Chapter 1: Chemical Composition and Alloying Elements of Ductile Iron Casting
Ductile iron casting, also known as nodular or spheroidal graphite iron, is a type of cast iron that has been treated with small amounts of magnesium or cerium to induce the formation of graphite in the form of nodules, rather than the flake-like structure found in traditional gray iron. The chemical composition and alloying element content of ductile iron casting can vary based on the specific grade and intended application. However, here is a general overview of the typical composition and alloying elements found in ductile iron casting:
Chemical Composition (Typical Range):
- Carbon (C): 3.2% – 4.2%
- Silicon (Si): 1.8% – 3.0%
- Manganese (Mn): 0.1% – 0.5%
- Sulfur (S): 0.02% max
- Phosphorus (P): 0.1% max
- Magnesium (Mg): 0.03% – 0.06% (for nodularization)
- Copper (Cu): 0.4% max (typically low)
Alloying Elements:
- Magnesium (Mg): Added in controlled amounts to promote the formation of nodular graphite (spheroids) instead of flake graphite. This enhances ductility and toughness.
Other Trace Elements:
- Chromium (Cr): Occasionally present in small amounts to enhance resistance to corrosion and wear, particularly in specialized applications.
- Nickel (Ni): Sometimes added to improve high-temperature properties and corrosion resistance.
- Molybdenum (Mo): Used in some grades to enhance mechanical properties and high-temperature strength.
It’s important to note that there are several grades of ductile iron casting, each with its own specific composition and alloying elements tailored for particular applications. For example, there are ferritic, pearlitic, and austempered grades of ductile iron casting, each designed to offer different combinations of mechanical properties such as strength, toughness, wear resistance, and machinability.
The chemical composition and alloying element content are carefully controlled during the melting and casting processes to achieve the desired microstructure and properties in the final ductile iron casting. The choice of grade and composition depends on factors such as the application’s mechanical requirements, corrosion resistance, and other performance characteristics.
Chapter 2: The Material Characteristics of Ductile Iron Casting
Ductile iron casting exhibits a combination of material characteristics that make it suitable for a wide range of industrial applications. These characteristics include:
1. Strength:
- Ductile iron casting has higher tensile strength than gray iron, making it well-suited for applications requiring load-bearing capacity and structural integrity.
- Its strength is comparable to some mild and low-alloy steels, allowing for the substitution of steel components in certain applications.
2. Toughness:
- Ductile iron casting is known for its excellent toughness and impact resistance due to its nodular graphite structure. The nodules act as “crack arresters,” preventing the propagation of cracks and enhancing overall durability.
- It can absorb more energy before failure compared to other cast irons, making it suitable for applications subject to dynamic loads.
3. Wear Resistance:
- Ductile iron casting can exhibit good wear resistance, particularly in abrasive environments, due to the presence of hard metallic carbides in its microstructure.
- Alloying elements like chromium and molybdenum can further enhance wear resistance in specific grades.
4. Machinability:
- Ductile iron casting can be machined relatively easily, especially when compared to some other cast metals like gray iron.
- It has good chip control and can be machined to tight tolerances.
5. Thermal Conductivity:
- Ductile iron casting has moderate thermal conductivity, allowing it to efficiently dissipate heat. This property is beneficial for applications involving heat transfer.
6. Corrosion Resistance:
- While not as corrosion-resistant as some non-ferrous metals, certain grades of ductile iron casting can offer satisfactory corrosion resistance in various environments.
- Alloying elements like chromium and nickel can enhance its resistance to certain types of corrosion.
7. Castability and Complexity:
- Ductile iron casting is highly castable, allowing for the production of complex shapes and intricate details.
- It can be cast using a variety of methods, including sand casting, investment casting, and more.
8. Damping Capacity:
- Ductile iron casting exhibits good damping capacity, making it suitable for applications where vibration and noise reduction are important.
9. Cost-Effectiveness:
- Ductile iron casting is generally more cost-effective than many other materials, such as steel or some non-ferrous alloys, making it an attractive choice for various applications.
