0 Introduction
Automotive engine heads have complex structures and are typically cast from cast iron or aluminum alloys, as shown in Figure 1. The cylinder cavity structure is complex, locally thick and easy Shrink. The cylinder head is installed on top of the cylinder block, sealing the cylinder from the upper part and forming the combustion chamber. It is often burned with high temperature and high pressure In contact with gas, it is subjected to a large thermal and mechanical load. The main waste leakage and trachoma, the manufacturing process has many complex parameters and changeable processes. There are many casting production processes, and each process has a wide variety of paper process data record tables, scattered in different stations, data query, statistics and analysis time-consuming, the annual output of two types of castings exceeds 200,000 pieces, the failure rate exceeds 5%, and the quality fluctuates greatly.
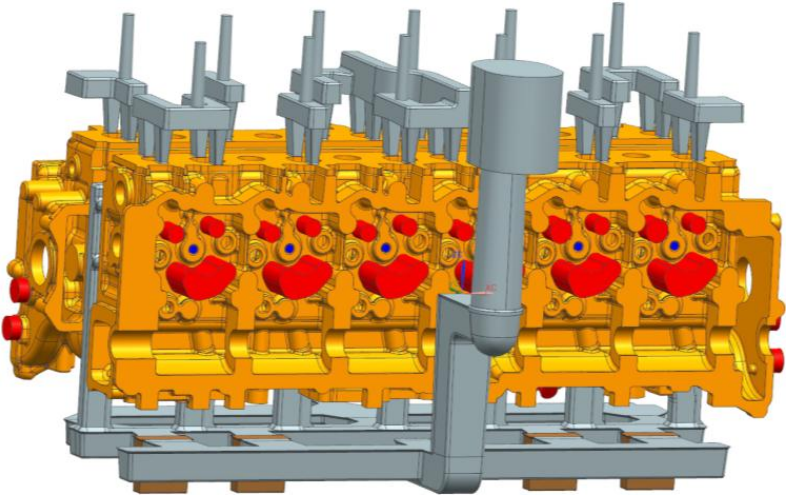
Fig. 1 3D diagram of cylinder castings, gating systems, etc
At present, the production of domestic automobile cylinder blocks and cylinder heads mainly adopts wet molding sand, resin self-hardening sand and triethylamine cold core forming process. The gas solute in the liquid phase is highly concentrated in the solidification of the casting, and vacuum holes will be generated when shrinkage occurs at the hot joint, and the existence of holes proposes a strong channel for the precipitation of gas, which then hinders the shrinkage of metal liquid and aggravates the formation of shrinkage defects. Common defects in cylinder heads are shown in Figure 2.
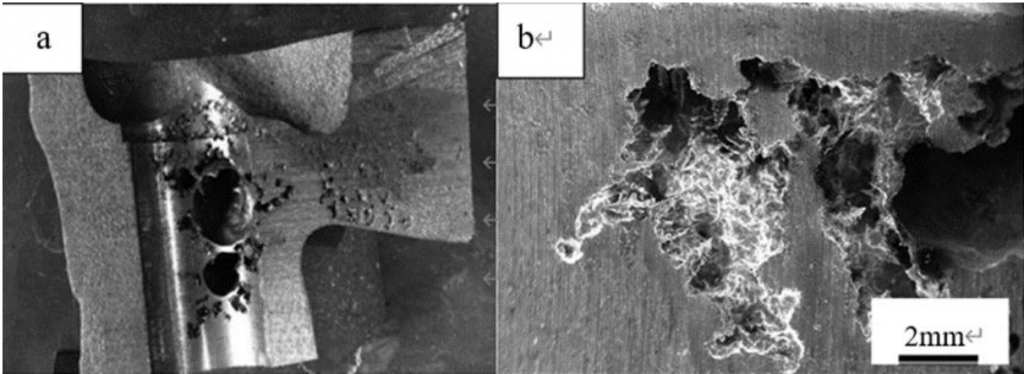
Fig. 2 Defect topography of cylinder head castings
Using computer numerical simulation technology to simulate the investment precision casting process, you can understand the casting solidification process in advance and predict the defects produced by the casting process, and you can determine the ideal process plan before the actual production, avoid technical risks, and improve product quality. Huazhong University of Science and Technology Huazhu CAE/InteCAST software system (referred to as Huazhu CAE system) is one of the powerful and widely used casting process analysis software in China, and the prediction of shrinkage holes and shrinkage defects has reached a quantitative degree. Using Huazhu CAE software, taking the process of a car engine cylinder head casting as an example, the CAE simulation software is used to study the key process parameters of sand casting, namely pouring temperature and casting temperature on shrinkage defects.
