders offer better flowability, reduced gas emissions during casting, and improved sand reusability. These advancements have contributed to higher dimensional accuracy, enhanced surface finish, and reduced casting defects.
- Rapid Prototyping and Small-Batch Production: Resin sand casting allows for rapid prototyping and small-batch production of metal components. By utilizing 3D printing technology to create the patterns, designers can quickly iterate and test their designs before committing to mass production. This enables faster product development cycles and cost-effective production of low-volume parts.
- Complex and Large-Scale Components: Resin sand casting has proven to be suitable for producing complex and large-scale components. It offers the capability to create intricate geometries, internal cavities, and thin walls that may be challenging or cost-prohibitive using other manufacturing methods. Industries such as aerospace, automotive, and industrial machinery benefit from the ability to manufacture large, complex parts in a cost-effective manner.
- Material Versatility: Resin sand casting supports a wide range of metals and alloys, including aluminum, iron, steel, bronze, and more. This material versatility allows for the production of components with varying properties such as strength, corrosion resistance, and thermal conductivity. Industries can choose the appropriate material based on their specific requirements, expanding the application possibilities of resin sand casting.
- Repair and Replacement Parts: Resin sand casting is an ideal method for producing repair and replacement parts. Instead of going through expensive tooling and setup processes for traditional manufacturing methods, resin sand casting offers a quicker and cost-effective solution. This is particularly useful in industries such as automotive, machinery, and infrastructure maintenance, where replacement parts are frequently required.
- Customization and Artistic Casting: Resin sand casting also finds applications in creating customized and artistic metal components. The process allows for the production of one-of-a-kind pieces with intricate details, textures, and designs. This has found utility in architectural applications, art and sculpture, jewelry, and other creative industries.
- Energy Efficiency: Resin sand casting can be more energy-efficient compared to other manufacturing methods. The process requires relatively low energy inputs compared to techniques like die casting or machining. Additionally, the use of sand as a mold material is environmentally friendly and easily recyclable, contributing to sustainability efforts.
- Cost-Effectiveness: Resin sand casting offers a cost-effective manufacturing solution, especially for medium to large-sized components or low to medium production volumes. It eliminates the need for expensive tooling and complex setups associated with other methods like investment casting or die casting. This makes it an attractive option for industries seeking cost savings without compromising quality.
As resin sand casting continues to advance, it is expected to find more applications in diverse industries, providing a bridge between design flexibility and cost-effective production of complex metal components.