It’s important to note that the specific material characteristics of ductile iron casting can be influenced by factors such as alloying elements, casting process parameters, and heat treatment. Different grades of ductile iron casting is designed to emphasize specific properties, allowing for customization based on the requirements of different applications.
Chapter 3: The Manufacturing Process of Ductile Iron Casting
The manufacturing process of ductile iron castings involves several key steps, each of which plays a crucial role in determining the properties and microstructure of the final product. Here’s an overview of the process:
1. Melting:
- Raw materials, including iron scrap, pig iron, and alloying elements, are charged into a melting furnace.
- The materials are heated to the desired temperature, typically above the melting point of iron.
- Alloying elements, such as magnesium for nodularization, are added to achieve the desired composition.
2. Treatment and Inoculation:
- Alloying elements, such as magnesium, are added to promote the formation of nodular graphite during the solidification process.
- Inoculants may be added to control graphite structure and improve mechanical properties.
3. Casting:
- The molten metal is poured into molds made from sand or other materials.
- The mold is typically designed to form the desired shape of the final casting.
4. Cooling and Solidification:
- The molten metal cools and solidifies inside the mold, forming the desired shape of the casting.
- The cooling rate affects the microstructure and mechanical properties of the ductile iron casting.
5. Shakeout and Cleaning:
- Once the casting has solidified, the mold is removed (shakeout), and the casting is cleaned to remove residual sand and other impurities.
6. Heat Treatment:
- Heat treatment is often used to improve the mechanical properties and microstructure of ductile iron casting.
- Austempering is a common heat treatment method for ductile iron casting. It involves quenching the casting into a bath at a specific temperature range to achieve a bainitic microstructure, which enhances strength and toughness.
- Annealing and normalizing may also be used to relieve stress, refine the microstructure, and improve machinability.
7. Machining and Finishing:
- The casting may undergo machining to achieve precise dimensions and surface finish.
- Additional processes, such as painting, coating, or plating, may be applied for corrosion protection or aesthetic purposes.
8. Inspection and Quality Control:
- The final ductile iron casting is inspected for dimensional accuracy, surface finish, and defects.
- Non-destructive testing methods, such as ultrasonic testing or X-ray inspection, may be used to detect internal defects.
Factors Affecting Properties and Microstructure:
- Alloy Composition: The specific alloy composition, including the type and amount of alloying elements, greatly influences the properties and microstructure of ductile iron casting.
- Cooling Rate: The cooling rate during solidification affects the size and distribution of graphite nodules and can influence mechanical properties.
- Heat Treatment: Proper heat treatment can refine the microstructure and enhance mechanical properties such as strength, hardness, and toughness.
- Inoculation and Treatment: The addition of inoculants and nodularizing agents controls the graphite structure and influences the material’s mechanical behavior.
- Mold Design and Process Control: Proper mold design and process control ensure consistent cooling and solidification, leading to desired properties.
By carefully controlling these factors and optimizing the manufacturing process, ductile iron castings can be produced with a tailored combination of mechanical properties and microstructure to meet the specific requirements of various applications.
Chapter 4: Heat Treatment Methods for Ductile Iron Casting
Heat treatment plays a significant role in enhancing the properties and microstructure of ductile iron casting. Different heat treatment methods can be employed to achieve specific goals. Here are some common heat treatment methods used for ductile iron casting:
1. Austempering:
- Process: The casting is quenched from the austenitizing temperature to a specific range within the bainite transformation region. It is then held at this temperature until the desired microstructure is obtained.
- Effect: Austempering produces a bainitic microstructure with improved mechanical properties, including high strength, toughness, and wear resistance. The resulting structure contains nodular graphite and bainite, which contribute to its unique combination of properties.
2. Annealing:
- Process: The casting is heated to a specific temperature and then slowly cooled in a controlled manner.
- Effect: Annealing relieves internal stresses, refines the microstructure, and improves machinability. It can also reduce hardness and increase ductility.