1 Test materials and methods
1.1 Test Materials
The casting material is vermicular graphite cast iron, the model is RU450, and the molding sand is used for green sand casting Sand, reused sand + bentonite + pulverized coal and other additives, the sand core is mainly cold box process, silica sand or recycled sand + cold core resin. As shown in Table 1, the main process parameters are pouring temperature, mould temperature, mould filling time, etc., and the pouring temperature and mould temperature are selected as the main influencing factors for simulation experiments. The simulation protocol is shown in Table 2.
Table 1 Process parameters
工艺参数 | 浇注温度/℃ | 铸型温度/℃ |
范围 | 1 360~1 400 | 20~40 |
Table 2 Simulation protocol
编号 | 浇注温度/℃ | 铸型温度/℃ |
1 | 1360 | 20 |
2 | 1370 | 20 |
3 | 1380 | 20 |
4 | 1390 | 20 |
5 | 1400 | 20 |
6 | 1360 | 30 |
7 | 1370 | 30 |
8 | 1380 | 30 |
9 | 1390 | 30 |
10 | 1400 | 30 |
11 | 1360 | 40 |
12 | 1370 | 40 |
13 | 1380 | 40 |
14 | 1390 | 40 |
Table 3 meshing scheme
网格类型 | 总网格数/个 | 铸件网格数/个 | 最大边长/mm | 最小边长/mm | 浇注重量/kg | 铸件毛重/kg | 工艺出品率 (%) |
均匀 网格 | 13296465 | 960627 | 3.5 | 3.5 | 408 | 283 | 69.33 |
1.2 Numerical simulation software and methods
The numerical simulation software used is Huazhu CAE system, which mainly uses its gravity compensation function to predict the formation of shrinkage holes and shrinkage during the solidification process. In the pre-processing stage, 3D models such as castings and casting systems are meshed, and the meshing scheme is shown in Table 3.
2 Test results and analysis
2.1 Solidification color temperature simulation results of castings
The pure solidification process of the cylinder head was simulated using Huazhu CAE software, and the simulation results are shown in Figure 3, due to the flat group vertical pouring process and the bottom injection jacking system, the solidification of the cylinder head is carried out sequentially from the bottom up.
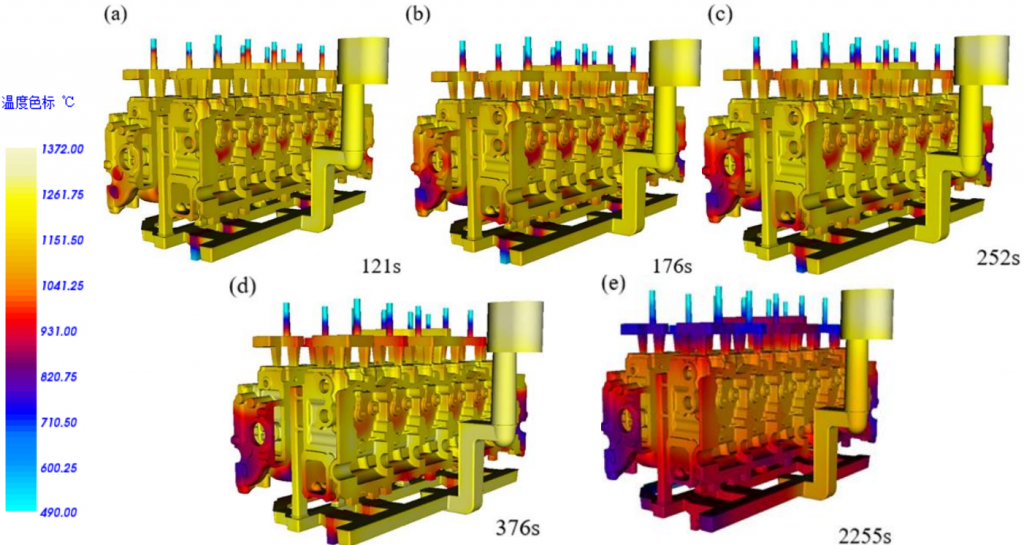
Figure 3 The solidification color temperature of the casting
2.2 Simulation results of shrinkage defect evolution
In the temperature range of the experiment (pouring temperature 1 360~1 400 °C, mold temperature 20~40 °C), it can be seen from Figure 4 that there are different amounts of shrinkage in the hot joint position inside the cylinder head.
