Lost foam casting offers several sustainable advantages, making it an eco-conscious choice for manufacturers looking to minimize their environmental impact and promote sustainable practices. Here are the ways in which lost foam casting contributes to sustainability:
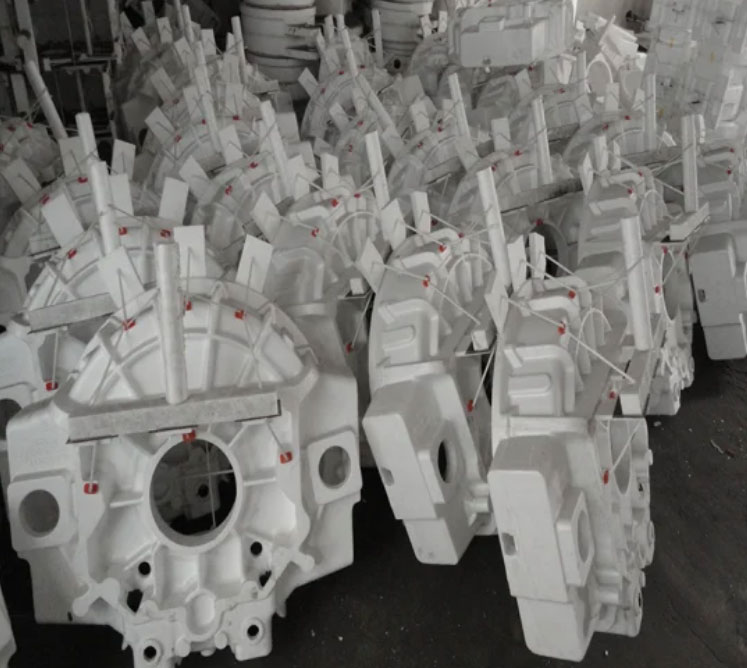
1. Material Efficiency:
- Lost foam casting produces near net shape castings, reducing the need for excessive material allowances typically required for machining in traditional casting methods. This leads to significant material savings and minimizes material waste.
2. Elimination of Pattern Waste:
- Unlike traditional casting methods that use expendable patterns made of sand, wax, or plastic, lost foam casting uses foam patterns that are entirely vaporized during the casting process. As a result, there is no waste associated with the removal or disposal of pattern materials.
3. Energy Conservation:
- Lost foam casting typically requires less energy compared to other casting processes that involve heating, melting, and maintaining high temperatures. The elimination of pattern removal and cleaning steps also contributes to energy savings.
4. Reduced Carbon Footprint:
- With reduced material waste, lower energy consumption, and fewer emissions associated with pattern removal, lost foam casting helps in lowering the overall carbon footprint of the casting process.
5. Recycling and Reuse:
- The foam patterns used in lost foam casting are expendable and can be easily recycled or reused, minimizing material waste and promoting sustainable practices.
6. Environmentally Friendly Materials:
- The foam patterns in lost foam casting are made of expanded polystyrene (EPS), which is a recyclable and non-toxic material. This makes it an environmentally friendly alternative to some pattern materials used in traditional casting methods.
7. Reclamation of Sand:
- Lost foam casting can be performed with sand casting molds, and foundries can implement sand reclamation technologies to recycle and reuse the sand used in the casting process. This reduces the demand for new sand and minimizes waste.
8. Reduction in Post-Casting Machining:
- Near net shape castings produced through lost foam casting require less post-casting machining and finishing, which reduces the energy consumption associated with machining processes.
9. Sustainable Design and Lightweighting:
- The design flexibility offered by lost foam casting enables the creation of lightweight and optimized components, leading to reduced material consumption and improved energy efficiency in end products.
10. Waste Reduction in Finishing Processes:
- The smoother surface finish of lost foam castings reduces the need for additional surface treatments, such as grinding or polishing, leading to further waste reduction.
Overall, lost foam casting aligns with sustainable manufacturing practices, providing manufacturers with an eco-conscious option for producing complex components with reduced material waste, lower energy consumption, and a smaller environmental footprint. By adopting lost foam casting, manufacturers can contribute to environmental preservation while achieving the desired product quality and design flexibility.