3. Normalizing:
- Process: The casting is heated to a temperature slightly above the austenitizing temperature and then air-cooled.
- Effect: Normalizing produces a finer pearlitic microstructure compared to as-cast conditions. It enhances mechanical properties and improves machinability.
4. Tempering:
- Process: Tempering involves reheating a previously quenched and hardened casting to a temperature below the critical point and then air-cooling.
- Effect: Tempering reduces the hardness and brittleness of the material, while maintaining desirable levels of strength and toughness. It can help relieve residual stresses generated during quenching.
5. Stress Relief Annealing:
- Process: The casting is heated to a temperature below the transformation range and then slowly cooled.
- Effect: Stress relief annealing reduces internal stresses and can improve dimensional stability. It is often used to alleviate stress after machining.
6. Solution Annealing:
- Process: Solution annealing involves heating the casting to a high temperature, typically above the critical temperature, followed by rapid quenching.
- Effect: Solution annealing is used to dissolve carbides and other phases, resulting in a homogenized microstructure. It can improve the castability and machinability of the material.
7. Sub-Critical Annealing:
- Process: The casting is heated to a temperature below the transformation range and held for an extended period before cooling.
- Effect: Sub-critical annealing can refine the microstructure and improve machinability. It is often used to improve certain mechanical properties without significantly affecting others.
The choice of heat treatment method depends on the desired combination of properties for a specific application. Proper heat treatment can tailor the microstructure of ductile iron to achieve the required strength, toughness, hardness, wear resistance, and other mechanical characteristics.
Chapter 5: The Surface Treatment Methods for Ductile Iron Casting
Surface treatment methods for ductile iron castings are employed to improve material properties, enhance corrosion resistance, extend service life, and achieve specific functional or aesthetic requirements. Here are some common surface treatment methods for ductile iron castings:
1. Painting and Coating:
- Process: Applying paint or protective coatings to the surface of the casting.
- Effect: Painting and coating provide a barrier against corrosion, abrasion, and environmental factors. Different types of coatings, such as epoxy, polyurethane, or zinc-rich coatings, can be chosen based on the application.
2. Galvanizing:
- Process: Immersing the casting in a bath of molten zinc, forming a zinc coating on the surface through a metallurgical reaction.
- Effect: Galvanizing provides excellent corrosion resistance and can protect the ductile iron casting from environmental exposure. It is commonly used in outdoor applications.
3. Electroplating:
- Process: Depositing a layer of metal, such as chromium, nickel, or zinc, onto the casting’s surface through an electrolytic process.
- Effect: Electroplating enhances corrosion resistance, wear resistance, and aesthetic appearance. It can provide a thin, uniform, and controlled coating.
4. Powder Coating:
- Process: Applying a dry powder coating to the surface of the casting, followed by curing in an oven.
- Effect: Powder coating offers a durable and attractive finish that resists chipping, scratching, and fading. It provides corrosion protection and can be applied in various colors and textures.
5. Thermal Spray Coating:
- Process: Spraying molten or semi-molten materials onto the casting’s surface, creating a coating.
- Effect: Thermal spray coatings improve wear resistance, thermal insulation, and corrosion resistance. Various materials, such as ceramics, metals, and polymers, can be used for different applications.
6. Anodizing:
- Process: Electrochemically treating the casting’s surface to create an oxide layer, typically using sulfuric acid.
- Effect: Anodizing enhances corrosion resistance and can improve adhesion for subsequent coatings or paint. It can also provide decorative finishes in different colors.
7. Passivation:
- Process: Treating the surface with an acid solution to remove contaminants and promote the formation of a protective passive oxide layer.
- Effect: Passivation improves the corrosion resistance of the casting’s surface and can be particularly effective for stainless ductile iron casting.
8. Shot Peening:
- Process: Bombarding the casting’s surface with small metallic or ceramic particles (shot) to induce compressive stresses and improve fatigue resistance.
