Casting defects can occur in resin sand casting due to various factors, but with proper understanding and preventive measures, most defects can be minimized or eliminated. Let’s explore some common casting defects in resin sand casting and how to prevent them:
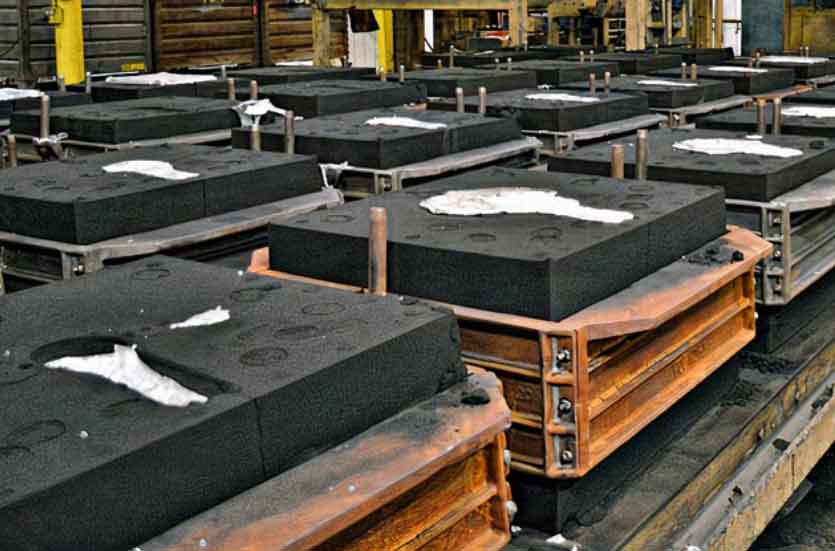
- Blow Holes/Pinholes:
- Defect: Blow holes or pinholes are cavities formed in the casting due to entrapped gases, such as air or water vapor.
- Prevention: Improve mold permeability, ensure proper venting, and use suitable anti-veining agents to reduce gas entrapment. Properly degas the molten metal before pouring to minimize gas content.
- Scabs:
- Defect: Scabs occur when the resin on the mold surface reacts with the molten metal, resulting in raised areas or rough patches on the casting surface.
- Prevention: Use anti-scabbing agents on the mold surface, optimize mold coatings, and control pouring parameters to prevent excessive reaction between the resin and metal.
- Misruns and Cold Shuts:
- Defect: Misruns happen when the metal does not fill the entire mold cavity, leaving voids in the casting. Cold shuts occur when two streams of metal fail to fuse, resulting in a surface defect.
- Prevention: Ensure proper gating and riser design to promote smooth and uniform metal flow, and avoid overly cold metal temperatures during pouring.
- Shrinkage Defects:
- Defect: Shrinkage defects appear as voids or cavities inside the casting due to uneven cooling and solidification of the metal.
- Prevention: Use proper risers and gating systems to feed additional molten metal into the casting as it cools to compensate for shrinkage. Optimize mold design to minimize thermal gradients.
- Hot Tears/Cracks:
- Defect: Hot tears or cracks occur when the casting solidifies and contracts unevenly, leading to internal or external fractures.
- Prevention: Control cooling rate and avoid sudden temperature changes to minimize thermal stresses. Modify the casting design to reduce stress concentration points.
- Metal Inclusions:
- Defect: Metal inclusions are non-metallic contaminants, such as sand particles, that become trapped in the casting during pouring.
- Prevention: Use high-quality sand and minimize sand breakdown during mold filling. Implement proper filtering and metal treatment to remove impurities.
- Rough Surface Finish:
- Defect: A rough surface finish is undesirable and may require additional post-casting machining.
- Prevention: Use finer sand grain size, improve pattern surface quality, and optimize the molding process to achieve a smoother mold surface.
- Dimensional Inaccuracy:
- Defect: Casting dimensions not matching the intended design can lead to rejection.
- Prevention: Ensure accurate pattern dimensions, proper mold compaction, and consistent mold curing conditions to achieve dimensional accuracy.
To prevent casting defects effectively, manufacturers should focus on proper mold design, gating, venting, and metal treatment. Additionally, a comprehensive quality control program, regular inspection, and continuous process improvement are essential for producing high-quality castings consistently in resin sand casting.