In order to solve the problems of cold shuts and blowholes in pressure casting, the following methods are adopted for adjustment:
1) Modify the mold and set a slag collecting bag (see Figure 1) at the oil plugging position of the die casting parts, which can effectively discharge the cold material, gas, slag and other impurities, and ensure that the quality of the product body meets the standard;
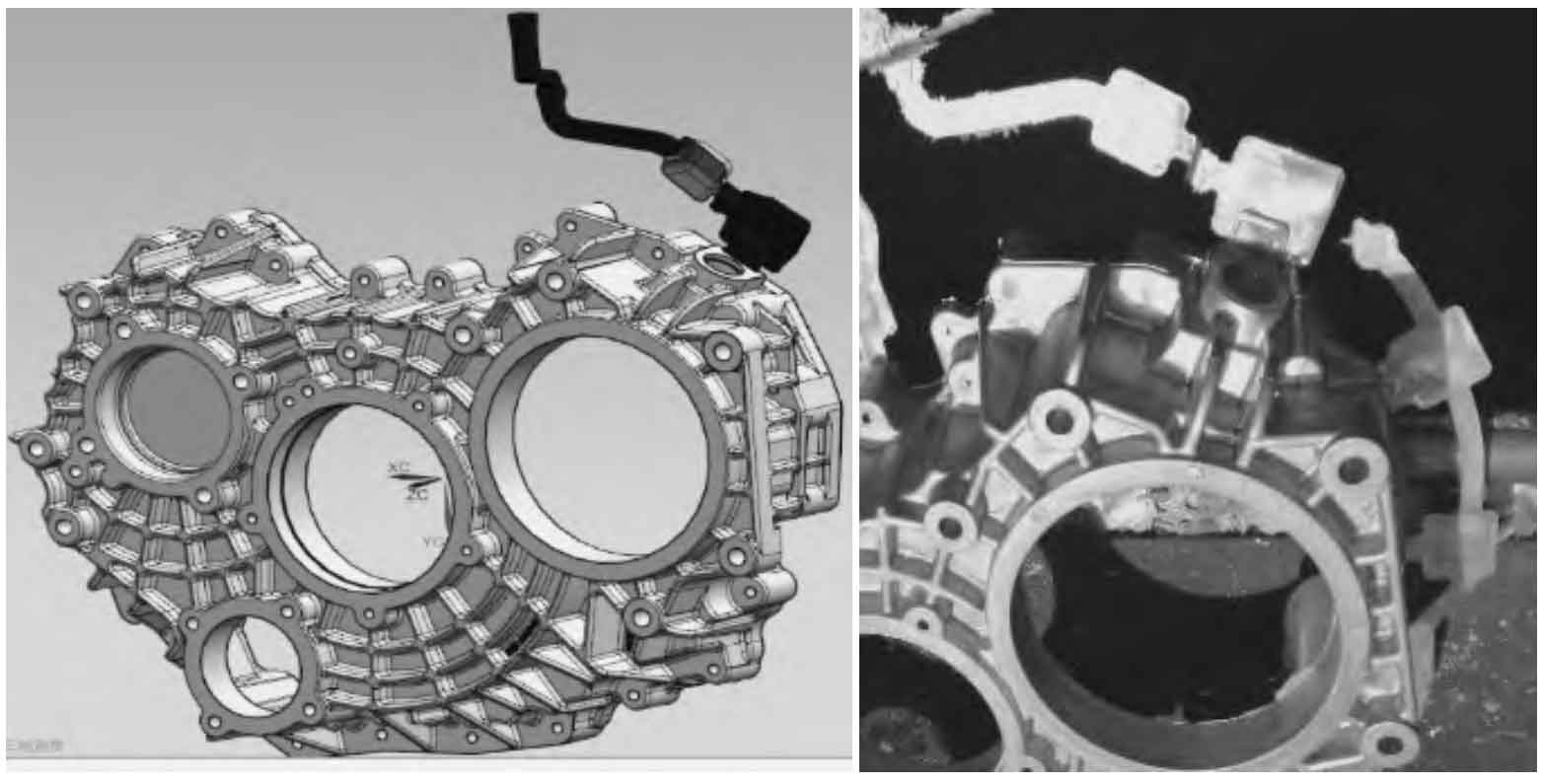
2) Add a mold temperature oil circuit at the mold corresponding to the oil plug hole to keep the mold temperature at about 180 ℃ during continuous production (see Figure 2);