- Effect: Shot peening enhances surface hardness, reduces stress concentrations, and increases the service life of the casting.
The choice of surface treatment method depends on factors such as the intended application, environmental conditions, required properties, and aesthetic considerations. Proper surface treatment can significantly extend the service life and performance of ductile iron castings in various industries and applications.
Chapter 6: The Microstructure and Structure of Ductile Iron Casting
The microstructure of ductile iron casting consists of several key components, including spherical graphite, matrix phase, and potential second phases. Each of these components plays a significant role in determining the material properties of ductile iron casting, including strength, fracture toughness, and wear resistance. Here’s an overview of their impact:
1. Spherical Graphite (Nodules):
- Morphology: Spherical graphite nodules are small, rounded particles of graphite dispersed within the iron matrix.
- Impact on Properties:
- Strength: Spherical graphite nodules act as crack arresters, preventing the propagation of cracks and enhancing the material’s strength. The nodules reduce stress concentrations and improve load-bearing capacity.
- Fracture Toughness: The presence of nodular graphite improves fracture toughness by allowing energy absorption through the deflection and branching of cracks.
- Ductility and Toughness: The nodules contribute to the ductility and toughness of ductile iron casting, making it more resistant to brittle fracture compared to gray iron.
- Wear Resistance: Nodules can help reduce wear by enhancing the ability of the material to deform plastically and dissipate energy during abrasive contact.
2. Matrix Phase:
- Composition: The matrix phase in ductile iron casting is primarily ferrite and pearlite, with small amounts of other phases depending on alloy composition and heat treatment.
- Impact on Properties:
- Strength: The matrix phase contributes to the overall strength of the material. The presence of pearlite can enhance strength, while ferrite provides good ductility.
- Fracture Toughness: The matrix’s composition and microstructure influence the fracture toughness of ductile iron casting. A well-balanced matrix contributes to improved toughness.
- Wear Resistance: The matrix phase affects wear resistance, with pearlitic microstructures often exhibiting better wear properties due to their hardness and fine lamellar structure.
3. Possible Second Phases:
- Examples: Possible second phases in ductile iron casting may include carbides, intermetallic compounds, or other inclusions.
- Impact on Properties:
- Strength: Depending on their type, distribution, and size, second phases can influence the strength of the material. Hard second phases like carbides can contribute to increased hardness and strength.
- Fracture Toughness: Second phases can act as stress concentrators and reduce fracture toughness if they are large or present in high concentrations.
- Wear Resistance: Hard second phases can improve wear resistance by providing a harder surface that resists abrasion.
The microstructure of ductile iron casting, particularly the presence of spherical graphite nodules, the composition of the matrix phase, and any potential second phases, significantly impact its material properties. The presence of nodules enhances strength, fracture toughness, and wear resistance by providing crack-arresting mechanisms and energy absorption capabilities. The matrix phase contributes to overall strength, toughness, and wear resistance, while the influence of second phases varies depending on their nature and distribution. The combination of these microstructural components allows ductile iron casting to exhibit a favorable balance of mechanical properties for a wide range of applications.
Chapter 7: The Mechanical Properties of Ductile Iron Casting
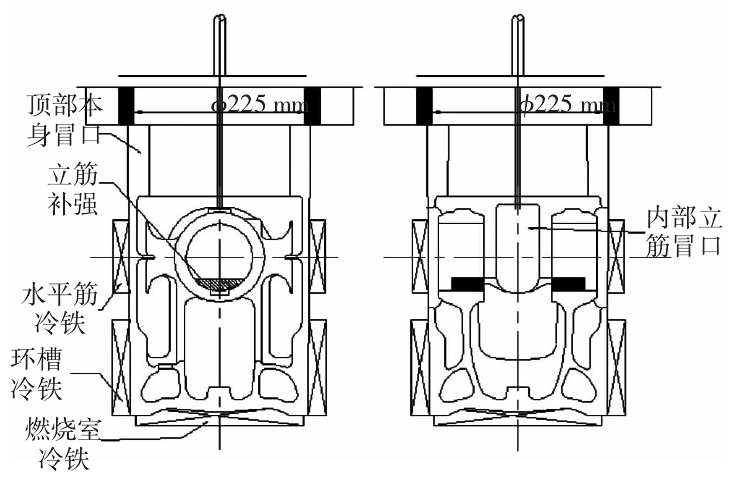
The mechanical properties of ductile iron casting is critical in determining the performance and suitability of castings for various practical applications. Here’s an explanation of these key mechanical properties:
1. Tensile Strength:
- Tensile strength is the maximum amount of tensile (pulling) stress that a material can endure without breaking.
