Pressure casting molding is an advanced and efficient casting molding method, which is widely used in automobile, communication, household appliances and other fields. In recent years, with the vigorous development and attention of energy conservation and emission reduction and product lightweight technology in the world, pressure casting parts have been paid attention to because of their thin, lightweight and durable wall in line with the concept of lightweight.
Element | Si | Fe | Cu | Mn | Mg | Ni | Zn | Sn | Ti | Cr | Pb | Al |
ADC12 | 9.6~ 12.0 | ≤1.3 | 9.6~ 12.0 | ≤0.5 | ≤0.3 | ≤0.5 | ≤1.0 | ≤0.2 | – | – | – | Allowance |
The gearbox studied is a high-performance all-aluminum alloy gearbox developed for high-end heavy truck models, with aluminum alloy die-casting shell. Due to its complex structure and novel design, the rear cover shell is prone to cold shut and air hole defects at the oil plug hole of the product during the production process, which exceeds the enterprise standard. In this paper, MAGMA software is used to simulate and analyze the shell structure, select the best pressure casting process to solve the product defects, and provide reference for later production of the same type of products.
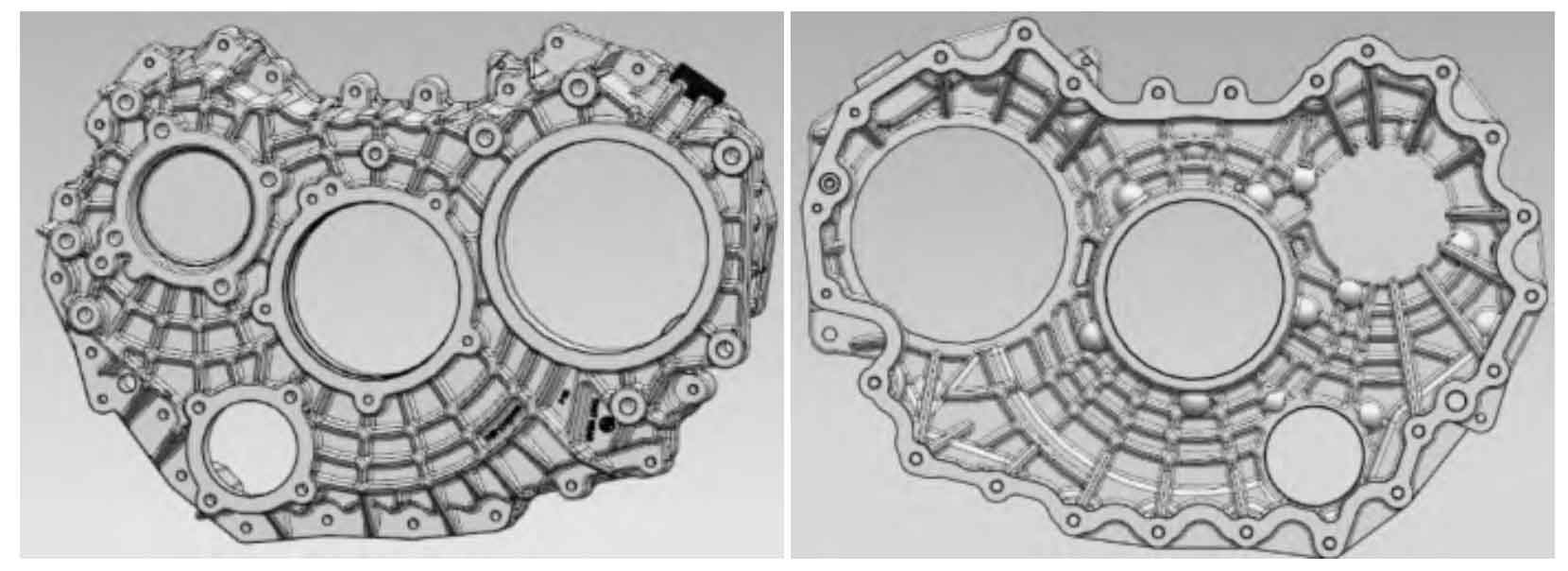
See the table for the chemical composition requirements of ADC12 pressure castings in JIS H5302: 2000.
The pressure casting of the rear cover housing is an important part of the heavy truck gearbox. The structure of the pressure casting is shown in the figure. Its overall dimension is 578 mm × 417 mm × 98 mm, weight about 9.5 kg, average wall thickness 7 mm. The pressure casting has complex structure, high air-tightness requirements, large local size thickness, and large wall thickness variation, which is easy to form cold shut and air hole defects locally.
1) The cold shut and blowhole defects at the oil plugging hole of pressure casting parts are formed due to the accumulation of cold material, gas and slag in the product. The design of slag collecting ladle at this part can effectively remove the cold shut and blowhole defects;
2) The oil plugging hole is located at the end of the pressure casting process. The temperature loss of aluminum liquid during mold filling is too large, which is easy to produce cold shut and air hole defects. Adding mold temperature system in this area can effectively remove the defects;
3) Before mold design, it is necessary to consider the possible defects of cold material, gas, slag and other defects at the far end, consider reserving the mold temperature oil interface, and reserving the slag bag to facilitate rapid change during mold test, so as to avoid causing a sharp increase in cost, delay in production, and even delivery time;
4) During the design of pressure casting parts, it is necessary to review in advance, and consider the approximate position of pouring row in advance to avoid placing some important parts at the filling end, which will affect the quality of pressure casting parts;
5) Applying the above 1), 2), 3) and 4) process methods to other transmission case pressure castings can also effectively remove the remote cold shut and air hole defects of the pressure castings.