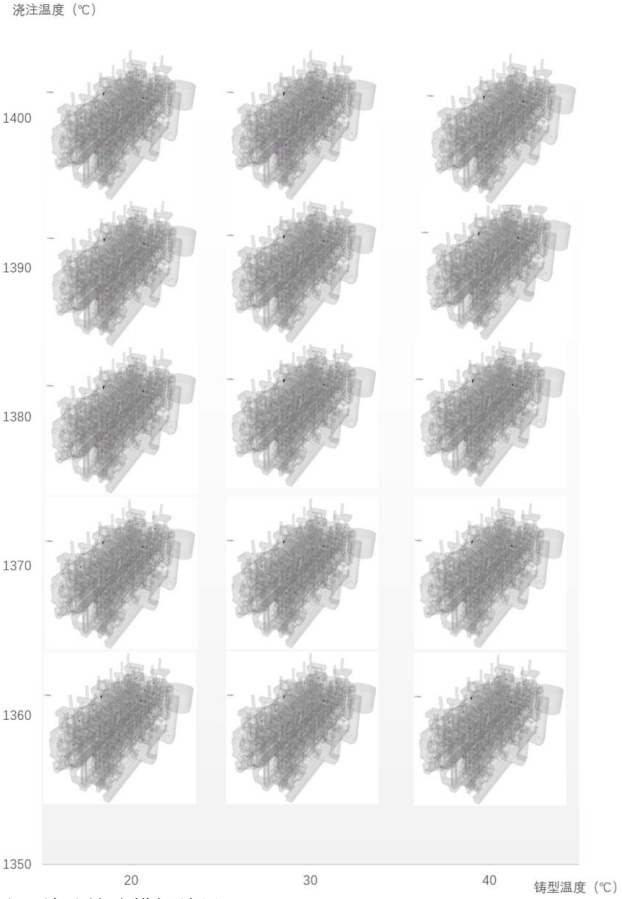
Figure 4 Shrinkage defect simulation results
2.3 Influence of pouring temperature and mold temperature on the number of shrinkage defects
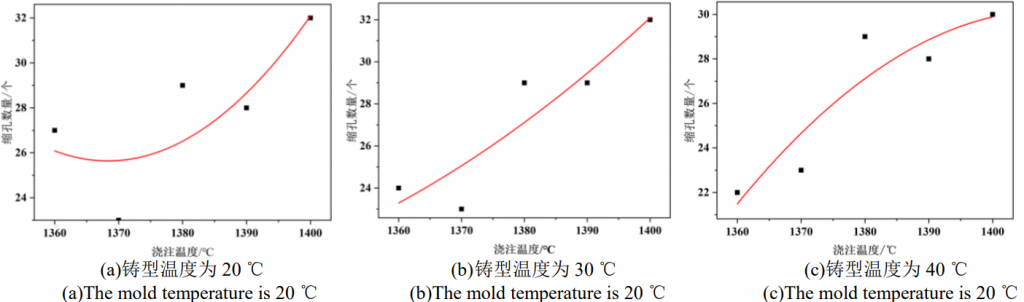
Fig. 5 Number of shrinkage holes in the cylinder head at different pouring temperatures
The number of shrinkage defects at different pouring temperatures is shown in Figure 5, when the cylinder head mould temperature is 20 °C, with the increase of pouring temperature, the number of shrinkage holes first decreases and then increases, when the pouring temperature is 1 370 °C, the minimum number of shrinkage holes is 22, when the mold temperature is 30 °C and 40 °C, the number of shrinkage holes increases with the increase of the pouring temperature, and the minimum number of shrinkage holes is 24 and 22 when the pouring temperature is 1 360 °C.