- In ductile iron casting, the presence of spherical graphite nodules enhances tensile strength compared to gray iron.
- Tensile strength is a measure of the material’s ability to withstand external loads and is crucial in structural applications.
2. Yield Strength:
- Yield strength is the amount of stress a material can withstand before it starts to undergo permanent deformation (plastic deformation).
- It is an indicator of the point at which a material transitions from elastic behavior (reversible deformation) to plastic behavior (permanent deformation).
- Yield strength is important in determining the maximum load a casting can support without undergoing permanent deformation.
3. Elongation:
- Elongation measures the ability of a material to deform plastically before breaking.
- It is expressed as a percentage increase in length after fracture compared to the original length.
- Higher elongation indicates greater ductility, which is desirable in applications where materials need to absorb energy through deformation before fracture.
4. Impact Toughness:
- Impact toughness (also known as Charpy or Izod toughness) measures a material’s ability to absorb energy under impact loading conditions.
- It is crucial in applications where sudden impact or dynamic loading is expected, as a higher impact toughness indicates better resistance to brittle fracture.
5. Hardness:
- Hardness measures a material’s resistance to indentation or scratching.
- Hardness is an important indicator of wear resistance and can influence the material’s ability to withstand abrasive or erosive conditions.
6. Fatigue Strength:
- Fatigue strength is the maximum stress a material can withstand for a specified number of loading cycles without failure.
- It is particularly important in applications involving cyclic or repeated loading, such as rotating machinery components.
7. Creep Resistance:
- Creep resistance measures a material’s ability to resist deformation over time when subjected to constant stress at elevated temperatures.
- It is important in applications where castings are exposed to high temperatures and sustained loads.
8. Modulus of Elasticity (Young’s Modulus):
- The modulus of elasticity represents a material’s stiffness and its ability to return to its original shape after deformation.
- It influences how a material responds to applied loads and is important in engineering calculations and designs.
These mechanical properties collectively determine the performance, reliability, and safety of ductile iron castings in real-world applications. The specific combination of properties required depends on the intended use of the casting and the environmental and loading conditions it will encounter.
Chapter 8: The Damage and Failure Mode of Ductile Iron Casting
Ductile iron castings can experience various types of damage and failure modes due to factors such as design flaws, manufacturing defects, material properties, and operational conditions. Some common failure modes include:
- Cracks and Fractures:
- Cause: Cracks can result from casting defects, residual stresses, improper cooling rates, or mechanical overloading. Fractures may occur due to excessive stress concentration.
- Prevention: Proper design, stress analysis, controlled cooling, and attention to casting defects during manufacturing can help prevent cracks and fractures. Enhancing ductility through proper heat treatment can also mitigate the risk.
- Fatigue Failure:
- Cause: Cyclic loading over time can lead to fatigue failure, resulting from the propagation of small cracks until catastrophic failure occurs.
- Prevention: Design components to withstand anticipated cyclic loading, conduct fatigue analysis, avoid stress concentrations, and ensure proper material selection.
- Corrosion and Oxidation:
- Cause: Exposure to corrosive environments or high temperatures can lead to material degradation, weakening the casting’s structural integrity.
- Prevention: Choose appropriate coatings, surface treatments, or materials with better corrosion resistance for the specific environment. Regular inspection and maintenance are essential.