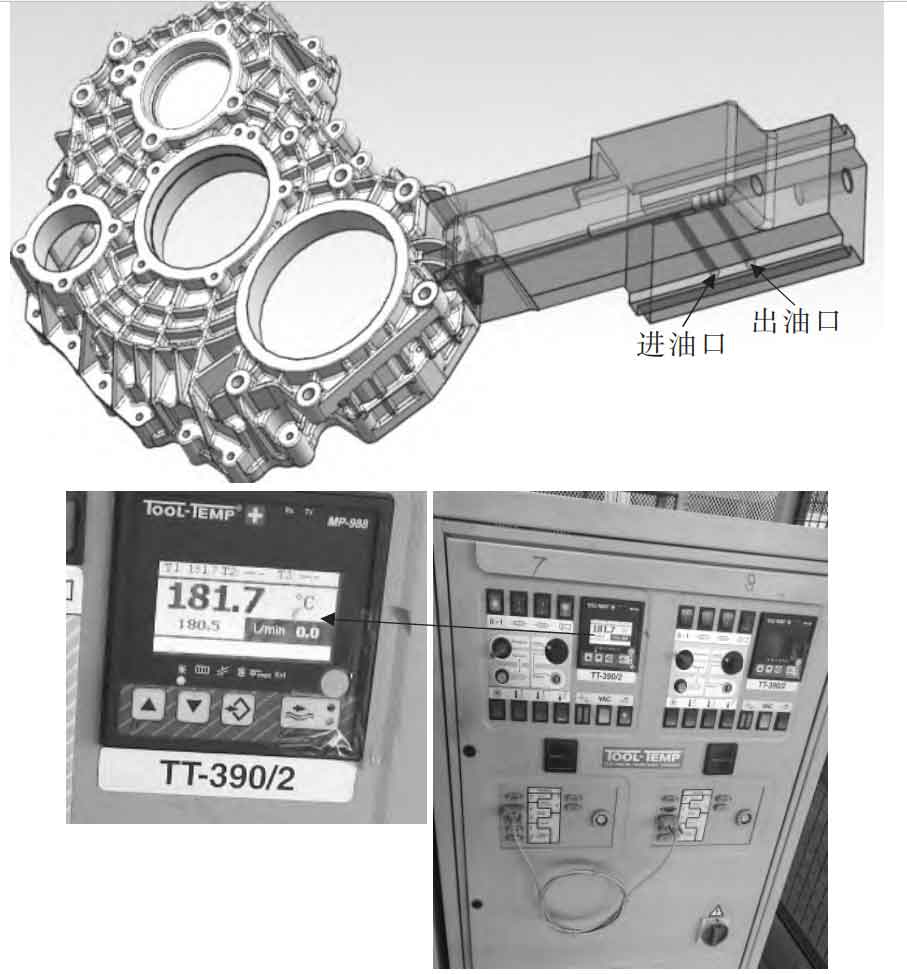
3) Increase the pouring temperature of molten aluminum for die casting parts from 660 ℃ to 670 ℃ to minimize the heat loss of molten aluminum due to the long process;
4) Increase the core temperature of the moving die from 110 ℃ to 180 ℃, increase the fluidity of aluminum liquid and reduce the heat loss;
5) The MAGMA software is used to simulate and set the auxiliary runner to shift the filling end position to the non-important area of the die casting (see Figure 3). The filling process of