1. Foam mold size determination
The design of foaming mould mainly includes the following aspects: determining the size parameters of foaming mould, designing the cavity surface of mould, designing the thin shell structure of mould, designing the structure of mobile mould, designing the core block and core pulling mechanism, designing the air permeability of mould, etc.
The size parameters of the mold are mainly determined by the size of the parts. On the basis of this, the processing parameters such as machining allowance, shrinkage rate and draft angle are considered. Finally, the molding process of the foam pattern is examined and approved to determine the size of the die.
Therefore, the blade parts obtained above need to be further processed, mainly including the following aspects:
Therefore, the blade parts obtained above need to be further processed, mainly including the following aspects:
(1) First of all, the shrinkage of casting should be determined, which includes three aspects. Σε=ε0+ε1+ε2。。 The shrinkage rate of EPC casting is the bus shrinkage of EPC Castings, and the linear shrinkage rate of EPC 0 is resin sand casting (blank type) casting. The casting shrinkage of GLH-5 high chromium alloy is calculated by 2%, and epsilon 1 is the linear shrinkage rate of the foaming moulds made of foam polystyrene (EPS) after foaming. 0.25%; ε 2 is the additional shrinkage of the model in the process of coating application and drying, which can be increased by 0.1% – 0.15% according to the difference of model structure and dry strength of the coating. In conclusion, Σ ε = 2.35%;
(2) The general principle of draft processing and slope setting is: the size of both ends of the draft should meet the tolerance of the parts; in order to facilitate the future repair of the mold, the product should be as small as possible. In order to ensure the accuracy of the blade, the movable block die structure is adopted and the draft is cancelled.
(3) Because the blade is located inside the impeller, there is no need to process, so there is no need to consider the machining allowance when designing the blade foaming mold;
(4) The typical feature of EPC foam mold is that the whole mold is the shape following of thin shell, and the shape following is the basis of obtaining the surface clean pattern. According to the design requirements of foaming mould, the thickness of die shell with aluminum material is 15mm. The follow-up surface can be guaranteed by the following specific NC machining process.
Through the above operations, the mold cavity size can be basically determined.
2. Foam mold module design
The core step of mold design is the selection of parting surface. The correct choice of parting surface has an important influence on the molding process, casting size, process equipment design, cost, accuracy and productivity. So the drawing of parting surface is very important. After research, it is determined that the following principles should be followed when drawing parting surface:
(1) The selection of parting surface is generally located on the largest projection surface of casting.
(2) All or major parts of castings shall be placed in the same half of the mold as far as possible to avoid dimensional deviation due to wrong mold.
(3) The number of parting surfaces should be minimized to ensure the casting accuracy and simplify the process.
(4) The parting surface should be as plane as possible to simplify the molding process and the manufacturing of the die base plate, so as to ensure the casting accuracy.
(5) The selection of parting surface of stressed parts shall not weaken the structural strength of castings.
For blades, the parting surface shall be determined according to the above principles. Since the blade is a space twisted shape, the method of curved surface parting and mold opening direction are adopted to avoid oblique core pulling and large movable block as much as possible. The shadow and the area that affects the mold taking shall be made into a live block. Through the analysis of the whole mold, four moving blocks are used. Exploded view of the whole mold.
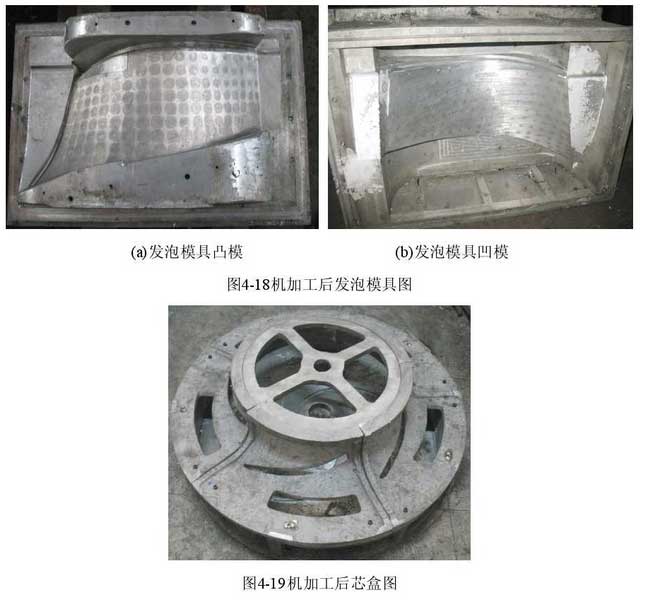