- Wear and Abrasion:
- Cause: Repeated contact with abrasive surfaces can cause material loss and dimensional changes in the casting.
- Prevention: Select materials with higher wear resistance, apply protective coatings, and ensure proper lubrication in moving parts.
- Brittle Fracture:
- Cause: Sudden, brittle fractures can occur due to low-temperature exposure, inadequate heat treatment, or poor microstructure.
- Prevention: Optimize heat treatment processes to achieve the desired microstructure, design components to prevent stress concentration, and ensure proper material selection for low-temperature applications.
Conducting Failure Analysis:
- Visual Inspection: Examine the failed casting to identify the fracture surface, crack initiation point, and propagation pattern. Look for signs of casting defects, inclusions, or stress concentrations.
- Microstructural Analysis: Analyze the microstructure of the failed component using metallography and scanning electron microscopy (SEM) to identify any anomalies or improper heat treatment.
- Chemical Analysis: Conduct chemical composition analysis to ensure the material meets specifications and identify any impurities that may have contributed to the failure.
- Mechanical Testing: Perform mechanical testing, such as hardness testing, tensile testing, and impact testing, to assess the mechanical properties of the casting and determine if they meet design requirements.
- Finite Element Analysis (FEA): Use FEA to simulate the loading conditions and stress distribution in the casting, identifying areas of high stress or potential failure.
- Environmental Analysis: Consider the environment in which the casting operated, including temperature, humidity, corrosive agents, and other external factors that may have contributed to the failure.
- Review of Manufacturing Processes: Evaluate the casting process, including mold design, pouring practices, heat treatment, and quality control measures, to identify potential issues.
- Operational Conditions: Consider the loading, temperature, and operational conditions the casting experienced to determine if they exceeded design limits.
By conducting a comprehensive failure analysis, you can pinpoint the root causes of ductile iron casting failures and implement corrective actions to prevent similar issues in the future. This involves a multidisciplinary approach that considers material science, engineering principles, and operational factors.
Chapter 9: Relevant Standards and Specifications for Ductile Iron Casting Materials
Ductile iron casting materials are subject to various international and industry standards that ensure consistency, quality, and compliance in production and use. Here are some of the relevant standards and specifications for ductile iron casting materials:
1. International Standards:
- ISO 1083: Foundry machinery and equipment – Terminology
- ISO 1084: Foundry machinery and equipment – Symbols for process charts and process measures
- ISO 17834: Foundry – Test piece and test procedure for moulding and core sand in chemically bonded moulds
- ISO 185: Grey cast iron and malleable cast iron – Determination of graphite content – Micrographic method using alkaline etching
- ISO 2531: Ductile iron pipes, fittings, accessories and their joints for water or gas applications
- ISO 7186: Foundry – Liquid penetrant inspection
- ISO 80000-8: Quantities and units – Part 8: Acoustics
- ISO 8044: Corrosion of metals and alloys – Basic terms and definitions
- ISO 1084: Foundry machinery and equipment – Symbols for process charts and process measures
- ISO 1084: Foundry machinery and equipment – Symbols for process charts and process measures
2. Industry Standards:
- ASTM A536: Standard Specification for Ductile Iron Castings
- ASTM A395: Standard Specification for Ferritic Ductile Iron Pressure-Retaining Castings for Use at Elevated Temperatures
- ASTM A897: Standard Specification for Austempered Ductile Iron Castings
- EN 1563: Founding – Spheroidal graphite cast iron
- BS EN 124: Gully tops and manhole tops for vehicular and pedestrian areas. Design requirements, type testing, marking, quality control
- JIS G5502: Ductile iron castings
These standards cover a wide range of aspects, including material composition, mechanical properties, testing methods, manufacturing processes, quality control, and more. They provide guidelines and specifications that help ensure the consistent production, performance, and safety of ductile iron castings in various applications.
When working with ductile iron casting materials, it’s essential to refer to the appropriate standards and specifications to ensure that your castings meet the required quality and performance criteria. Compliance with these standards helps maintain consistency, reliability, and compatibility across different suppliers, manufacturers, and users within the industry.
