The influence of different pouring speeds in lost foam casting is shown in the figure. When the pouring speed is 74 mm/s and 104 mm/s respectively, the maximum effective stress is 221 MPa and 202 MPa respectively.
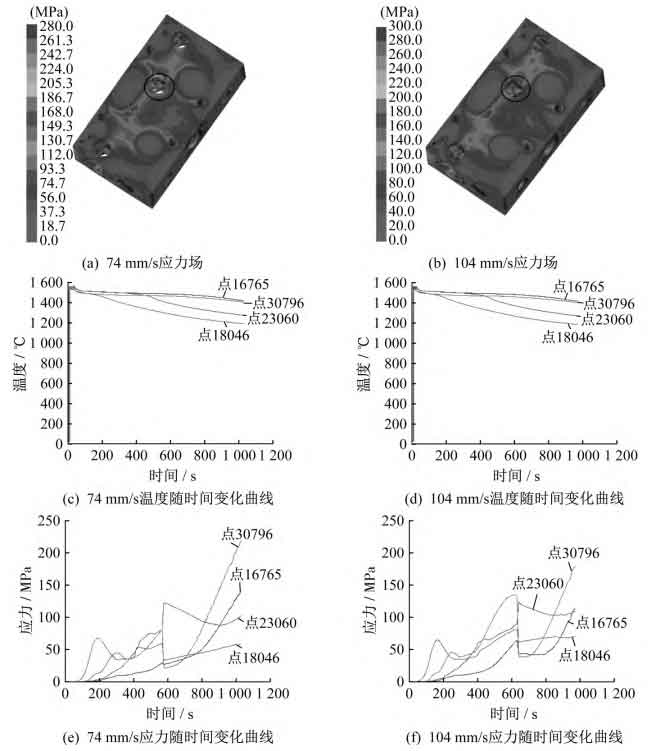
At different pouring speeds, the temperature curve of each point in lost foam casting showed a trend of increasing first and then decreasing. The point near the pouring riser solidified first, and the temperature decreased slowly. The change of stress curve under different pouring speeds at the same node is close, which shows that there will be no complex stress fluctuation when the pouring speed changes. Keeping other conditions unchanged, the simulation calculation shows that when increasing the pouring speed can reduce the increase of stress by MPa, the change trend of the stress curve at the selected points is quite different.
When the vacuum degree is low, the stress fluctuation of point 23060 at the junction of the runner and the lost foam casting and point 30796 near the riser is large within a certain range, which indicates that the vacuum degree has a great impact on the stress. Compared with the simulation results, the stress value at the joint of riser and lost foam casting can be reduced by adopting the process of reducing vacuum degree.