Ductile iron casting, also known as nodular iron casting or spheroidal graphite iron casting, has seen significant advancements and innovations that have expanded its possibilities and improved its performance in various applications. Here are some notable advancements in ductile iron casting:
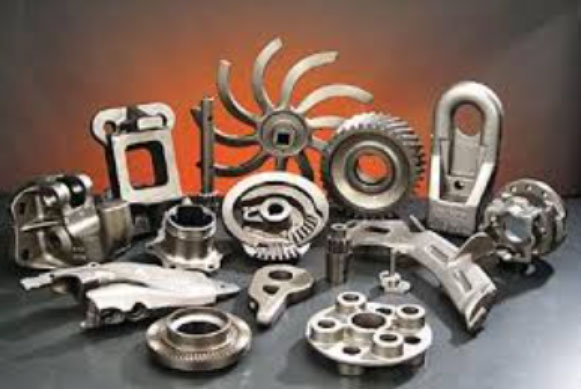
1. Alloying and Heat Treatment: Advances in alloying techniques and heat treatment processes have led to the development of high-performance ductile iron grades with enhanced properties. Alloying elements such as chromium, molybdenum, and nickel can be added to improve strength, corrosion resistance, and wear resistance. Heat treatment processes like quenching and tempering can further optimize the microstructure and mechanical properties of ductile iron components.
2. Thin-Wall Casting: Innovations in casting technologies have enabled the production of thin-walled ductile iron castings with complex geometries. Thin-wall casting techniques, such as lost foam casting and precision sand casting, allow for the creation of lightweight yet strong components. This advancement has expanded the use of ductile iron in applications where weight reduction and intricate designs are crucial, such as automotive components.
3. Improved Casting Processes: Advancements in casting processes have led to increased efficiency and improved product quality. Computer simulation software and modeling techniques enable the optimization of casting parameters, reducing the risk of defects and ensuring consistent quality. Automated and robotic systems have also enhanced the precision and repeatability of the casting process, resulting in improved dimensional accuracy and reduced variability.
4. Surface Treatment Technologies: Surface treatment technologies have evolved to enhance the performance and durability of ductile iron components. Processes such as shot blasting, powder coating, and electroplating provide improved corrosion resistance, wear resistance, and aesthetic appeal. These surface treatments extend the lifespan of components and expand their applications in various industries.
5. Non-Destructive Testing (NDT) Techniques: Non-destructive testing techniques have advanced in detecting and evaluating potential defects in ductile iron castings. Techniques such as ultrasound, magnetic particle inspection, and X-ray imaging allow for accurate and efficient inspection of castings, ensuring the integrity and reliability of the components before they are put into service.
6. Sustainable Practices: The ductile iron casting industry has also embraced sustainable practices to minimize environmental impact. Improved process efficiencies, recycling of scrap material, and the use of environmentally friendly molding materials are some of the steps taken to reduce waste generation and energy consumption in ductile iron production.
These advancements in ductile iron casting have expanded its possibilities in terms of strength, durability, complexity, and performance. Engineers and manufacturers now have access to a wider range of ductile iron grades and more efficient casting processes, allowing them to design and produce components that meet stringent performance requirements while optimizing cost and sustainability considerations. The continuous innovation in ductile iron casting is expected to drive further advancements and open up new possibilities in the future.