Chapter 10: The Application of Ductile Iron Casting in Different Fields
Ductile iron casting finds widespread applications in various fields due to its unique combination of mechanical properties, cost-effectiveness, and versatility. Different application scenarios indeed have distinct requirements for material properties. Here are some examples of how ductile iron castings are used in different industries:
1. Automotive Manufacturing:
- Applications: Engine blocks, cylinder heads, crankshafts, suspension components, transmission housings, brake components, steering knuckles.
- Requirements: Ductile iron’s high strength and good machinability make it suitable for critical automotive components that require both durability and ease of manufacturing.
2. Mechanical Engineering:
- Applications: Machine frames, gears, pulleys, brackets, pump bodies, valve components, couplings.
- Requirements: Ductile iron’s excellent mechanical properties, including high tensile strength and toughness, make it ideal for a wide range of mechanical components subjected to varying loads and dynamic conditions.
3. Construction and Infrastructure:
- Applications: Manhole covers, drainage grates, pipe fittings, bridge components, building structural elements.
- Requirements: Ductile iron’s durability, corrosion resistance, and ability to handle heavy loads make it suitable for construction materials that need to withstand harsh environmental conditions and support structural integrity.
4. Agriculture and Heavy Machinery:
- Applications: Tractor parts, plow components, tillage equipment, gearboxes, couplings.
- Requirements: Ductile iron’s robustness and ability to handle high loads make it a suitable choice for agricultural machinery and heavy equipment used in demanding conditions.
5. Energy and Power Generation:
- Applications: Wind turbine hubs, turbine housings, pump casings, power transmission components.
- Requirements: Ductile iron’s strength and resistance to wear and corrosion make it suitable for components used in energy generation and transmission systems.
6. Rail and Transportation:
- Applications: Railway components, couplers, brake systems, suspension parts, cast iron wheels.
- Requirements: Ductile iron’s ability to withstand impact and dynamic loading is valuable in the rail and transportation industry where safety and reliability are paramount.
7. Water and Wastewater Management:
- Applications: Pipe fittings, valves, pumps, hydrants, manhole covers, water treatment equipment.
- Requirements: Ductile iron’s corrosion resistance and durability make it well-suited for water and wastewater management systems exposed to various chemical and environmental conditions.
8. Marine and Offshore:
- Applications: Ship components, offshore platform structures, marine propulsion systems.
- Requirements: Ductile iron’s resistance to corrosion and ability to withstand harsh marine environments make it suitable for marine applications.
These examples highlight how ductile iron casting serves a wide range of industries by meeting specific requirements for material properties, durability, and performance. The ability to tailor ductile iron’s microstructure and mechanical properties through appropriate heat treatment and alloying further enhances its suitability for various applications.
Chapter 11: The Quality Control of Ductile Iron Casting
Evaluating the quality of ductile iron castings involves a combination of quality control measures and testing methods to ensure that the castings meet desired specifications and performance criteria. Here are some common quality control and testing methods used for evaluating ductile iron castings:
1. Metallographic Microscopy:
- Metallographic microscopy involves examining the microstructure of ductile iron casting using a microscope after preparing polished and etched samples.
- It helps assess the size, distribution, and morphology of graphite nodules, as well as the matrix phase and potential second phases.
- This method provides insights into the casting’s material properties and any microstructural defects that might affect performance.
2. Scanning Electron Microscopy (SEM):
- SEM allows for detailed imaging of the surface and internal microstructure of ductile iron castings at higher magnifications.
- It can reveal features such as fracture surfaces, inclusions, and microstructural anomalies that may impact casting quality and integrity.
3. Hardness Testing:
- Hardness testing involves measuring the resistance of the casting’s surface to indentation or scratching.
- It provides information about the material’s mechanical properties, including its strength and wear resistance.
- Common hardness tests include Brinell, Rockwell, and Vickers hardness tests.
