Shrinkage cavity and shrinkage porosity are common internal casting defects in heavy position of ductile iron castings. The shrinkage cavity and porosity of the intake cylinder casting are mainly distributed in the cross section of the upper 400mm stator blade flange and the wall thickness intersection area with complex hot spot distribution. From the observation of the cross-section morphology revealed after processing, the hole wall of shrinkage cavity and porosity defect is rough with dendrite, and the contour is very irregular, which is centralized distribution (usually called shrinkage cavity) and dispersed distribution (commonly called shrinkage porosity). Some defects are exposed after machining (as shown in Fig. 1), and some defects are distributed in the casting, which can be detected by ultrasonic testing.
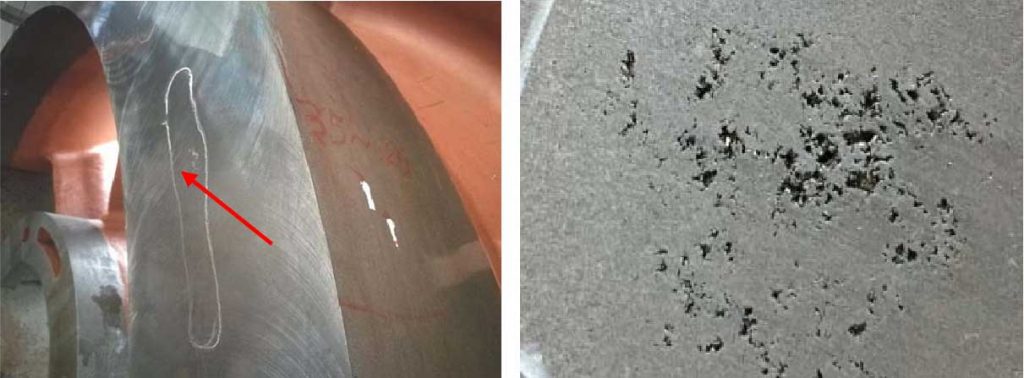
Shrinkage cavity and porosity will reduce the physical and mechanical properties of the gas turbine inlet cylinder casting, especially the bearing area of the bearing part, and even cause serious accidents in the process of use and service due to the stress concentration. If there is large area of shrinkage cavity and porosity defects in the heavy load-bearing castings similar to the gas turbine inlet cylinder, the castings will be scrapped directly. Nodular cast iron casting has poor repair weldability, so it is not allowed to repair defects by welding. If some defects are exposed when the subsequent finishing is about to be completed and belong to the key bearing position, it will lead to the scrapping of all parts and components matched with the inlet cylinder, and the economic loss to the company is estimated to be more than 2.3 million yuan.
Therefore, shrinkage cavity and porosity are not allowed in the important inspection position required in the acceptance standard of intake cylinder casting. Shrinkage cavity and porosity defect with large section is one of the key points in the research of intake cylinder casting technology.
In ductile iron (nodular cast iron) castings, such as intake cylinders with heavy sections, the distribution of isolated hot spots and shrinkage porosity is a significant concern that can affect the casting’s mechanical properties, durability, and overall performance. Understanding the formation and distribution of these defects is crucial for optimizing casting processes and improving the quality of the final product.
Formation of Isolated Hot Spots and Shrinkage Porosity
- Isolated Hot Spots: These are areas within the casting that cool more slowly than the surrounding material. In heavy section castings, isolated hot spots are common due to the varied thicknesses of the material, where thicker sections retain heat longer. These areas can remain molten while the rest of the material solidifies, leading to local mismatches in cooling rates and potential for defects.
- Shrinkage Porosity: As ductile iron solidifies and cools, it undergoes a volume reduction. If the liquid metal feeding cannot compensate for this shrinkage, voids or porosities can form. Shrinkage porosity is more likely to occur in areas where solidification is the last to complete, such as isolated hot spots. In heavy sections of a casting, the risk of shrinkage porosity increases due to the difficulty in ensuring adequate feeding of molten metal to these regions as solidification progresses.
Distribution in Heavy Section Castings
The distribution of isolated hot spots and shrinkage porosity in heavy sections of ductile iron castings, like intake cylinders, is influenced by several factors:
- Section Thickness: Thicker sections are more prone to developing isolated hot spots due to slower cooling rates. These areas are at a higher risk for shrinkage porosity since they are the last to solidify, potentially creating voids if not properly fed with molten metal.
- Casting Design: The geometry of the casting can influence the distribution of these defects. Areas with complex geometries or sudden changes in section thickness are particularly vulnerable.
- Feeding System Design: An inadequate gating and riser system can lead to insufficient feeding of molten metal to heavy sections, exacerbating the formation of shrinkage porosity.
- Material Composition and Cooling Rate: The chemical composition of the ductile iron and the cooling rate also play roles in the formation of these defects. Alloying elements that influence the solidification temperature range can affect the risk of shrinkage porosity.
Mitigation Strategies
- Optimize Casting Design: Design modifications, such as adding fillets, changing section thicknesses gradually, or using cores to create uniform section thicknesses, can help minimize hot spots.
- Improved Gating and Risering: Designing an effective gating and riser system ensures adequate molten metal supply to compensate for shrinkage throughout the solidification process, especially in heavy sections.
- Controlled Cooling: Applying controlled cooling techniques, such as directional solidification or the use of chills, can help manage the cooling rate, reducing the risk of isolated hot spots and shrinkage porosity.
- Heat Treatment: Post-casting heat treatments may also alleviate some effects of these defects by homogenizing the microstructure, although they cannot remove porosities.
Understanding and addressing the distribution of isolated hot spots and shrinkage porosity in heavy sections of ductile iron castings are vital for producing high-quality, defect-free components. Through careful design, process control, and post-casting treatments, manufacturers can significantly reduce the incidence of these defects, enhancing the performance and reliability of the cast products.