Grey cast iron foundry practices face several challenges and continually strive for innovations to improve efficiency, sustainability, and product quality. Here are some of the key challenges and ongoing innovations in grey cast iron foundry practices:
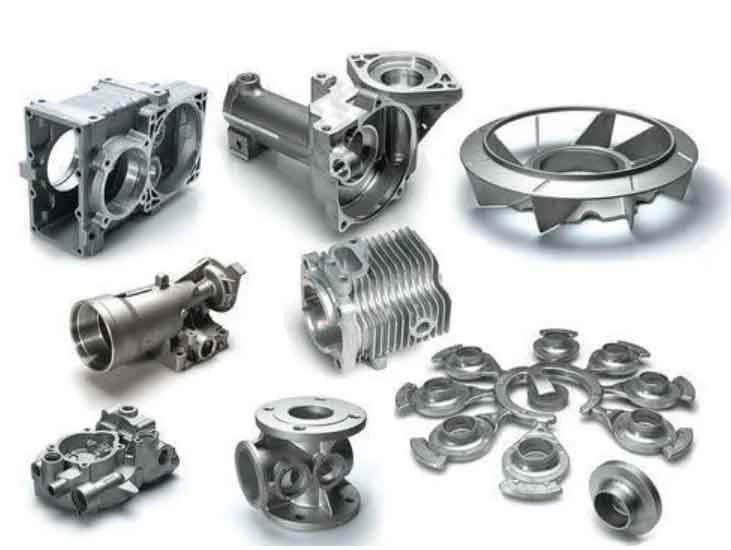
Challenges:
1. Environmental Regulations:
- Foundries must comply with stringent environmental regulations regarding emissions, waste management, and energy consumption. Meeting these requirements can be challenging for traditional foundries that may have older equipment and processes.
2. Recycling and Sustainability:
- While grey cast iron is recyclable, optimizing the recycling process and incorporating more sustainable practices, such as using renewable energy sources and reducing material waste, remains an ongoing challenge.
3. Material Sourcing and Cost:
- Access to high-quality raw materials, such as scrap iron and alloys, at reasonable prices can impact the overall cost and profitability of foundry operations.
4. Energy Efficiency:
- Foundries are under pressure to improve energy efficiency and reduce their carbon footprint. Reducing energy consumption while maintaining production efficiency can be a significant challenge.
5. Workforce Skills and Training:
- As foundries modernize their processes and implement new technologies, they need a skilled workforce capable of operating and maintaining advanced equipment.
6. Casting Defects:
- Grey cast iron foundries must address common casting defects, such as porosity, inclusions, and shrinkage, which can impact product quality and increase the need for post-casting rework.
7. Machining and Finishing Operations:
- Machining and finishing grey cast iron components can be labor-intensive and time-consuming, affecting overall production efficiency.
Innovations:
1. Advanced Simulation and Modeling:
- Foundries are increasingly adopting computer simulation and modeling tools to optimize mold design, gating systems, and solidification processes. These technologies help identify potential defects and improve casting quality.
2. Additive Manufacturing for Tooling:
- The use of additive manufacturing (3D printing) for producing sand molds and cores has shown promise in reducing lead times and enabling more complex and customized designs.
3. Automated and Robotic Systems:
- Automation and robotics are being introduced in foundries to enhance production efficiency, reduce labor-intensive tasks, and improve consistency in casting operations.
4. Eco-Friendly Binders:
- Foundries are exploring eco-friendly binder systems that reduce emissions and waste while maintaining casting quality.
5. Real-Time Monitoring and Quality Control:
- Implementing real-time monitoring systems allows foundries to identify potential issues during the casting process and take corrective actions promptly, leading to higher-quality products.
6. Surface Coatings and Treatments:
- Advanced surface coatings and treatments can improve the wear resistance and performance of grey cast iron components, expanding their range of applications.
7. Green Sand Reclamation:
- Grey cast iron foundries are investing in green sand reclamation technologies to recycle and reuse sand, reducing the environmental impact of sand disposal.
Addressing these challenges and adopting innovative practices is vital for grey cast iron foundries to remain competitive, sustainable, and efficient in today’s manufacturing landscape. By leveraging technology, optimizing processes, and embracing sustainability, foundries can continue to produce high-quality grey cast iron components while reducing their environmental impact.