Lost foam casting and sand casting are two popular methods used in the metal casting industry. While both techniques are used to produce metal parts, there are significant differences between them in terms of the process, complexity, cost, and the types of parts they can produce. Here’s a comparative analysis of lost foam casting and sand casting:
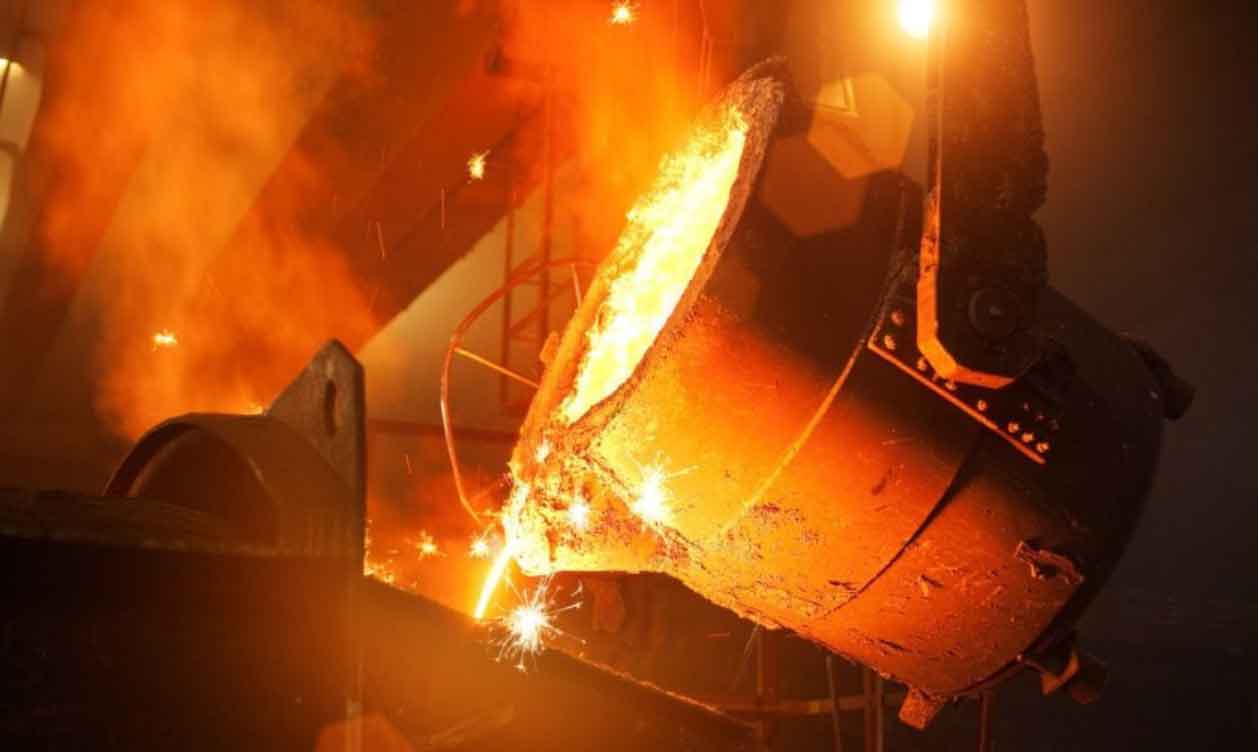
- Process:
- Lost Foam Casting: In lost foam casting, a foam pattern of the desired part is created and coated with a refractory material. The coated foam pattern is then embedded in sand, and molten metal is poured into the mold. The heat of the metal vaporizes the foam, causing it to disappear and leave behind a cavity in the shape of the desired part. The metal fills the void, solidifies, and forms the final part.
- Sand Casting: Sand casting involves creating a mold made of compacted sand mixed with a bonding agent. A pattern of the part is pressed into the sand, removed, and the cavity left behind represents the shape of the part. Molten metal is then poured into the mold, allowed to cool and solidify, and the sand is subsequently removed to reveal the finished part.
- Complexity:
- Lost Foam Casting: Lost foam casting allows for the production of complex and intricate parts with detailed features. The foam patterns can be easily shaped and manipulated, enabling the casting of parts with undercuts, thin walls, and complex geometries.
- Sand Casting: Sand casting is a versatile method but is generally better suited for producing simpler and larger parts with less intricate details. It is more difficult to achieve intricate shapes and fine details with sand casting due to the limitations of the molding process.
- Surface Finish and Tolerance:
- Lost Foam Casting: Lost foam casting generally produces parts with a smooth surface finish and precise dimensions. The refractory coating on the foam pattern helps capture the details of the pattern, resulting in a high-quality surface finish.
- Sand Casting: Sand casting can produce parts with a rougher surface finish compared to lost foam casting. The texture of the sand mold and the potential for sand-related defects can impact the surface finish. Sand casting also tends to have slightly looser tolerances compared to lost foam casting.
- Cost and Tooling:
- Lost Foam Casting: Lost foam casting requires the creation of foam patterns, which can be more expensive and time-consuming compared to the patterns used in sand casting. However, lost foam casting eliminates the need for complex molds and cores, which can offset the initial pattern cost for large production runs.
- Sand Casting: Sand casting is generally more cost-effective for producing low to medium volumes of parts. The patterns used in sand casting are usually made from cheaper materials, such as wood or resin. However, for complex parts that require intricate sand cores, the tooling costs may increase.
- Part Size and Weight:
- Lost Foam Casting: Lost foam casting is well-suited for producing both small and large parts. The foam patterns can be easily scaled up or down to accommodate different part sizes and geometries.
- Sand Casting: Sand casting is commonly used for larger parts, such as engine blocks, large pipes, and heavy machinery components. It can handle larger volumes of metal and is generally more suitable for bulkier parts.
Lost foam casting and sand casting offer different advantages and are used in different scenarios. Lost foam casting is advantageous for producing complex, detailed parts with a high surface finish, but it can be more expensive upfront. On the other hand, sand casting is more versatile for larger parts but may have limitations in terms of intricate shapes and surface finish. The choice between the two methods depends on the specific requirements of the part, the desired production volume, and cost considerations.