The production difficulty of impeller mainly lies in the whole molding process. Using traditional casting technology, it is difficult to obtain the whole sand core with wood mold or metal mold. In order to improve the production efficiency, a new casting process must be adopted. At present, the main methods used to produce complex shape castings are investment casting and lost foam casting.
(a) Investment casting
Die casting is also called investment casting. This method is to use fusible materials to make a precise and clean pattern – wax mold, to coat the wax mold with multi-layer refractories, or to pour high temperature resistant ceramic slurry, and then to form the mold after hardening and drying. Then the wax mould is melted and flowed out, and the molten liquid metal is poured into the roasted mould. The liquid metal is cooled and solidified in the mould and becomes a precise and smooth casting.
Investment casting has many advantages: high dimensional accuracy and small surface roughness; it can cast thin-walled castings and castings with small weight; more importantly, investment casting can produce castings with complex shapes. The shape and cavity shape of investment casting are almost unlimited. It can be used to produce complex parts which are difficult to be manufactured by sand casting, forging, cutting and other methods.
But investment casting has its own shortcomings. Due to the limitation of the strength of the shell, investment casting can not produce large castings. The maximum diameter of impeller is Φ 820mm, the height is 425mm, and the net weight of single piece is 478kg. The strength of investment casting shell can not meet the requirements, and the time of making mold will be greatly extended. Therefore, investment casting is not suitable for the production of such desulfurization pump impeller.
(b) Lost foam casting
Lost Foam Casting (LFC) or expendable pattern casting (EPC) is a new casting method that combines the foam model with the size and shape of the casting into a model cluster, brushing the refractory coating and drying it, and embedding it in the dry sand for vibration modeling, pouring under normal pressure or negative pressure, making the model vaporized, the liquid metal occupying the model position, and solidifying and cooling to form the casting.
Lost foam casting has the following advantages: accurate size and shape, high surface finish, with the characteristics of precision casting; it provides sufficient freedom for the structural design of the casting. The components originally processed and assembled by multiple parts can be cast as a whole through the method of piecewise casting and then bonding after adopting lost foam casting process.
However, the unique disadvantage of lost foam casting is that the flow front of molten metal is the pyrolysis product (gas and liquid) of the foam pattern. It will react with the metal liquid and affect the filling of the metal liquid. If the pyrolysis products can not be discharged smoothly during the filling process, it is easy to cause defects such as porosity, wrinkling and carbon carburization. The impeller of desulfurization pump is made of high alloy steel. If the lost foam casting process is adopted as a whole, on the one hand, the fluidity of high alloy steel is poor, and it is easy to produce defects such as insufficient pouring and cold insulation; on the other hand, the surface carburization will greatly weaken the mechanical properties and corrosion resistance of the impeller.
(c) Composite process
Whether it is sand casting, investment casting or lost foam casting, it has its own advantages and its own insurmountable defects. Therefore, the composite process can take advantage of the advantages of various processes, produce castings faster and better, and achieve the effect of learning from each other.
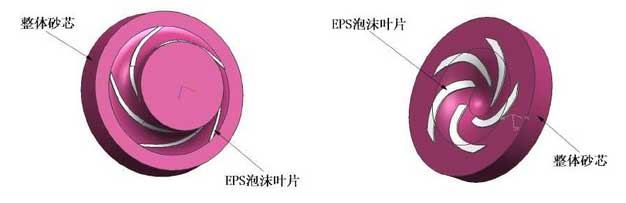
Through the analysis and Research on the structural and technological characteristics of this kind of impeller casting as well as the advantages and disadvantages of sand casting, investment casting and EPC process, it is found that if the blades of this kind of impeller are not taken out during the molding, and after the completion of the whole sand core, the method of EPC and investment casting is used to make the impeller part form a cavity, so that a complete sand core can be formed. Finally, according to the The traditional process of closed box pouring. This process can not only use the original tooling equipment and pouring process, but also improve the labor efficiency and casting accuracy, greatly saving the cost of process improvement.
The blades used in molding can be made of foam or investment pattern. The blade manufactured by investment casting has high precision and low surface roughness, but the production process of investment casting is complicated. Generally, the manufacturing cycle of the shell is more than 7 days, and the cost is high, so it is not suitable. The lost foam foam blade is simple, low cost and high precision. The combined sand core and EPS foam blades are shown in the diagram.