4. Impact Testing:
- Impact testing evaluates the material’s ability to absorb energy under sudden impact loading.
- It assesses the ductile iron casting’s toughness and resistance to brittle fracture.
- Charpy and Izod tests are commonly used impact testing methods.
5. Tensile Testing:
- Tensile testing measures the material’s response to axial loading by pulling a sample until it fractures.
- It provides data on properties such as tensile strength, yield strength, and elongation.
- Tensile testing helps ensure the casting’s ability to withstand mechanical loads.
6. Dimensional Inspection:
- Dimensional inspection involves measuring the casting’s dimensions and geometrical features against design specifications.
- This ensures that the casting meets the required size, shape, and tolerances.
7. Non-Destructive Testing (NDT):
- NDT methods, such as ultrasonic testing, X-ray inspection, and magnetic particle testing, can detect internal defects and irregularities without damaging the casting.
- NDT is valuable for identifying hidden flaws that might affect casting performance.
8. Chemical Composition Analysis:
- Chemical analysis verifies the composition of the ductile iron casting, ensuring that it meets required specifications for alloying elements and impurities.
- Spectroscopy techniques like optical emission spectroscopy (OES) and energy-dispersive X-ray spectroscopy (EDS) are commonly used.
9. Visual Inspection:
- Visual inspection involves examining the casting’s surface for defects, irregularities, or signs of poor workmanship.
- It is a fundamental and cost-effective method for detecting visible flaws.
Effective quality control and testing methods help ensure that ductile iron castings are produced to high standards, meet performance requirements, and are free from defects that could compromise their functionality and durability.
Chapter 12: The Environmental Performance of Ductile Iron Casting Materials
Ductile iron casting materials offer several environmental advantages due to their recyclability, reusability, and other inherent properties. Here are some key points highlighting their environmental performance and advantages compared to other materials:
1. Recyclability:
- Ductile iron castings are highly recyclable. They can be melted down and reused as raw material in new casting production without significant loss of material properties.
- The recycling process for ductile iron casting is energy-efficient and reduces the demand for primary raw materials, contributing to resource conservation and minimizing environmental impact.
2. Reusability:
- Ductile iron castings can often be refurbished or repaired, extending their service life and reducing the need for new manufacturing.
- Components that have reached the end of their original service life can be repurposed or melted down for recycling.
3. Energy Efficiency:
- Ductile iron castings require less energy in their production compared to some other materials like steel or aluminum.
- Lower production energy requirements translate to reduced greenhouse gas emissions and a smaller carbon footprint.
4. Durability and Longevity:
- Ductile iron’s strength, wear resistance, and corrosion resistance contribute to the longevity of castings.
- Longer service life reduces the frequency of replacement, conserving resources and reducing waste generation.
5. Reduced Waste Generation:
- Ductile iron casting processes often generate less waste compared to other manufacturing methods, as excess material can be recycled or reused.
6. Compatibility with Sustainable Practices:
- Ductile iron castings are commonly used in applications related to renewable energy, such as wind turbine hubs and water management systems, aligning with sustainable technologies.
7. Low Toxicity:
- Ductile iron casting materials have low toxicity and do not release harmful chemicals during production, use, or disposal.
8. Reduced Need for Virgin Resources:
- The ability to recycle ductile iron casting reduces the demand for virgin raw materials, which can help conserve natural resources and reduce the environmental impact of mining and extraction.
9. Localized Production:
- Ductile iron castings are often produced locally, reducing the energy and emissions associated with transportation.
10. Comparative Advantages:
- Compared to materials like plastics, ductile iron casting has a lower environmental impact and can withstand harsher conditions.
- When compared to some alternative metals, such as aluminum or titanium, ductile iron casting can offer comparable strength and performance with a potentially smaller environmental footprint.
While ductile iron casting materials offer several environmental advantages, it’s important to consider specific applications and local conditions when assessing their overall sustainability. Proper recycling, efficient manufacturing practices, and responsible end-of-life management further enhance the environmental performance of ductile iron castings.