Sand casting parts, a method used for centuries, has seen numerous innovations in recent years, particularly with advancements in technology and material science. Here are some key innovations in sand casting parts for manufacturing parts:
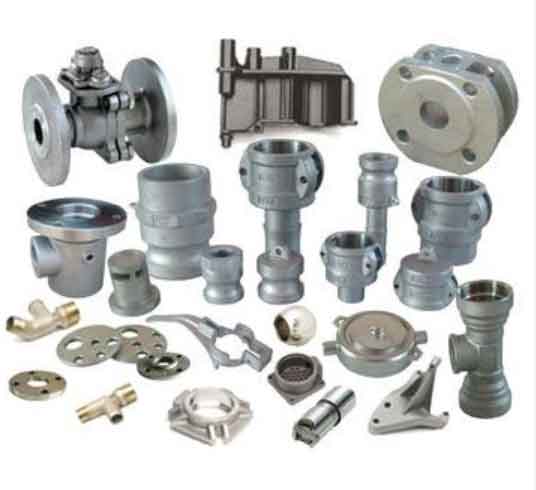
- Digital Sand Printing: This technology, a form of 3D printing, allows for the creation of complex sand molds and cores directly from a digital model. It’s faster than traditional mold-making and allows for greater complexity in design.
- Improved Sand Quality and Binders: Advances in sand quality, such as finer grain sizes and better controlled compositions, have led to improved casting finishes and dimensional accuracy. New binder technologies also enhance mold strength and environmental friendliness.
- Simulation Software: Computer-aided design (CAD) and simulation software now enable precise modeling of the sand casting parts. This technology predicts potential issues like shrinkage or air entrapment, allowing for adjustments before actual casting, saving time and resources.
- Automated Sand Casting: Automation in sand casting parts involves the use of robotics for tasks such as mold making, pouring, and part extraction. This reduces labor costs and increases consistency and quality.
- Environmentally Friendly Practices: There’s a growing focus on making sand casting parts more sustainable. This includes recycling used sand, reducing waste, and employing non-toxic binders.
- Enhanced Quality Control Techniques: The use of X-ray fluorescence (XRF), computed tomography (CT), and other non-destructive testing methods are increasingly common. These techniques allow for thorough inspection of internal structures without damaging the part.
- Customized Alloys: The development of new metal alloys, tailored for specific applications, can be used in sand casting parts to achieve desired properties in the final product, such as increased strength or corrosion resistance.
- Rapid Prototyping Integration: Sand casting parts can be integrated with rapid prototyping techniques to accelerate the design-to-production timeline, making it feasible to produce small batches or custom parts efficiently.
These innovations collectively have expanded the capabilities of sand casting parts, making it more efficient, precise, and environmentally friendly, while also broadening the range of applications in various industries like automotive, aerospace, and construction.