molten aluminum was simulated by MAGMA, and it was found that adding auxiliary runner could not shift the filling end to the non-important area.
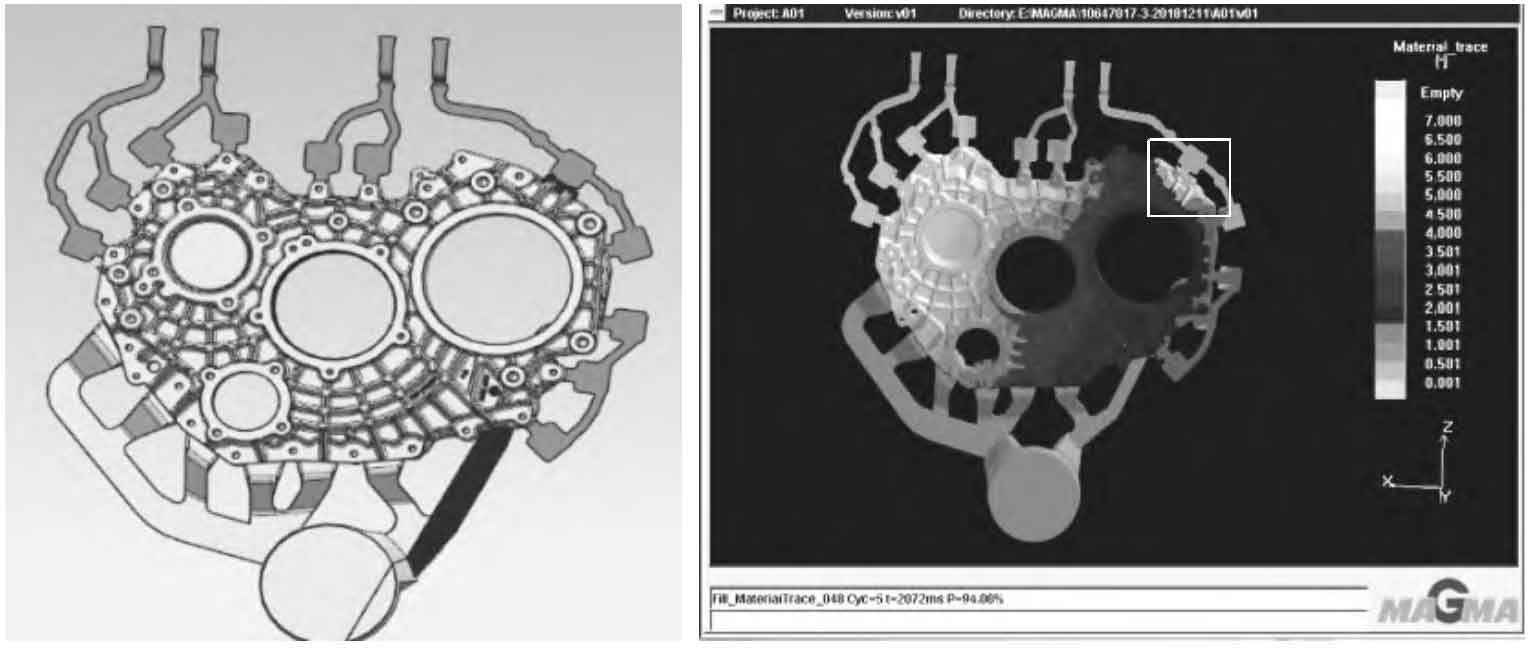
The optimized process was used for small batch production verification of gearbox rear cover shell die casting, and the product qualification rate reached 98.2%. Figure 4 shows the die castings produced after the improved process. It can be seen from Figure 4 that the defects at the oil plugging hole of the product have been effectively improved.
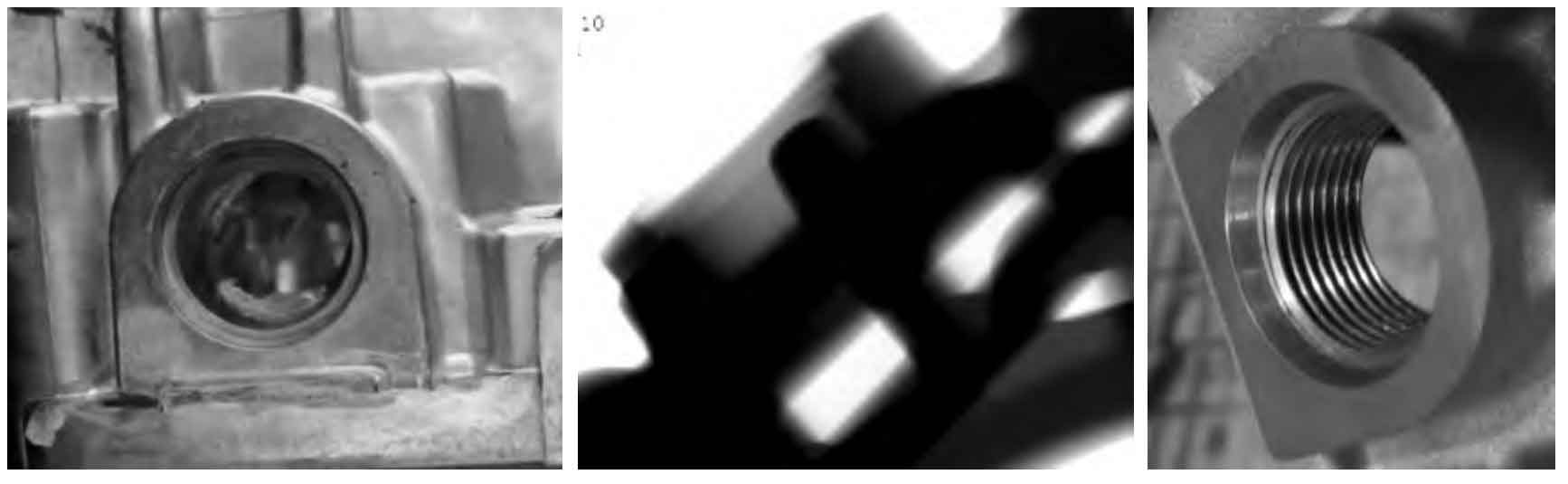