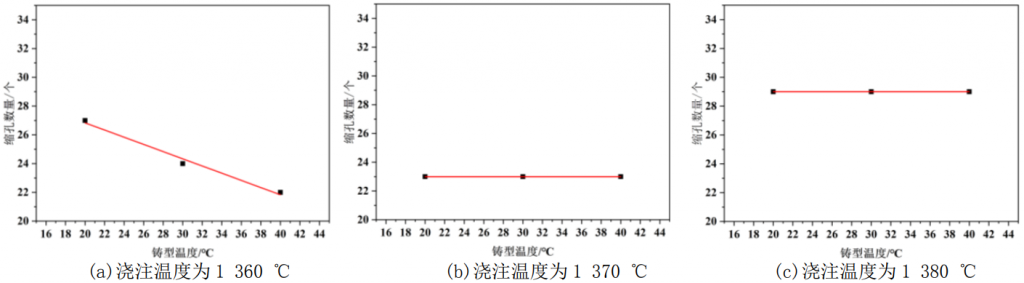
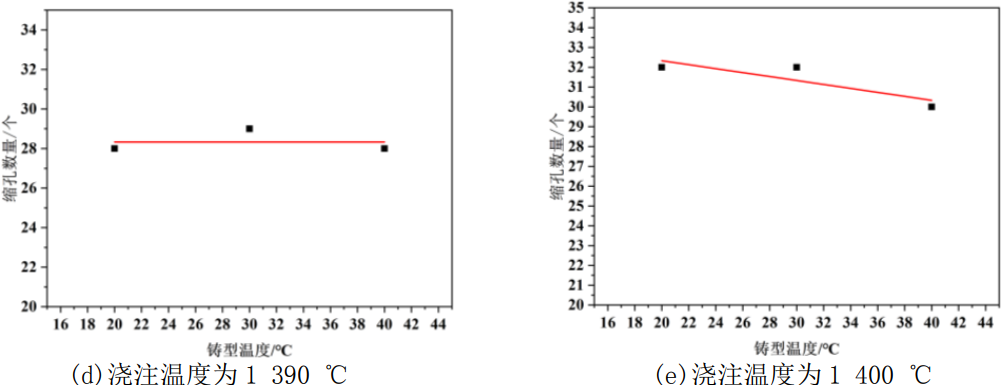
Fig. 6 Number of shrinkage holes in the cylinder head at different mould temperatures
The number of shrinkage defects with different mold temperatures is shown in Figure 6, and when the pouring temperature is between 1 370~1 400 °C, the number of shrinkage holes is not sensitive to the mold temperature in the range of 20~40 °C.
2.4 Analysis of sensitivity analysis of shrinkage defects to pouring temperature and mold temperature
From Figures 5 and 6, it is easy to see that the number of shrinkage holes has an approximate linear relationship with the pouring temperature and the mold temperature, and the linear correlation coefficient r of the number of shrinkage holes and the pouring temperature and the mold temperature can be found.composed(2-1)式:

where Cov(X,Y) is the covariance, Var[X] is the variance of X, and Var[Y] is the variance of Y.
The correlation coefficient between the number of crater holes and the pouring temperature r1=0.725 1 at a mould temperature of 20 °C, r2= 0.919 9 for the number of craters and the pouring temperature at a mould temperature of 30 °C, and r3= 0.910 5 for the number of craters and the pouring temperature at a mould temperature of 40 °C When the injection temperature is 1 360 °C, the correlation coefficient between the number of shrinkage holes and the mold temperature is r4= -0.993 4, and when the pouring temperature is 1 370 °C, the variance of the number of shrinkage holes is 0, which is considered uncorrelated. When the pouring temperature is 1 380 °C, the variance of the number of crater holes is 0, which is considered uncorrelated; When the pouring temperature is 1390 °C, the correlation coefficient between the number of shrinkage holes and the mold temperature r5 = 0 is considered uncorrelated; At a pouring temperature of 1 400 °C, the correlation coefficient between the number of craters and the mould temperature is r6= -0.866. In summary, it can be seen that at a casting temperature of 20~40 °C and a pouring temperature of 1 360~1 400 °C, the influence of pouring temperature on the number of shrinkage holes is more obvious than that of the mold temperature, that is, the number of shrinkage holes is more sensitive to the pouring temperature.
3 Conclusion
(1) The cylinder head uses vermicular graphite cast iron RU450, the internal cavity structure is complex, locally thick and easy to shrink, and it is easy to produce shrinkage hole defects at the internal thick wall.
(2) When the cylinder head casting temperature is 20 °C, with the increase of the pouring temperature, the number of shrinkage holes first decreases and then increases, when the pouring temperature is 1 370 °C, the minimum number of shrinkage holes is 22, when the mold temperature is 30 °C and 40 °C, with the increase of pouring temperature, the number of shrinkage holes increases, and when the pouring temperature is 1 360 °C, the minimum number of shrinkage holes is 24 and 22, respectively.
(3) When the pouring temperature is 1 370~1 400 °C, the number of shrinkage holes is not sensitive to the mold temperature of 20~40 °C.
(4) When the mold temperature is 20~40 °C and the pouring temperature is 1 360~1 400 °C, the influence of pouring temperature on the number of shrinkage holes is more obvious than the mold temperature, that is, the number of shrinkage holes is more sensitive to the pouring temperature.